Bonjour les makers et les makeuses !
Voici la suite de la découverte de la Voron 2.4 R2.
Avant de commencer, je remets la thématique de l’enchaînement des articles :
- Partie 1 – Présentation du kit Voron 2.4 de chez Siboor
- Partie 2 – L’assemblage
- Partie 3 – La configuration Klipper et le calibrage
- Partie 4 – Les tests, impressions et conclusion (À venir )
- Partie 5 – Les upgrade (À venir)
Si vous ne savez pas ce qu’est Voron, ou un kit Voron et que vous n’avez pas lu la partie 1, je vous conseille de le faire, car c’est la suite directe !
Si en revanche vous connaissez, ou que vous vous en moquez, alors pour pouvez continuer 😀.
Donc comme vous vous en doutez, ici on rentre dans le vif du sujet, l’assemblage de la bête !
Pour cela, Siboor met à disposition, sur son github, une série de pdf qui sont les instructions de montage annotées pour correspondre à leur kit:
https://github.com/Lzhikai/SIBOOR-Voron-2.4-AUG/tree/main/Manual
Il y a aussi un pdf qui est une compilation des instructions ChaoticLab pour les Kit CNC, mais j’ai préféré prendre les pdf séparés directement sur leur github:
https://github.com/Chaoticlab/Voron-2.4-CNC-Parts-Kit-V2.0
Le montage va être réalisé dans l’ordre du manuel:
- Le châssis
- Les Rails linéaires Z
- La plaque de fond et les rails DIN (pour l’électronique)
- Les supports des moteurs Z (Kit CNC Chaoticlab)
- Les tensionneurs de courroie Z (Kit CNC Chaoticlab)
- Le plateau chauffant
- Le portique (ou gantry) qui comprend aussi
- Le support des moteurs A/B CNC de Chaoticlab
- Le kit de jointure X/Y CNC de Chaoticlab
- Le kit de tensionneur X/Y CNC de Chaoticlab
- Le montage du portique sur les axes Z avec le kit de jointure Z CNC de Chaoticlab
- La tête Stealthburner
- L’électronique et le câblage
- Les parties décoratives et les ventilateurs de l’électronique
- Les panneaux en polycarbonate
- L’extracteur d’air, pour le contrôle de température de la chambre
- Le module Nevermore
Je vous préviens, étant donné la bête, l’article va être long, dans le sens où il va y avoir beaucoup de photos du montage.
Le châssis :
Préparation des profilés et assemblage
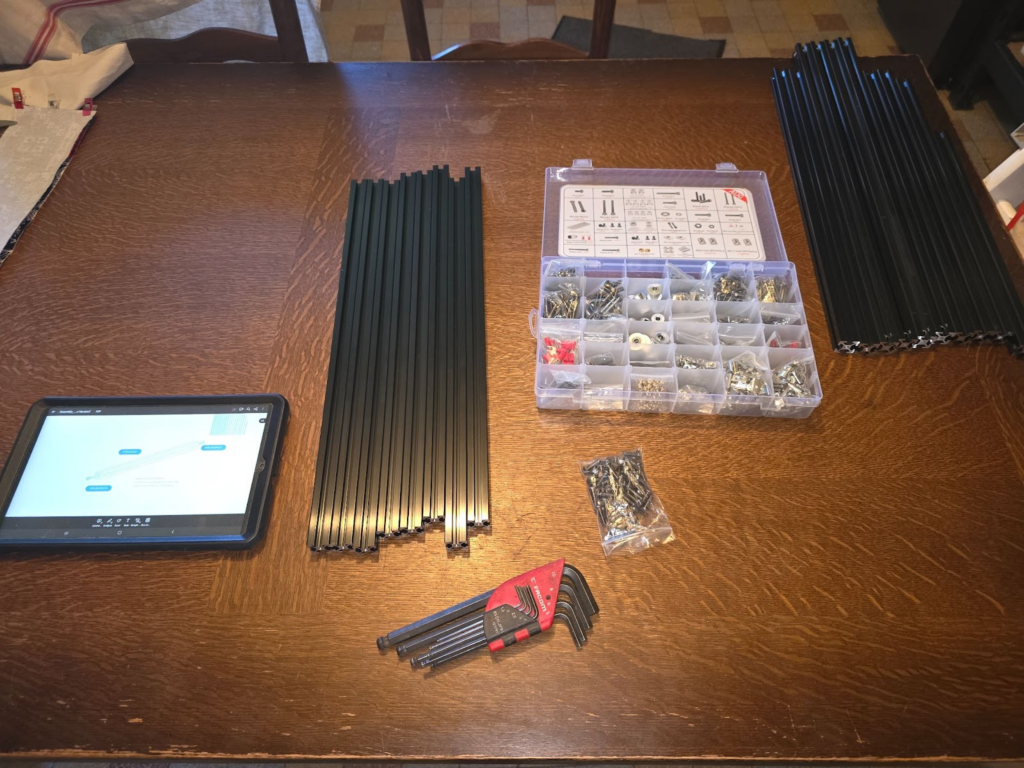
Après assemblage, mise en place des traverses. Etant donné que la machine sera prévue pour de grandes vitesses (300 mm/s en impression et 600mm/s en déplacement) ainsi que de fortes accélérations (plus de 20.000 mm/s²), je conseille fortement d’utiliser le frein filet bleu (pas le rouge, ou sinon c’est quasi indémontable) pour éviter que tout ne se desserre avec les vibrations de la machine.
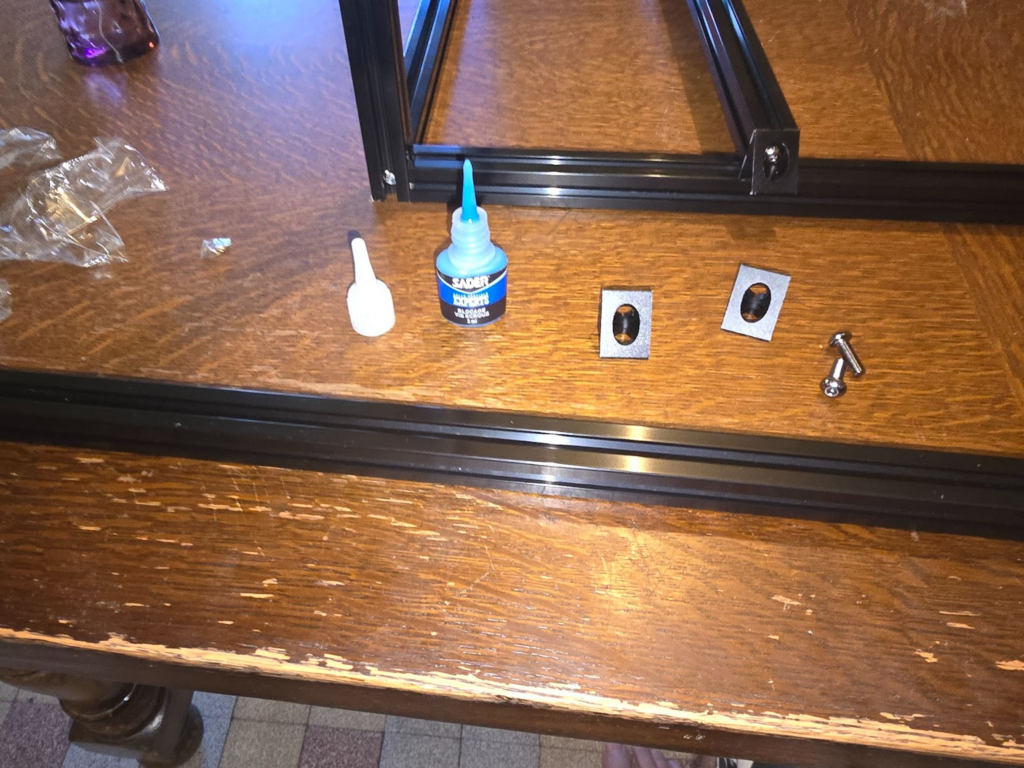
Il faut bien vérifier l’alignement et que tout soit d’équerre !
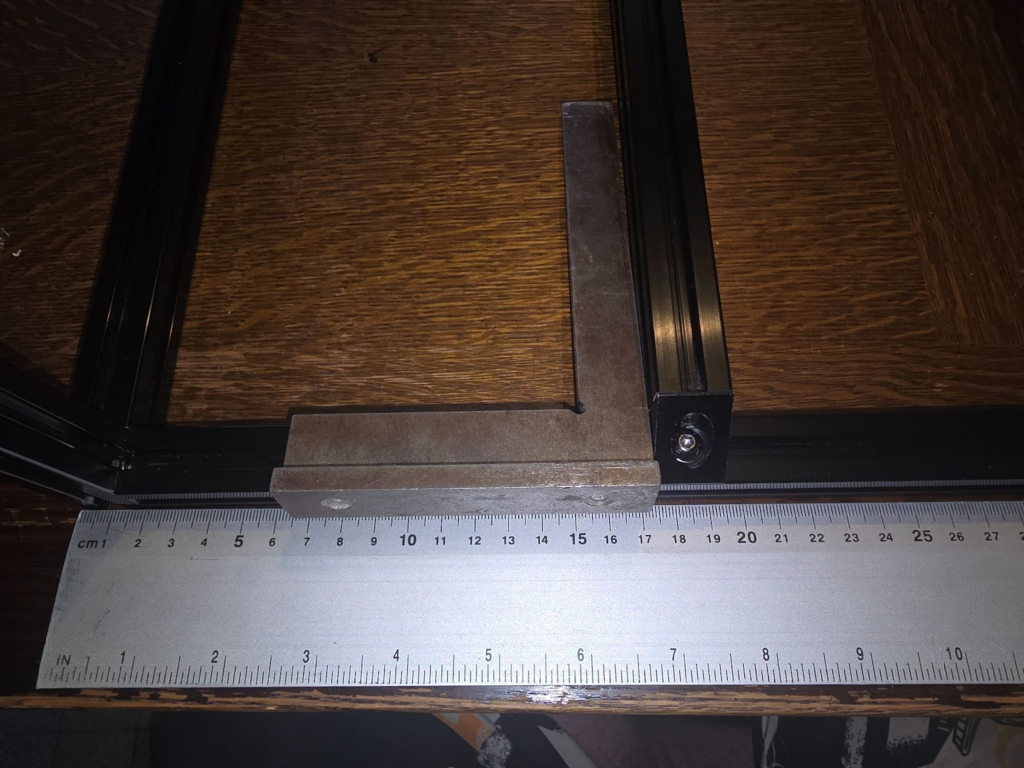
Châssis Terminé !
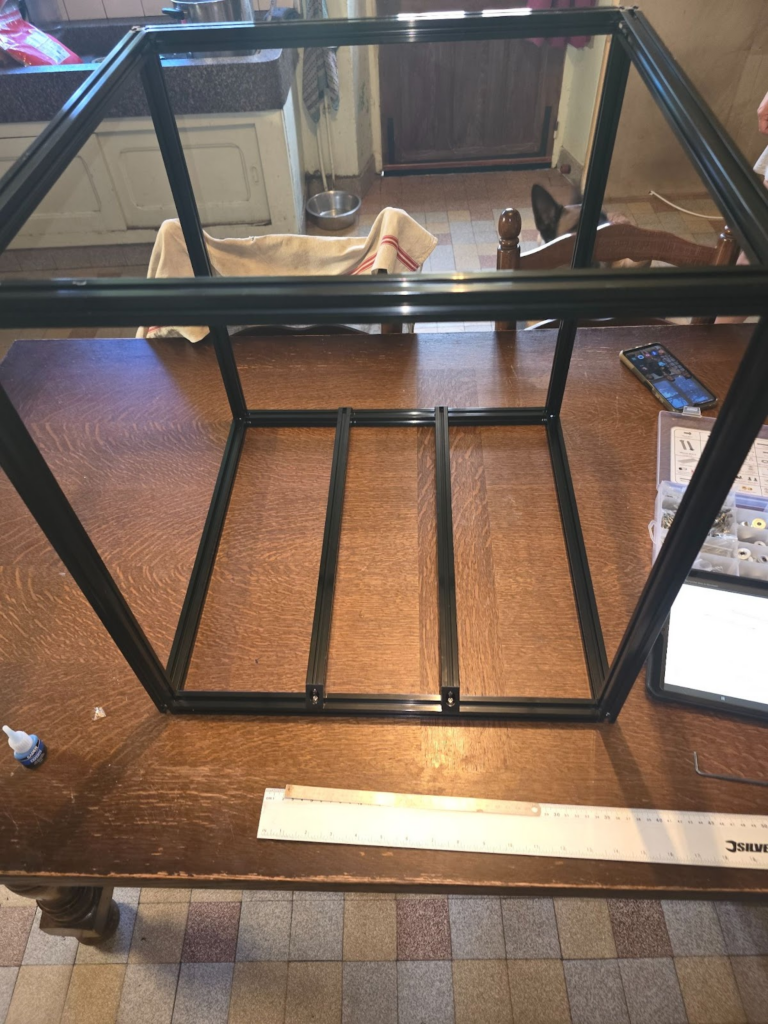
Les Rails linéaires Z
Rien de bien compliqué, bien suivre les instructions de positionnement, en utilisant les gabarits de centrage fournis, avant de serrer les vis et mettre du frein filet sur les vis.
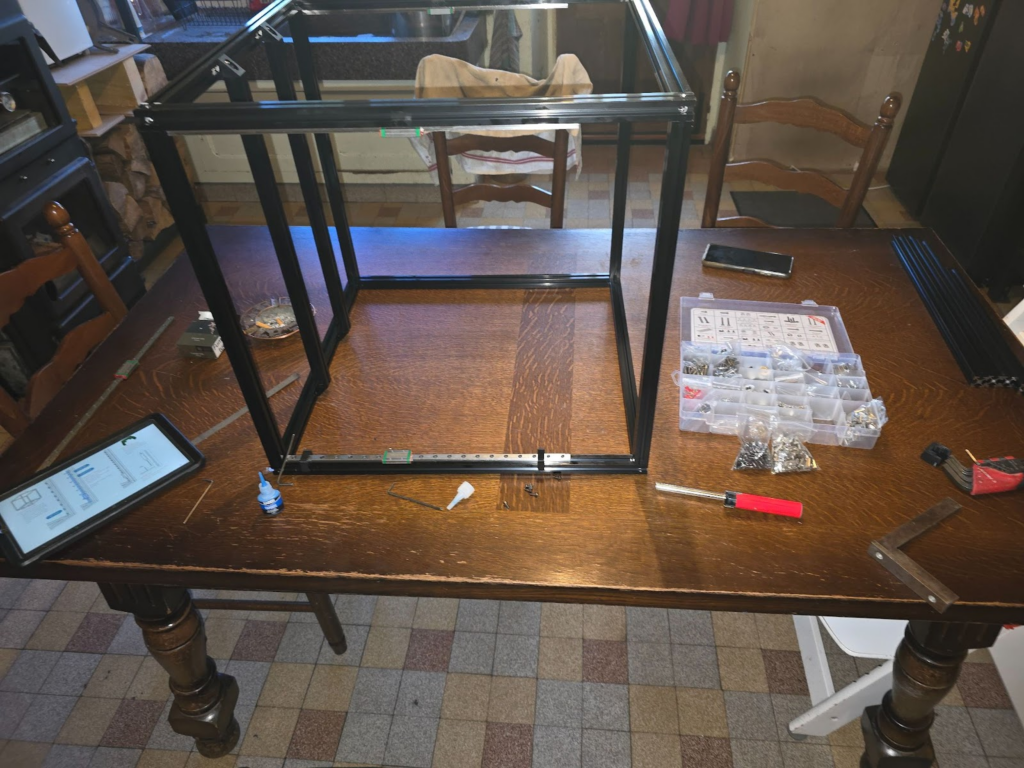
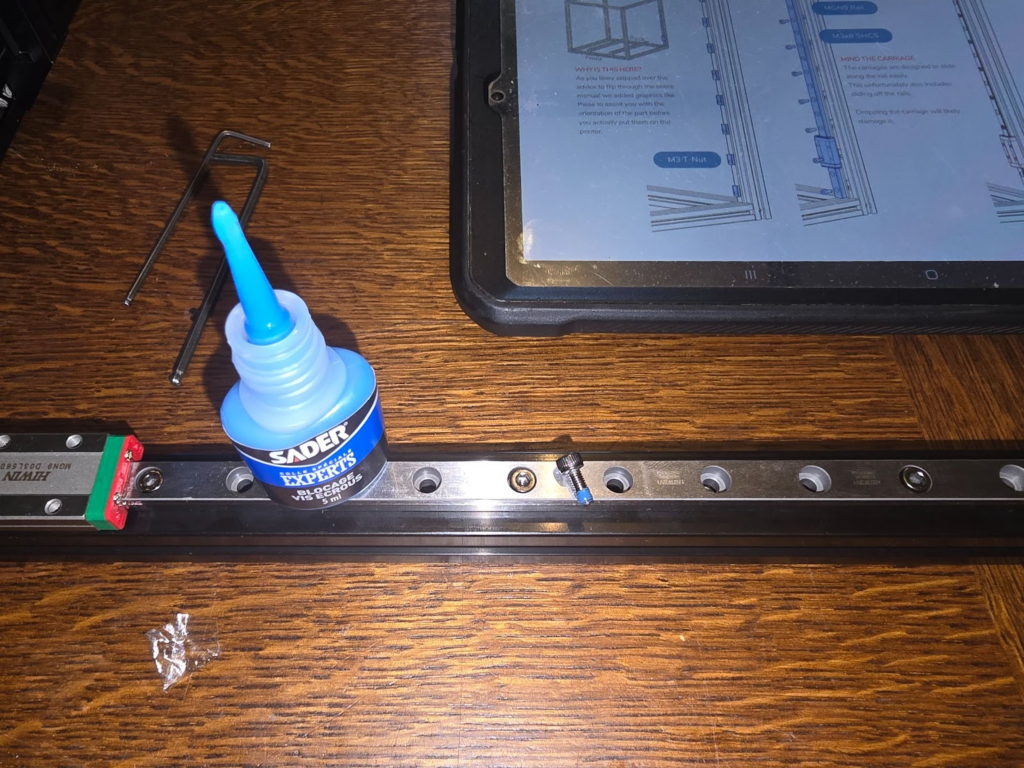
Une fois les 4 rails posés, je passe à la suite.
La plaque de fond et les rails DIN
Partie très simple: juste du positionnement !
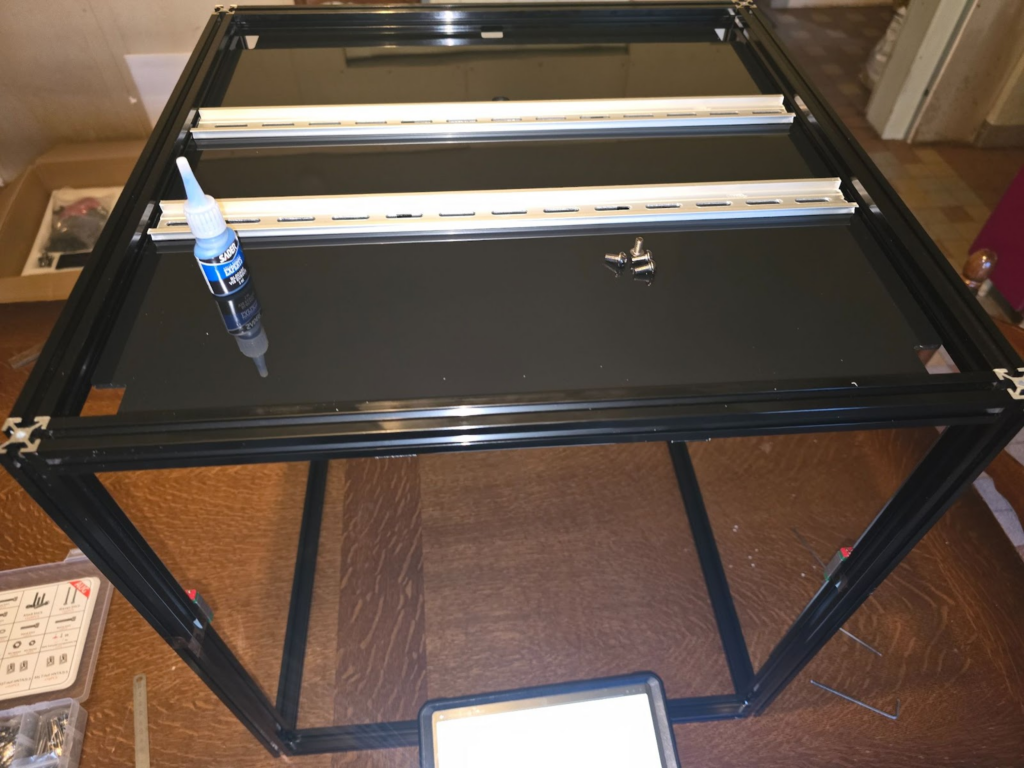
Les support des moteurs Z (Kit CNC Chaoticlab)
Cette partie est importante et nécessite d’être attentif et minutieux. Comme il s’agit du kit de chez Chaoticlab, je passe la section dédiée dans la documentation Siboor et prend la documentation du Kit.
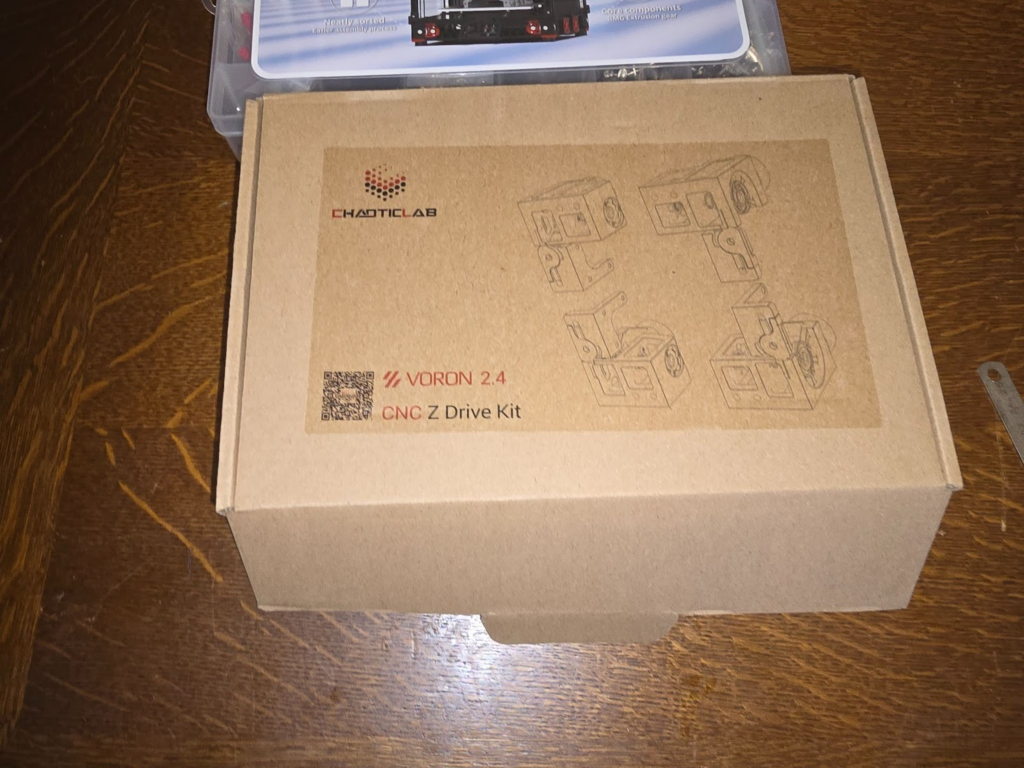
Comme vous pouvez le voir, le packaging est impeccable !
