Les différents type de filament
Les différents filament dans le monde de l’impression 3D
Il existe une multitude de filaments ainsi qu’une multitude de fabricants de filaments, et donc avec des différences plus ou moins importantes. Ce n’est pas toujours facile de s’y retrouver, de choisir le bon filament et de comprendre pourquoi d’une marque à l’autre, ou dans la même marque, il peut y avoir des différences.
Pour mieux comprendre, je vous propose un rapide tour d’horizon de l’ensemble des matières plastiques ainsi qu’une présentation du procédé de fabrication de ces filaments pour finir par une description des filaments les plus utilisés en impression 3D par dépôt de filament ainsi qu’un tableau récapitulatif.
Généralité sur les matières
Les filaments sont fabriqués à partir de matière thermoplastique qui ont donc la capacité de changer d’état (solide/visqueux) indéfiniment avec la température ce qui permet de les transformer et les recycler facilement. Le plastique comme on l’appelle vulgairement entoure nos vies que ce soit dans les emballages, le bâtiment, l’automobile, l’électroménager, le médical. Mais il existe de nombreux thermoplastique. Les plus utilisés sont les polyoléfines (PP,PE) suivie du PET et du PVC.
On représente l’ensemble des thermoplastiques dans le pyramide ci-dessous par niveau de performance et selon leur famille de nature chimique amorphe ou semi-cristalline. Cette notion de base de la structure de la matière est fondamentale pour les propriétés de la matière mais aussi pour l’utilisation en impression par dépôt de filament.

Les matières amorphes ont une structure moléculaire disposée aléatoirement, et n’ayant pas de point de fusion précis, se ramollissent progressivement à mesure que la température augmente. Les matières amorphes ont des retraits (différence de dimension entre l’impression chaude et la pièce froide) faible et isotrope (identique dans toutes les directions d’impression). Plus le retrait est faible et isotrope, moins vous aurez de risque de déformation, gauchissement (warping) sur vos impressions. Les résines amorphes perdent leur résistance rapidement au-dessus de leur température de transition vitreuse (Tg) qui est schématiquement la température du passage de l’état rigide/cassant à l’état mou/déformable.
En général, pour les matières amorphes, qui sont donc le type de matière le plus utilisé en impression 3D filament, la température du plateau doit être au plus proche de la transition vitreuse de la matière qui est donc également proche de la tenue température.
Les matières semi-cristallines possèdent une structure moléculaire hautement ordonnée dite cristalline mais conserve également une part de structure désordonnée amorphe car pour différentes raisons ces matières ne peuvent pas cristalliser complètement. Les matières semi-cristallines ont des points de fusion très précis (température à laquelle la phase cristalline ce désordonne et devient amorphe). Elles ne ramollissent pas à mesure que la température augmente, mais restent dures jusqu’à ce qu’une certaine quantité de chaleur soit absorbée, puis se transforment rapidement en un liquide à basse viscosité. Ces matières ont un retrait plus important (qui augmente avec la cristallinité de la matière) et anisotrope (différent selon les directions) ce qui engendre du gauchissement. La cristallinité apporte à la matière une meilleure résistance chimique, mécanique et thermique. Les matières semi-cristallines renforcées ont des propriétés haute-températures bien meilleures, et conservent des niveaux de résistance et de rigidité au-delà de leur température de transition vitreuse (Tg).
La cristallisation de la matière s’opère donc dans une phase de refroidissement. Certaines matières cristallisent très lentement, et sont facilement solides à l’état amorphe bien que leur structure leur permettent de cristalliser. C’est le cas par exemple du PET, PETG et du PLA qui sont donc représentés au milieu du triangle car ces matières existent dans les deux états, même si en impression 3D on les garde sous la forme amorphe.
Un autre exemple de matériau semi cristallin utilisé en impression 3d (Grâce à l’avancé des technique) et le PEEK qui est 30% cristallin et 70% amorphe.
La fabrication de filament
Passons maintenant à la fabrication du filament.
Les fabricants utilisent une extrudeuse comme le schéma ci-dessous.
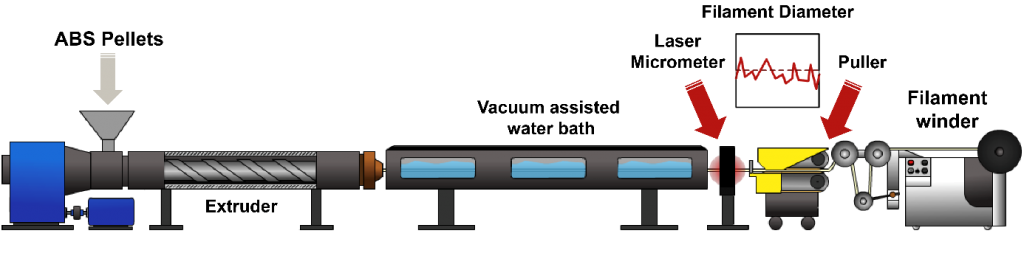
(source: University of Wisconsin-Madison)
L’extrudeuse est alimentée avec des granulés de matière thermoplastique auquel le fabricant peut ajouter des colorants. Les fabricants les plus techniques peuvent également ajouter eux-mêmes des charges (bois, fibres,….),ou d’autres matières.
