Bonjour les makers et les makeuses !
Après maintenant 6 mois d’utilisation de cette voron 2.4R2, il est temps de faire un retour sur l’utilisation de celle-ci.
Au vu du titre de l’article, vous allez me dire que j’ai pu en faire des tests et des impressions avec cette imprimante !
Et bien oui ! Beaucoup !
J’ai même poussé au point que j’ai cassé pas mal de pièces, notamment des cartographer, la hotend Dragon de chez phaetus et même le tapis chauffant de 650W.
Je remercie d’ailleurs au passage la SAV de Siboor qui m’a très bien accompagné alors qu’il n’y était pas obligé. Je rappelle que cette machine ne m’a pas été envoyé pour test, que c’est un achat personnel, et que donc les casses que j’ai faites en poussant la machine ne rentraient absolument pas dans les conditions de garantie.
Cet article, comme vous pouvez vous en douter, ne sera pas aussi long et détaillé que les précédents.
Il s’agit surtout d’un retour d’expérience sur l’usage d’une machine que je juge “avancée”, les vorons n’étant pas à mettre entre toutes les mains.
Dernière précision, les impressions que vous verrez tout au long de cet article sont dans l’ordre chronologique de l’utilisation de la machine. Les 1ère remontent donc à il y a un peu plus de 6 mois avec une machine fraichement monté, alors que les dernières sont d’il y a quelques jours, avant l’écriture de cet article avec tout un tas de réglages faits au fur et à mesure des tests.
Commençons !
Le slicer utilisé est OrcaSlicer.
Comme tout départ avec une machine, il faut régler certains paramètres importants concernant l’extrusion. Je ne parle pas des réglages firmware (rotation distance) mais plutôt de la rétractation, distance et vitesse.
Je pars du profil de base fourni par Siboor et utilise du PLA Gris de chez Eryone.
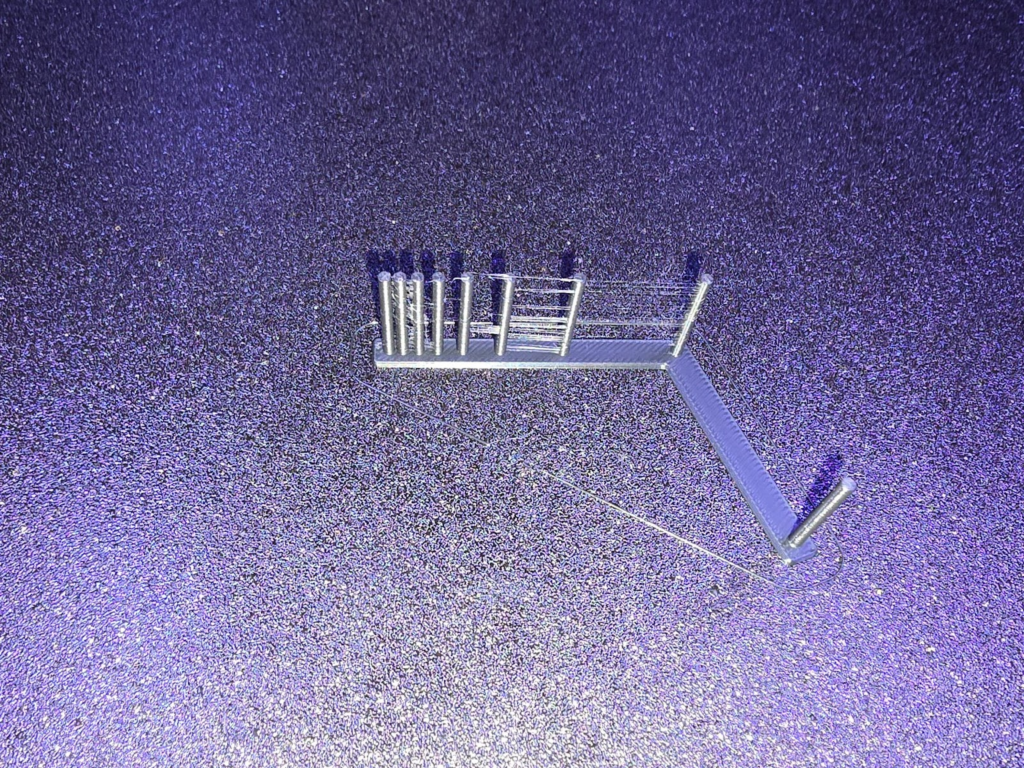
Quelques réglages s’imposent ! Une fois ceux-ci faits, je lance un “torture test”.
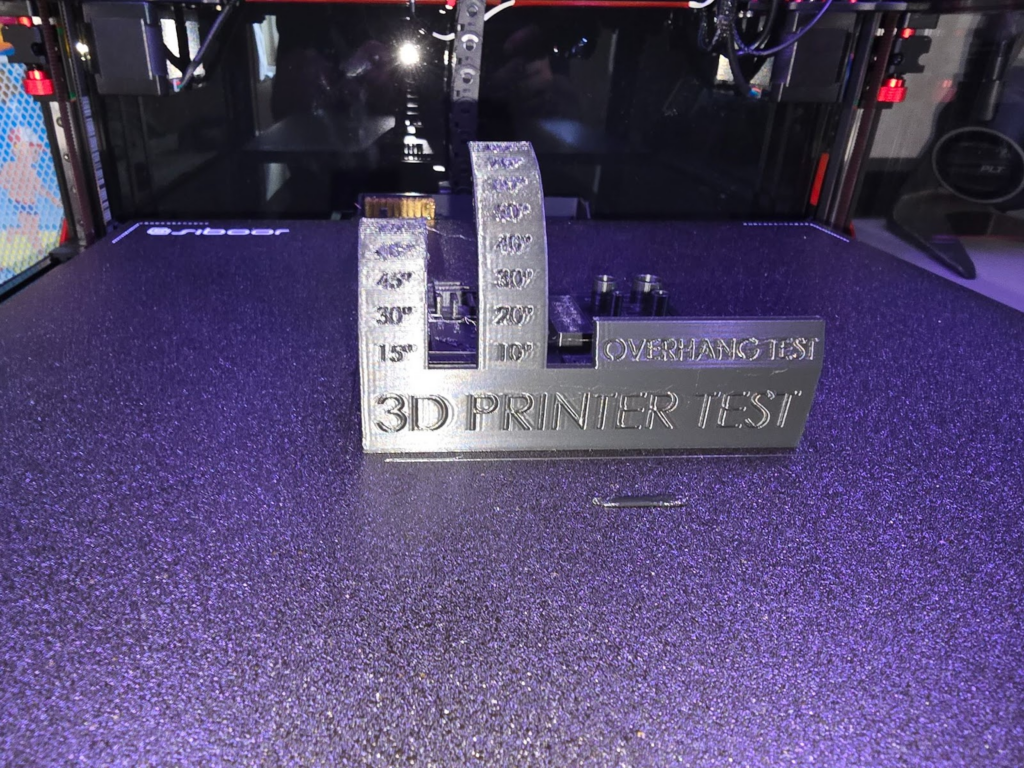

Il y a encore des réglages à effectuer côté “oozing”, qui peuvent venir de plusieurs paramètres (température, hygrométrie du filament, etc ) mais par contre, côté “overhang”, c’est plutôt pas mal (même plutôt bien) pour une machine stock !
Pour éliminer le facteur hydrométrique, je relance le test de rétractation mais cette fois avec du PLA Marbre de chez Evryone qui a passé 8h au séchoir.