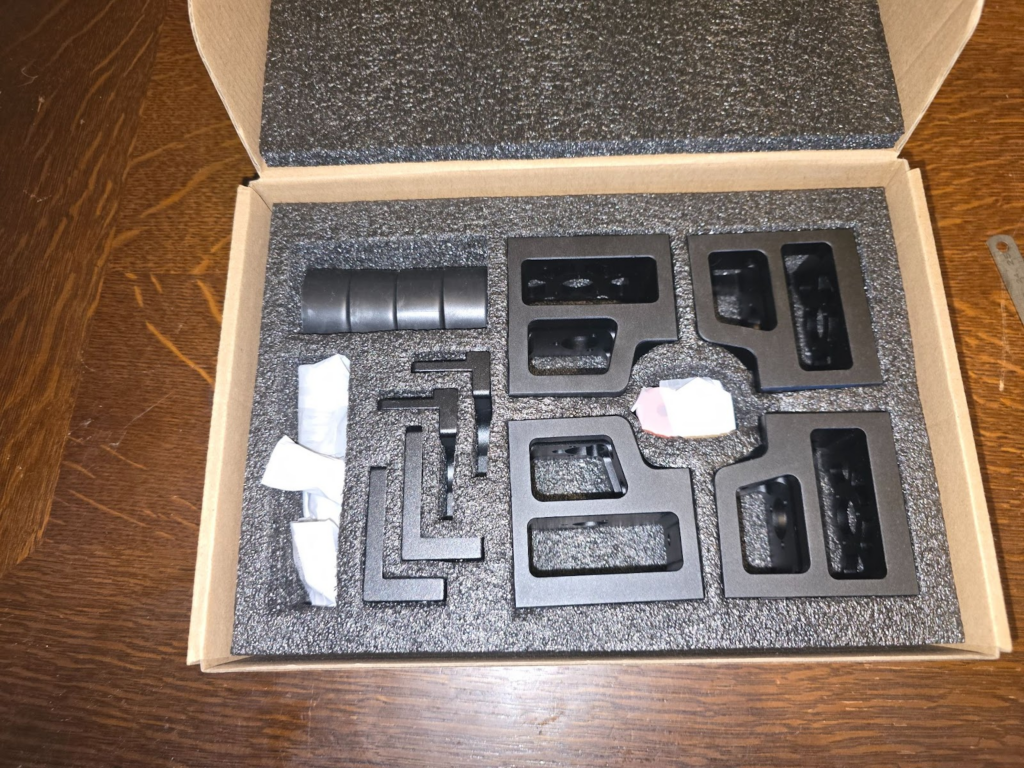
Toutes les vis, rondelles, écrous sont bien identifiés
Les poulies (grandes et petites) ainsi que les axes viennent du kit siboor.
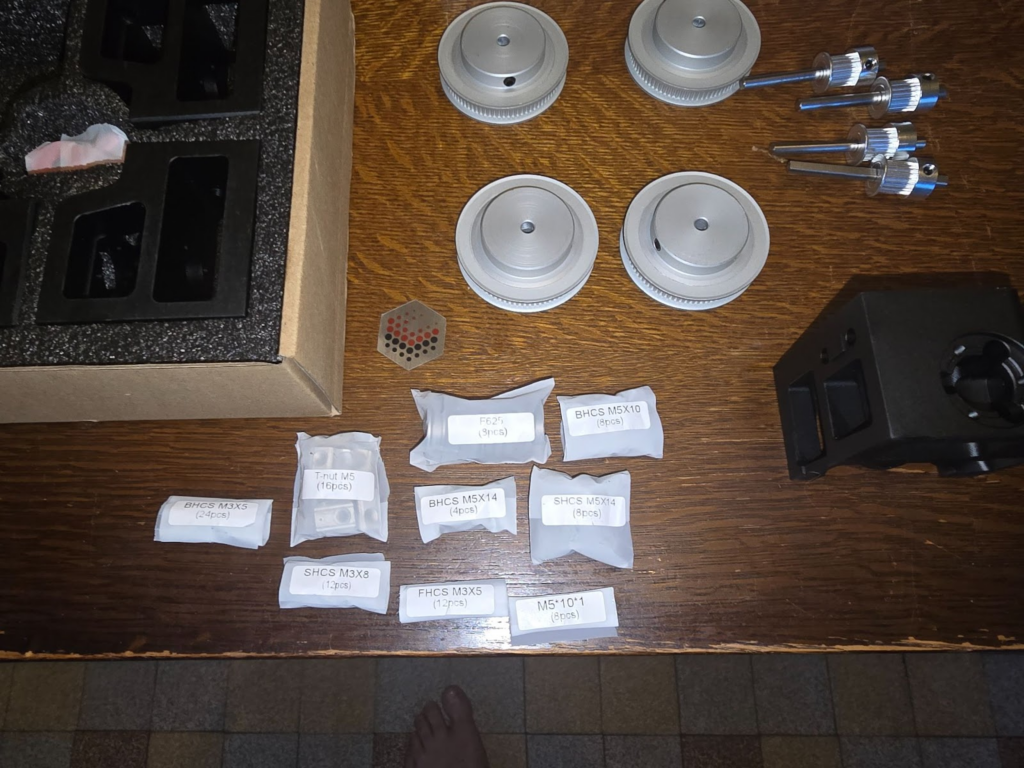
Pas besoin de frein filet ici, les vis du Kit sont déjà enduites !
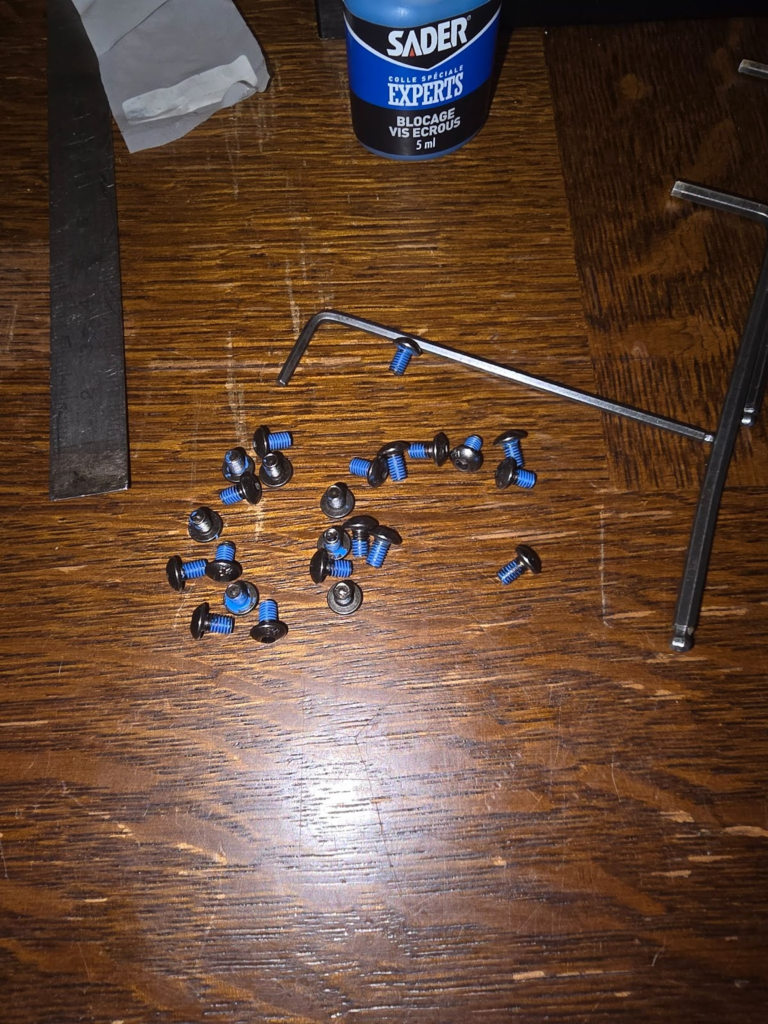
Le montage est bien détaillé dans le guide et se passe bien !
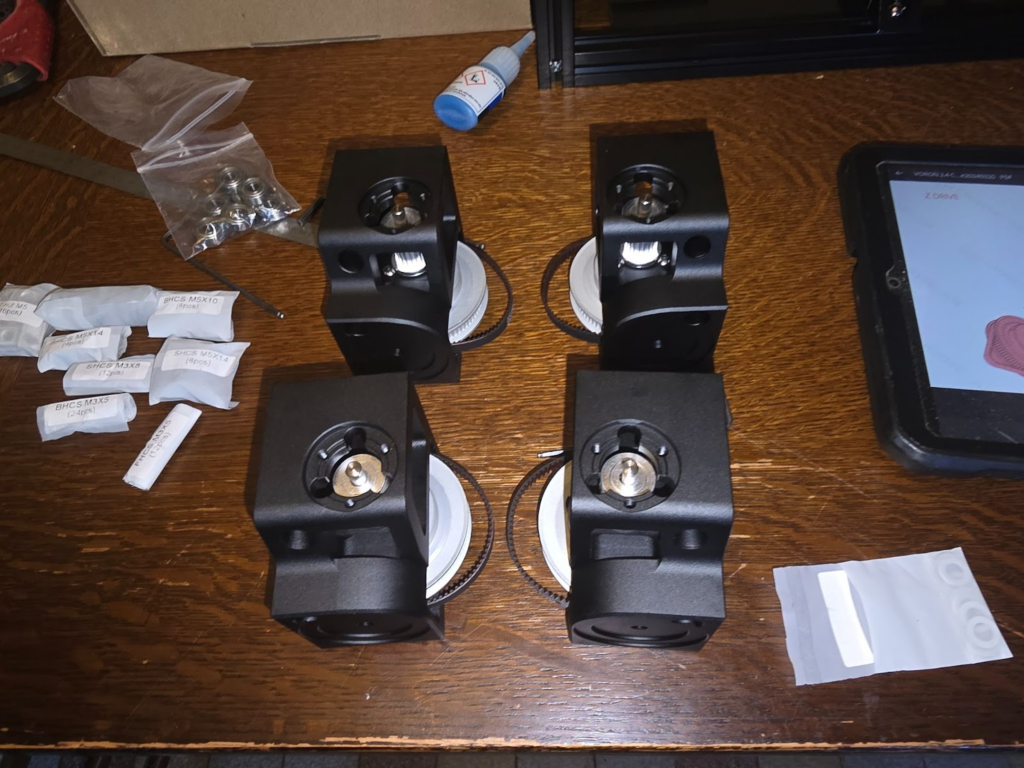
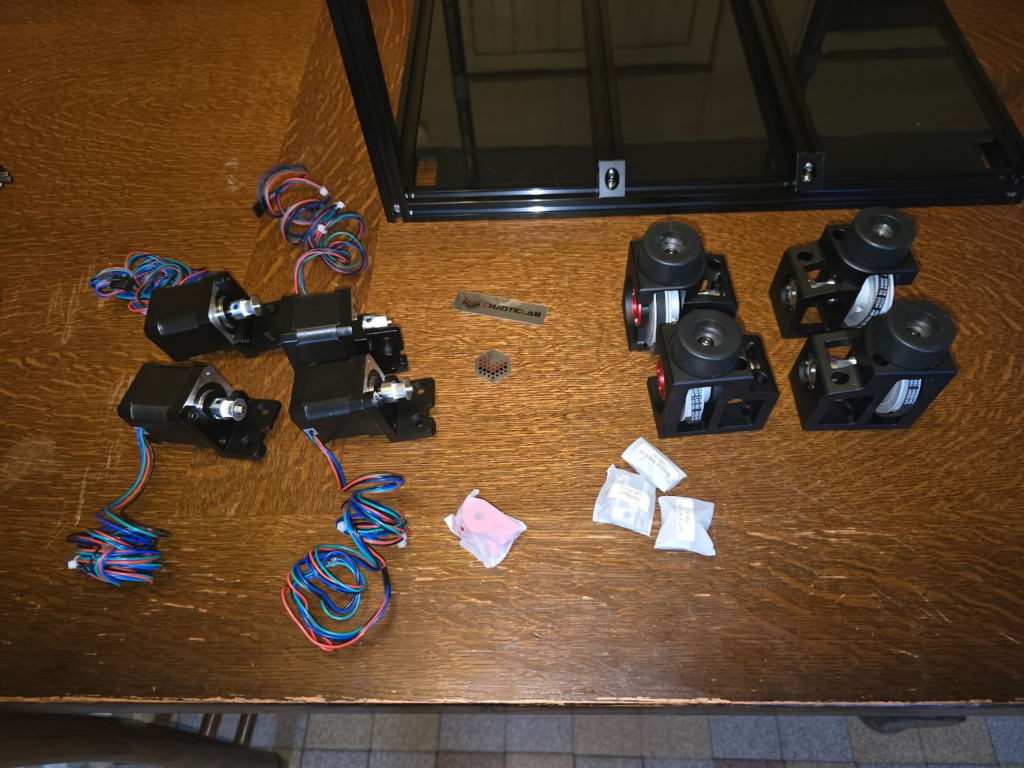
Petite remarque liée à la documentation : pour pouvoir positionner la poulie sur l’axe moteur, ils préconisent une distance de 10.7mm entre le flan du moteur et le flanc de la poulie.
Et bien ça ne fonctionne pas !
Comme vous pouvez le voir, la courroie est complètement de travers. J’ai donc desserré les vis des poulies à 20 dents et les ai recalées sur l’arbre moteur pour que les courroies n’aient aucune contrainte.
Une autre remarque concernant les moteurs cette fois, le méplat de l’arbre ne va pas jusqu’au bout, ce qui fait que les deux vis tombent sur le rond. A voir a l’usage si les poulies ne glissent pas sur l’axe.
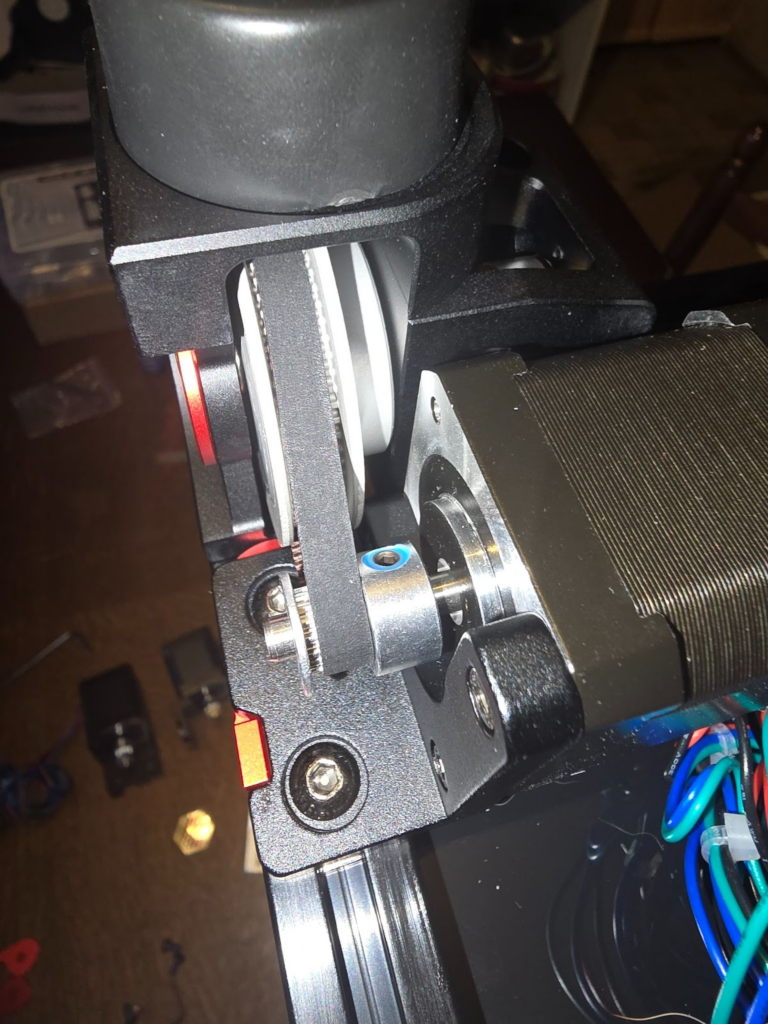
Installation des quatre supports et des moteurs;
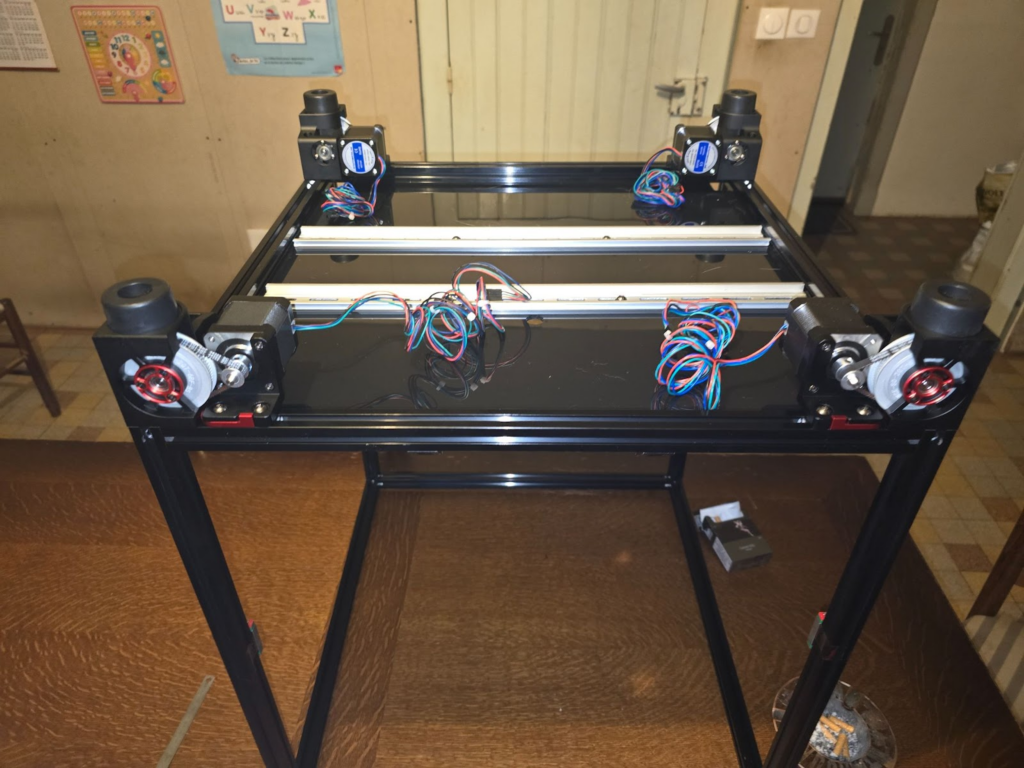
Et voilà, une grosse partie de finie !
Ca ne parait pas, mais il aura fallu 3 heures pour en arriver là !
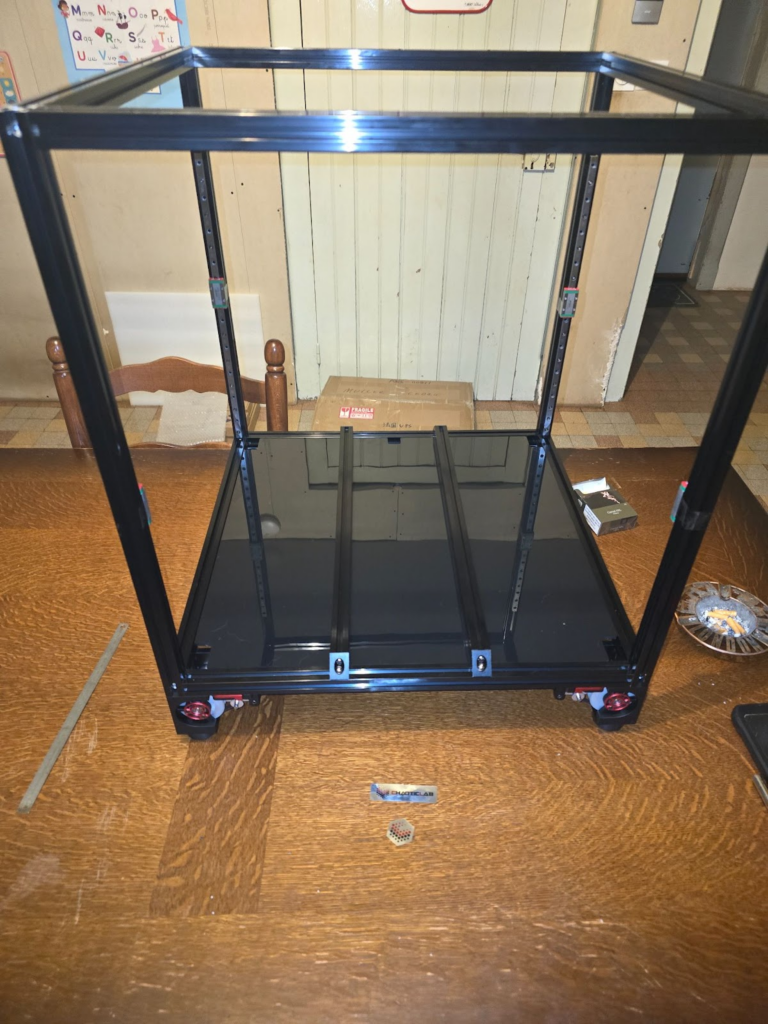
Les tensionneurs de courroie Z (Kit CNC Chaoticlab)
Cette partie est relativement simple, les tensionneurs arrivant déjà montés.
Il faut juste ajouter les poulies dentées fournies dans le kit Siboor et les mettre en place.
