Test de la buse NiTro Max de chez Hotend.fr
Salut à toutes et tous, on va se retrouver aujourd’hui autour d’une innovation conçue et fabriquée en France : la Buse NiTro Max de chez Hotend.fr. Une boite que son fondateur définie en ces quelques mots : “Fabricant Français D’accessoires Et De Solutions Innovantes Et Exclusives Pour L’impression3D”,
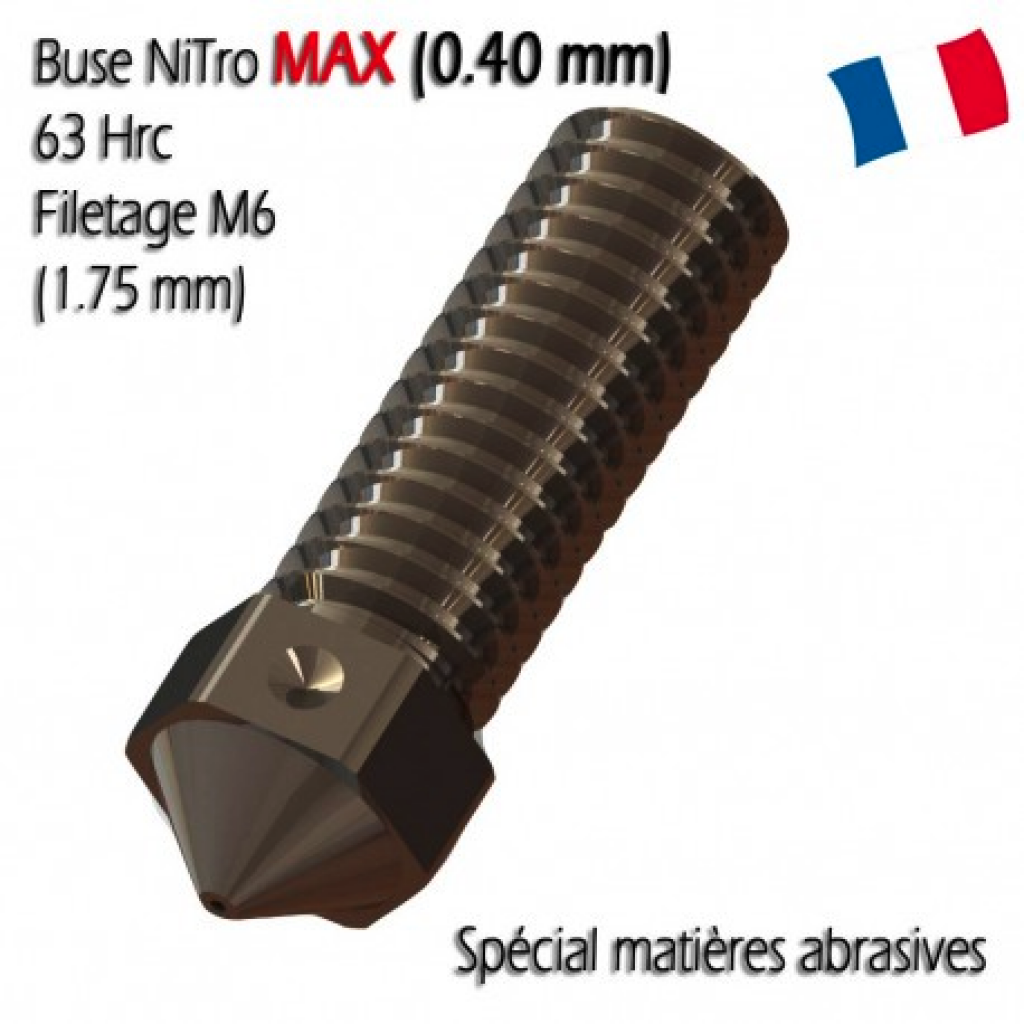
1 – Présentation de la marque :
Pour tout vous dire j’ai passé un coup de fil à Fred, le fondateur et créateur de la société Hotend.fr, pour lui demander un peu sa philosophie, et l’origine de ses motivations à développer autant de produits autour de la fabrication additive et de nos chères imprimantes FDM : la réponse fut cinglante : “c’est simple, on regarde où sont les problèmes, on cherche et développe une solution simple et pérenne, une solution durable, qui s’inscrit dans une logique de fiabilité, et une exigence d’avoir un haut niveau de qualité sur le produit fini, solution définitive !!! philosophie du durable !” je ne m’attarderai pas sur le reste de notre discussion car entre passionnés elle a duré plus d’une heure, et encore nous n’avons pas abordé le Rugby (Clermont vs Toulouse) ….