L’extrudeuse est équipée d’une vis sans fin qui tourne dans un fourreau chauffé pour fondre, mélanger la matière et la pousser dans une filière qui lui permet de sortir sous la forme de filament. Le filament est alors refroidi, généralement dans un bac d’eau chauffé ou non selon les matières. Le filament est également tiré à l’extrémité et enroulé en bobine. Pour vous donner un ordre d’idée, une ligne d’extrusion complète mesure plusieurs dizaines de mètres. Le travail du fabriquant de filament, après avoir bien sélectionné ses matières, est donc de les extruder en respectant les températures d’extrusion ainsi que le temps et les températures de refroidissement pour que la matière garde ses propriétés. Mais aussi de fabriquer un filament calibré qui a un diamètre constant et bien sûr un bon bobinage et emballage.
Les différentes matières
PLA :
Le PLA pour Polylactic Acid est un biopolymère selon les norme EN16785-1 et ASTM D6866, provenant du manioc, de l’amidon de maïs, de la canne à sucre ou de la betterave. Ces ressources sont en fait utilisées pour produire deux types d’acide lactique utilisé dans la fabrication du PLA ( l’acide (L)-lactique (LLA) et l’acide (D)-lactique (DLA)). Selon l’utilisation de l’un ou l’autre ou des deux les propriétés finales et d’impression seront différentes.
Le PLA est une matière biodégradable selon la norme EN 13432 car ça composition lui permet de se dégrader en composés organiques (CO² et minéraux) avec une teneur maximale en métaux lourd. Mais le PLA est dégradable en compost industrielle uniquement, donc sous température (60°C) et atmosphère contrôlé. Par conséquent, le PLA ne peut pas être utilisé dans sa forme actuel pour des applications en compostage à la maison. De plus, lors de la fabrication de filaments des additifs sont ajoutés pour la couleur ou pour améliorer des propriétés. Ces additifs ne sont pas forcément biodégradables.
Dans l’industrie le PLA est actuellement essentiellement utilisé pour de l’emballage alimentaire, des jouets, les textile intissés (couche bébé).
Le PLA est la matière de référence en impression 3D car dans sa forme amorphe le PLA a très peu de retrait donc de gauchissement (warping), il se travaille avec des températures basses et il a peu d’odeur. Il est donc facile à imprimer. Il est également facile à poncer et à peindre. C’est une matière très rigide et cassante avec une faible tenue en température.
Il est également possible de faire cristallisé le PLA avec une recuisson pour lui apporter des meilleures propriétés mécaniques et thermiques. C’est notamment le cas des PLA Ingeo 3D850 et Ingeo 3D870 de NatureWorks proposé par divers fabricants de filaments.
Avantages :
Impression très facile
Très large gamme de couleurs disponible
Faible odeur
Inconvénients :
Fragile
Tenue température
Résistance à l’humidité et aux UV (mais vous pouvez le peindre).
Applications :
Prototype, figurine,…..
PET et Co-polyester (PETG)
Le PET pour polyester téréphtalate est une matière que vous trouvez tout autour de vous régulièrement, de la bouteille de soda au t-shirt en polyester. Le PET est effectivement un Polyester fabriqué avec un Acid (Acid Téréphtalique) et dans le cas du PET-G, d’un Glycol (l’éthylène Glycol).
C’est une matière transparente sous sa forme amorphe avec une bonne souplesse et résistante aux chocs. Sous sa forme cristalline cette matière est au contraire très rigide et avec une bonne tenue en température.
On l’utilise en impression 3D par dépôt de filament sous sa forme amorphe pour ça bonne résistance au choc, résistance chimique et température. En fait peut de marque propose juste le PET et dans la grande majorité c’est plutôt la forme PET-G qui est commercialisée.
Comparés au PET, les Co-polyesters sont fabriqués avec un Glycol (Cyclohexane dimethanole) ou un Acid (Acid Isophthalique) en plus. Cet ajout permet d’améliorer les propriétés mécaniques, thermiques et chimiques en comparaison avec le PET. Cela limite également la cristallisation de la matière pour une meilleure transparence, adhésion des couches et un faible gauchissement. Il existe donc plusieurs copolyeters (PETG, PCTG, PCTA, …) selon les proportions de l’un ou de l’autre des Glycols et des Acides. Bien que les fournisseurs de filament appellent tous leurs bobines PETG, vous pouvez en réalité souvent trouver des PCTG ou PCTA. Les propriétés bien que similaires sont différentes. C’est pourquoi vos paramètres d’impression et les résultats finaux sont différents.