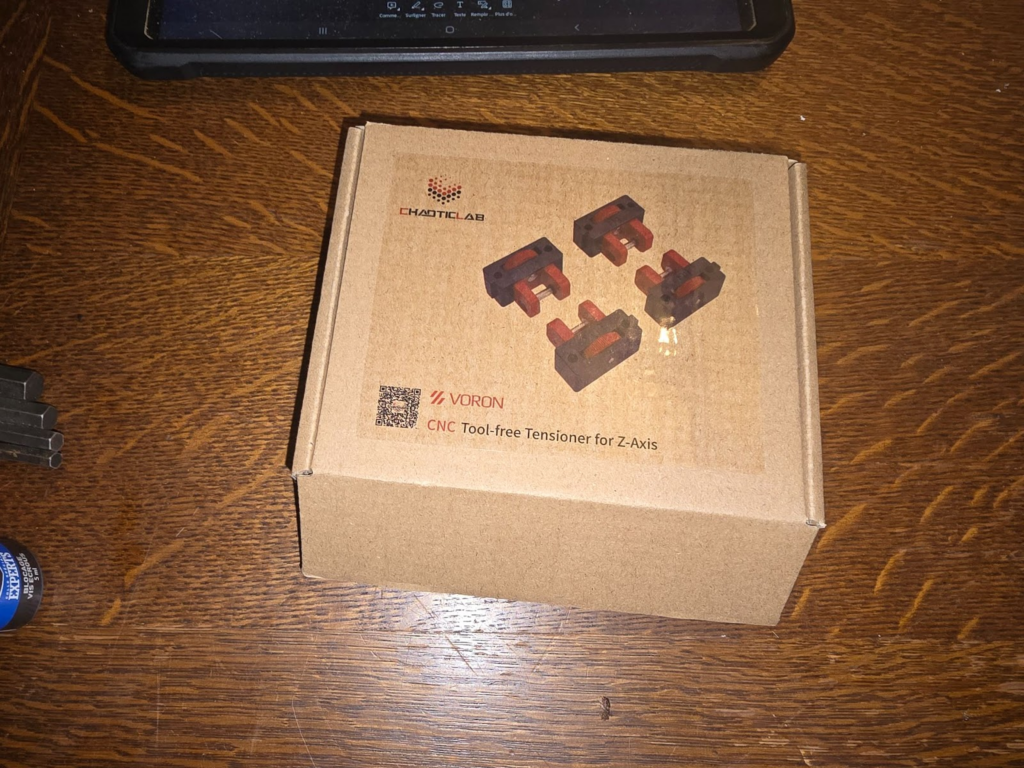
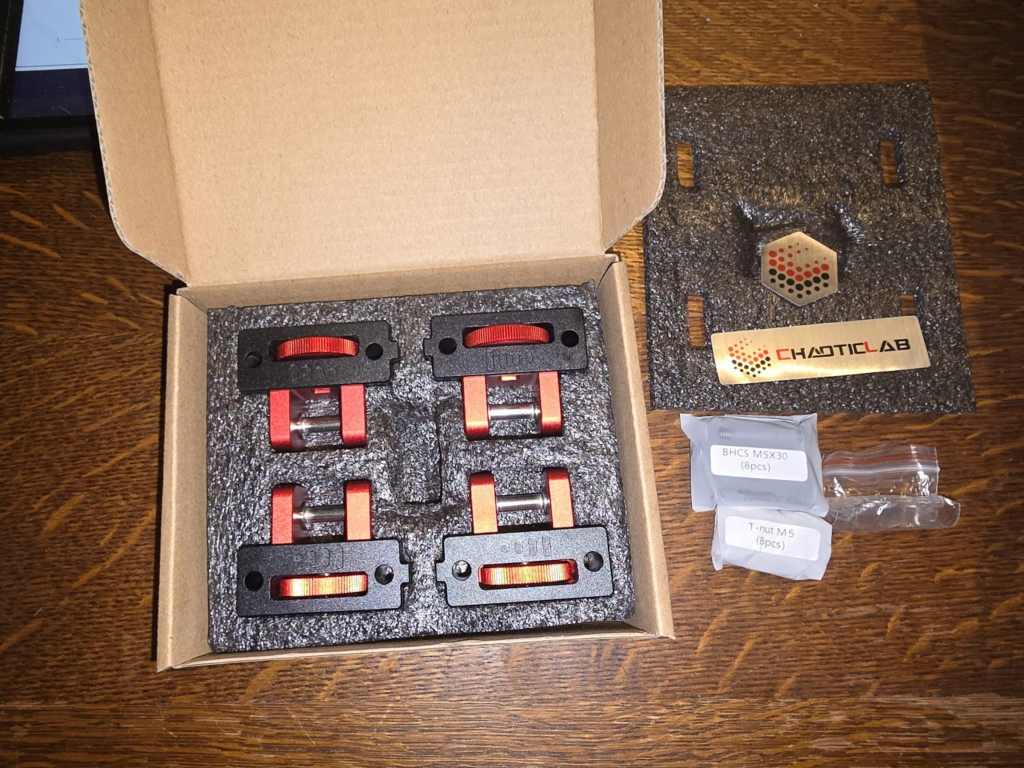
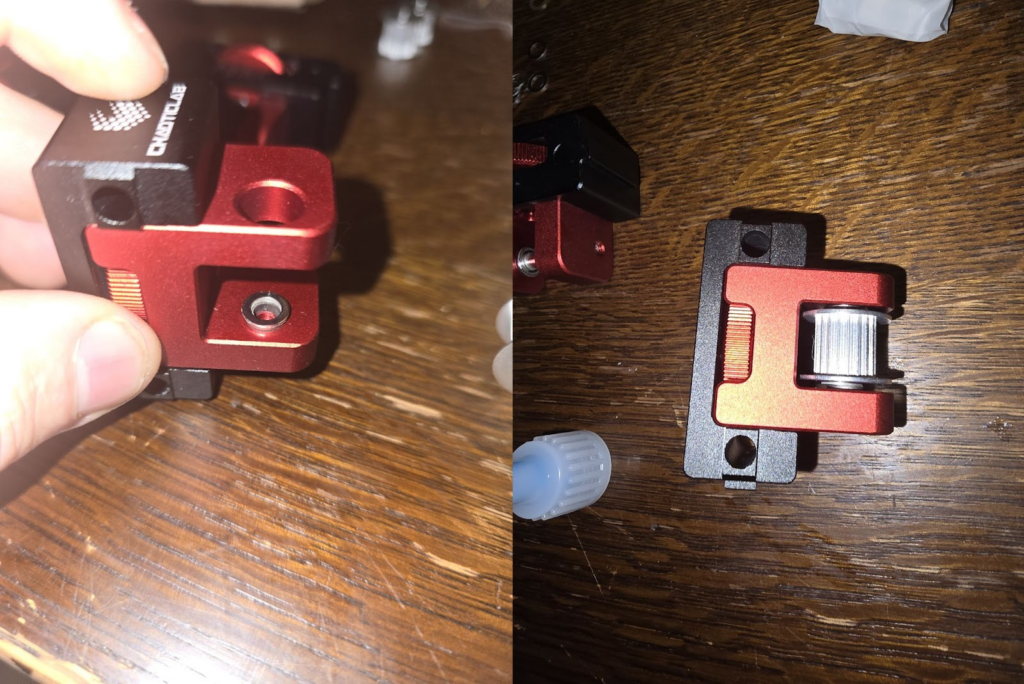
Le petit logo ChaoticLab présent sur les pièces pour bien estampiller la machine 😉.
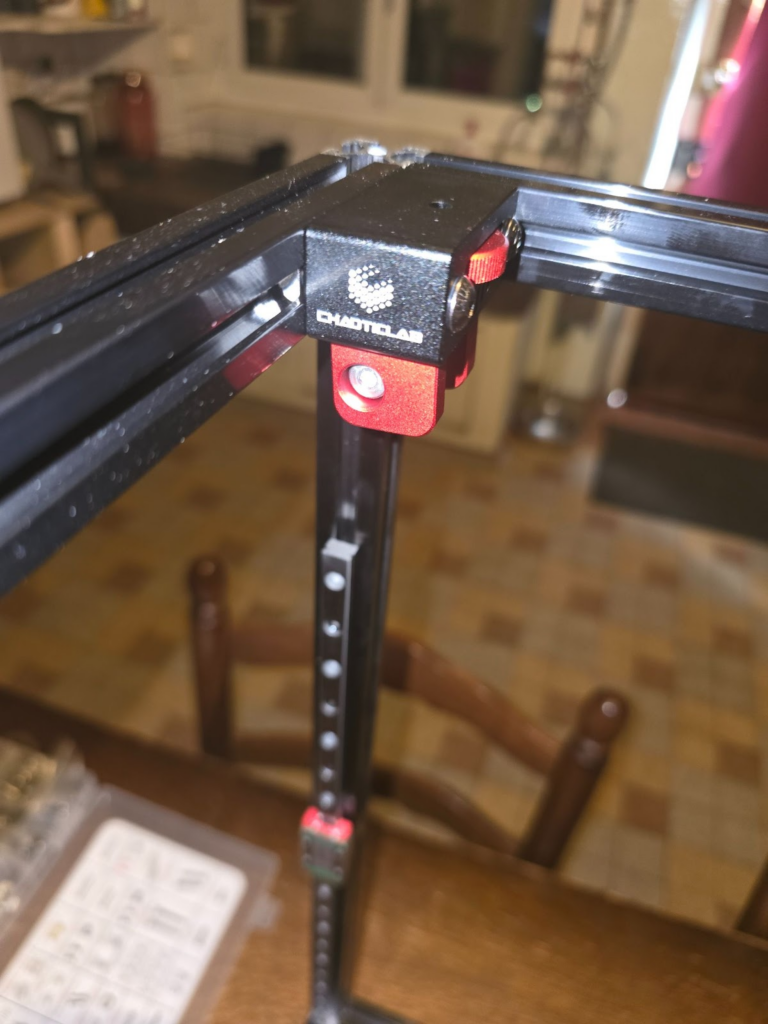
Le plateau chauffant
Ici aussi c’est assez simple, par contre je suis vraiment surpris de l’épaisseur de la plaque d’aluminium ! ça ne risque pas de bouger !
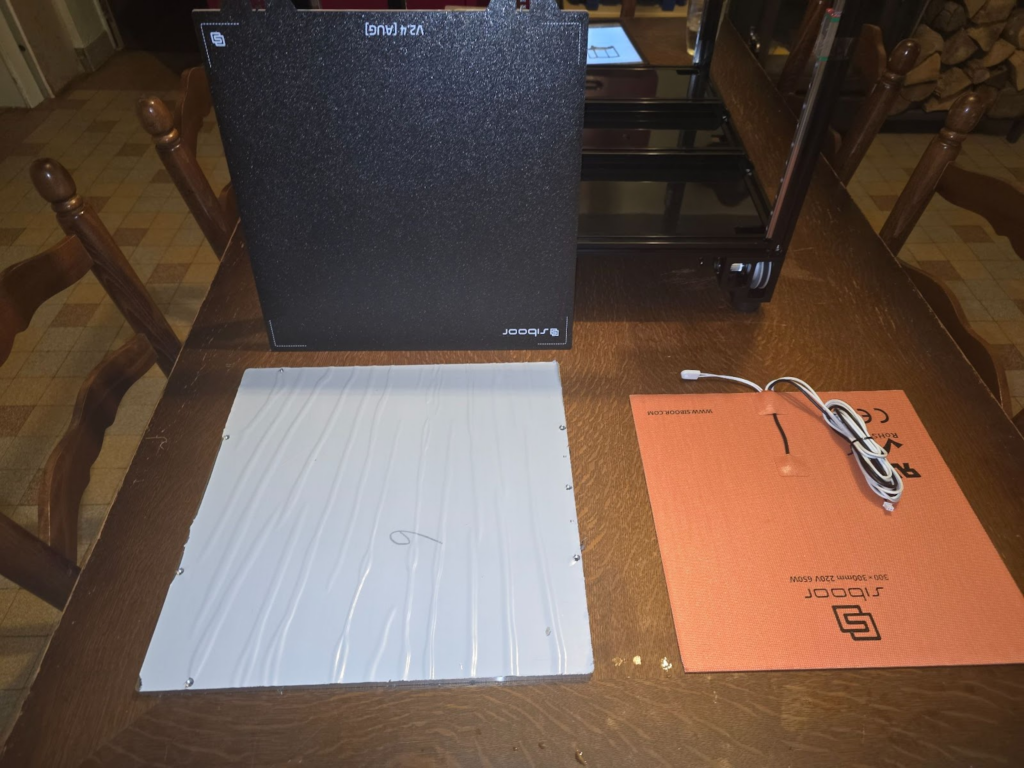
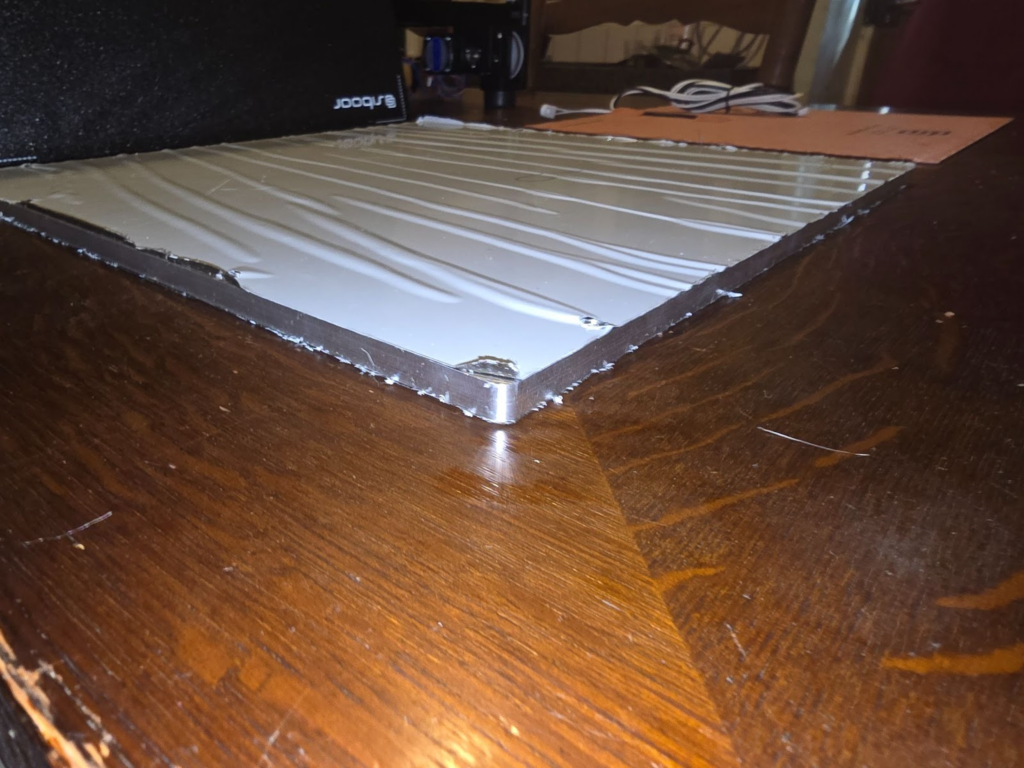
On voit bien les traces d’usinage, normalement la planéité devrait être bonne !
Cela se vérifiera pendant l’étape de calibration ( Partie 3).
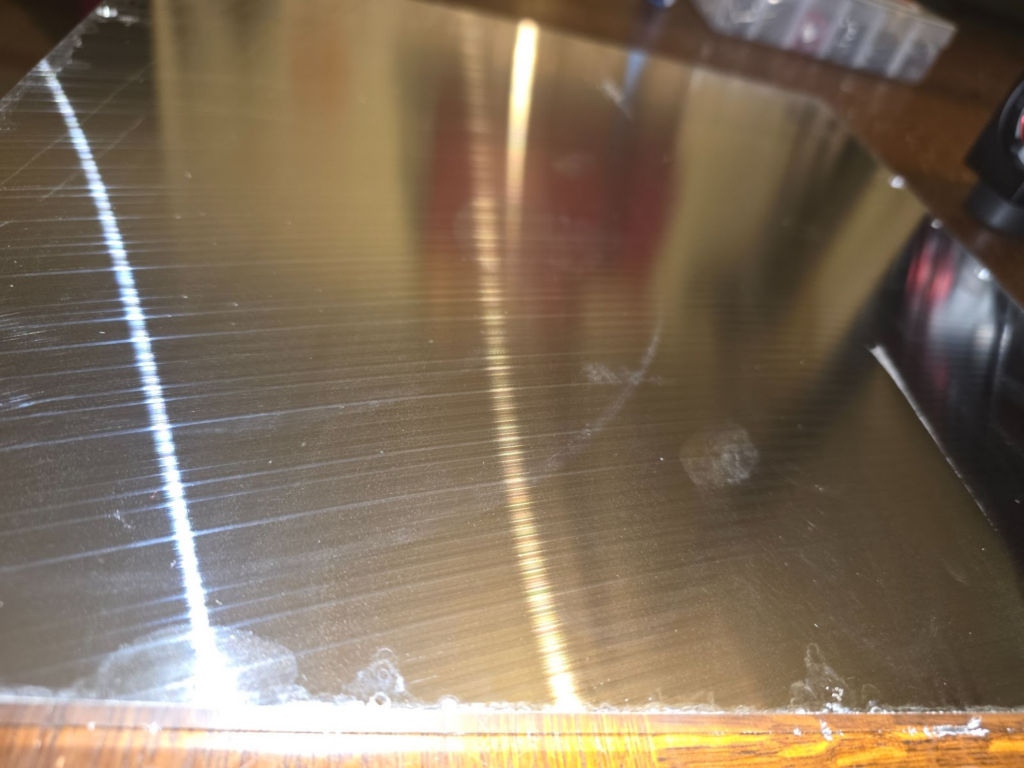
Un bon coup d’alcool isopropylique pour bien dégraisser et enlever toutes les traces de colle.
Après quoi, je colle le patch chauffant sur le plateau mais pas le “build plate” comme préconisé dans le manuel. En effet, si vous collez le build plate, vous n’accéderez plus aux trous de fixation du plateau.
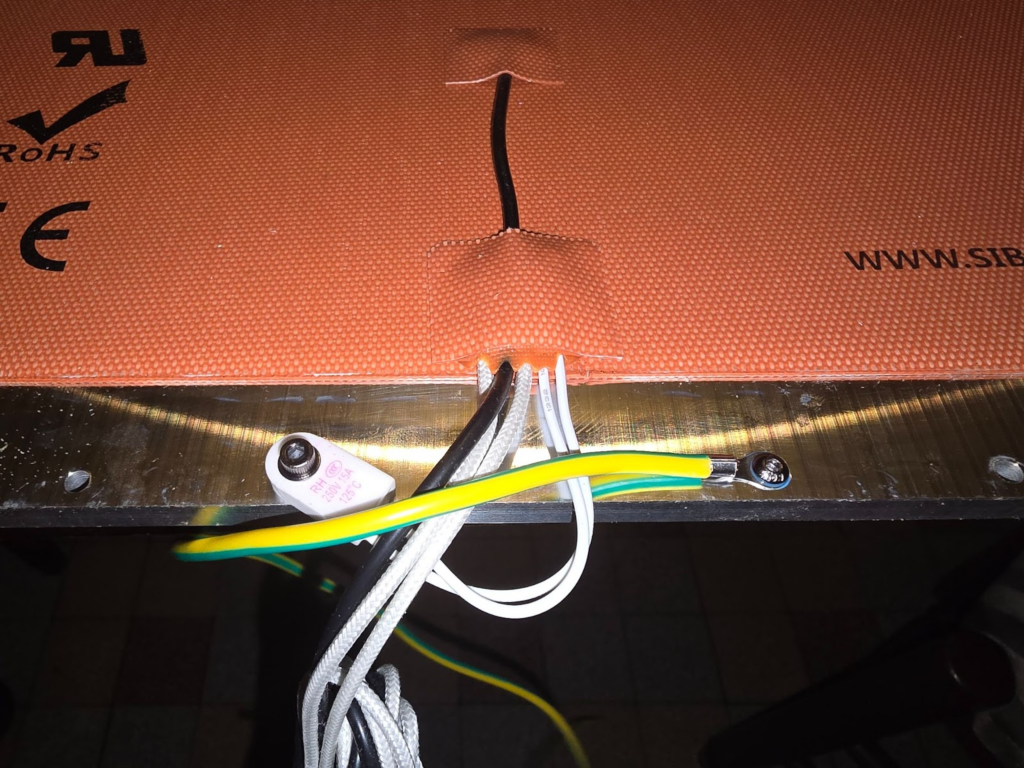
Mise en place des écrous T et des rehausses :
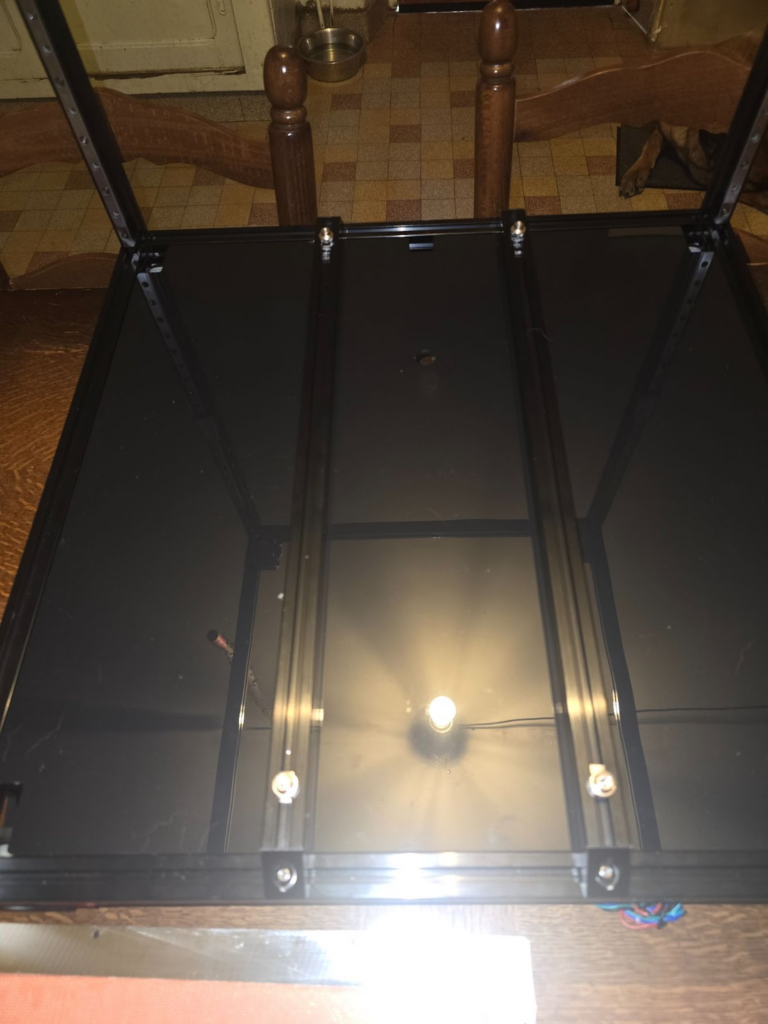
Et enfin fixation du plateau et mise en place du build plate:
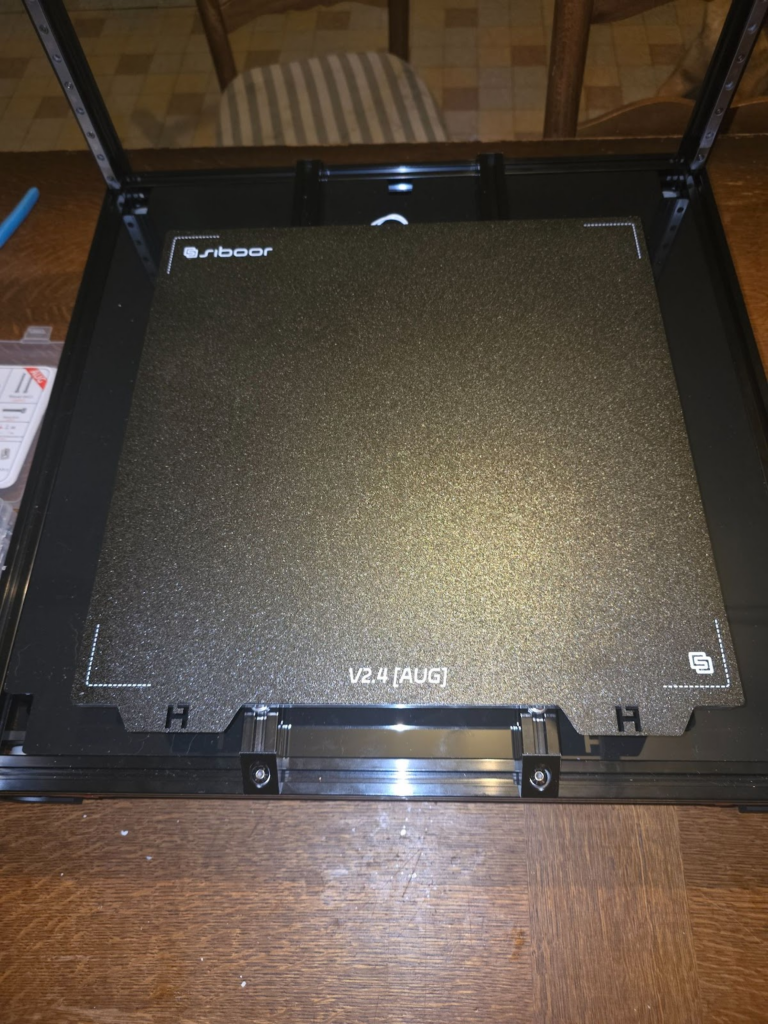
Le portique (ou gantry) qui comprend :
- Le kit de jointure X/Y CNC de Chaoticlab
- Le kit de tensionneur X/Y CNC de Chaoticlab
- le support des moteurs A/B CNC Chaoticlab
Contrairement aux deux précédentes parties, celle-ci est un peu plus compliquée.
En même temps il s’agit du ‘cœur’ de la machine !
Ne pas hésiter à prendre son temps et à contrôler plusieurs fois son travail.