En résumé : Hotend.fr conçoit et fabrique des produits “haut de gamme”, en France, avec un cahier des charges très relevé, assurant à tous ses clients une garantie d’un travail bien fait et ça, personnellement ça me plaît, d’autant plus que j’avais déjà eu la chance de tester un autre “best seller” de la marque : le Magnet MK10 sur ma CR10S Pro.
Cette fois, j’ai reçu la buse NiTro Max. Adapté à la tête de type Volcano de ma Sidewinder X1 V4, filetée en M6.
2 – Mais c’est quoi la NiTro Max :
La buse NiTro Max est une buse avec un corps en laiton, usinée et traitée en France, calibrée au micron près, et vous pouvez me croire sur parole, Fred se charge lui même de vérifier les relevés de fabrication, s’assurant ainsi des valeurs des marges et d’assurer un tel détail de précision.
Une fois usiné, le corps en laiton de la buse est recouvert d’une couche de nickel de 25 microns d’épaisseur, déposée par bain chimique. Ce rajout permet de renforcer la buse, d’obtenir un effet anti-abrasif en augmentant la dureté de l’ensemble, rendant la buse comparable à une buse en acier trempé en termes de résistance (noté par les essais sur test de Rockwell l’acier trempé commence à 60 Hrc, la buse de Hotend.fr atteint elle 63 Hrc)
À noter :
- la coupe de la buse (cf photo du site ci-après) : sur une buse classique, le profil interne est droit, ici le profil est conique, ce détail a toute son importance, le profil conique rend l’extrusion plus rapide et si vous regardez bien la photo, ça augmente la quantité de laiton autour de la sortie de matière, plus de laiton = meilleur quantité de chaleur et meilleur qualité de chaleur = moins de température de chauffe.
- la buse est disponible en 4 diamètres de sortie : 0,4 – 0,6 – 0,8 et 1 mm
- un codage à point vous permet d’identifier les diamètres facilement de 1 point pour la 0,4 mm jusqu’à 4 point pour le 1 mm.
- 60mm de PTFE Capricorn sont offert lors de l’achat de la buse pour remplacer le heatbreak sur la Sidewinder X1 et Genius.
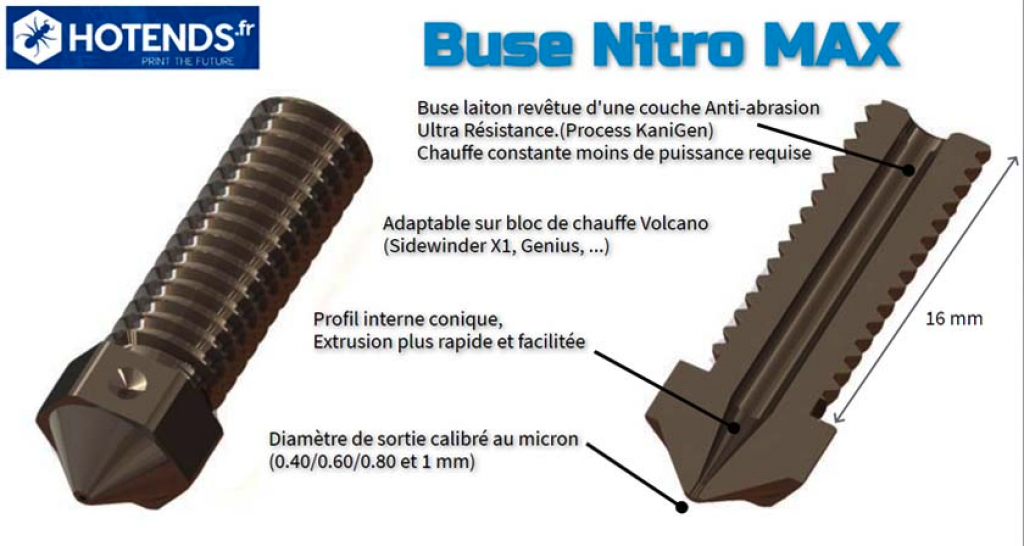
3 – Avantages de la buse NiTro Max :
Je ne vais pas commencer la liste des avantages de la buse NiTro Max par : “elle est Made in France”, on me traiterait surement de démago, même si sérieusement c’est un peu ce que je pense, donc :
Premièrement la dureté, la buse NiTro Max est créée pour passer en quantité les filaments les plus agressifs, hotend.fr assure au minimum 6kg de PLA chargé en carbone avec la même buse et connaissant le lascar : si il dévoile son jeu c’est qu’il en a encore sous la main et je rajouterai bien deux ou trois kilos de matériaux abrasifs derrière le chiffre volontairement annoncé.