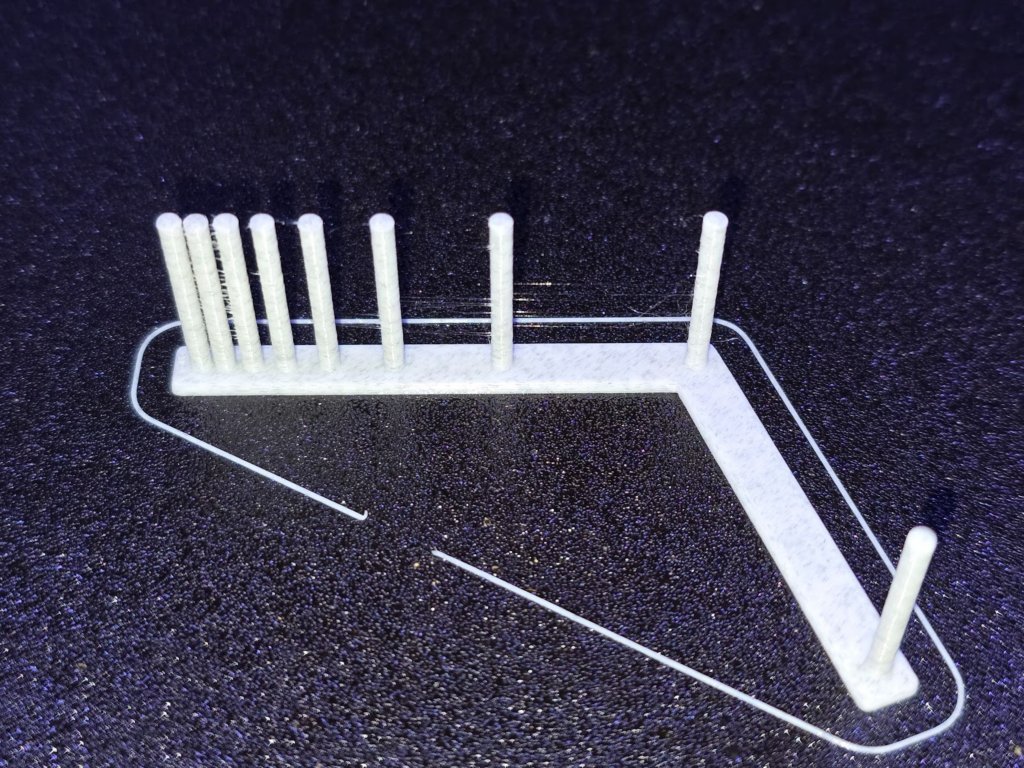
Moralité, toujours s’assurer d’avoir un filament bien sec avant de valider des paramètres d’impression ! Ici je valide donc les valeurs utilisées lors du stress test.
Pour m’assurer à nouveau que tout est correct, je vais lancer un autre type de “torture test” https://www.printables.com/model/428481-torture-test-trophy
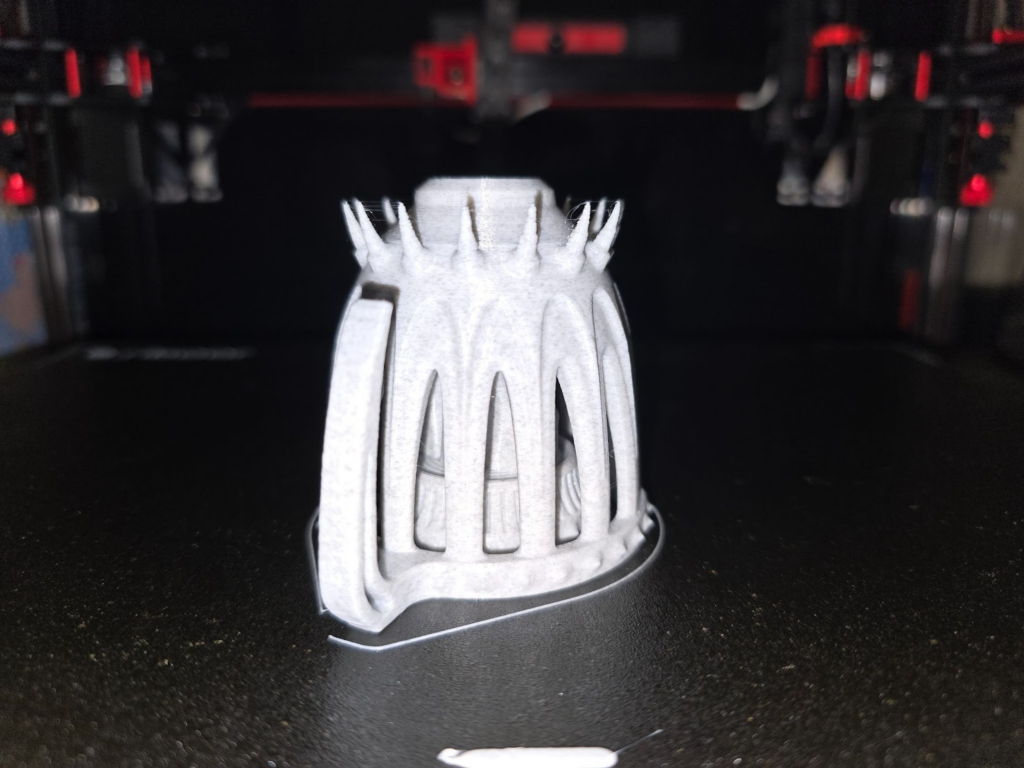
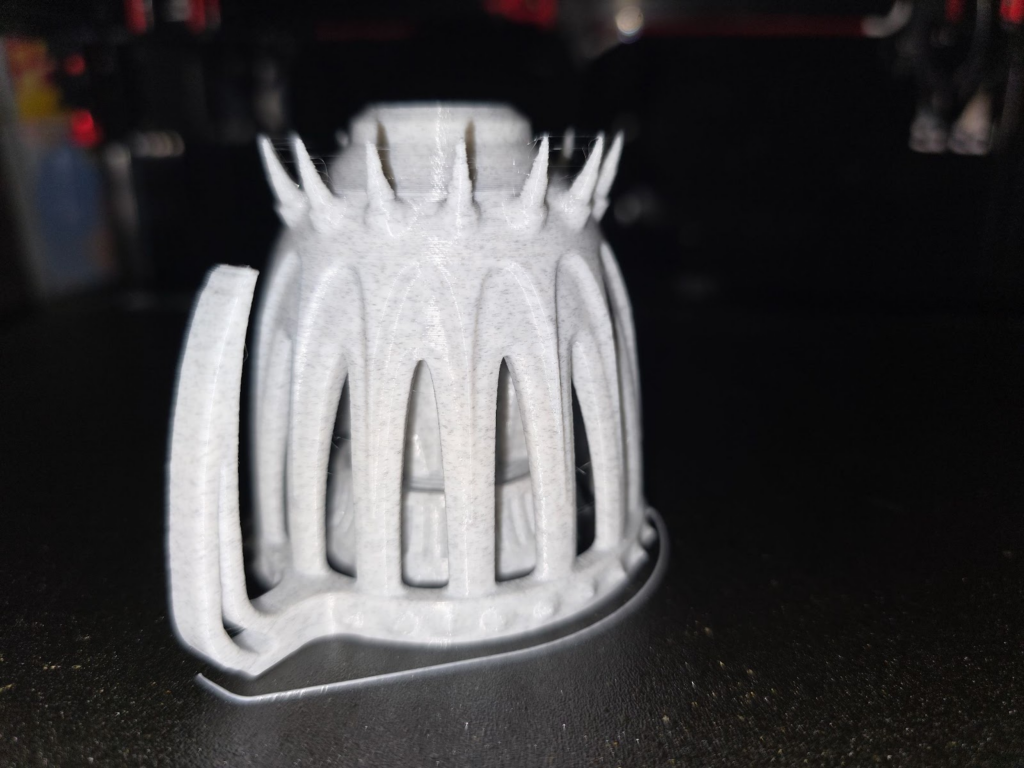
La qualité est très très correcte ! Surtout pour une machine full DIY. Certes c’est une voron mais comme toutes machines DIY, la qualité des composants a un impact mais la qualité du montage aussi ! Je suis donc content d’avoir pris le temps et d’avoir été minutieux sur le montage de cette voron 2.4R2.