Comme pour le châssis, la qualité de montage influe sur la qualité d’impression future !
Je commence donc par le kit CNC de fixation des moteurs A/B de chez Chaoticlab.

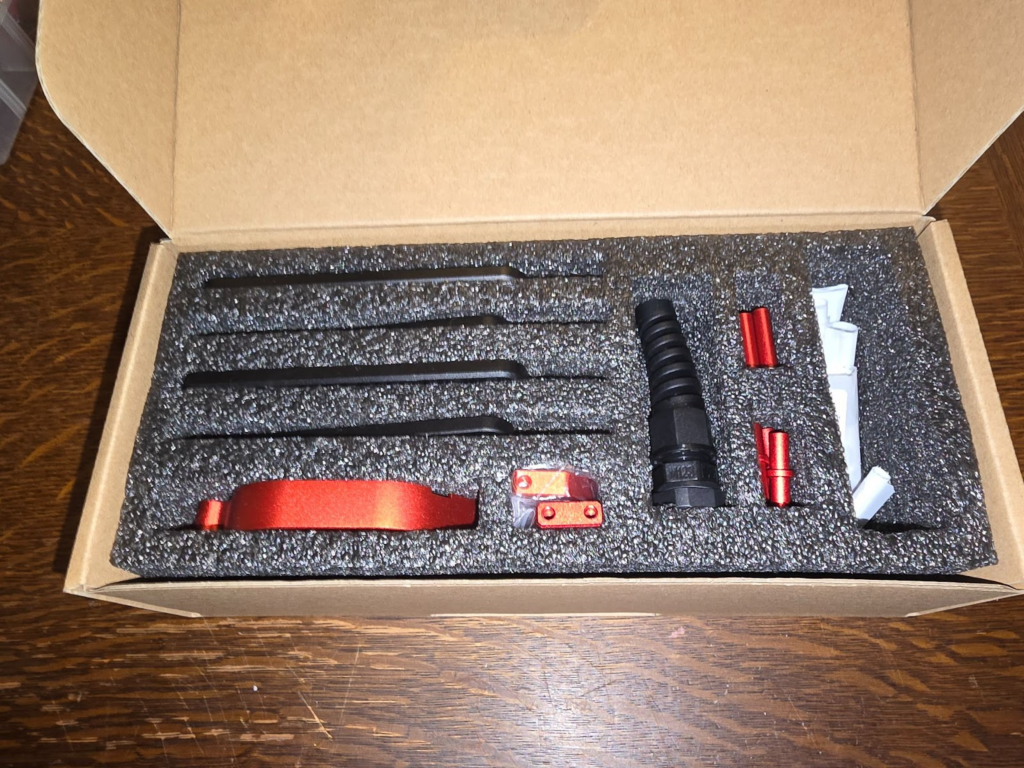
Ce kit est à assembler, car certaines pièces ne sont pas fournies et sont dans le kit Siboor
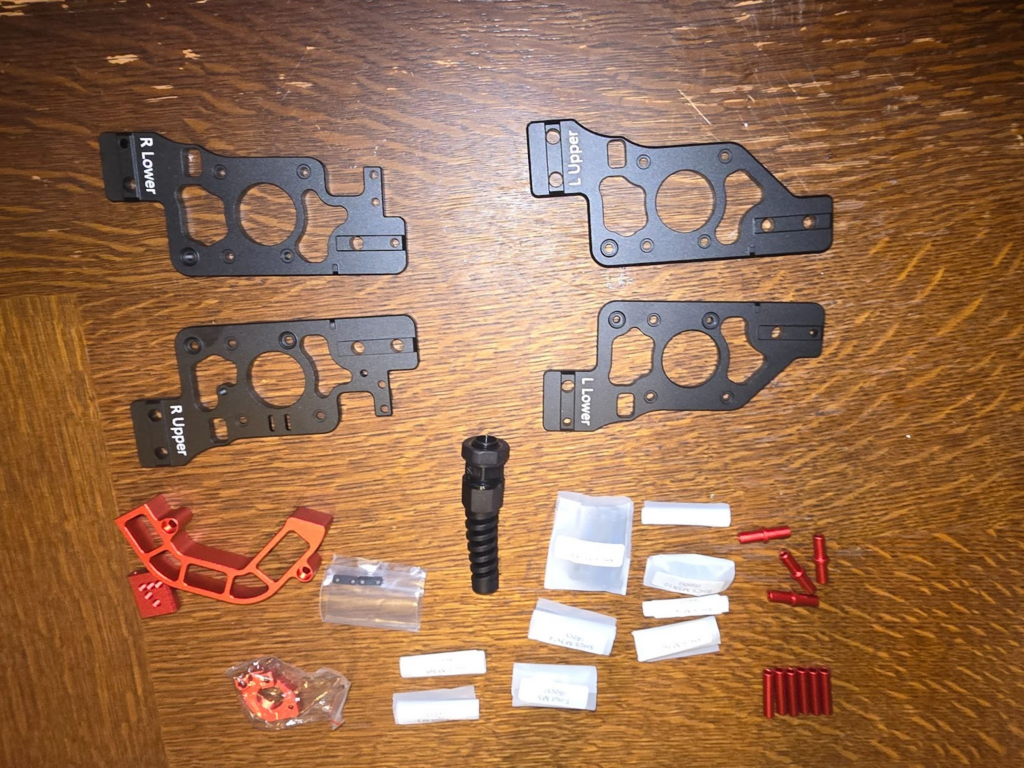
Siboor fournit d’ailleurs un outil pour positionner correctement les poulies dentées sur les arbres moteur.
Très pratique !
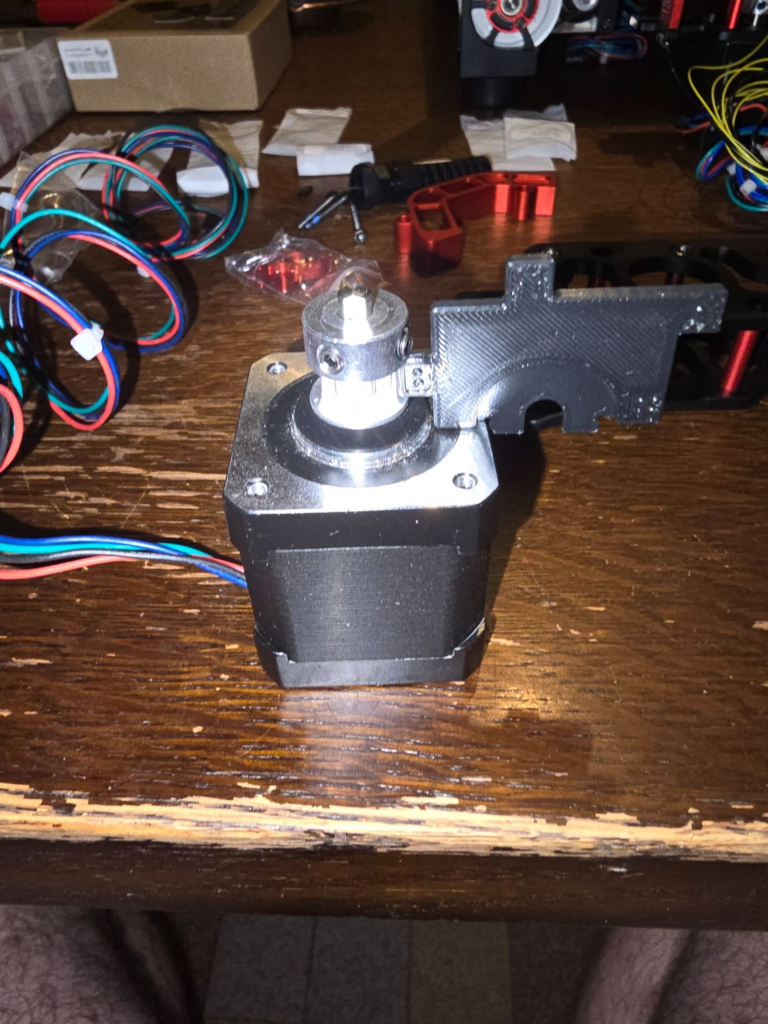
Montage du tout :
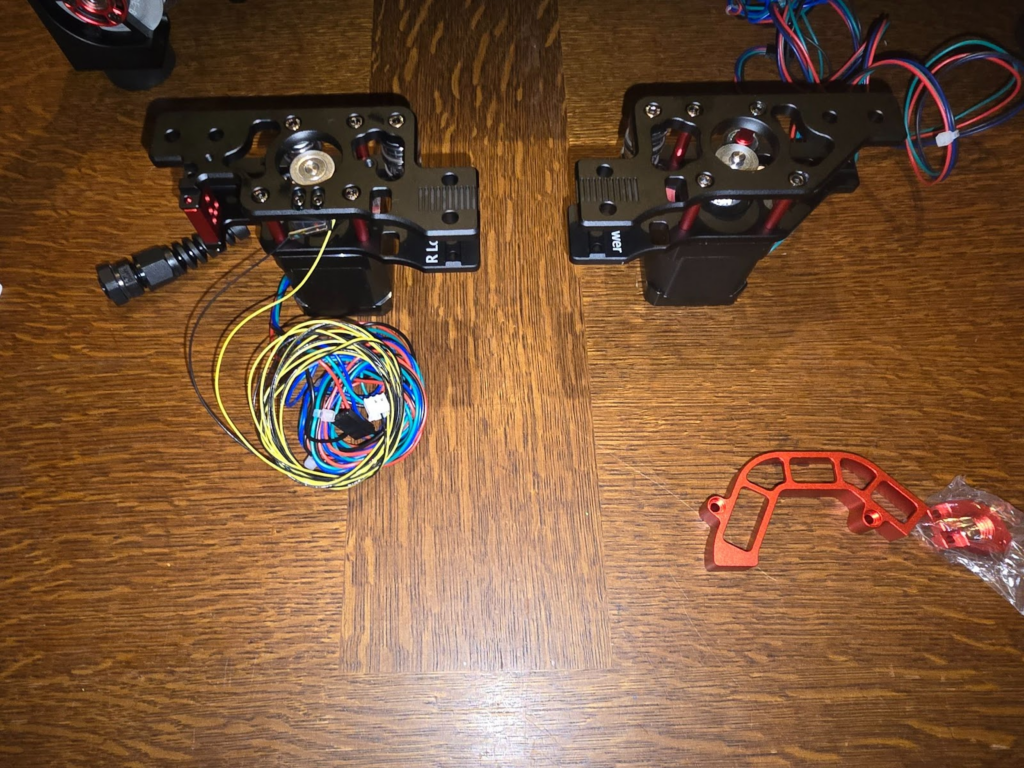
Et là, petit souci. Dans la documentation, il est marqué que la pièce rouge doit être fixée avec des vis M3x14, hors le taraudage n’est pas assez long !
Je pense donc à une erreur dans la documentation mais les bonnes vis ne sont pas fournies non plus !
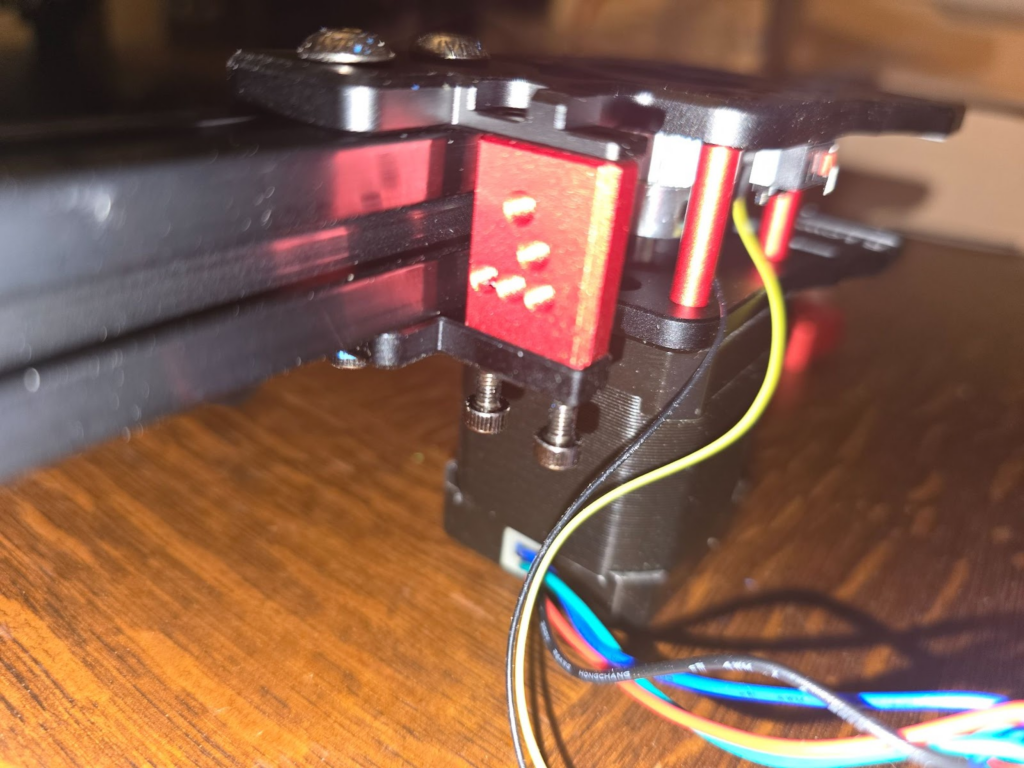
J’ai pris les bonnes dans le kit Siboor (en espérant qu’elles ne manqueront pas plus tard). Ce sont des M3x8 SHCS
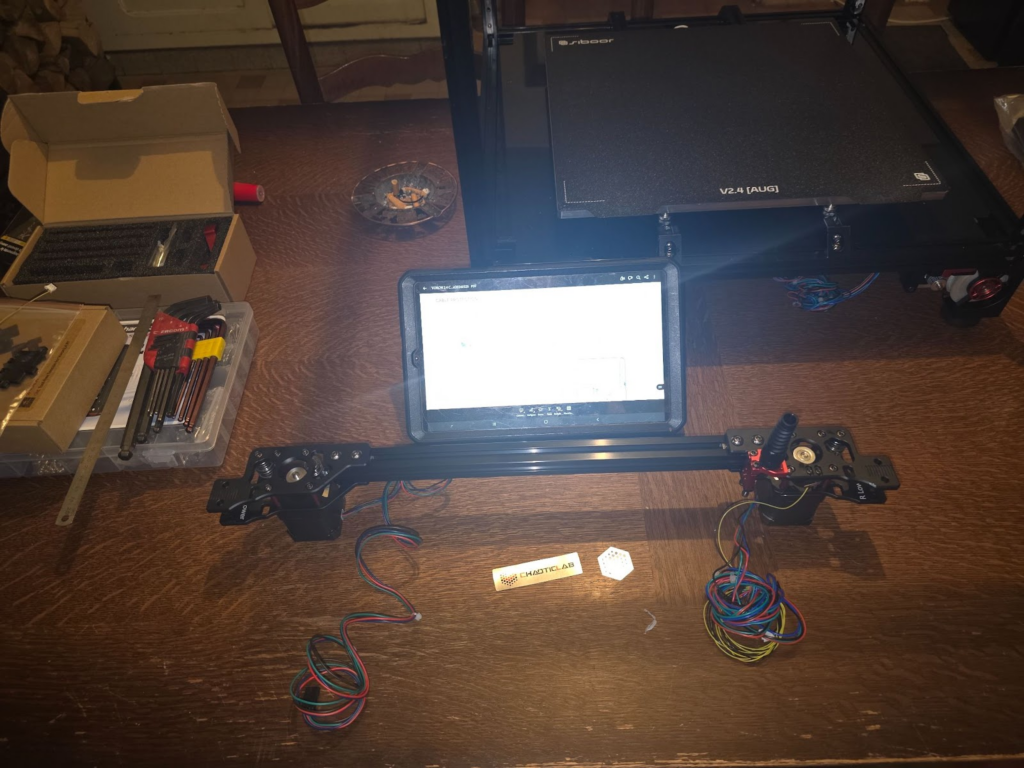
Installation des rails linéaires MGN9H pour l’axe Y, en utilisant le frein filet requis comme pour les rails Z.
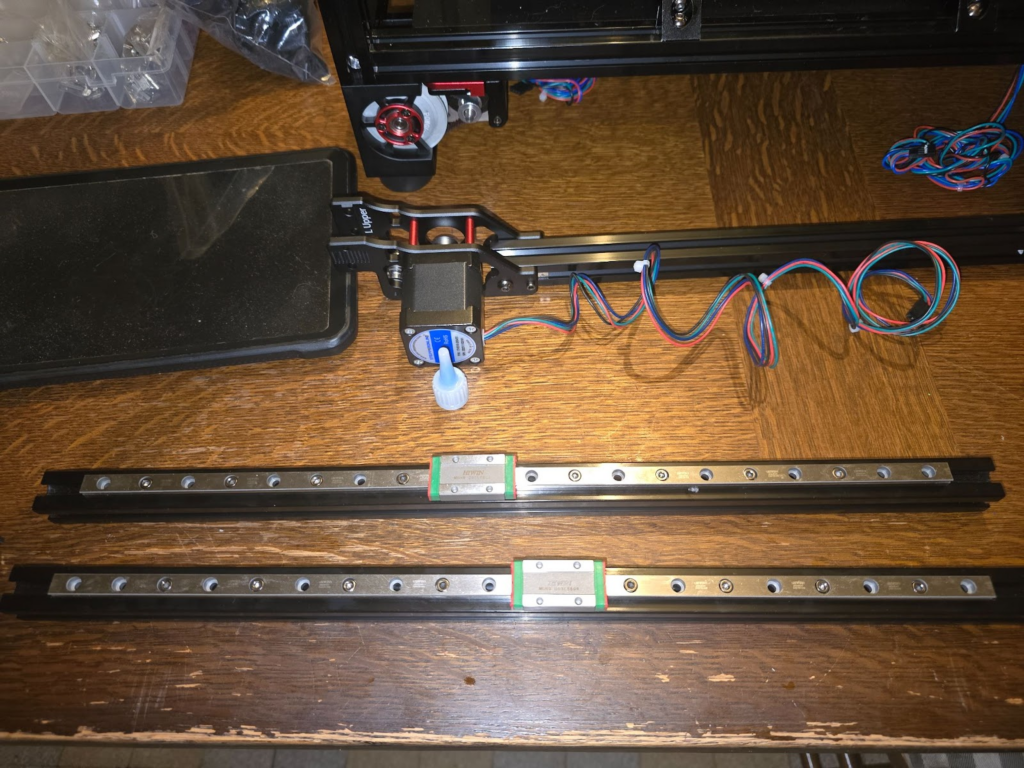
Le kit de tensionneur de courroie A/B CNC de Chaoticlab :
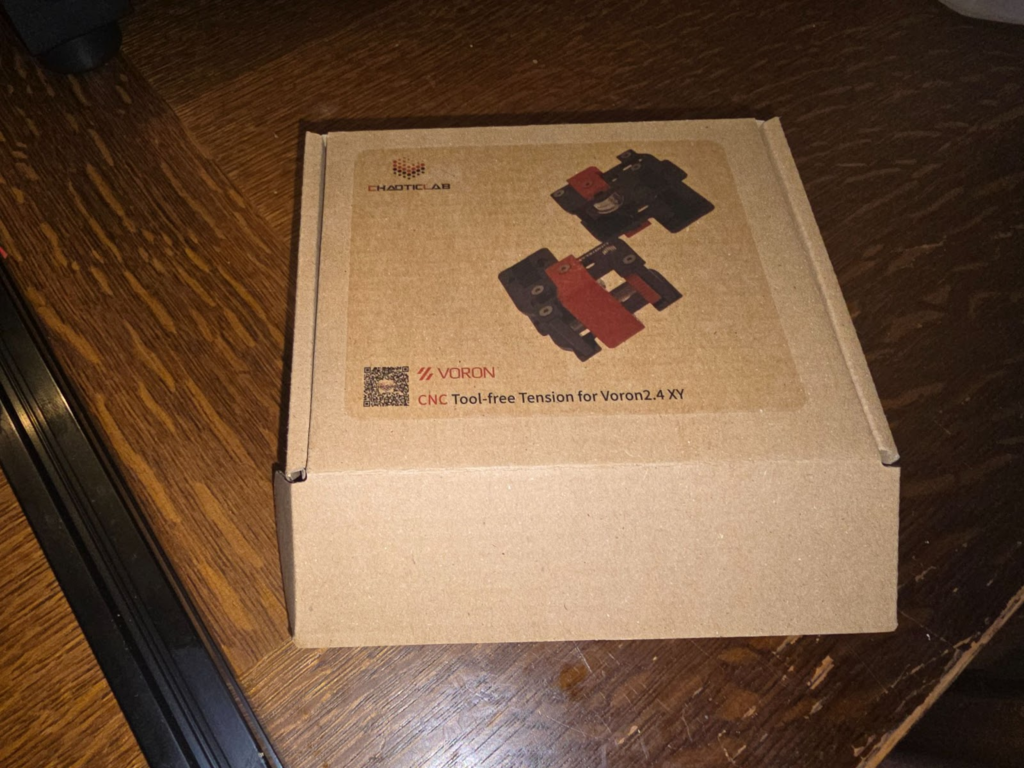
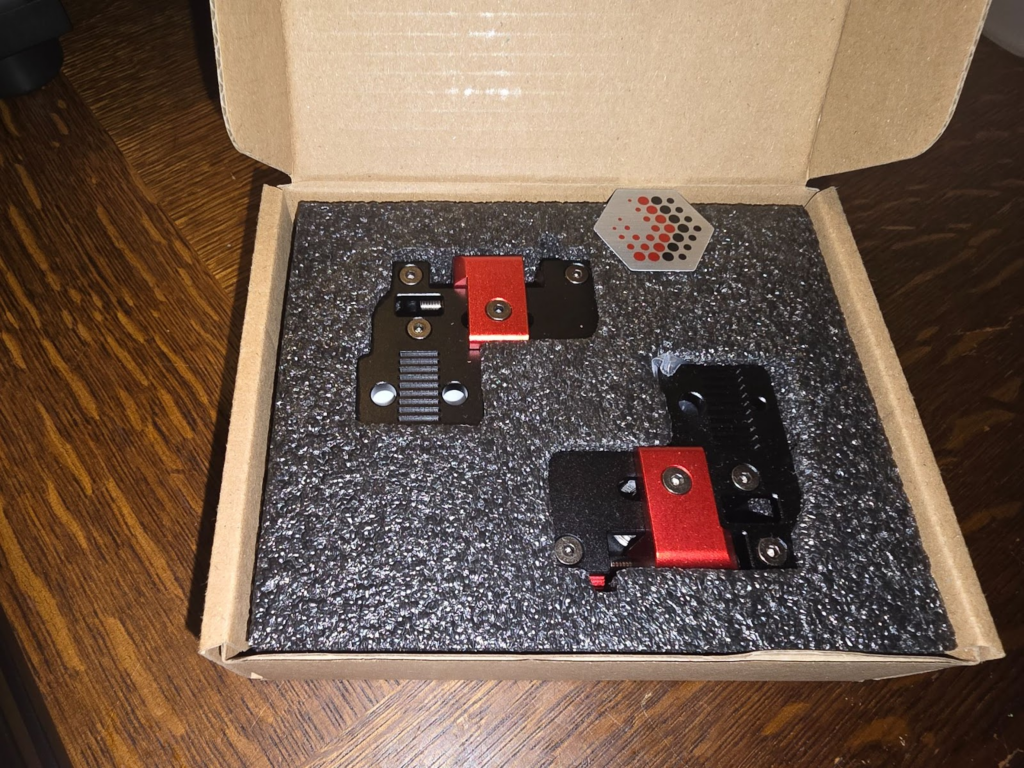
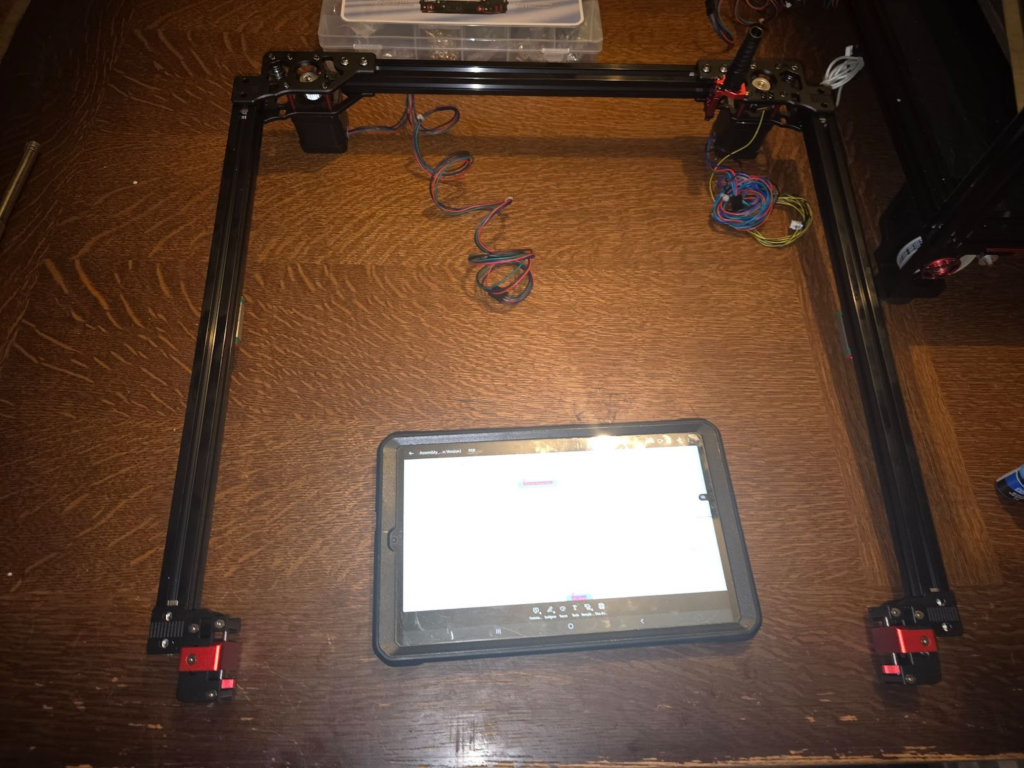
Dans la notice, il faut fixer le tout avec des plaques, sauf que lesdîtes plaques (qui servent aussi à bloquer les courroies Z) ne se trouvent pas dans l’un des deux kit précédents.