Deuxièmement, la conductivité de la chaleur, rien d’original dans le fait que le laiton soit un excellent conducteur de chaleur, je pense que ça tout le monde l’a remarqué, par contre je reviens sur le profil interne en cône qui permet d’augmenter la quantité de laiton autour de la tête, et par conséquent la quantité de chaleur, pour l’exemple, le PLA noir qui sert dans ce test sortait à 200-205 sur la buse d’origine, avec la NiTro Max j’ai du revoir mes paramètres d’impression (rien que ça !) pour finir à une température idéale de 185° au plus bas. Un gain de 15-20° sur la température de fusion du PLA, c’est simplement génial !!!! … et par la même occasion, même s’il est minime un gain de consommation de courant.
Troisièmement, et c’est un effet qui découle de l’addition des deux précédents : si vous pouvez augmenter la température, tout en permettant au matériaux de s’écouler mieux et plus vite = vous pouvez augmenter vos vitesses d’impression ni plus ni moins.
J’y vois donc un petit inconvénient, c’est cool de n’en dire que du bien mais il y a donc un revers à la médaille et vous l’aurez compris : vous montez la buse de Hotend.fr et hop ! Quasiment tous vos profils à retravailler, je dis ça sur le ton de la plaisanterie, mais c’est un fait, prenez bien le temps de voir comment le plastique que vous avez l’habitude de travailler va se comporter avec la buse NiTro Max en faisant un petit print sans support mais avec du surplomb.
4 – Quelques Photos :
Je ferai un article / “tuto” pour vous montrer l’intégralité du démontage et montage de la buse sur la X1 Sidewinder, mais vraiment par chance j’ai eu un fails :

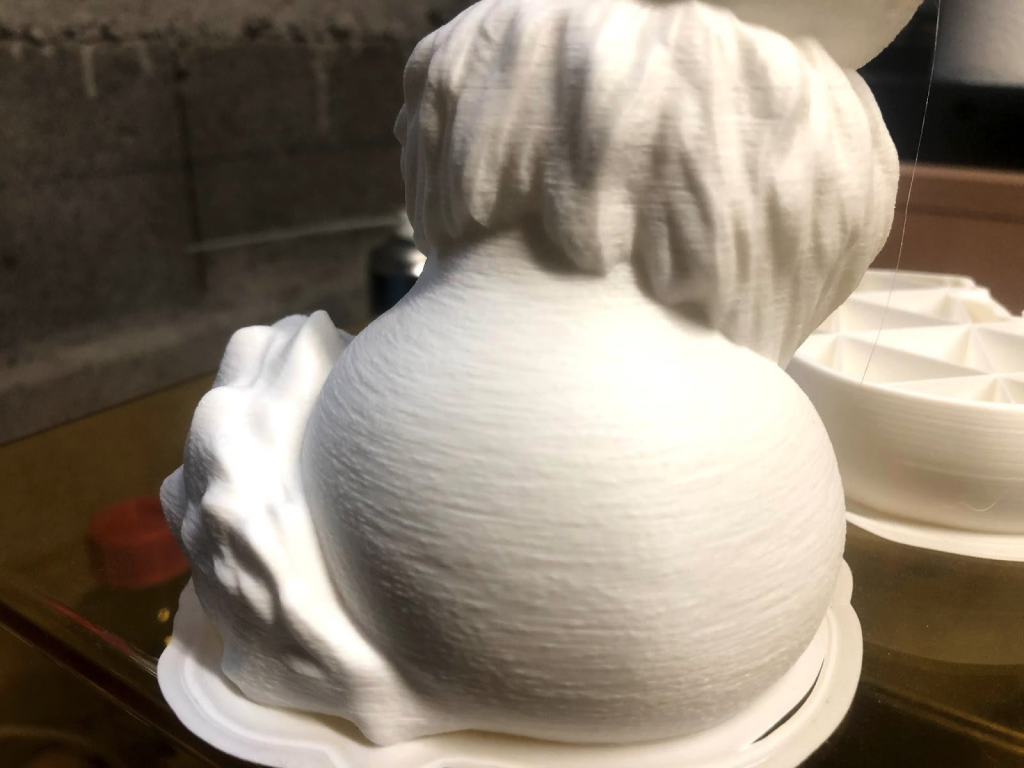
un petit coup d’œil le matin du print et j’avais cette texture, granuleuse avec un manque de matériaux par endroit, signe direct d’une sous extrusion sévère et probablement de buse bouchée.