Les Co-polyesters (PETG) sont de plus en plus utilisés en impression 3D car ils restent faciles à imprimer, avec une très bonne adhérence inter couches et apportent plus de résistance mécanique et thermique que le PLA. Il est également « sans odeur ». Le principal défi est de gérer le stringing (petits-fils) par la température, la rétraction et le stockage/séchage de vos bobines. Et oui le PETG absorbe très rapidement l’humidité de l’air qui a une influence directe sur le stringing, la transparence et l’adhésion des couches.
Avantages :
Impression facile
Transparence
Résistance au choc
Pas d’odeur
Transparence
Résistance à l’eau
Inconvénients :
Résistance aux UV
Rigidité
Applications :
Figurines, jouets, pièces devant résister aux chocs, vases, pièces en contact prolongé avec l’eau, emporte pièces de cuisine (avec filament alimentaire et précaution adéquate)
ABS (Acrylonitrile butadiène styrène)
Schématiquement l’ABS est un matériau dit bi-phasé. Il est fabriqué en mélangeant un copolymère de styrène-acrylonitril (le SAN) qui apporte tenue chimique, température et brillance, à un élastomère à base de polybutadiène qui apporte de la résistance au choc. L’ABS est très utilisé dans l’électroménager, les jouets, la cosmétique, le bâtiment pour sa bonne résistance aux chocs et son aspect.
C’est une matière très utilisée en impression 3D car elle apporte des bonnes propriétés mécaniques et thermiques avec la possibilité d’un lissage facile en vapeur d’acétone. Son principal inconvénient est que cette matière est sujette au gauchissement. De plus, des études ont montré que l’impression de l’ABS émettait beaucoup de microparticules dans l’air. il font donc être vigilant à l’emplacement de l’imprimante quand on imprime ce genre de matériau.
Avantages :
Compromis choc et rigidité
Résistance en température
Lissage en vapeur d’acétone