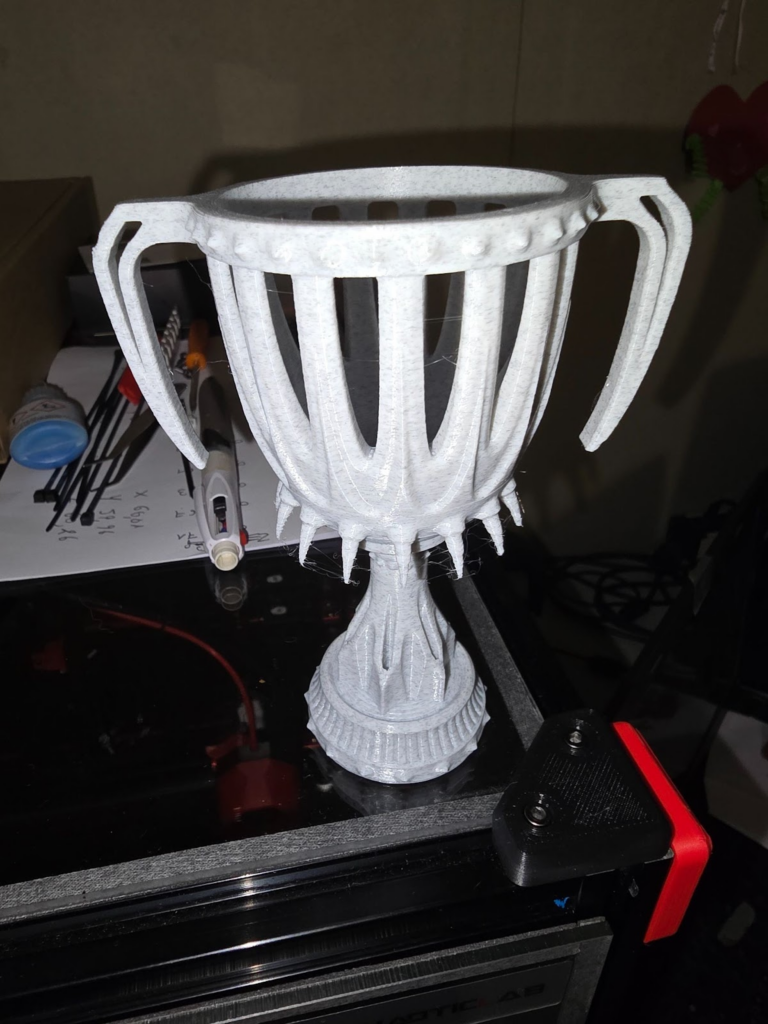
Il est temps de passer à des choses plus sérieuses et d’imprimer autre chose que du PLA, d’autant plus que cette imprimante est en caisson fermé.
Il s’agit donc d’ABS de chez Capifil et de pièces pour l’ERCFv2 (MMU)
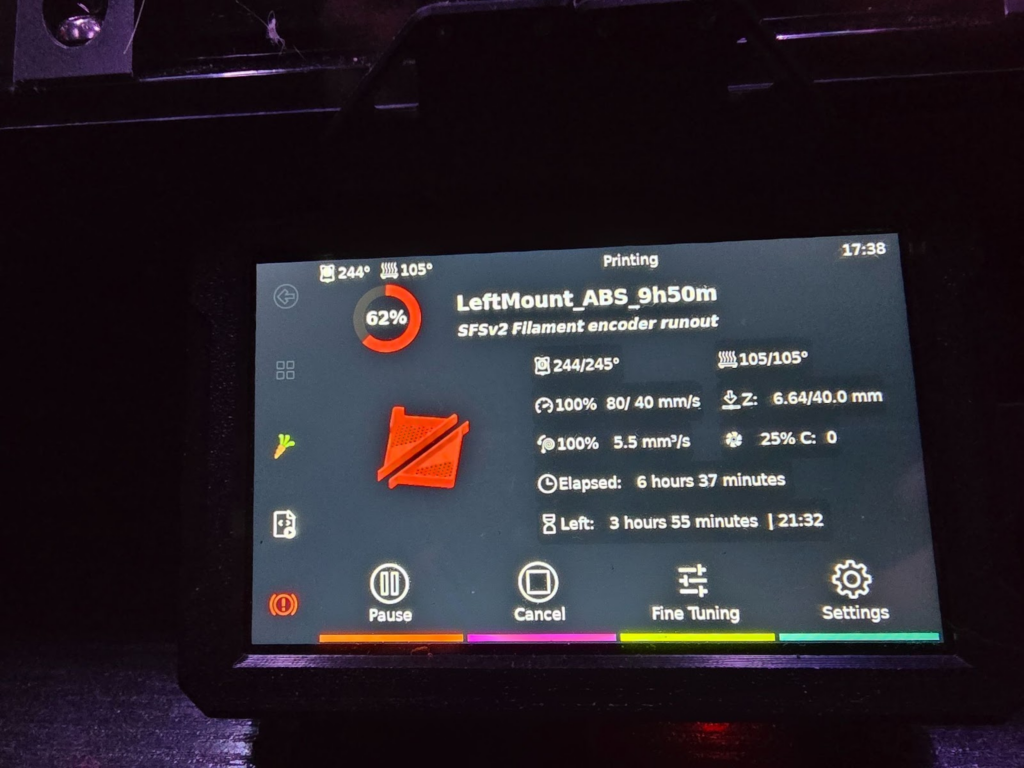
Aucun warping pendant l’impression. Le plateau ‘pro’ texturé aide énormément à l’accroche aussi.
Aucun besoin de colle ou autre produit d’accroche.
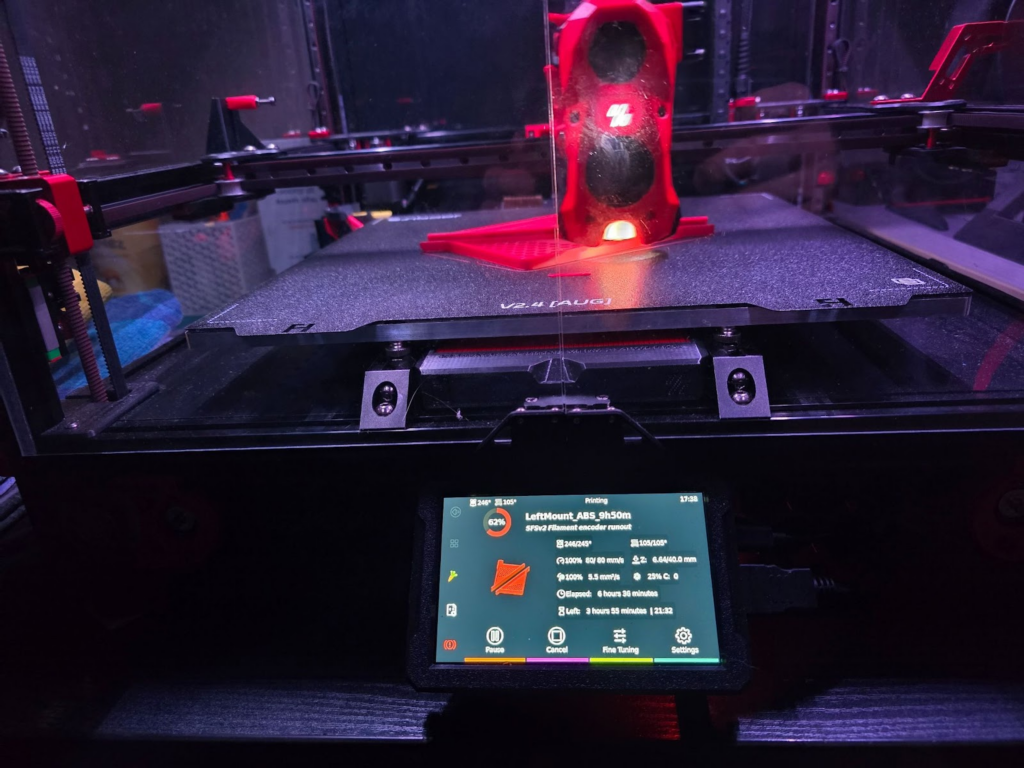
Voici le résultat une fois en place :
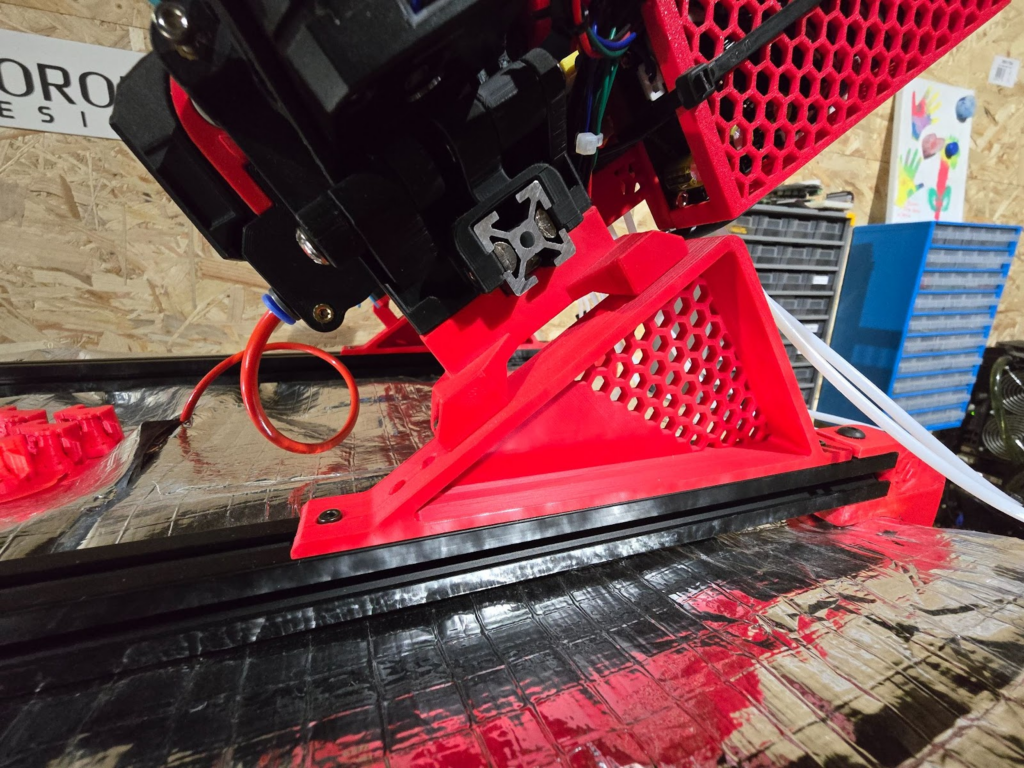
Après l’ABS, je vais faire encore plus technique. Dans l’intervalle j’ai reçu une bobine de PA12-CF de chez Extrudr (le test ici).