J’avais la chance d’avoir sous la main la buse NiTro Max de Fred, et je l’ai montée dans la foulée, (j’avais un énorme bouchon que je vous montre dans le tuto) et là :
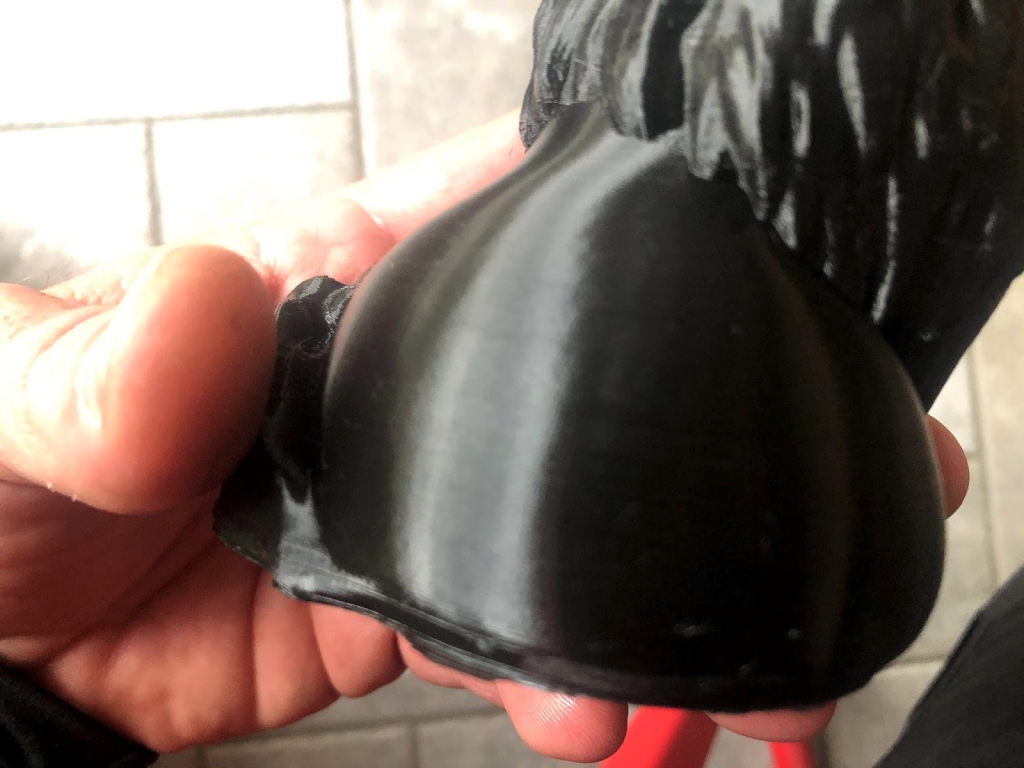
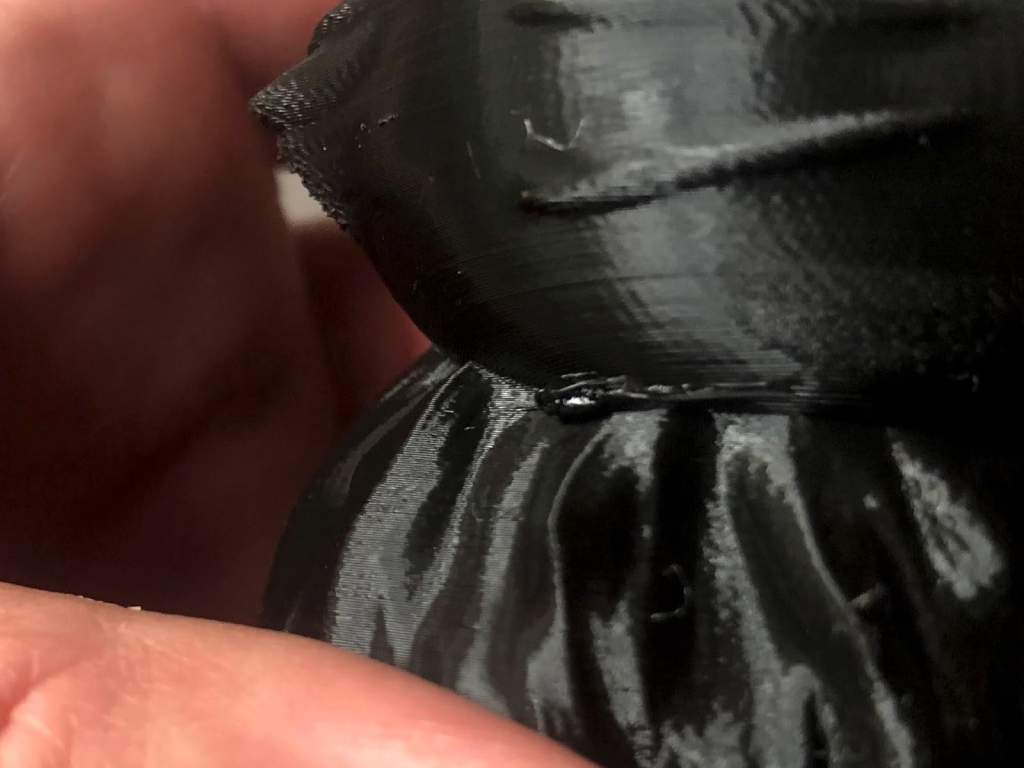
Alors, oui je n’avais plus de sous extrusion mais des “coulures”, un excès de PLA par endroit et carrément les bords parfois saillants, difficile à prendre en photo, mais j’ai percuté que c’était la température qui n’allait pas, j’avais relancé le STL sans le slicer de nouveau, j’ai diminuer manuellement la température jusqu’à 185° pour finir tranquillement,
J’ai ensuite refait un support dont j’avais besoin, laissant la température d’origine mais en accélérant la Sidewinder (70 mm/s , 45 mm/s pour les parois, 50 mm/s pour le remplissage), j’ai dû augmenter un peu les paramètres de rétraction, le print n’était pas compliqué mais on est loin des vitesses à laquelle j’utilise cette grosse imprimante d’habitude :