Inconvénients :
Résistance aux UV (jaunie et devient cassant)
Odeur
émission de micro particules.
Tendance au décollement, gauchissement
Applications :
Figurines, jouets, pièces légèrement sollicitées mécaniquement,
ASA
L’ASA est une matière proche de l’ABS à la différence qu’il utilise un élastomère acrylique et non du butadiène. Ce qui lui donne une très grande résistance aux UV. C’est pourquoi cette matière est très utilisée dans les applications extérieures, le bâtiment et dans l’automobile.
Cependant, attention sur la tenue aux UV. Car même si l’ASA résiste naturellement bien aux UV, les colorants et pigments utilisés peuvent eux être sensibles aux UV. Il faut donc veiller que le fabricant de filament ait bien ajouté des anti-UV pour protéger les couleurs.
L’ASA aura également une tenue en température légèrement supérieure à l’ABS et également une meilleure résistance chimique. Il est par contre plus rigide et moins résistant au choc.
Tout comme l’ABS, l’ASA émet beaucoup de micro particules pendant l’impression.
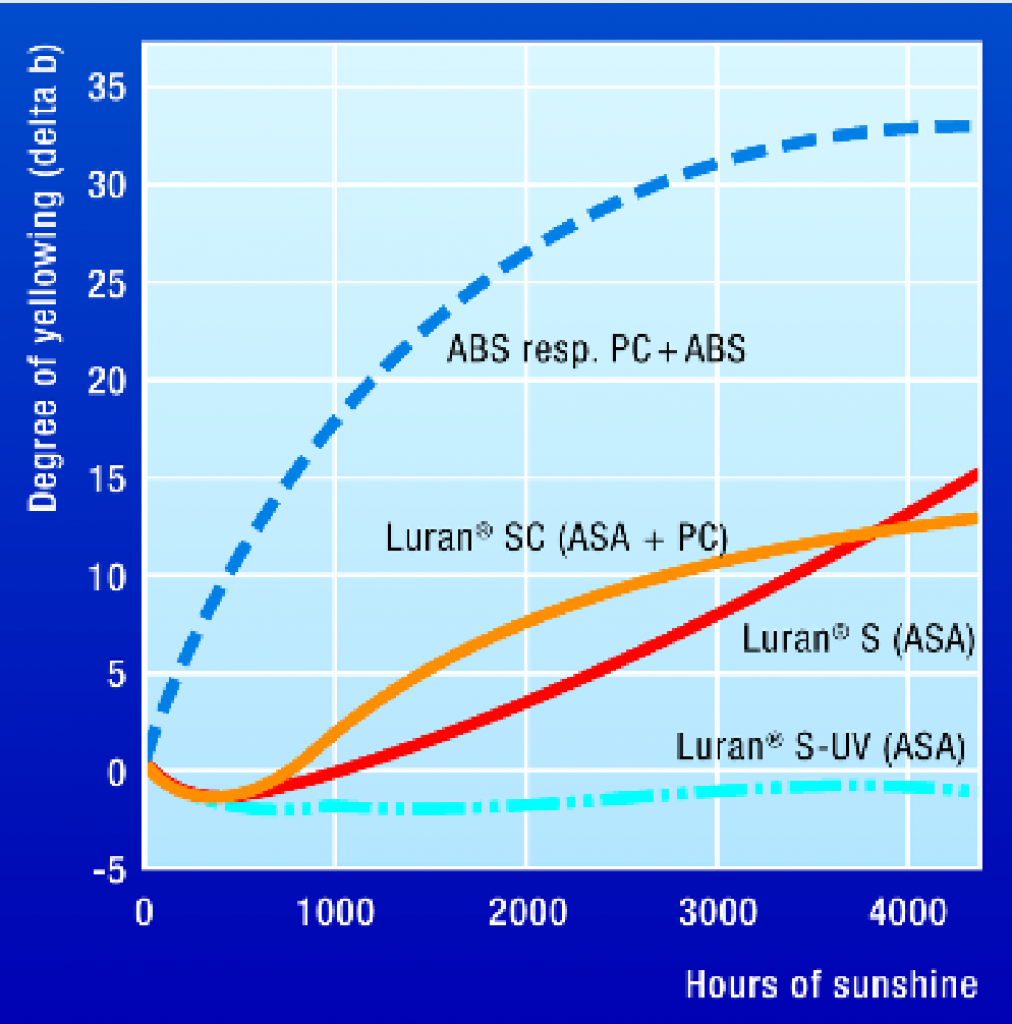
(source Ineos Styrolution (ex.BASF) producteur d’ASA et d’ABS)
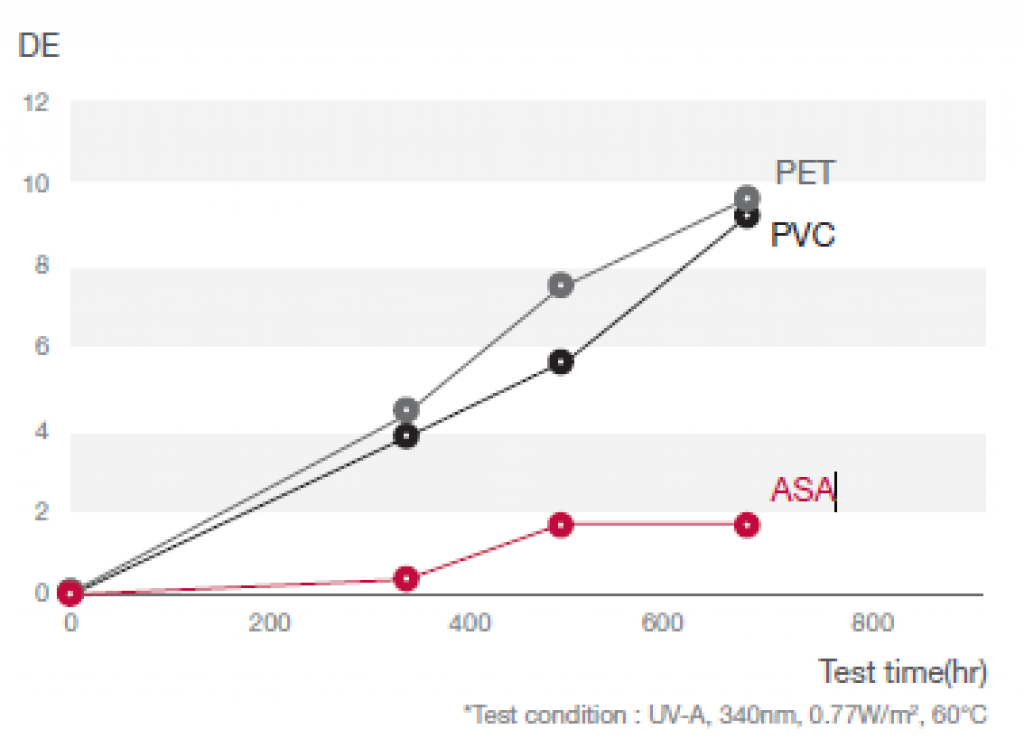
(source LG Chem producteur d’ASA et d’ABS)
Avantages :
- Résistance au UV
- Compromis choc et rigidité
- Résistance en température
Inconvénients:
- Odeur
- émission de micro particules.
- Tendance au décollement, gauchissement
Applications :
Toutes pièces extérieure, pièces intérieur automobile
HIPS
Le HIPS est un polystyrène choc très utilisé dans l’emballage et l’électroménager qui sont des applications avec des filiaires de recyclage déjà bien établies. Il est donc facile de trouver du HIPS recyclé.
En impression 3D il est essentiellement utilisé comme support soluble car ce dissous avec le D-limonène. Mais il peut également être utilisé en alternative à l’ABS.