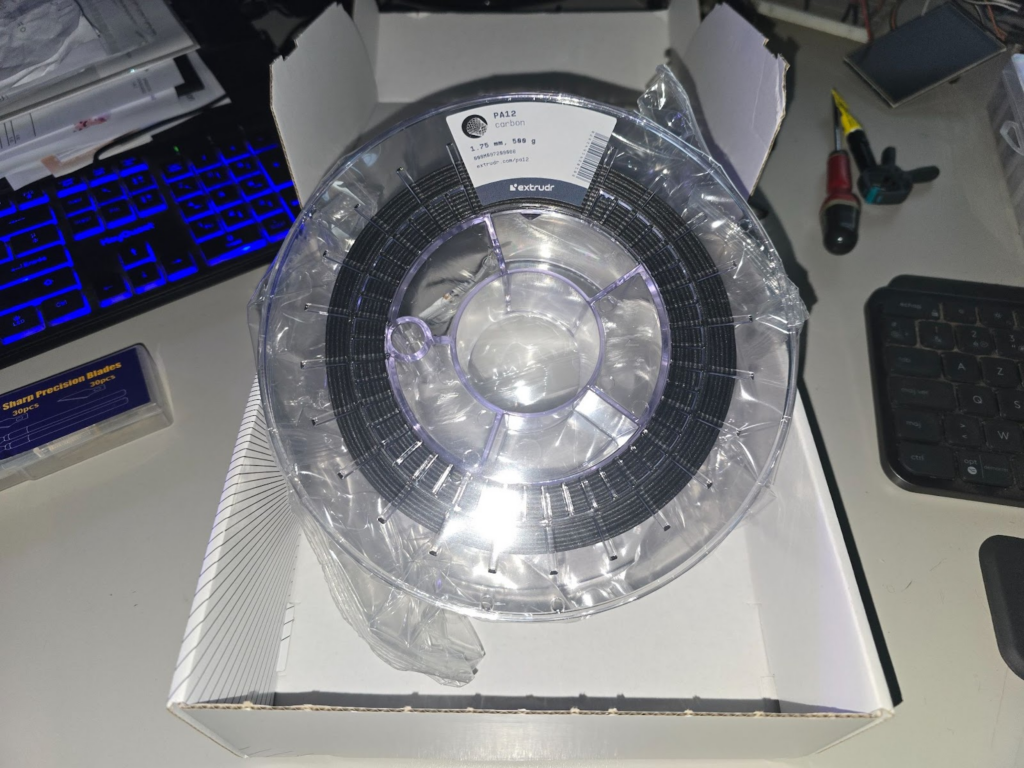
Le PA12 (Nylon) étant très technique, j’ai bien sûr réalisé des tests et des petites pièces au début. Une fois réglé, j’ai lancé l’impression d’une pièce large, ce qui est le pire pour le nylon car très sujet au warping.
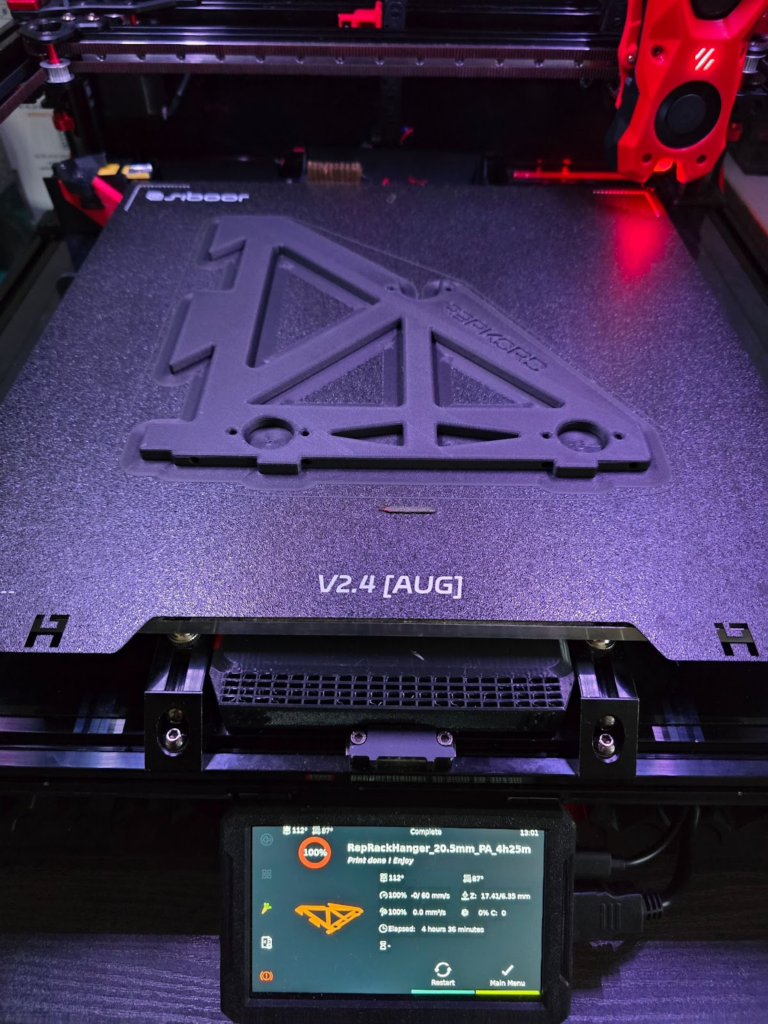
Aucun problème. Bon, j’ai quand même mis un brim pour vraiment être sur !
Vous verrez un peu plus tard à quoi sert cette pièce.
Dernier test technique, et pas des moindres : du PP-CF de chez Eryone. Le défi ici c’est pas tant l’impression du filament en lui-même mais plutôt l’adhérence. En effet le PolyPropylène n’est pas vraiment difficile à imprimer, mais il a la particularité de n’adhérer qu’à lui-même ou à un composite de lui-même.