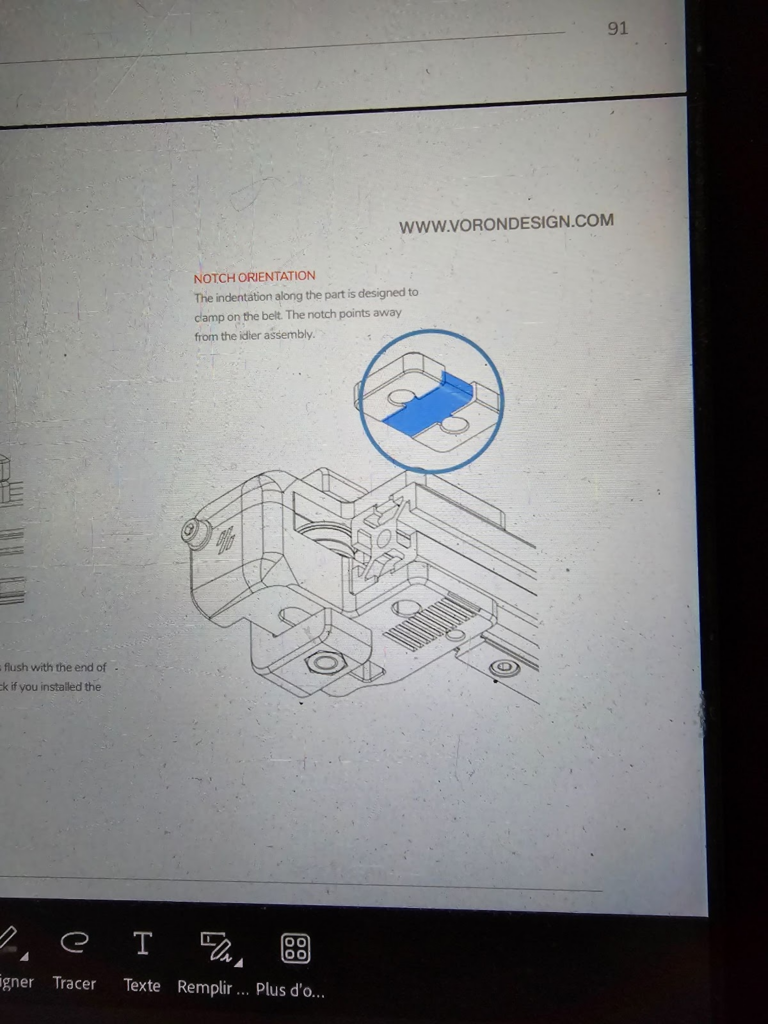
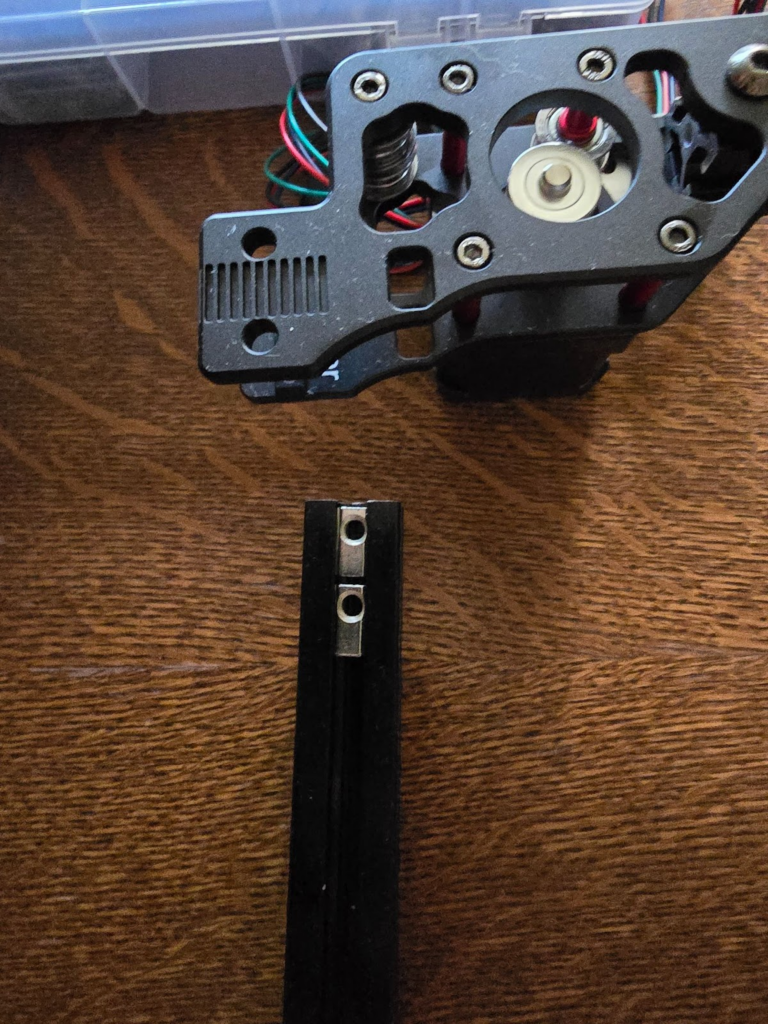
Ces plaques se trouvent en fait dans le kit suivant, le CNC Z Joint kit :
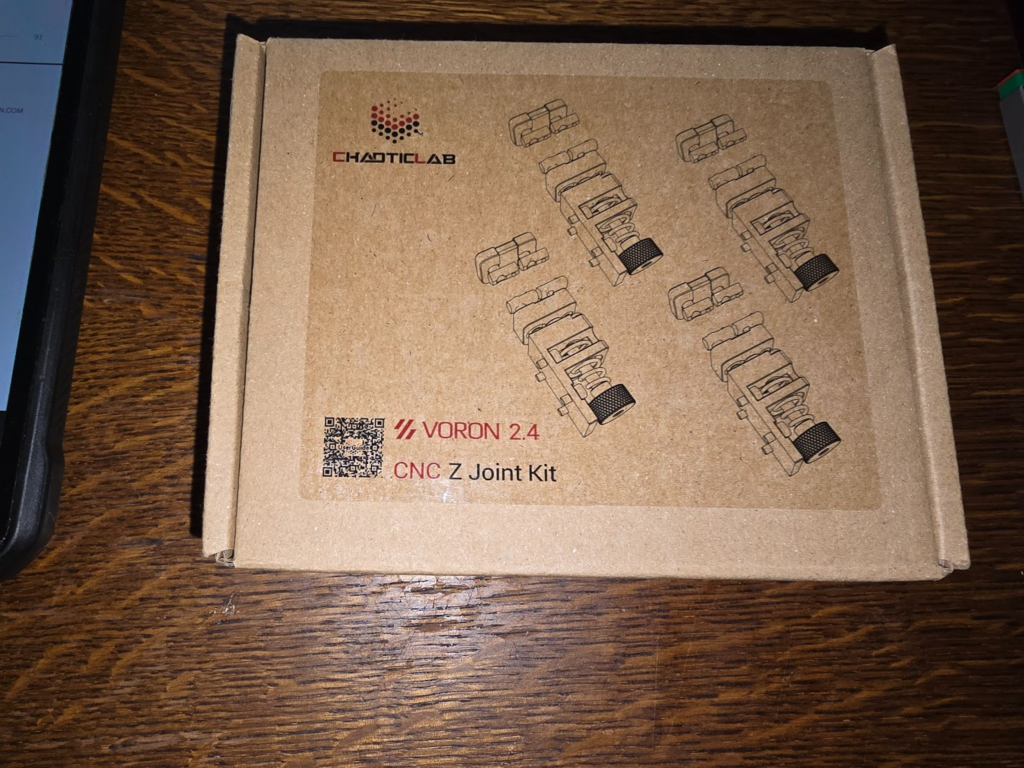
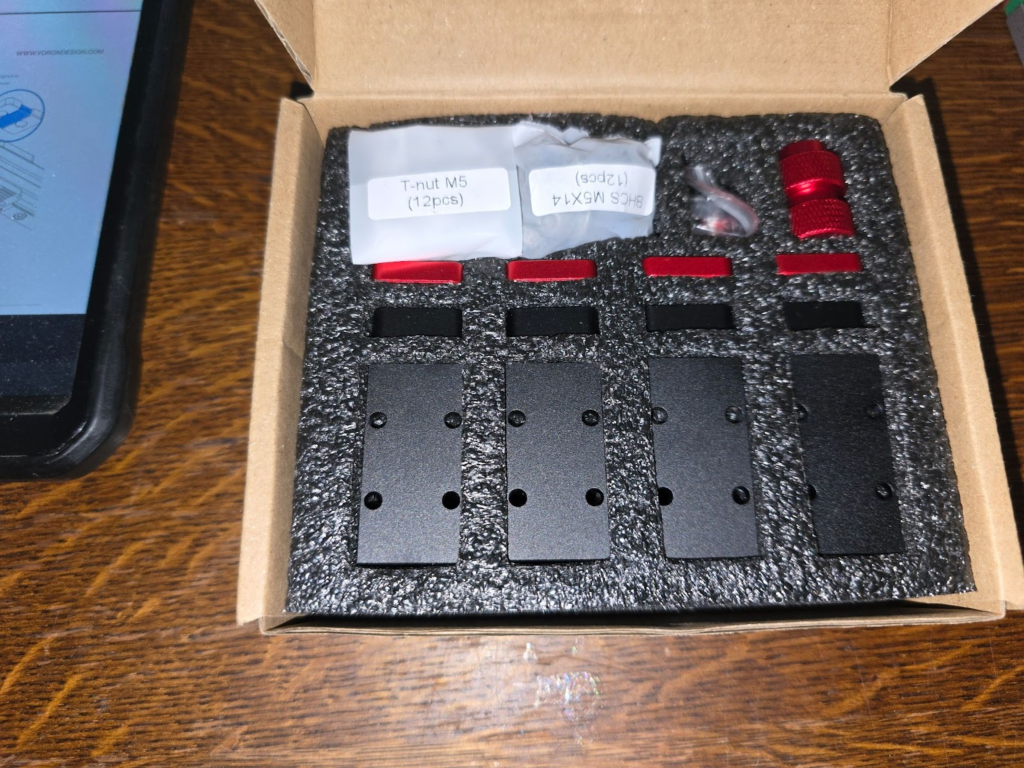
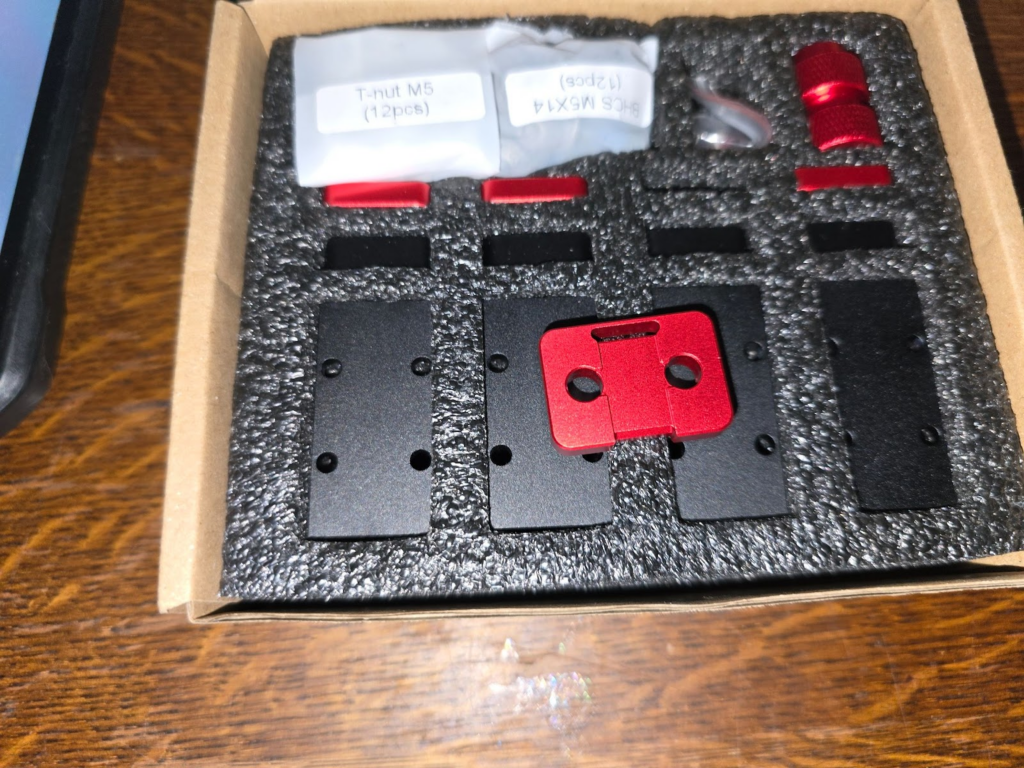
Et là encore, petit problème ! Les vis fournies pour fixer les plaques sont des M5x16 BHCS, Elles sont bien dans la nomenclature et dans la documentation, mais sur le kit de tensionneurs on voit bien qu’elles sont trop longues !

Par contre, pour le kit de montage des moteurs A/B, pas de soucis !
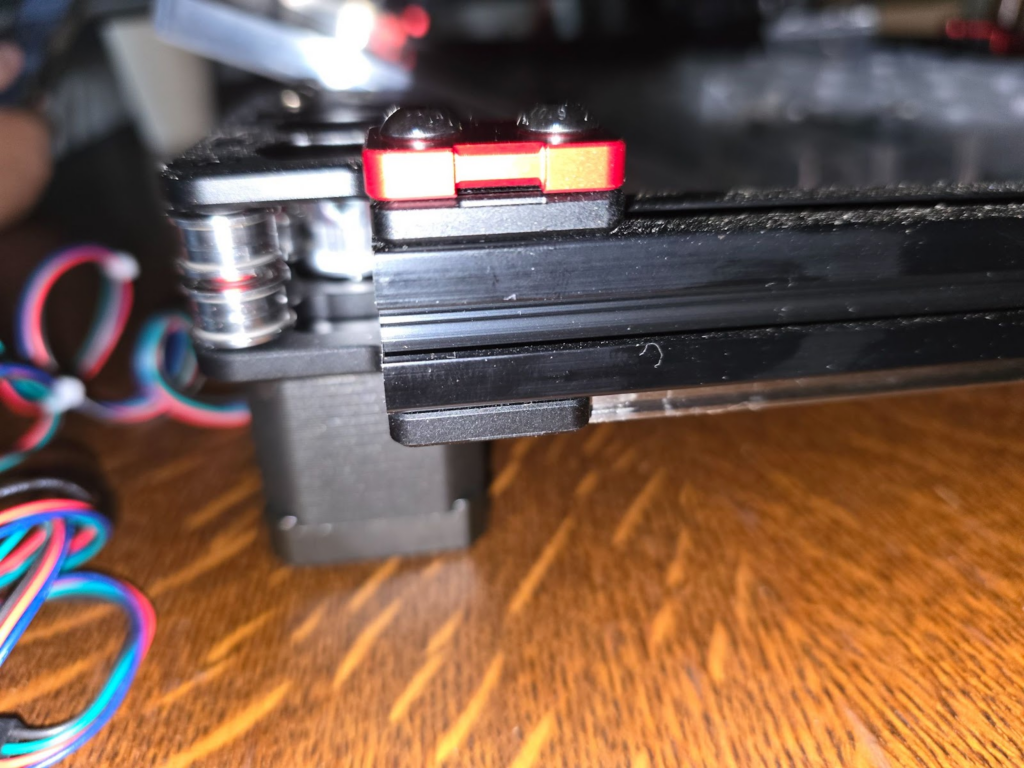
Pour la suite, je vais monter l’axe X et pour cela j’ai besoin du dernier kit CNC, le X/Y joint :

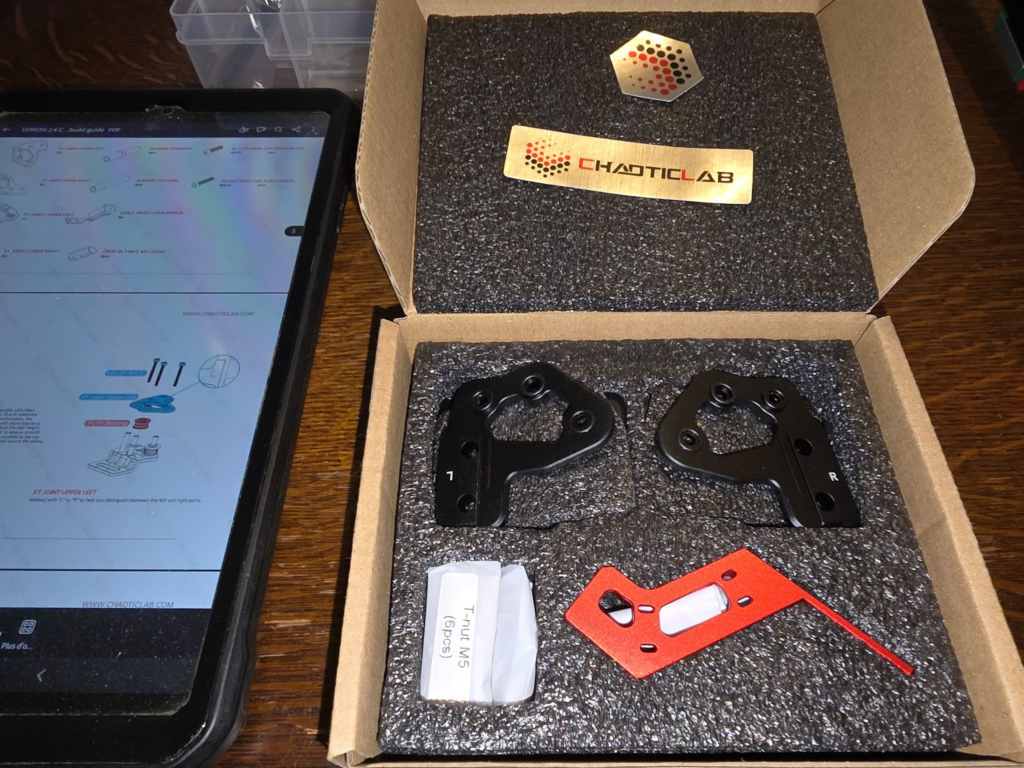
Comme pour les moteurs A/B, celui-ci doit être assemblé avec des pièces du kit Siboor
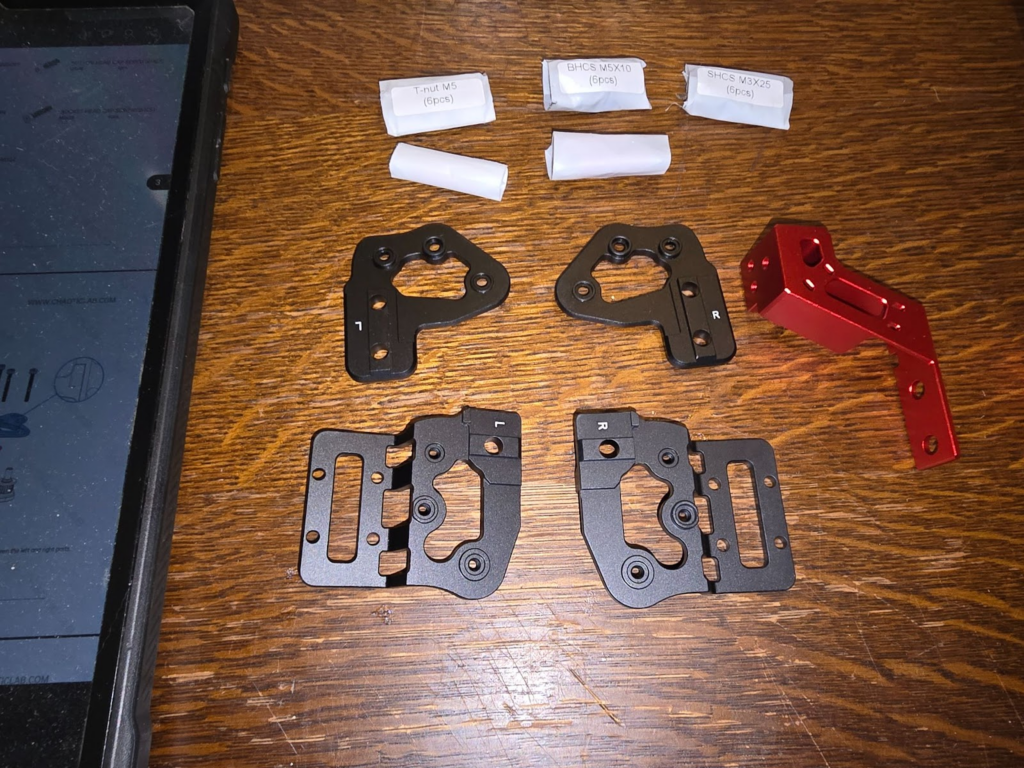
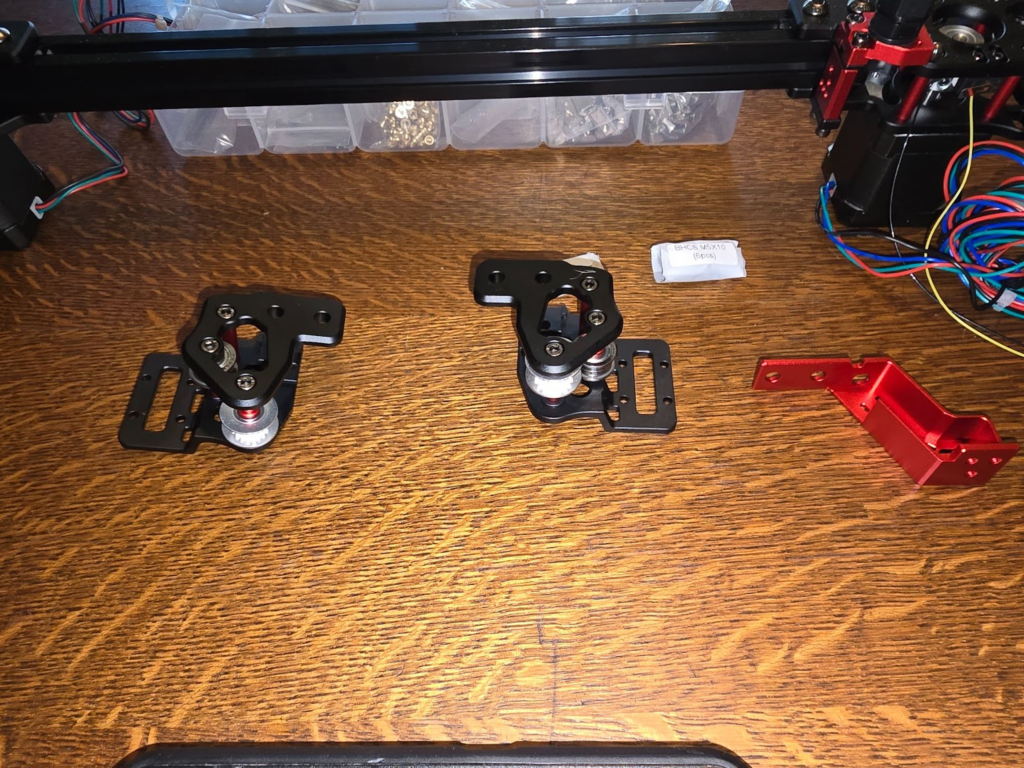
Petite surprise au passage, un écrou T-Nut M5 défectueux ! Hé oui ce n’est pas parce qu’une marque est leader dans son domaine qu’elle est exempte de QC (Quality check). Vous verrez d’ailleurs un peu plus loin que ce n’est pas la seule surprise que j’ai eue avec Chaoticlab, la dernière étant un peu plus sérieuse !