Avantages :
Résistance au choc
Soluble dans le D-limonene
Inconvénients :
Odeur
Tendance au décollement, gauchissement
Flexible TPE
Le TPE pour thermoplastique élastomère désigne donc un ensemble de matière parmi lesquelles le TPU, le TPV , le TPS ou SEBS, PEBA,… Chaque matière aura donc ses caractéristiques. Nous nous attarderons sur les deux plus représentées.
Les élastomères sont généralement caractérisés par leur dureté qui exprimé en dureté Shore.
Il existe deux types de dureté Shore. Le Shore A pour les produits les plus souple et le Shore D pour les produits les plus durs. Normalement le passage d’une mesure de Shore A à Shore D s’effectue à 90 Shore A, valeur après laquelle cette mesure n’est plus pertinente car ne différencie pas assez les duretés. Comme vous pouvez le voir ci-dessous dans la courbe de correspondance des duretés. Mais malheureusement la grande majorité des fabricants de filaments proposent du 95 Shore A. Cette valeur étant non pertinente, vous comprenez pourquoi vous vous retrouvez avec des différences de dureté quand vous comparez divers marques de filaments TPU 95 Shore A.
Sachant également qu’à dureté équivalente, la rigidité de la matière peut être différente.
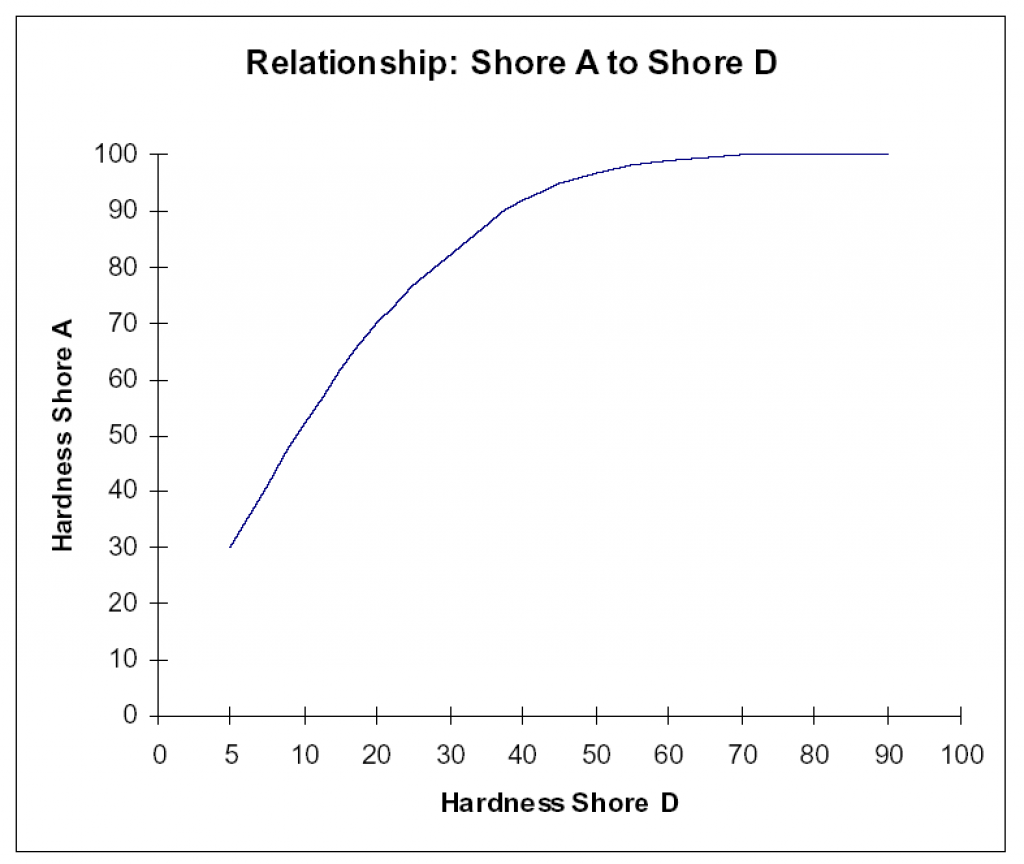
TPU
Le TPU est certainement l’élastomère le plus utilisé en impression 3D. Dans l’industrie vous le retrouverez également dans de nombreuses applications comme les roues de valises, les pommeaux de vitesse, les planches de bords auto moyen et haut de gamme, le soft des tournevis haut de gamme, les chaussures de ski,…
Mais le TPU est une famille de matière assez vaste car le TPU peut être fabriqué de différentes façons notamment avec soit un Polyester soit un Polyéther.