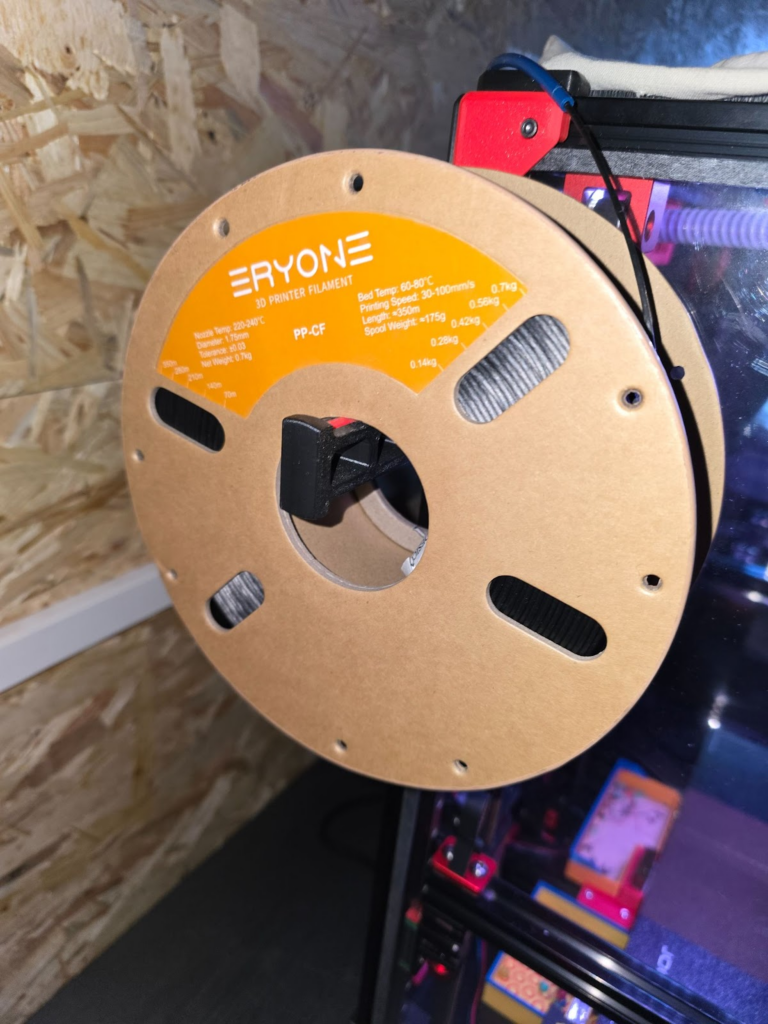
Donc je vous passe les fails, mais le filament ne tient pas du tout sur le plateau d’origine. Il existe plein de solutions mais celle que j’ai retenue et la plus facile à mettre en œuvre, c’est le scotch marron utilisé pour faire les cartons de déménagement. En effet, celui-ci est composé de polypropylène.
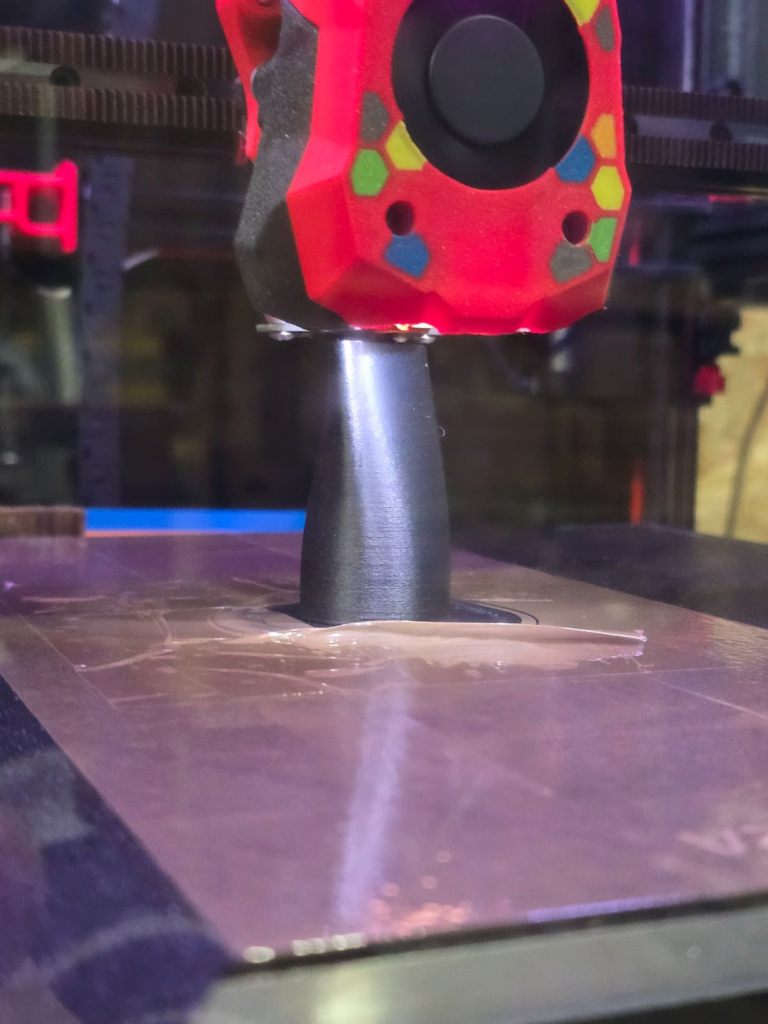
Bon par contre ça tire fort sur le scotch, donc bien surveiller et s’assurer que celui-ci tient bien au plateau. (ici l’impression n’a pu aller au bout, la pièce avait trop de balan)
Pour finir, j’ai voulu tester le débit avec la hotend dragon de chez Phaetus. Pour cela j’ai monté une buse de 1mm.
L’impression a été réalisée en PETG transparent de chez Gratkit, mode vase avec une hauteur de couche de 0.5mm et une vitesse de 30mm/s.
Le résultat parle de lui même :
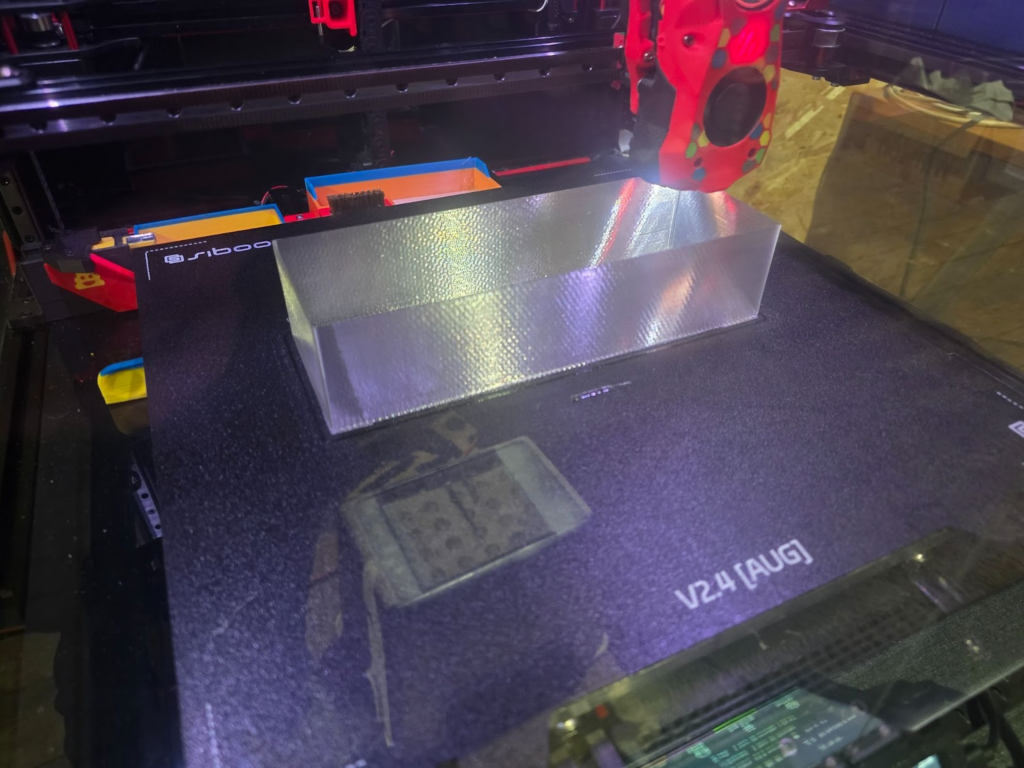
C’est assez bluffant !