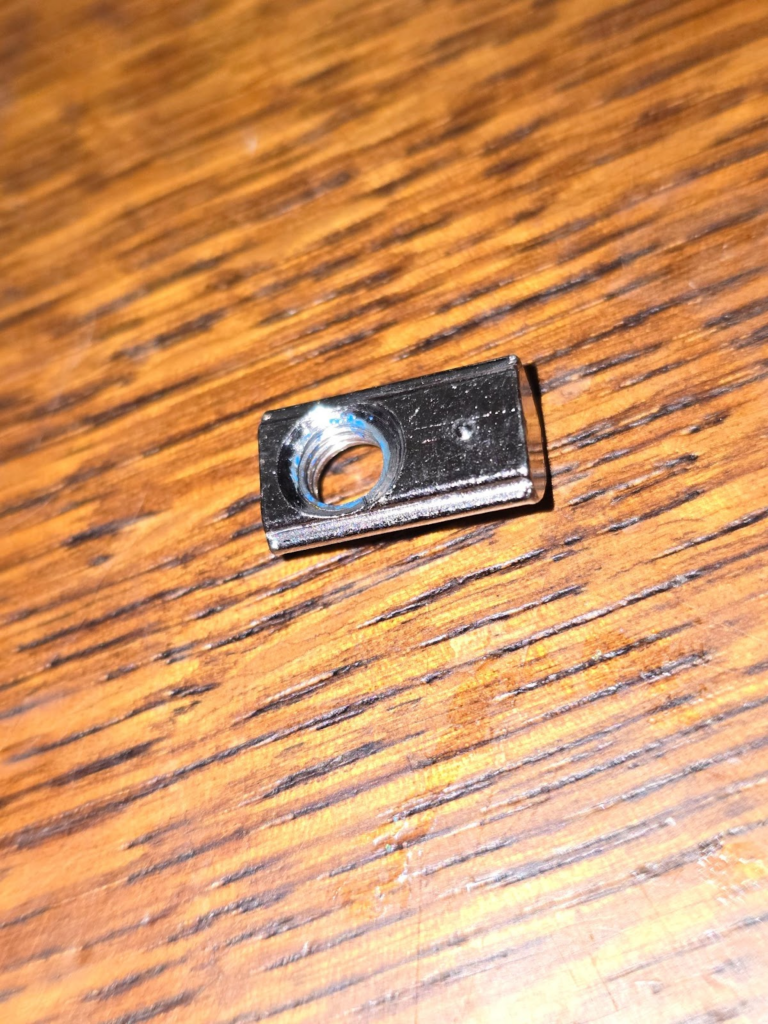
Montage de l’axe X sur les rails linéaires Y, et bien là aussi souci !
La documentation Chaoticlab dit qu’il faut monter sur les chariots Y avec des vis M3x6 SHCS.
Lorsque c’est de couleur rouge, ce n’est pas fourni dans le Kit.
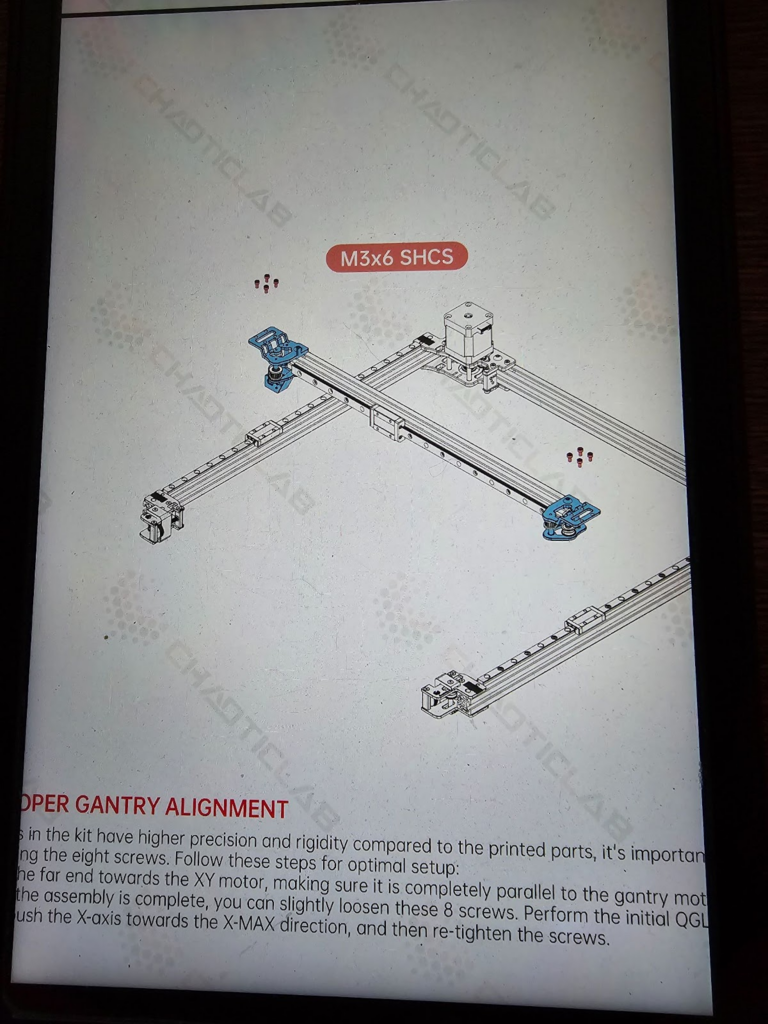
Je prends la doc Siboor, et là, surprise aussi: eux disent qu’il faut des vis M3x10 BHCS
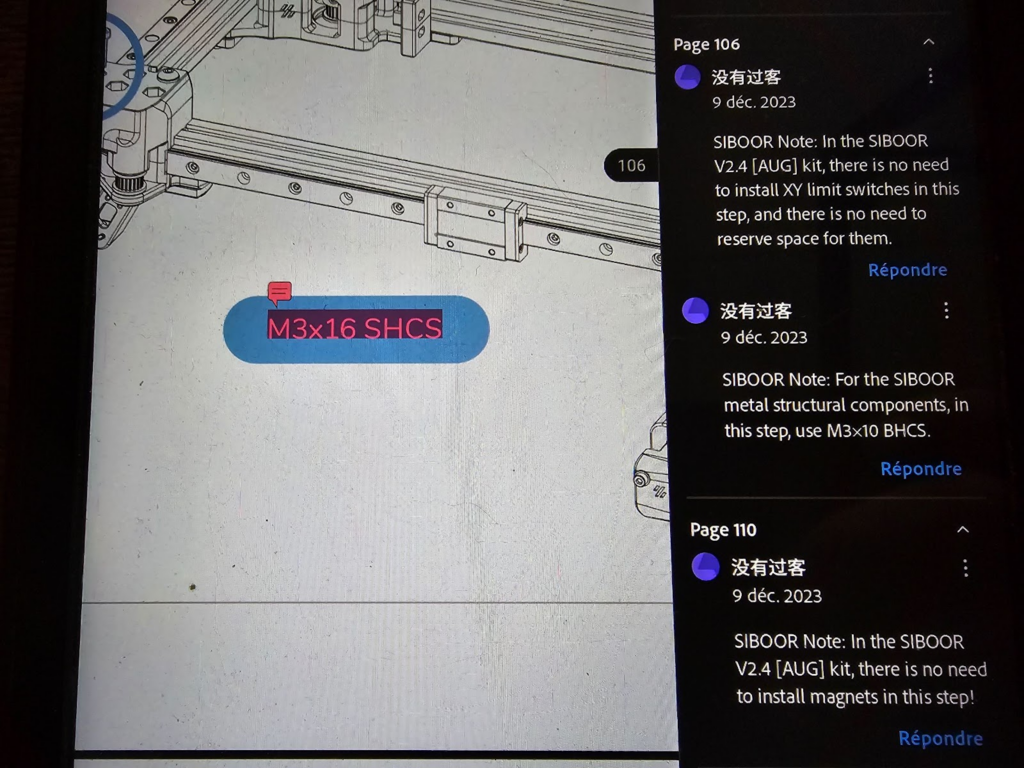
Sauf qu’avec des M3x10 BHCS ça ne fonctionne pas, les vis sont trop longues et il faut bien des M3x6 SHCS
Heureusement que j’en avais dans mon stock !
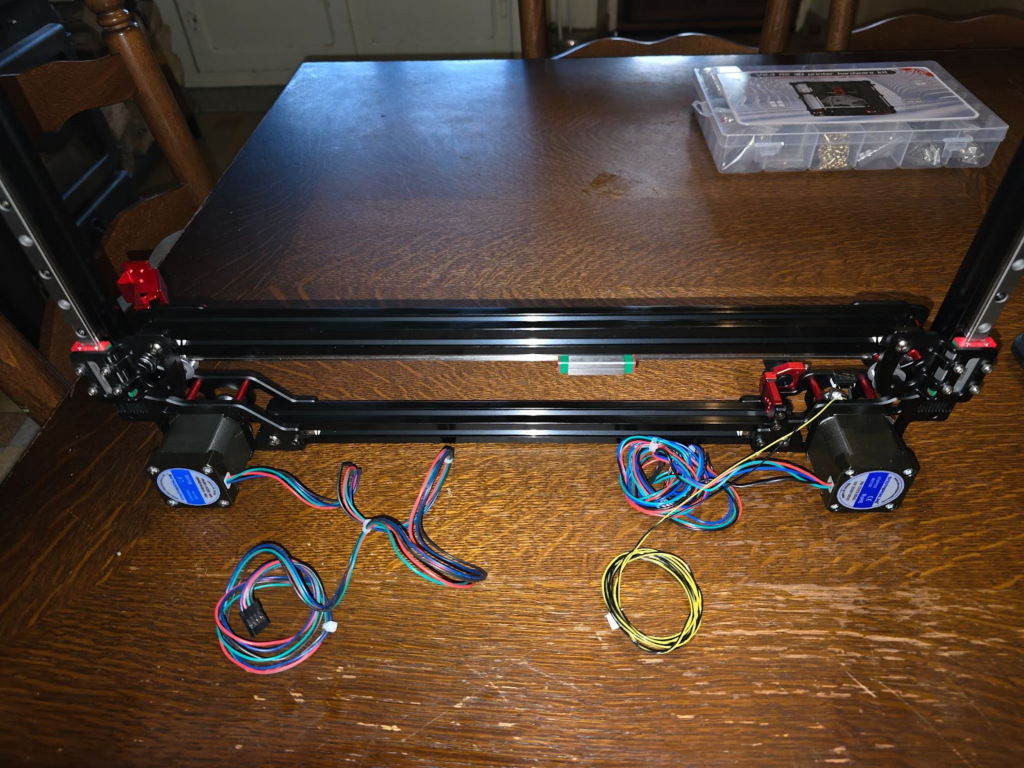
Passons maintenant au montage du portique sur la machine !
Pour cela, j’ai besoin du reste du kit de jointure de Chaoticlab
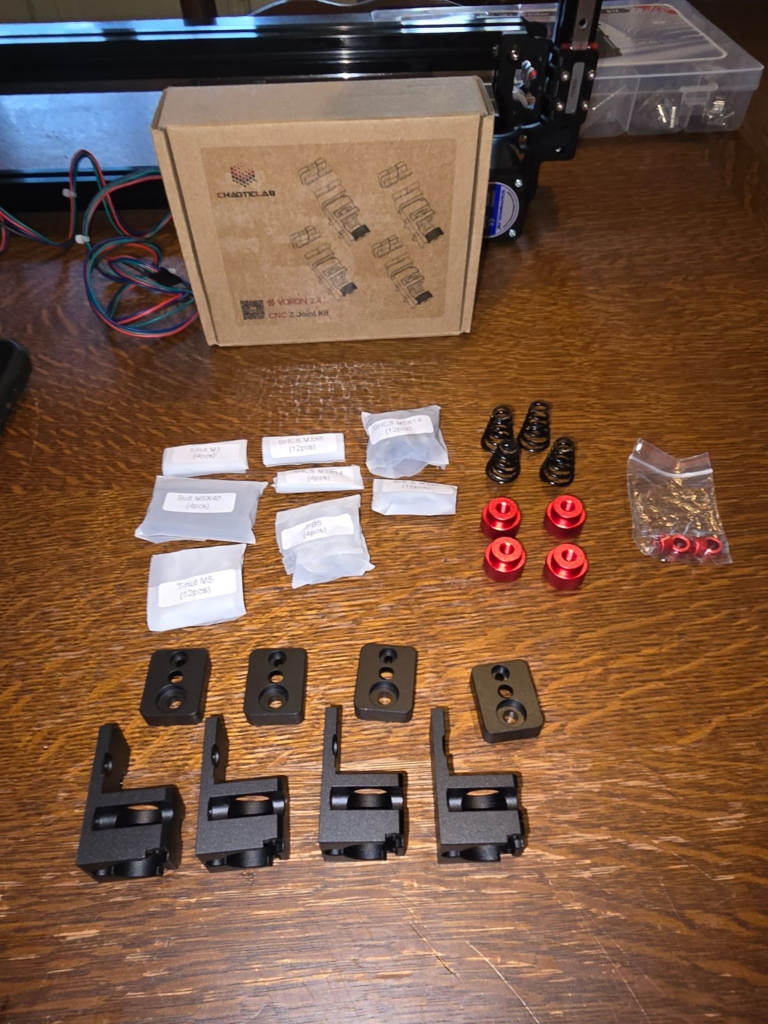
Avant de continuer, il me faut les courroies Z. Et pour avoir les longueurs, il faut se référer à la documentation car cela dépend de la taille de votre machine.
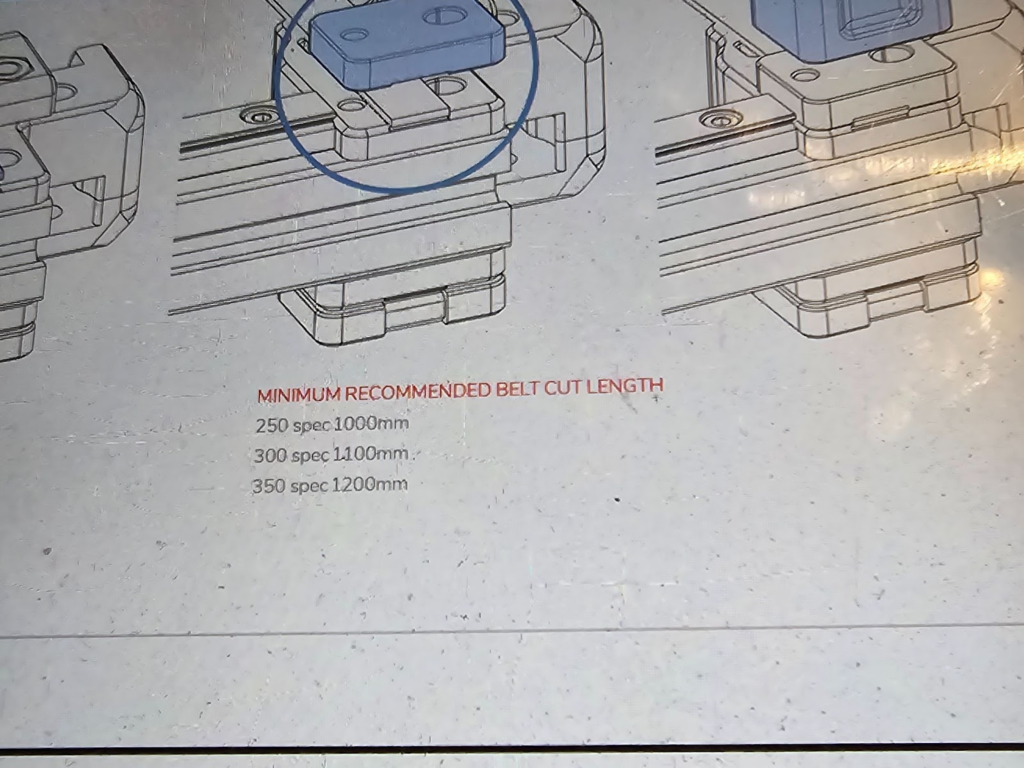
Me concernant, je suis en 350mm donc il me faut 4 courroies de 1200mm
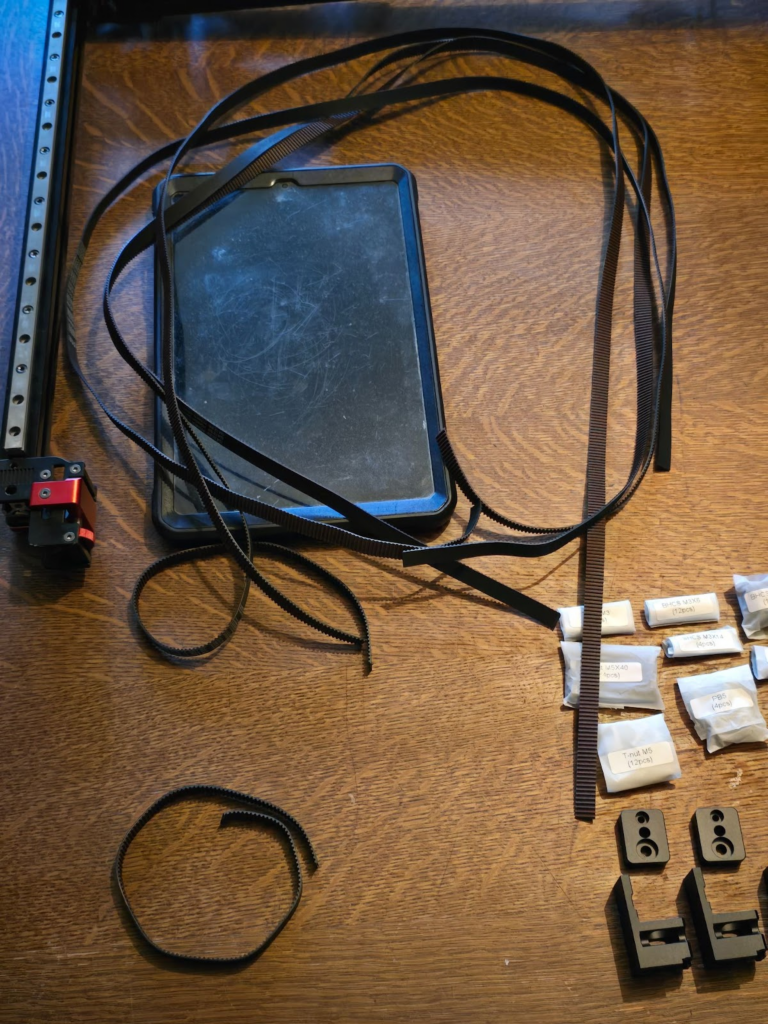
Début du montage du Kit CNC: je remarque déjà un excellente chose, la jointure se fait avec des roulements de type rotule ! C’est donc parfait vu que les quatre coins du portique sont sur des moteurs indépendants et servira donc parfaitement pour la fonction QGL (Quad Gantry leveling).