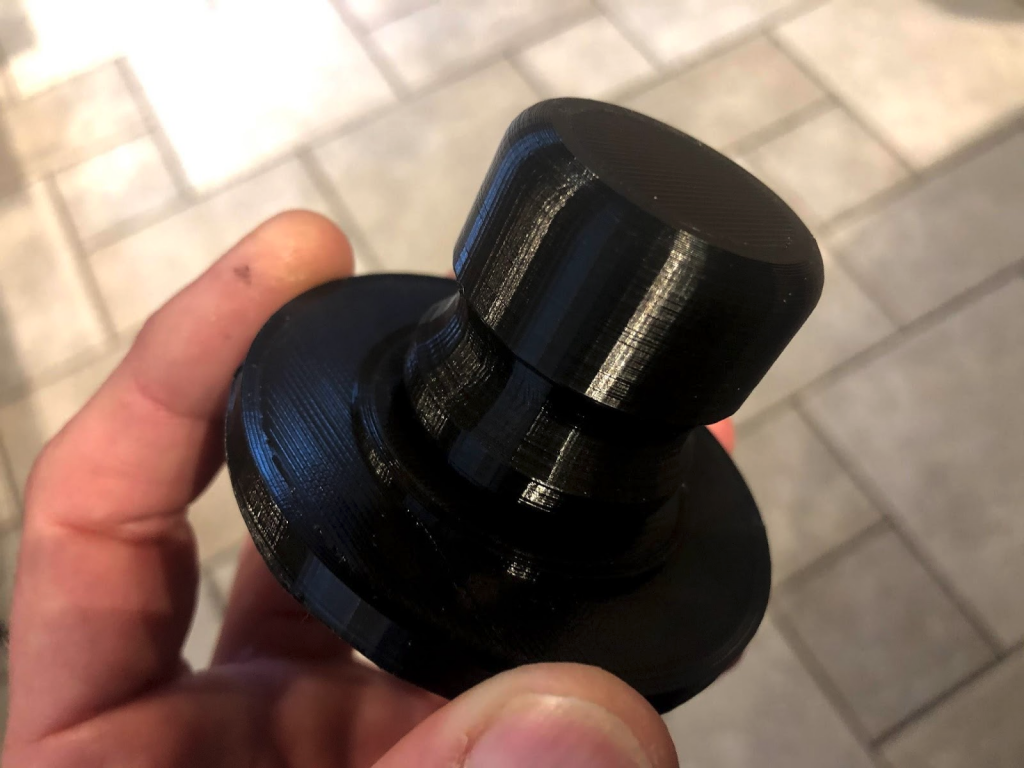

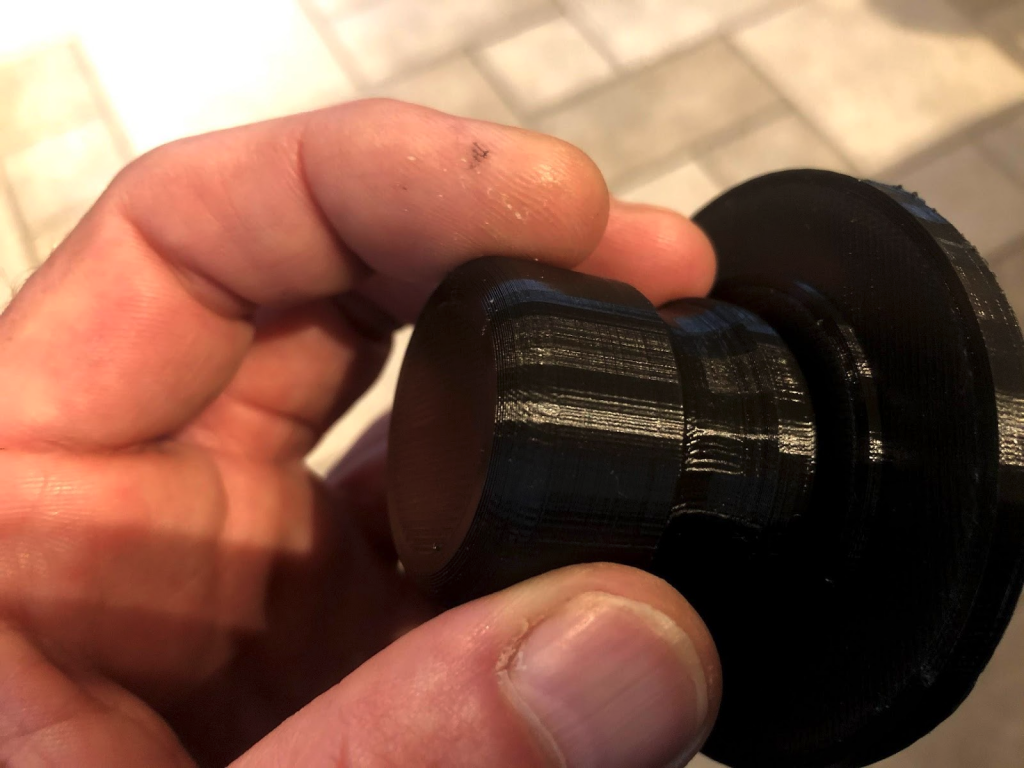
c’est sorti super propre, très intéressant comme expérience, je reçois bientôt la Super Racer de Flsun, je serais curieux d’installer ce type de buse sur une imprimante Delta avec laquelle j’ai moins de scrupule à faire imprimer rapidement.
À noter : je n’aime pas du tout imprimer si vite avec la Sidewinder, je l’ai fait juste pour le test…
5 – Dois-je investir ?:
Très bonne question, j’ai pour l’habitude de dire : “tant que ça marche, tu touches pas!”, encore plus sur la Sidewinder, mais gardez à l’esprit ces quelques petites choses :
- vous pourrez ensuite imprimer tous types de matériaux,
- pour la même somme, certes vous achèterez une dizaine de buses traditionnelles fabriquées en Asie mais bien moins durables,
- vous allez y gagner en confort d’impression, et ne plus jamais penser à changer la buse, surtout si vous imprimez en majorité du PLA et du PETG classique, comme le dit Fred “si tu ne sors que du PLA, ma buse elle sera encore parfaite que ta machine sera déjà en vrac!”
Maintenant vous avez toutes les infos pour faire votre choix, à titre personnel c’est sur que je vais m’équiper pour les autres machines vu le choix disponible sur le site de Hotend.fr, d’autant qu’avec le paquet vous recevez un petit code de 10% sur l’ensemble des produits.
Merci à Nozzler et à Hotend.fr de m’avoir fait confiance pour ce test, merci aux designers et concepteurs, toujours plus nombreux à nous proposer des STL sur les sites de partages dédiés. Restez connectés sur nos réseaux et notre Insta où nous postons régulièrement nos réalisations avec les matériaux testés sur Nozzler.
TEST RÉALISÉ PAR GUILLAUME MERCIER POUR NOZZLER.