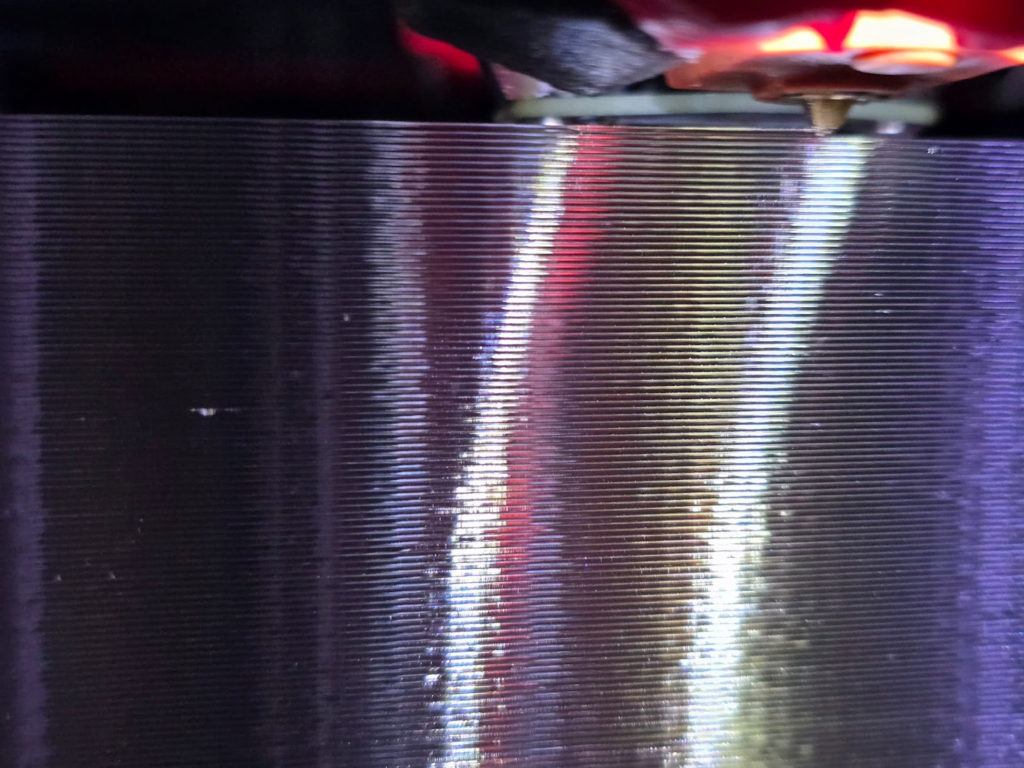
Voilà, j’en ai fini avec toutes les impressions test.
Après tout cela, j’ai principalement utilisé la machine pour sa propre amélioration et faire un support latéral de 8 bobines de 1Kilo. Pourquoi ? parce j’ai équipé la machine de l’ERCFv2 (un MMU) à 8 entrées.
Voici ce que cela donne.
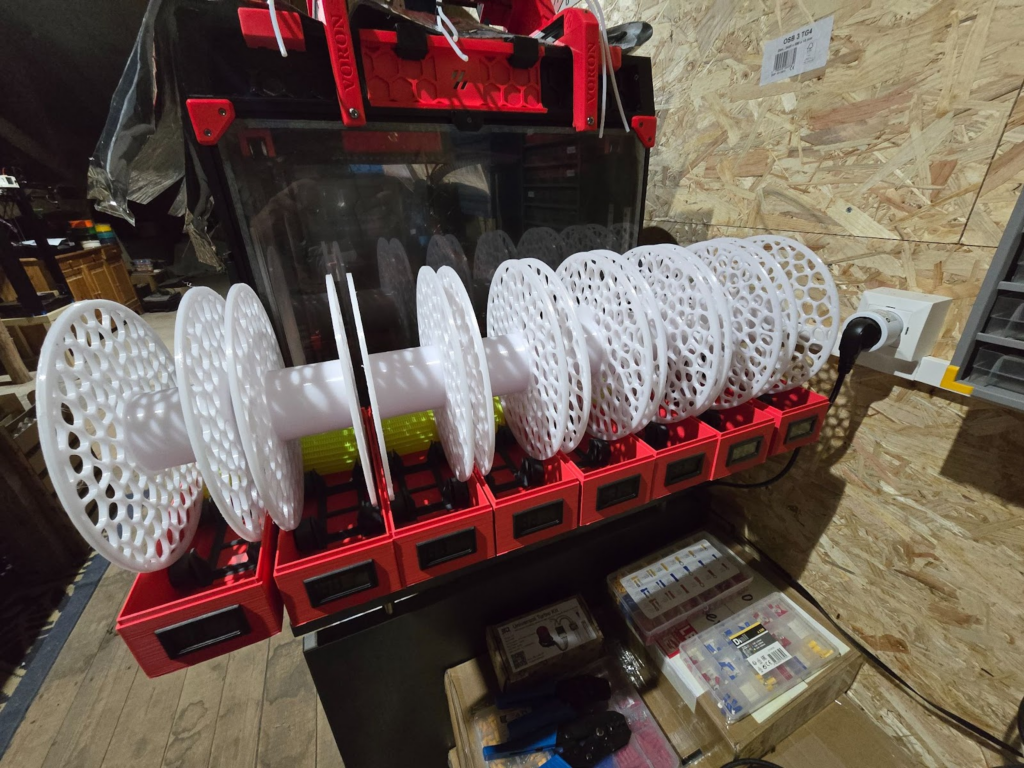
Le design est un remix que j’ai fait à partir du projet RepRack :
https://www.printables.com/model/129024-reprack-open-source-spool-holder-and-storage-syste
Vous vous souvenez de la pièce en PA12-CF ? Et bien voici son utilité :
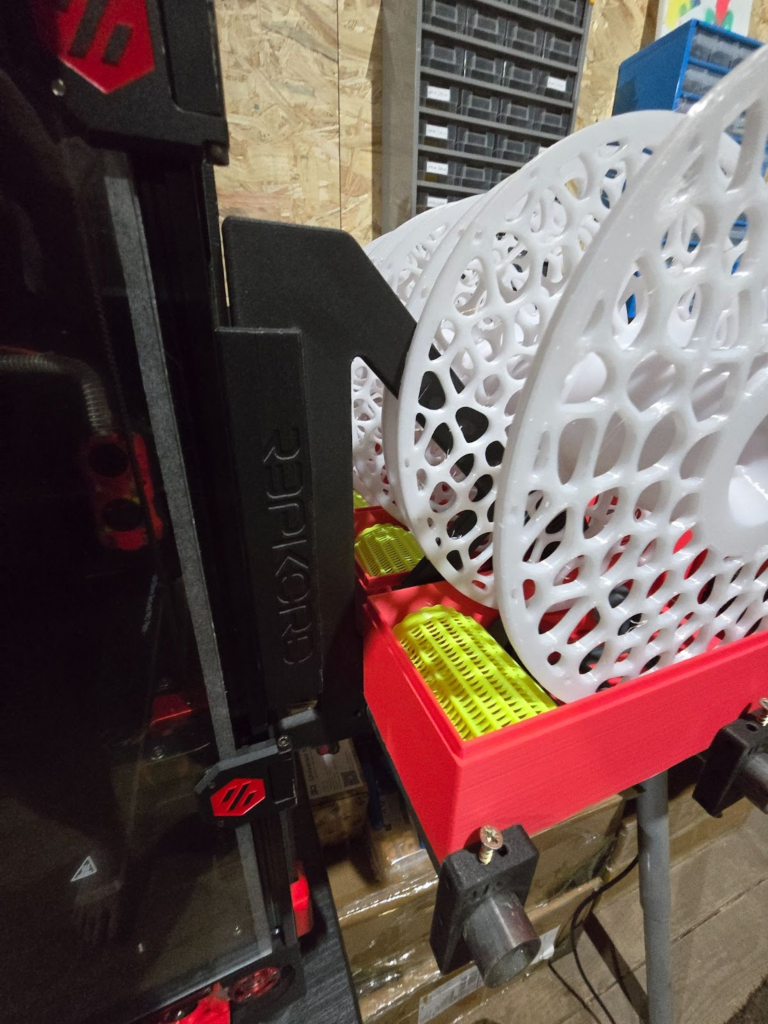
c’est l’équerre qui supporte tout le poids.