Les polyesters ont de meilleures résistances à l’abrasion, une meilleure mémoire élastique et une meilleure résistance en température. Ils ont cependant une mauvaise résistance à l’hydrolyse et aux attaques microbiennes. Ce n’est pas le cas des polyéther qui en plus ont une meilleure résistance chimique, aux basses températures et aux UV même si ils jaunissent quand même à moyen-long terme. Le problème c’est toujours qu’il est difficile de savoir quel TPU est utilisé pour les filaments. Mais bien souvent, pour une question de prix les fabricants des filaments TPU utilisent une base Polyester.
Les TPU ont généralement une adhérence naturelle sur l’ABS et le polycarbonate. Ils peuvent également adhérer sur les polyamides et les copolyesters (PETG). Les TPU Polyéther donneront d’ailleurs de meilleurs résultats. Tout comme le PETG, le TPU reprend l’humidité assez rapidement, ce qui peut avoir des influences sur vos impressions.
Avantages :
- Souplesse, résistance au choc
- Résistance aux graisses
- Résistance à l’abrasion
- Résistance à la déchirure
- Résistance en température 80°C (certaine formulation peuvent tenir à 110°C)
- Transparence
Inconvénients :
- Résistance au UV
- Résistance en milieu humide (si Polyester)
Application :
Roues, protections, joints, jouets,…
TPC
L’autre élastomère que l’on rencontre est le TPC pour thermoplastique copolyester, notamment connu sous le nom d’Arnitel dans l’impression 3D. Cette matière a des propriétés proche du TPU avec une meilleure résistance en température (140°C) mais existe uniquement dans des duretés élevées de 90 Shore A minimum. On retrouve donc cette matière dans des applications comme les soufflets automobiles, les conduits d’air chaud ou les amortisseurs des sommiers à lattes.
Avantages :
- Souplesse, résistance au choc
- Résistance au graisse
- Résistance à l’abrasion
- Résistance à la déchirure
- Résistance en température 80°C (certaine formulation peuvent tenir à 110°C)
Inconvénients :
- Résistance au UV
- Résistance en milieu humide (si Polyester)
Applications :
protections, piècse soumises à de nombreuses déformations.
POLYAMIDE
La famille des polyamides est constituée de nombreuses chimies et bien souvent les fabricants de filament grand public utilisent uniquement le terme polyamide voir Nylon sans plus d’information.
Le Polyamide 66 a été le premier polyamide inventé en 1935 aux USA par Du Pont de Nemours sous le nom de Nylon. C’est 3 ans plus tard que les Allemands inventent le Perlon qui est un polyamide 6. Ce sont toujours les polyamides les plus utilisés, notamment pour le textile, les films d’emballage et la fabrication de pièces techniques pour l’automobile, le sport et loisir et les applications électriques. Ces matières reprennent beaucoup d’humidité jusqu’à 9.5% pour le PA6 et 8.5% pour le PA66 à saturation. Il faudra donc maîtriser ce paramètre pour l’impression car l’humidité peut poser des problèmes d’impression, mais aussi sur les caractéristiques finales de la pièce car plus elle absorbe l’humidité, plus elle est souple et résistante aux chocs.
En impressions 3D on trouve finalement souvent du PA6 qui a une température d’impression plus faible.
Les autres polyamides sont les PA11 et PA12 que l’on retrouve également en impression car plus facile à travailler avec des températures plus basses mais surtout une reprise d’humidité moindre (2.9% pour le PA11 et 1.5% pour le PA12 à saturation).
Avantages :
- Résistance mécanique traction, fatigue, choc
- Résistance au hydrocarbure
- Résistance thermique
- Résistance à l’abrasion
Inconvénients :
- Absorption d’humidité importante.
- Gauchissement important
- Résistance à l’hydrolyse
Applications :
Pièces mécaniquement sollicitées
POLYCARBONATE PC
Le Polycarbonate est une matière transparente avec une très grande résistance au choc et à la température et une bonne résistance au feu C’est pourquoi elle est très utilisée dans le bâtiment sous forme de plaques, dans l’industrie automobile (projecteurs, voyants rétroéclairés), l’éclairage, le médical, le ferroviaire ou pour les plus nostalgiques pour la fabrication de CD.
Mais qui dit matière avec une très bonne résistance en température, dit haute température d’impression pour avoir les pleines caractéristiques du polycarbonate. (Plateau à 135°C et Filament entre 290 et 310°C). C’est le principal frein de cette matière en impression 3D. Plusieurs fabricants proposent maintenant des Polycarbonates modifiés pour faciliter l’impression. Mais les propriétés se trouvent ainsi réduites.
Avantages :
- Transparence
- Résistance au choc
- Résistance en température (115°C en continué et 135°C en pointe)
- Résistance en stérilisation vapeur
- Bonne résistance à la flamme (classement V2)
Inconvénients :
- Condition d’impression
- Tendance au décollement, gauchissement
Applications :
Pièces avec besoin de résistance aux chocs et thermique, notamment dans l’éclairage.