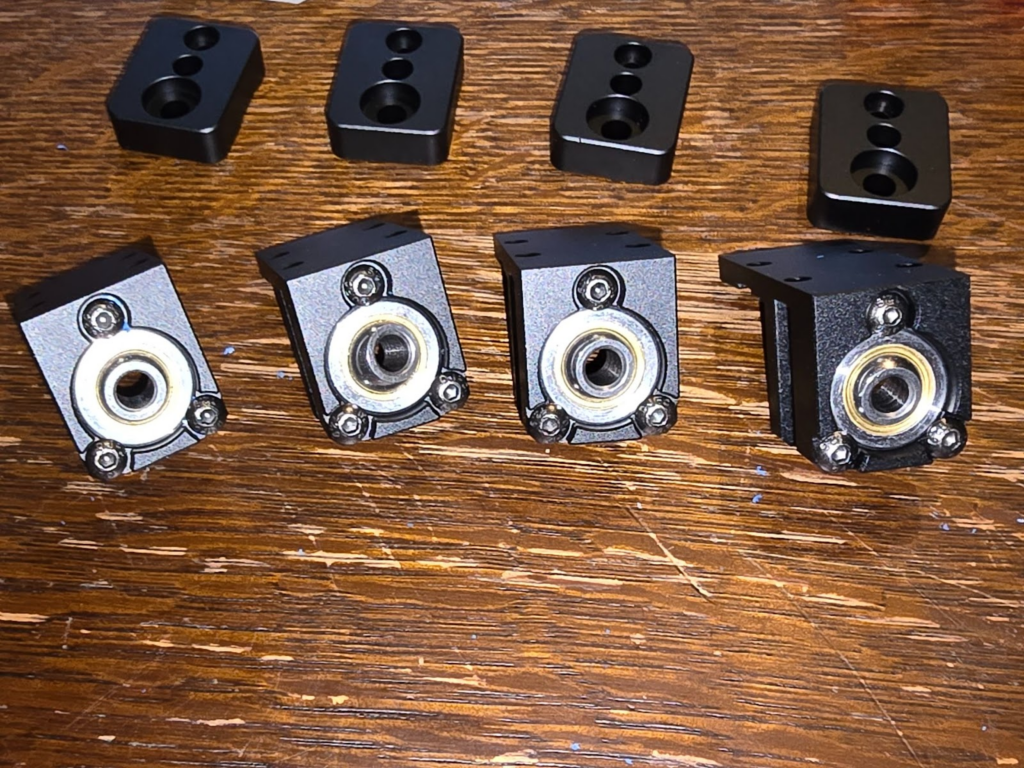
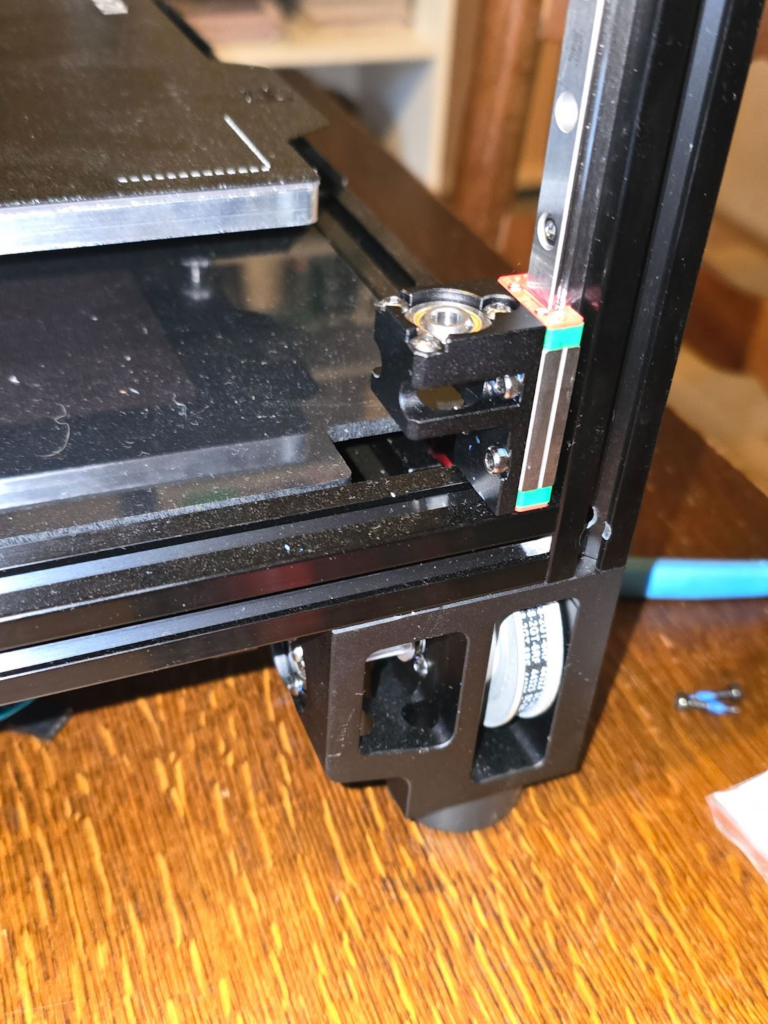
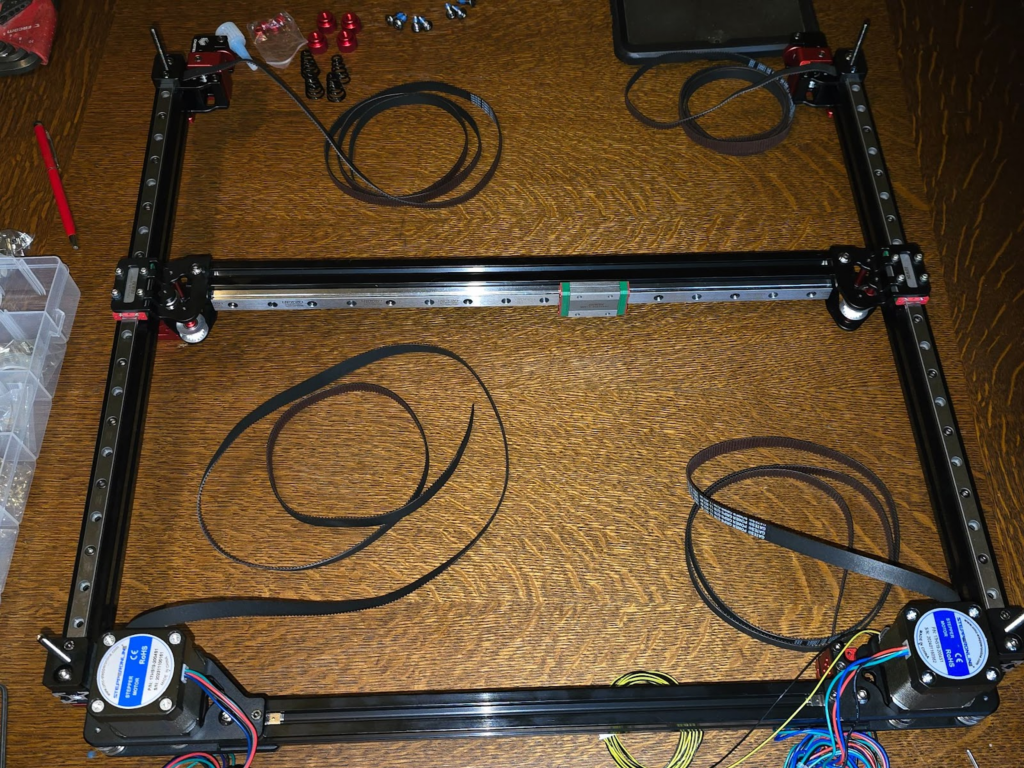
Le montage du portique sur les axes Z avec le kit de jointure Z CNC de Chaoticlab
Pour le montage du portique, la documentation Siboor fournit une astuce pour le montage:
Le suspendre avec des grands Colrings (Zipties).
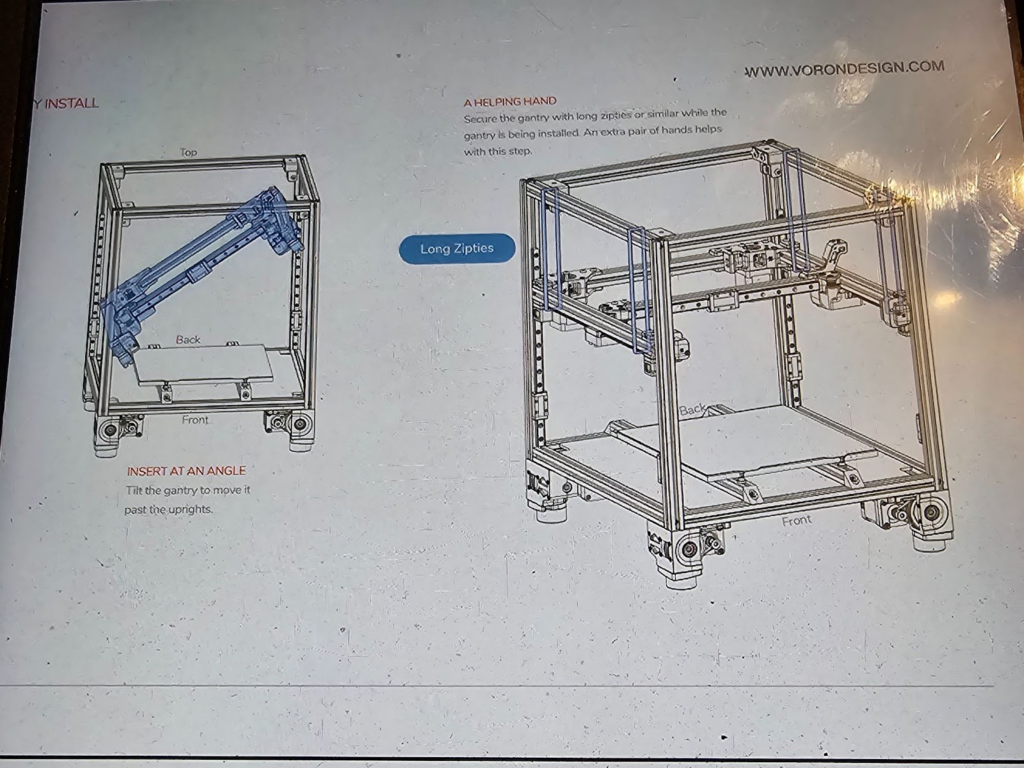
Et c’est là qu’arrive la grosse surprise dans le kit Chaotic lab ! Et pas des moindres !
Les ressorts sont carrément HS !
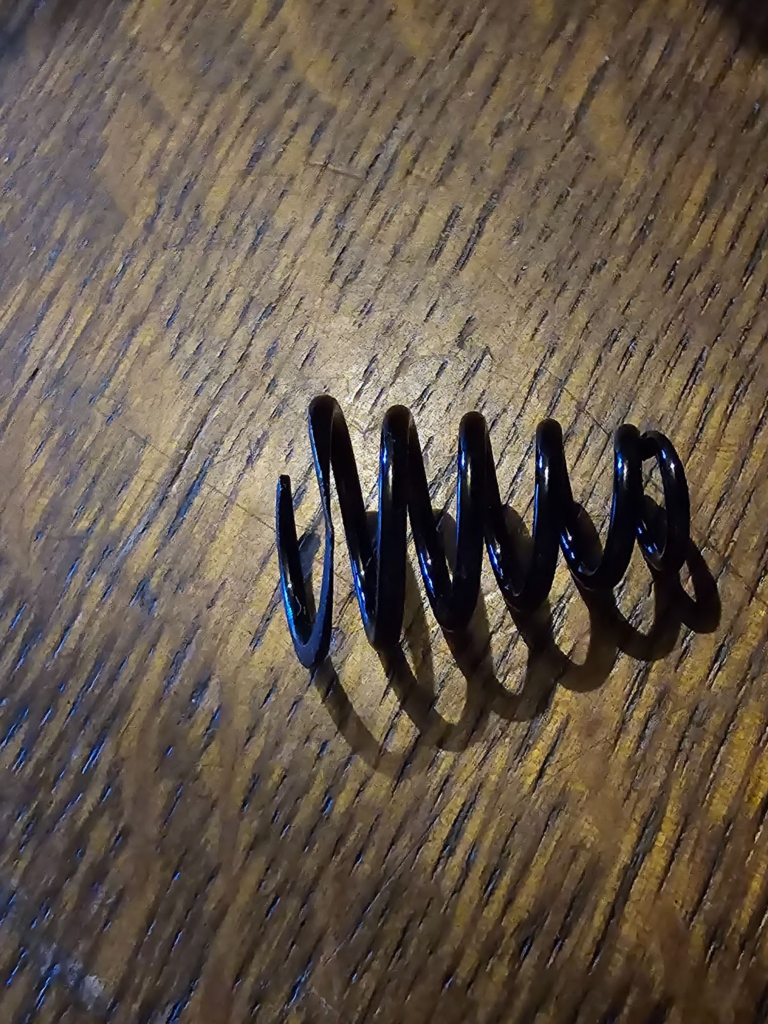
Alors, si vous vous souvenez, dans la première partie de cette suite d’articles, je vous avez expliqué que dans le kit Siboor, il manquait le Kit CNC Z drive. Et que du coup il m’avait envoyé un kit complet CNC ! et bien heureusement !
Donc pour le coup le QC de Chaoticlab n’est pas top, car pour ces pièces là, ce n’est pas Siboor qui est en cause (même s’il aurait pu checker avant de mettre le tout en carton).
Voila la comparaison des ressorts !
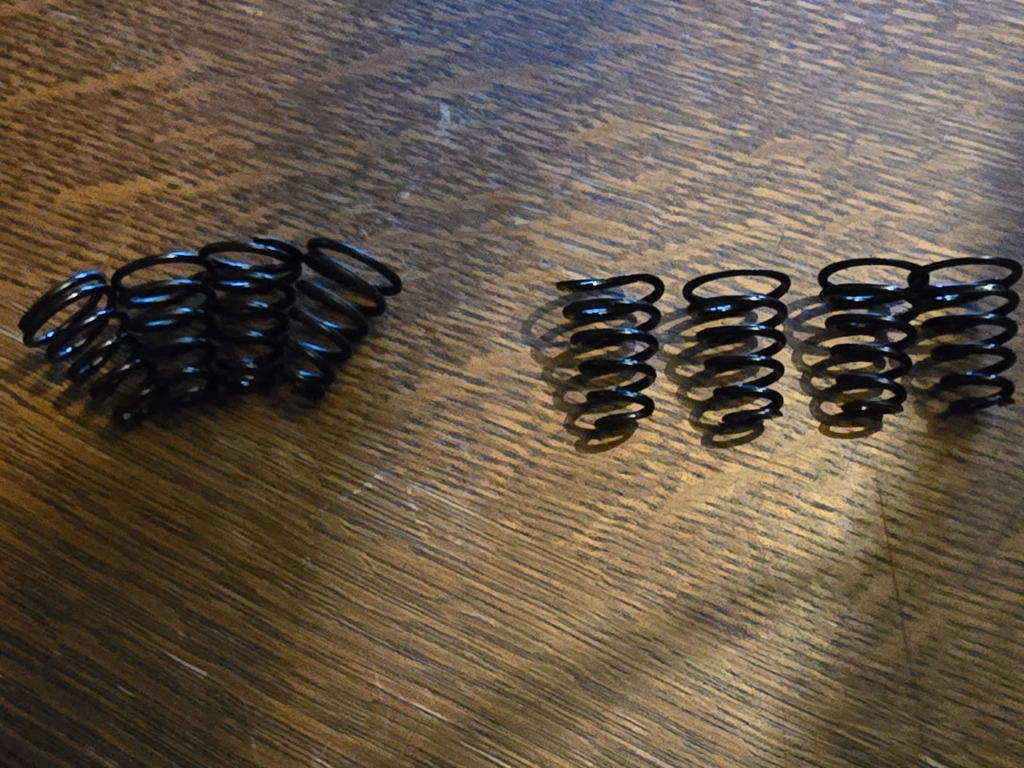
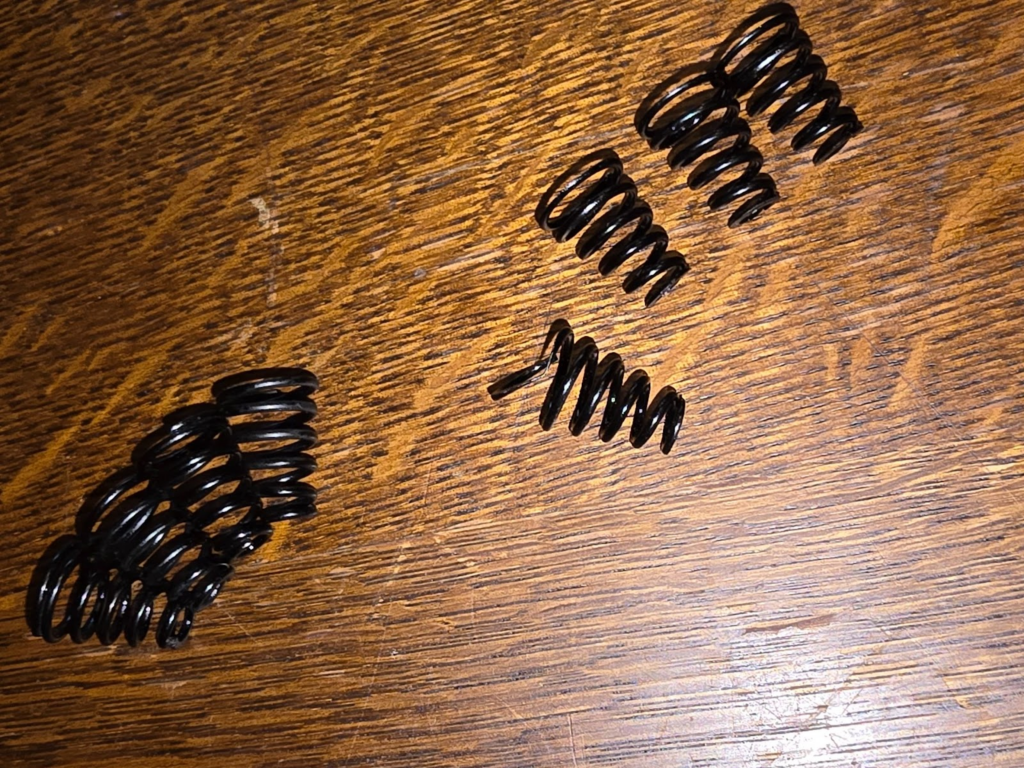
Après l’installation du portique, regardez bien, car il y a quelque chose qui ne va pas !
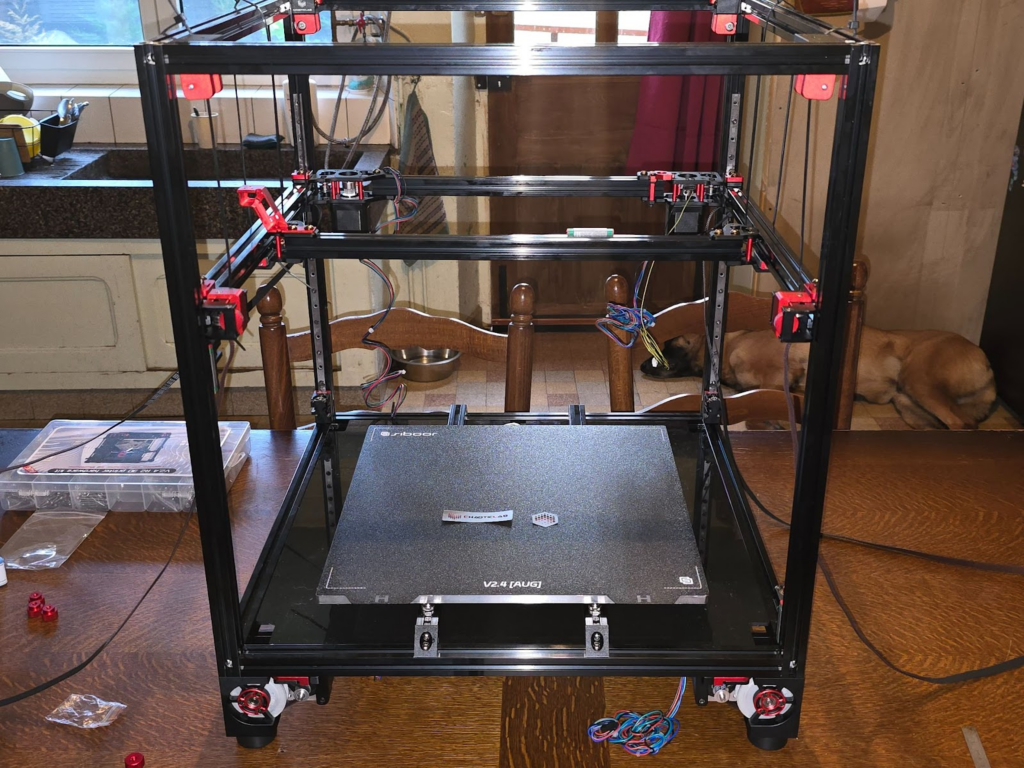
L’axe X est monté à l’envers ! D’où l’importance de toujours vérifier son travail !
Du coup rectification :
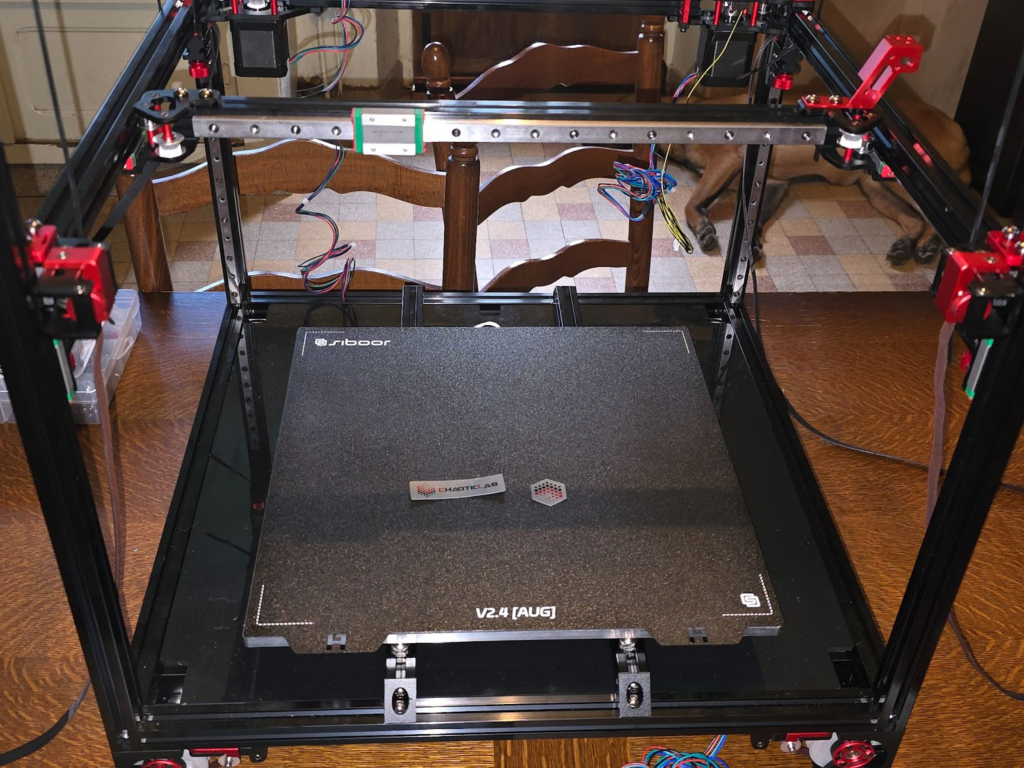
Et enfin, montage des courroies dans leurs logements :
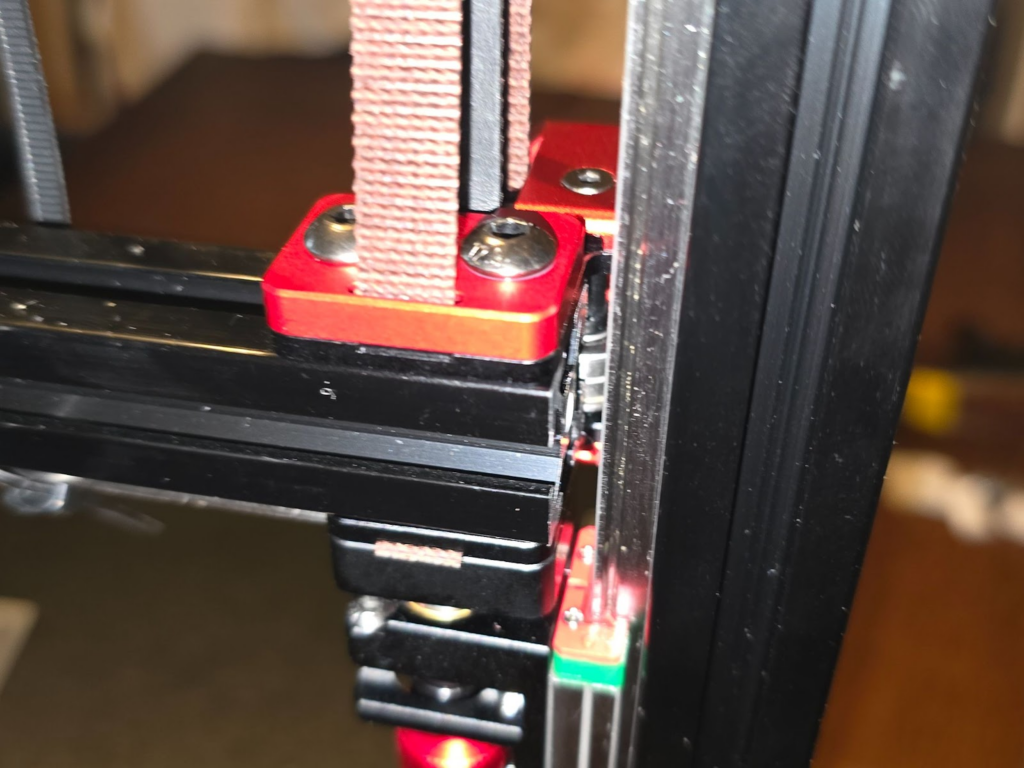
Et donc, pour les bloqueurs de courroie, du côté des tensionneurs, il faut des vis M5x14 BHCS et pas des M5x16 BHCS.