Les boitiers jaunes que vous voyez dedans sont des réservoirs pour accueillir du disséquant régénérable. Imprimé en PLA et en mode vase (j’ai aussi fait des verts 😛) :
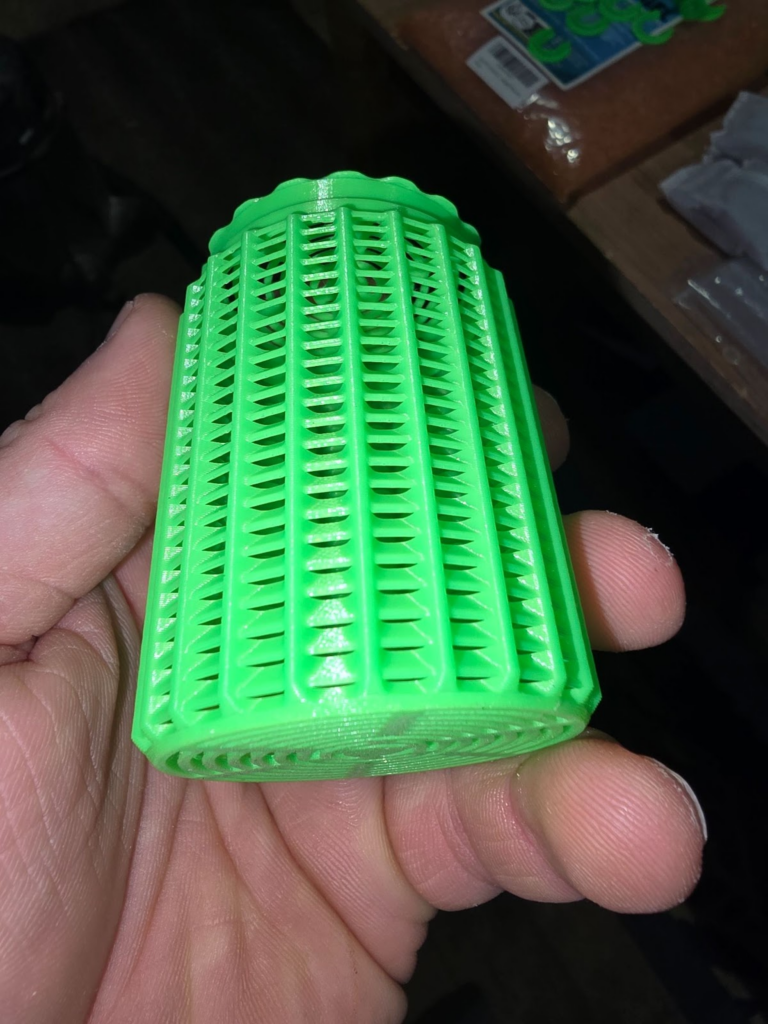
Quant aux bobines, elles ont été imprimées en PETG blanc de chez sunlu :
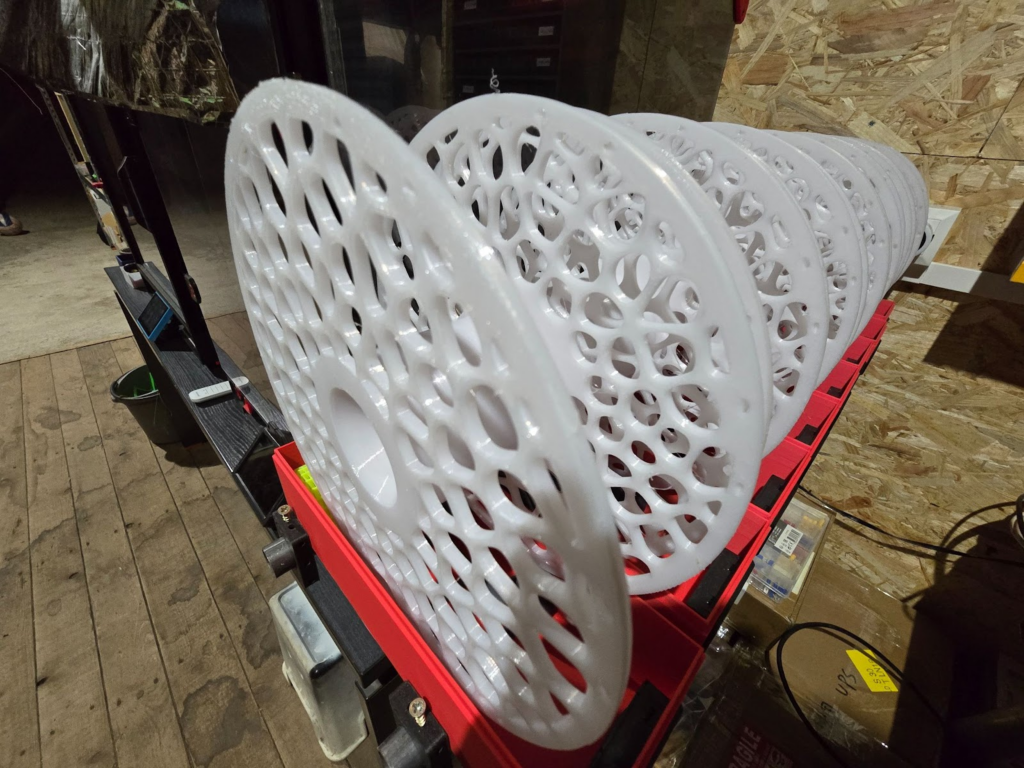
Pour ceux qui auront reconnu, les bobines viennent d’un des systèmes de ‘respooling’ ou ‘Spool rewinder’ que l’on trouve sur makerworld.
Voici le lien de la bobine réutilisable :
https://makerworld.com/fr/models/565057-cell-spool-bambu-lab-ams-ok#profileId-484654
Je fais ce système car j’ai beaucoup de soucis (comme de nombreuses personnes) avec les bobines en carton. L’idée en soit des bobines en carton n’est pas mauvaise mais elle amène pas mal de soucis. En effet c’est un gros capteur d’humidité, humidité qui est ensuite transmise au filament. De plus, la bobine a tendance à se déformer avec l’utilisation de support de type roller (comme les AMS).
Du coup, la suite logique, c’est donc la réalisation du ‘respooller’ en lui-même.
Voici les liens des STL utilisés :
https://makerworld.com/fr/models/561571-cell-spool-winder#profileId-481024
https://makerworld.com/fr/models/604481-spool-winder-split-base#profileId-527156
Et la réalisation intégralement en ABS :
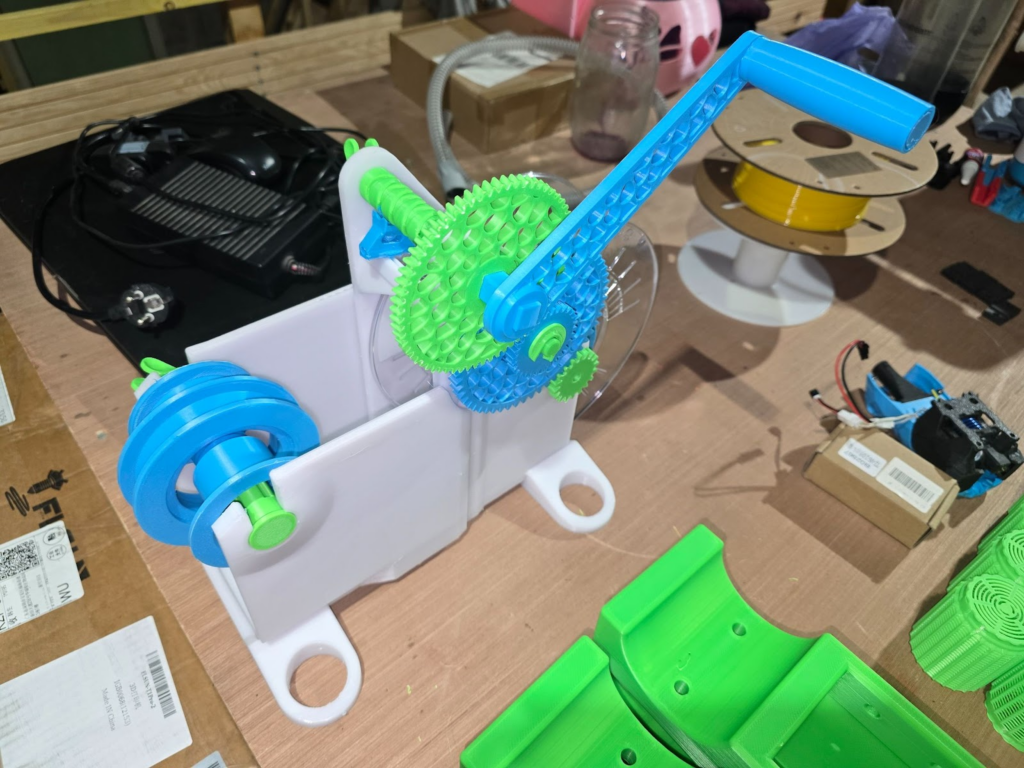
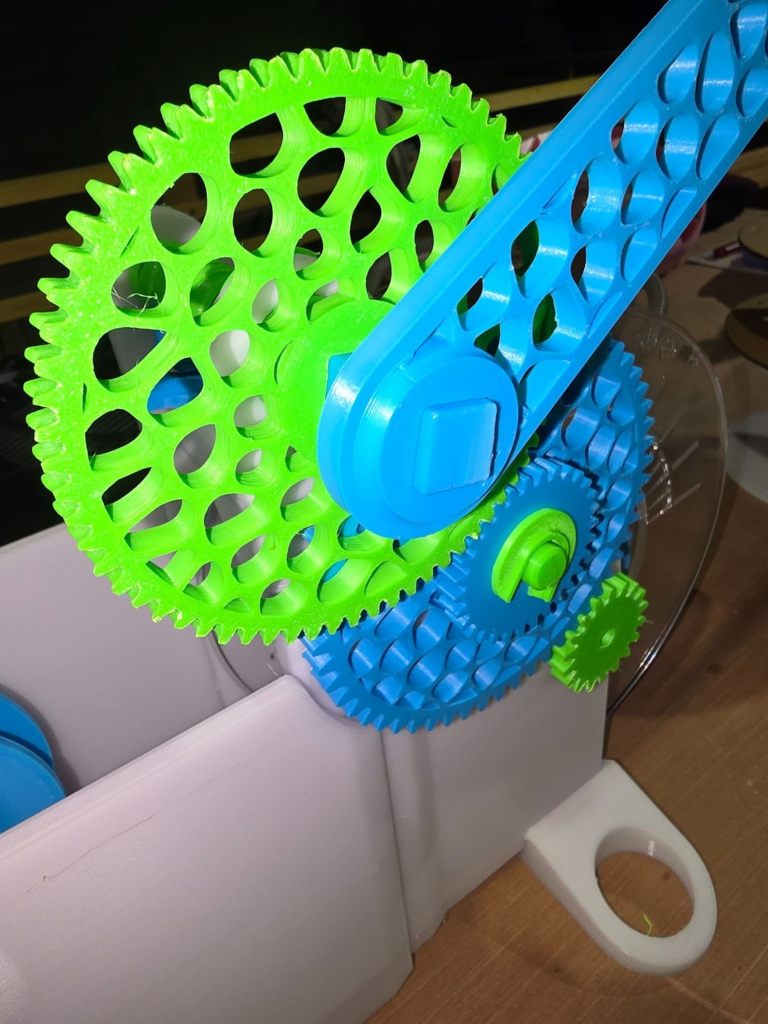
Aucun souci, tout s’emboite parfaitement.