PP
Le Polypropylène, est la matière la plus fabriquée et consommée. Car elle combine faible densité, prix faible (de la matière pas du filament) , résistance thermique et mécanique intéressante, très bonne résistance chimique, compatibilité alimentaire…. Voilà pourquoi vous la trouvez dans des domaines aussi variés que l’emballage, l’automobile, le médical. Le PP est également connu pour être difficile à peindre et à coller du fait de sa polarité. Il faudra donc procéder à des préparations de surface notamment flammage.
Cette polarité pose également le problème de l’adhérence sur le plateau d’impression. C’est pourquoi’ l’utilisation d’un adhésif PP (généralement les adhésifs marron ou transparent pour les cartons) est conseillé.
Le PP est une matière avec un retrait important qui peut poser des problèmes d’impression.
Avantages :
- Résistance chimique
- Résistance mécanique
- Résistance au UV correcte
Inconvénients :
- Gauchissement important
- Adhérence
Applications :
Pièces avec besoin de résistance chimique, applications alimentaires,…
PEI
Le PEI polyétherimide est une matière tout en haut de la pyramide, donc très performante et en plus amorphe, donc plutôt intéressante pour l’impression 3D. Cette matière a été inventée en 1982 par General Electric Plastics qui a été rachetée par le saoudien SABIC qui fabrique et commercialise cette matière sous le nom Ultem. Divers fabricants de filaments spécialisé proposent des produits sur cette base. Le PEI est connu pour sa bonne résistance mécanique, sa résistance chimique et sa très bonne résistance thermique, ainsi que d’isolant électrique sous haute température. Il est employé dans des applications très exigeantes d’aéronautique, le médicale, l’électronique.
Avantages :
- Résistance chimique
- Résistance mécanique
- Résistance au UV
- Résistance à la flamme V0
Inconvénients :
- Prix
- Transformation avec des imprimantes haute température (350-380°C)
PEEK
Dans l’industrie le PEEK est principalement utilisé pour des applications soumises à hautes contraintes multiples (Température et/ou mécanique et/ou frottement et/ou chimique) pour des paliers de frottement, cage de roulement dans l’aéronautique, corps de vanne en industrie chimique, prothèse médicale,…
C’est la matière tout en haut de la pyramide des thermoplastiques car la plus résistante. Mais également la plus onéreuse. En impression 3D c’est également un très gros challenge pour l’imprimer. Elle nécessite des hautes températures d’impression mais aussi une enceinte avec une température constante et chaude. En effet le PEEK est une matière cristalline mais qui peut rester facilement à l’état amorphe si elle est chauffée et refroidie trop rapidement (avant cristallisation). Il faut donc laisser le temps à la matière de cristalliser pour qu’elle ait le maximum de ses propriétés.
Le PEEK commence aussi a avoir des applications médicales intéressantes notamment dans l’impression de prothèses en remplacement du titane.
Avantages :
- Résistance chimique
- Résistance mécanique
- Résistance à la flamme V0
- Résistance à l’usure
Inconvénients:
- Prix
- Transformation très délicate, nécessitant un matériel de haute performance.
Support soluble
L’alcool polyvinylique (PVA ) est soluble dans l’eau. Il est donc surtout utilisé dans les emballages solubles type tablettes de lave-vaisselle. En impression 3D il est utilisé comme matière de supports en impression multi matières. Les supports pourront alors être dissous dans l’eau.
Vous pouvez également trouver des filaments en Butenediol Vinyl Alcohol Co-polymer (BVOH) pour des résultats similaires. Le BVOH se dissout généralement plus rapidement et sa tenue en température plus élevée le rendra plus facile d’utilisation pour des impressions longues.
Le principal problème de ce type de filament c’est qu’il absorbe très facilement l’humidité environnante. il faut absolument le passer au déshydrateur avant de s’en servir et même directement à la sortie il recommence immédiatement à capter l’humidité. Pour d’autres raisons les fabricants ont conçu des boitier type ‘filadryer’ et il est alors fortement recommandé lors de l’impression d’un filament soluble d’utiliser ce genre de boitier pendant l’impression.
Charges
Il existe plusieurs types de charges utilisées pour modifier les propriétés des matières que ce soit esthétique ou mécanique.
Dans tous les cas l’ajout de charge sera bénéfique en impression 3D pour réduire le retrait et donc le gauchissement. Par exemple, eSun ajoute 2% de charge minéral à son PLA+ (information trouvée sur la fiche de donnée de sécurité).
Mais attention au diamètre de buse trop fin car une accumulation de charge peut boucher la buse. Les buse laiton vont également souffrir de l’abrasion de la charge
Bois/ Marbre/cuivre,….
Toutes ces charges sont de fines particules intégrées au filament pour modifier l’aspect, voir le touché de la matière.
Phosphorescent
Les filaments phosphorescents souvent appelés glow in the dark, vont absorber l’énergie de la lumière du jour et surtout des UV pour réémettre dans le noir. Il existe différentes couleurs de phosphorescences comme le bleu, le rouge, mais le plus connu et le plus performant est le vert. Selon la quantité et surtout la qualité des pigments utilisés par le fabricant de filament, la durée de phosphorescence sera plus ou moins longue. Les particules de phosphore étant très abrasives, les buse laiton s’use très vite avec ce genre de filament et il est alors recommandé d’utiliser des buses renforcées comme celle en acier.
Conduction Electrique ESD
Pour des applications électriques en environnement explosif, il peut être nécessaire d’utiliser des matières de conduction ou de dissipation électrique. Les matières plastiques étant intrinsèquement isolantes électriques, on ajoute généralement plus ou moins de noir de carbone conducteur selon les valeurs recherchées.
Carbone
La fibre de carbone apporte le meilleur rapport poids/rigidité. Elle permettra donc de rendre le filament beaucoup plus résistant aux contraintes mécaniques. Il permettra également d’augmenter sensiblement la tenue en température ainsi que les propriétés tribologiques (glissement/frottement) de votre pièce. A partir de 10% de fibre carbone, une matière devient également conductrice électrique.
Attention au terme conductrice d’électricité, dans ce cas on parle de l’électricité statique. En aucun cas vous n’aurez les propriétés conductrice lié au métaux comme le cuivre et par conséquent le courant continue type 12v ne sera pas conduit par ce type de filament.
Avantages :
- Très haute rigidité
- Conduction électrique
- Résistance en température
- Réduit fortement le gauchissement.
Inconvénients :
- Abrasif pour les buses/extrudeur
- Noir ou noir
- La fibre de carbone favorise la corrosion des métaux. Il faut égalent faire attention aux métaux utilisés pour l’assemblage.
- Prix
Verre
La fibre de verre est très utilisée comme renfort. Bien moins rigide que la fibre de carbone et plus dense, elle est surtout beaucoup moins onéreuse et moins fragile. Comme la fibre de carbone, elle permettra d’augmenter sensiblement la tenue en température et de la rigidité et résistance en contrainte.
Avantages :
- Haute rigidité
- Résistance en température
- Réduit le gauchissement.
Inconvénients :
- Abrasif pour les buses laiton
Difficile à imprimer avec une buse de diamètre de 0.4, il faut au minimum 0.5
Conclusion sur les différents type de filament de l’impression 3d
Comme vous l’avez vu, il y a beaucoup de matières et de qualité de filaments différents. Il faut donc bien prendre en compte les contraintes de vos applications pour sélectionner le filament le plus approprié. Et prendre en compte également vos capacités d’impression de matières techniques dans de bonnes conditions.
Tableau comparatif
Propriétés | Densité (g/cm³) | Tenue température HDT B @0,45 Mpa (°C) | Rigidité Module de Traction (Mpa) | Résistance mécanique en Traction (Mpa) | Résistance au choc Izod à 23°C J/m | Résistance au choc Izod à -30°C J/m |
PLA | 1,24 | 60 | 3 600 | 60 | 16 | 0 |
PETG | 1,23 | 77 | 1 800 | 34 | 70 | 38 (-40) |
PET | 1,33 | 63 | 2 000 | 0 | 20 | 0 |
ABS | 1,03 | 97 | 1 900 | 38 | 36 | 14 |
ASA | 1,07 | 101 | 2 300 | 48 | 17 | 4 |
HIPS | 1,04 | 90 | 1 800 | 24 | 12 | – |
PA6 | 1,14 | 170 | 3 100/1 000¹ | 90/45¹ | 5/NB¹ | 5/5¹ |
PA66 | 1,13 | 220 | 3 100/1 100¹ | 85/50¹ | 5,5/NB¹ | 6/6¹ |
PA12 | 1,01 | 115 | 1 100 | 40 | 7 | 6 |
PA12 GF30² | 1,24 | 175 | 6 500 | 120 | 23 | 21 |
PA12 CF30³ | 1,15 | 180 | 12 000 | 140 | 13 | 8 |
PC | 1,2 | 135 | 2 400 | 63 | 65 | 20 |
PP Copo | 0,9 | 80 | 1 100 | 27 | 13 | 4 |
PEEK | 1,3 | 240 | 3 800 | 96 | 9,1 | 0 |
PEI | 1,27 | 200 | 3 200 | 105 | 6 | 6 |
¹ : Valeurs après reprise d’humidité
² : Polyamide 12 chargé 30% Fibre de verre
³ : Polyamide 12 chargé 30% Fibre de carbone
Les valeurs indiquées sont des valeurs moyennes pour les matières généralement utilisées pour la fabrication des filaments.
Ces valeurs sont des mesures sur pièces injectées. Les propriétés en impression seront donc souvent inférieures et dépendantes des conditions d’impressions.
Article réalisé par CedricPlast & Cédric Muller pour Nozzler.