Dernière réalisation, une pièce que j’ai modélisée pour la construction d’une serre, imprimée aussi en ABS.
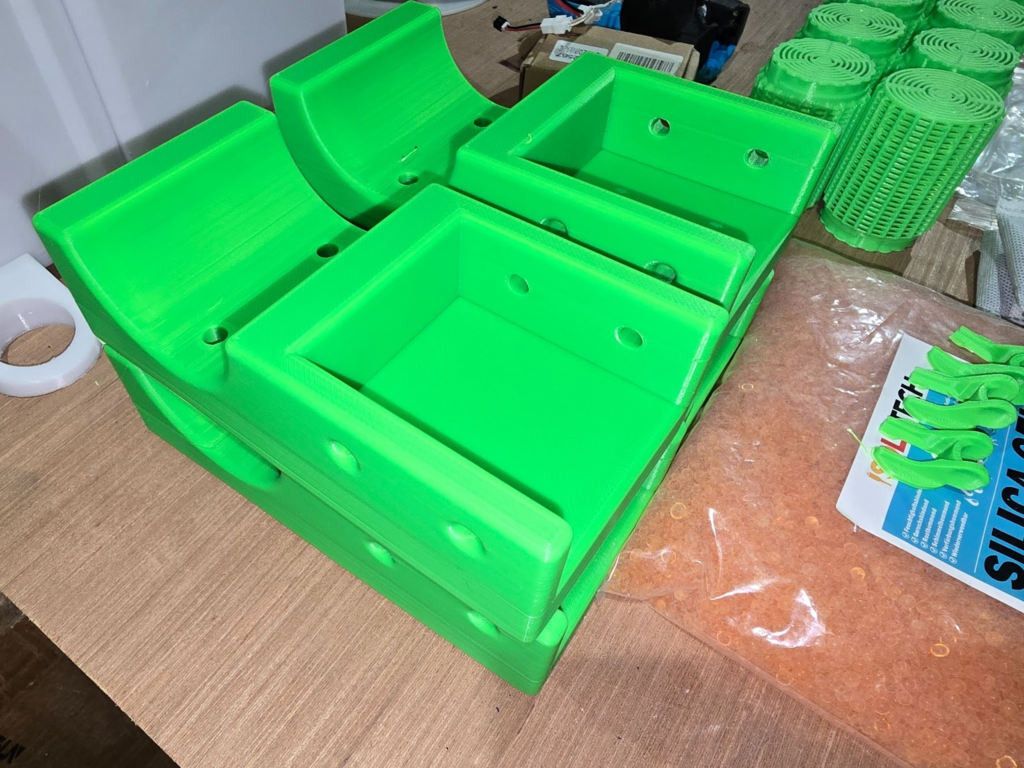
Aucun souci structurel, pas de warping ni de délamination !
Conclusion :
Vous imaginez bien que je ne vais pas vous dire que cette machine n’est pas terrible, bien au contraire!
Cependant, il y a des mais !
Vous avez pu le voir, la qualité des pièces produites est juste impeccable. Même avec l’ABS, qui est pourtant réputé pour être difficile à imprimer, à cause de son fort taux de retrait, les côtes sont respectées.
Cette machine est extrêmement polyvalente mais aussi très technique ! Ne cherchez pas dans cette machine une bête de performance, ça n’en est pas une. En tout cas, pas en l’état.
Cette machine correspond exactement à ce que je recherchais. Une imprimante me permettant d’imprimer toutes sortes de filaments, avec un gros volume d’impression et une excellente précision.
Les ‘mais’ maintenant !
Ce n’est pas une imprimante que l’on peut mettre entre toutes les mains.
Déjà il faut la monter entièrement, ce qui en soit est toute une aventure.
De plus la qualité du montage, donc votre assiduité et minutie à la monter correctement, influera directement sur la qualité d’impression obtenue.
Et enfin, il faut comprendre toute la mécanique derrière (QGL, Cartographer avec mesh et touch, etc etc) pour configurer les fichiers klipper correctement et configurer aussi votre slicer. Ceci afin d’en tirer tout le potentiel qu’elle a à offrir.
A titre personnel, j’ai mis environ 3 à 4 semaines à la monter, environ 10 jour à comprendre et faire les fichier de configuration et pratiquement 3 mois à faire des tests, des impressions et des réglages plus ou moins fin jusqu’à ce que l’imprimante réponde parfaitement à mon besoin (bon je suis un tantinet perfectionniste mais bon …)
Est ce que je recommande cette imprimante : Bien sur ! Elle est géniale !
Est ce qu’un débutant peut commencer avec ? Franchement non, ou alors avoir de solides connaissances dans le domaine, ce qui est un peu paradoxal si on débute.
Est ce que cette imprimante vaut son prix ? Franchement oui ! La qualité des composants ainsi que des pièces imprimées en ABS sont très bonnes.
Et enfin est ce que cette imprimante fonctionne telle quelle ou faut t’il faire des améliorations ?
Et bien cela dépend de ce que vous voulez en faire. Personnellement j’ai fait énormément d’améliorations dessus, ce qui sera d’ailleurs le sujet de la partie 5, mais vous pouvez très bien l’utiliser ainsi !
Voila, après cette conclusion un peu volumineuse qui finit cette partie 4, je vous donne donc rendez vous pour la dernière partie qui concerne toutes les améliorations que j’ai effectuées pour rendre cette imprimante encore plus performante !
A Bientôt.
Super retour Cédric, je l’attendais avec impatience. Je suis en train de monter la mienne (de chez Siboor également) 🙂 J’ai hâte d’arriver au bout …
PS : Lors du montage, tu avais fais une remarque sur les poulies fixées sur les moteurs de l’axe z car les vis ne se prenaient pas sur le méplat de l’axe du moteur. En inversant le sens de montage de la poulie crantée, cela règle le problème … A +
merci beaucoup !
ce genre de commentaire est inspirant pour nous. j’espère que ta 2.4R2 te donnera autant de satisfaction que la miennes.