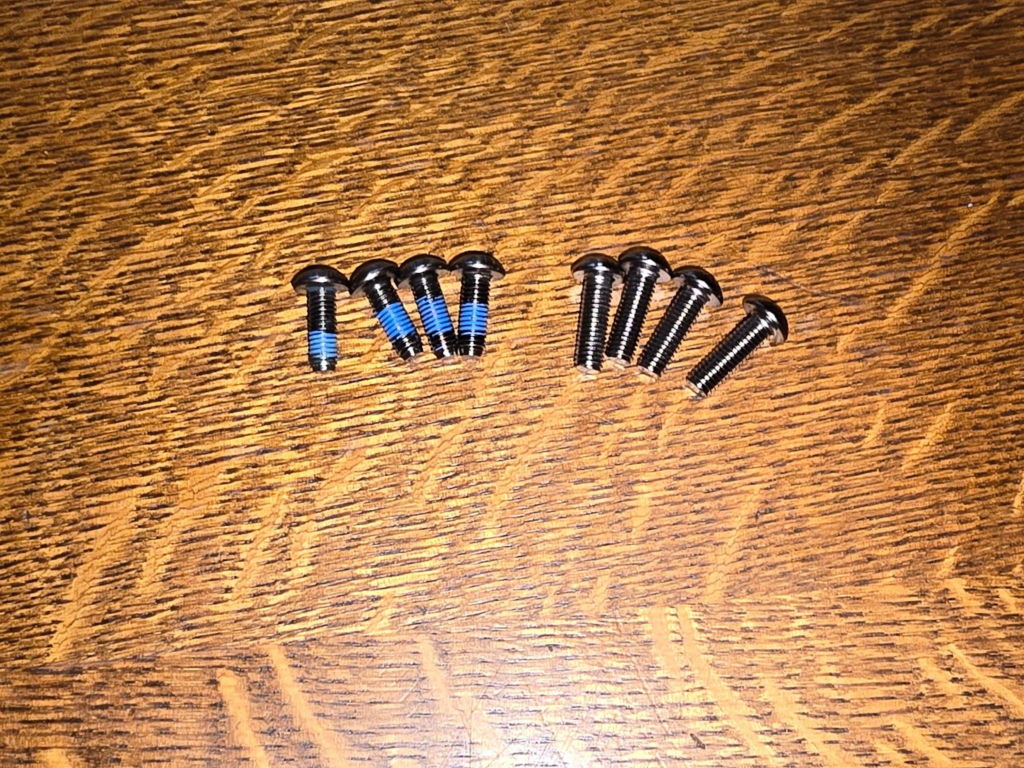
Finalisation du montage :
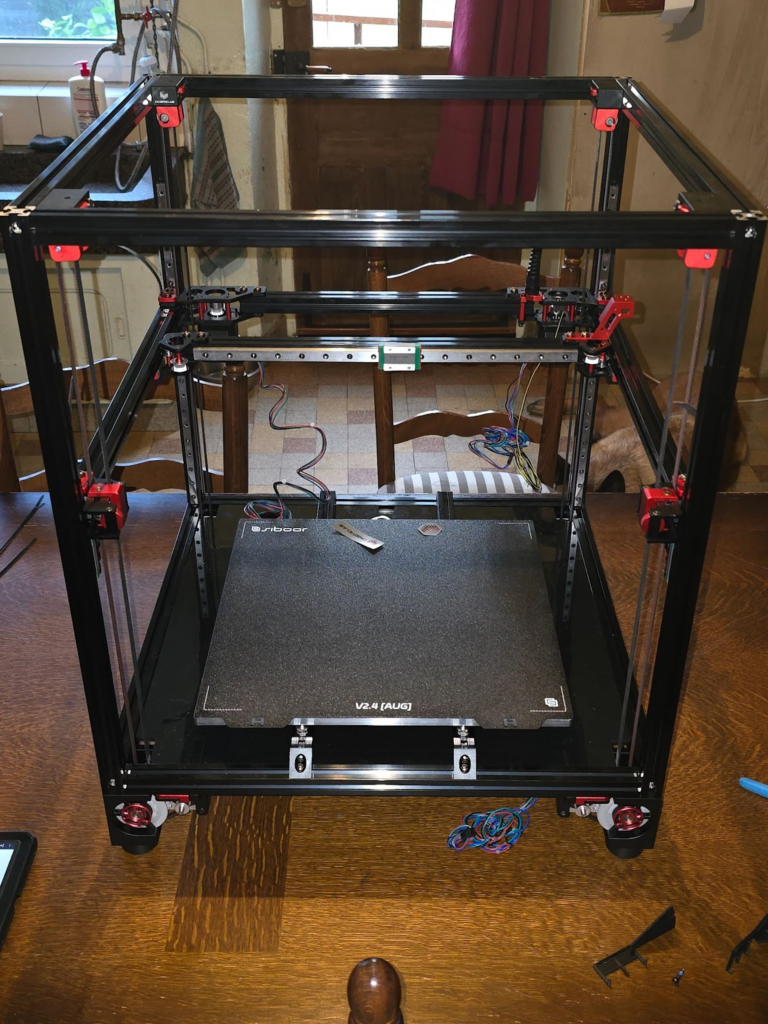
Puis alignement, enfin plutôt contrôle de la rectitude de l’ensemble.
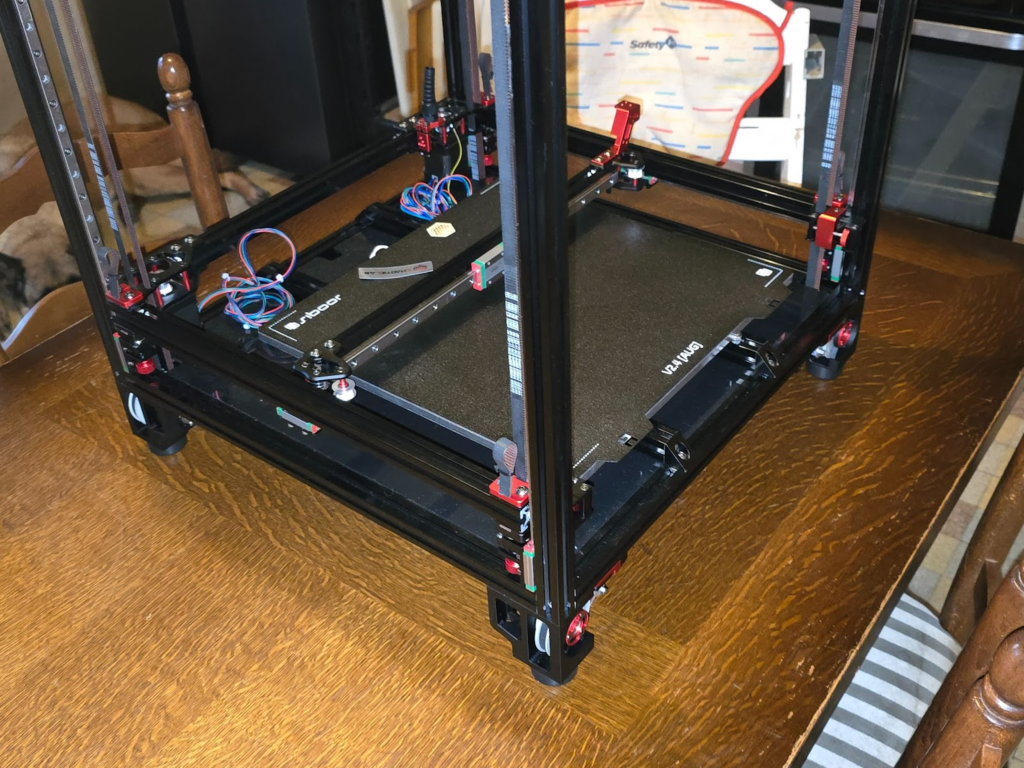
Et enfin, passage des courroies A et B avec montage du support de la tête ( support CNC lui aussi ).
Au passage: montage du endstop X et du module cartographer. Ce module, fournit par Siboor sert à 3 choses : Z end stop, Mesh leveling et comme il embarque une puce ADXL, il servira pour l’input shapping.
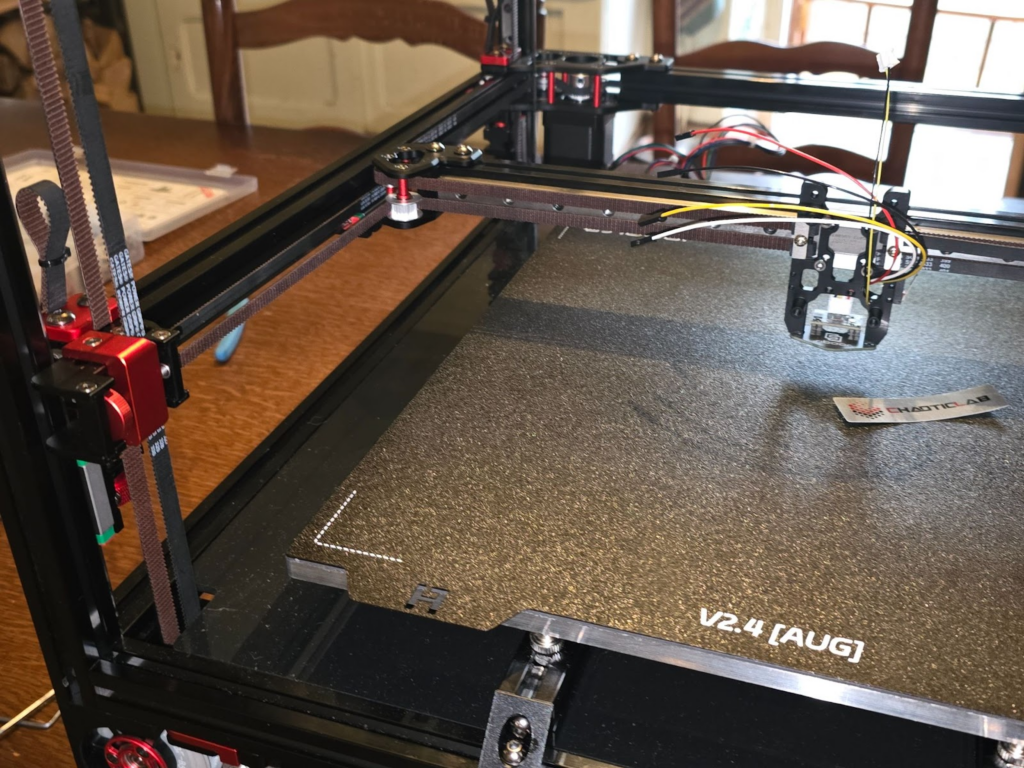
Voilà, la cinématique de la machine est finie ! J’en suis à environ 7h de montage.
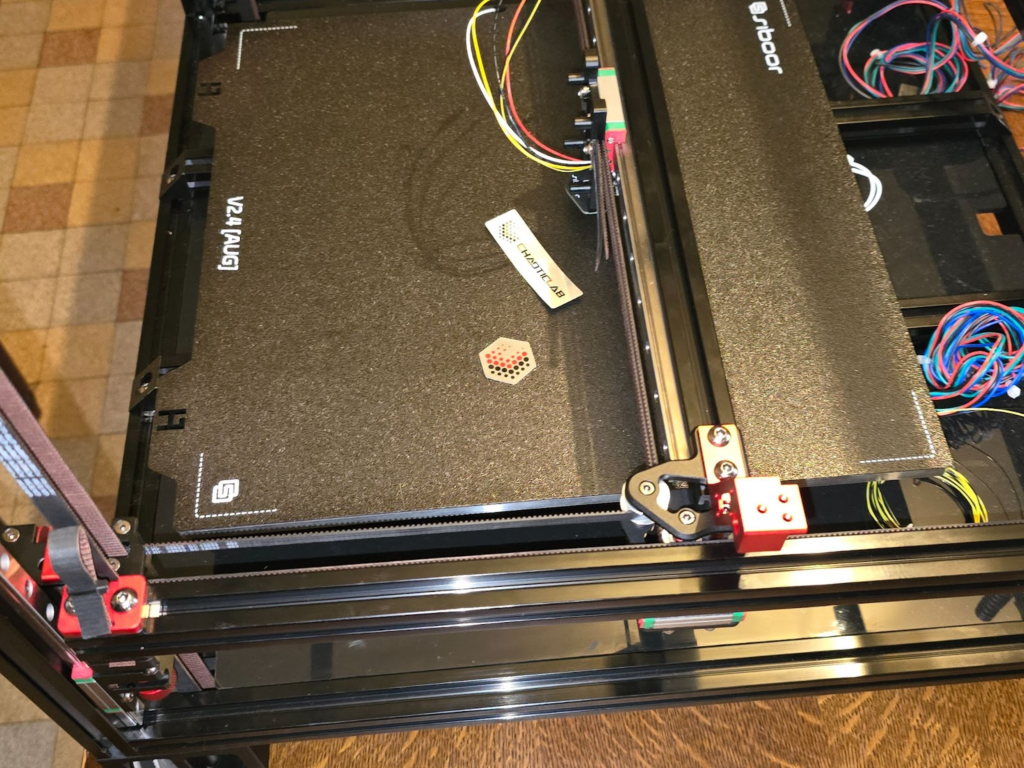
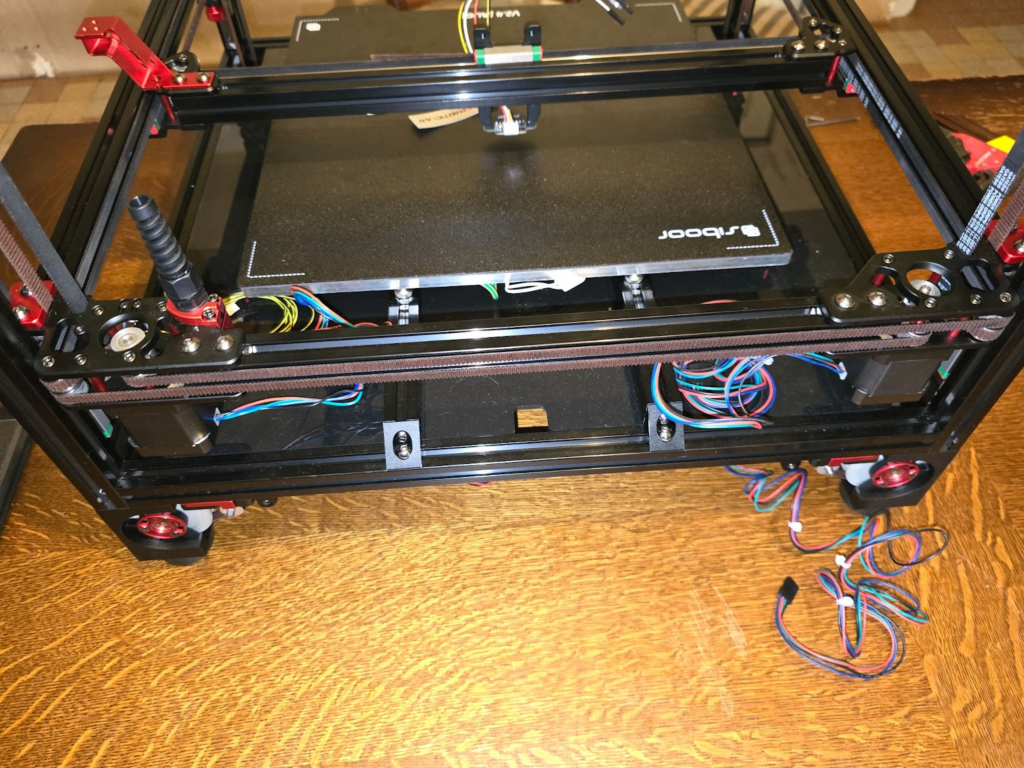
La tête Stealthburner
Après le long montage précédent, voici le moment du montage de la partie sans laquelle une imprimante 3D n’en serait pas une : la tête d’extrusion. Sur ce modèle, elle est nommée Stealthburner.
J’imagine parce qu’elle est plus silencieuse que la version précédente.
Voici les parties du Stealthburner.
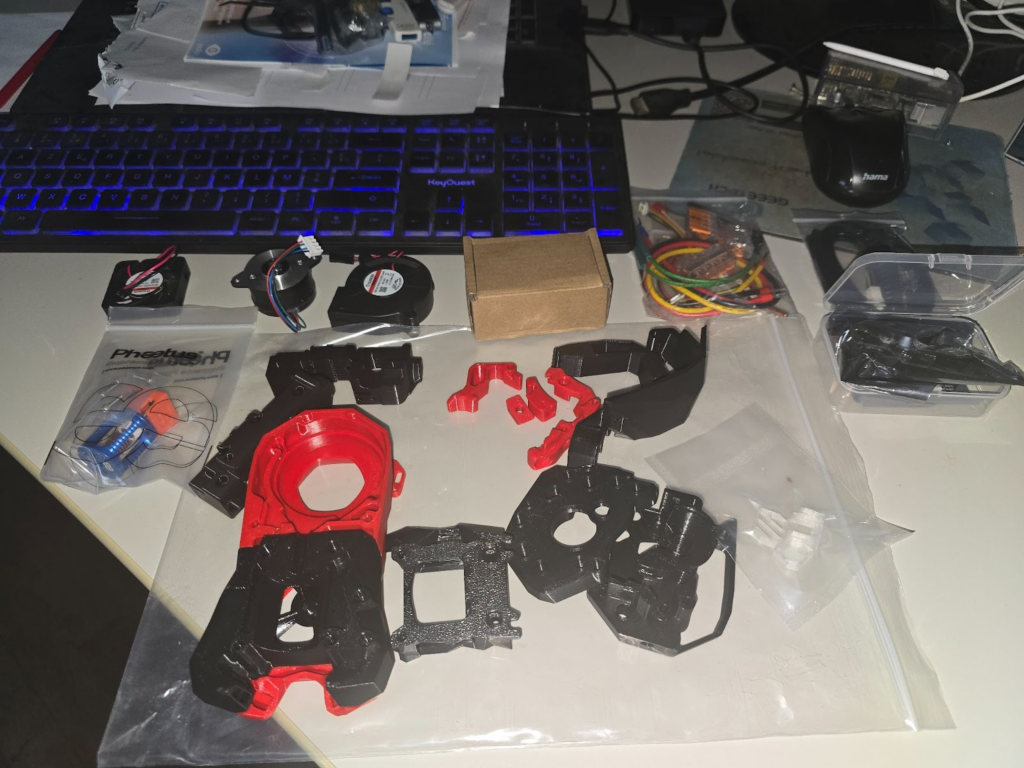
Je commence l’assemblage par l’extrudeur de type BMG.
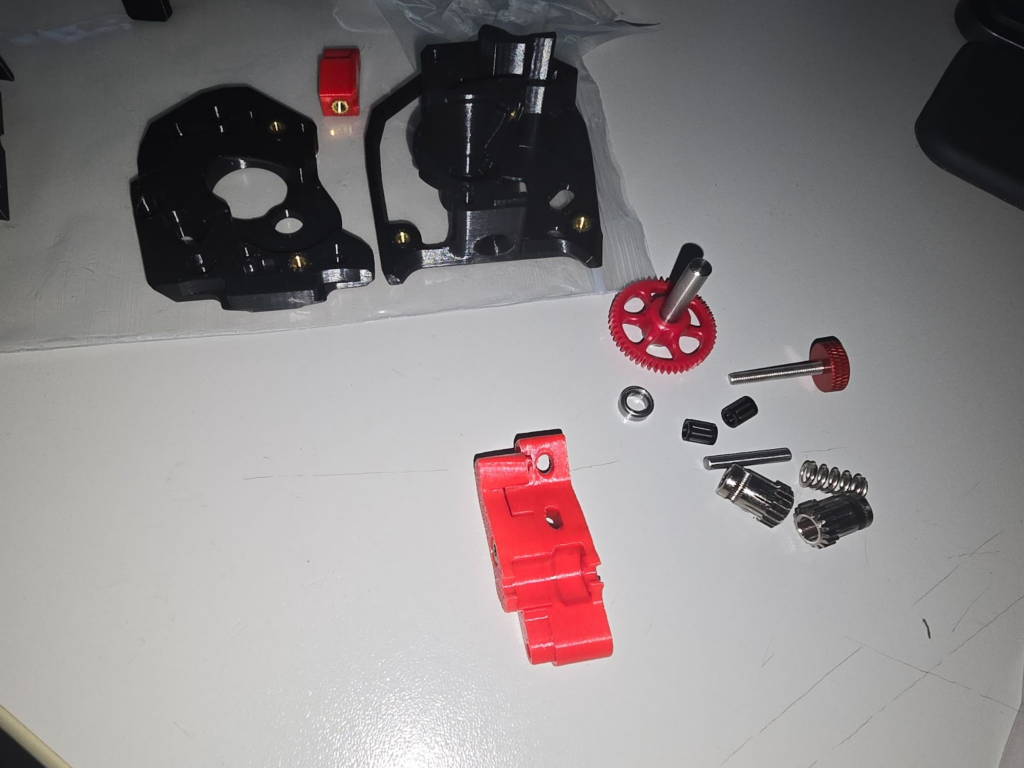
Alignement des engrenages BMG à l’aide d’un bout de filament.
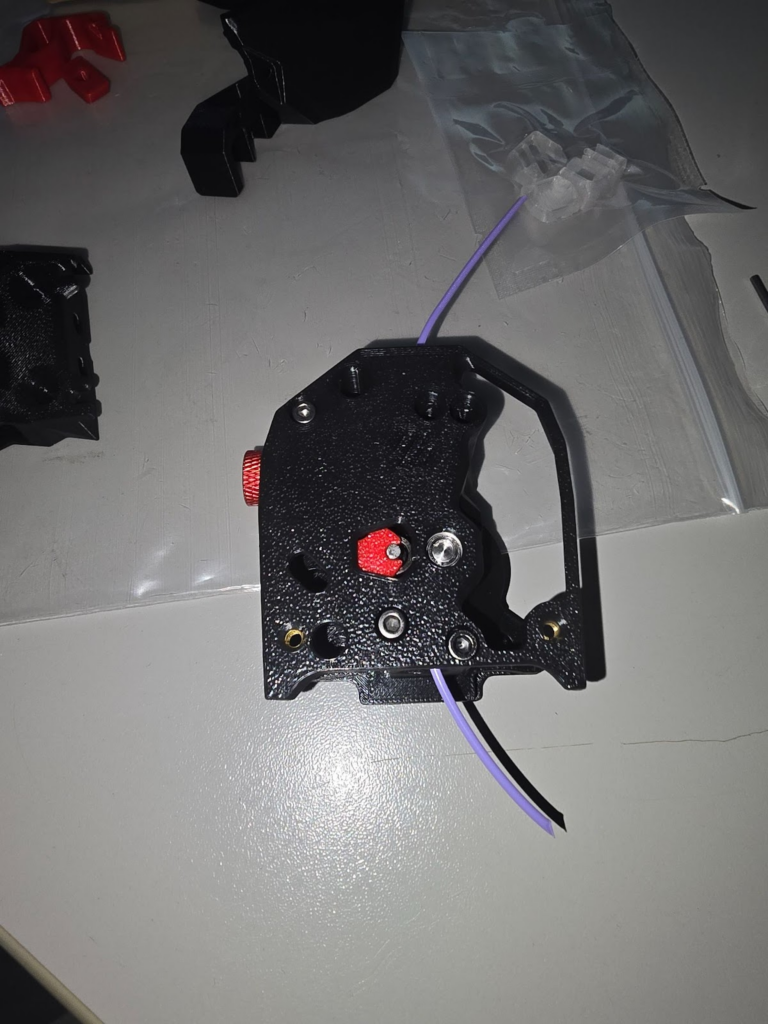
Assemblage du moteur ‘PanCake’
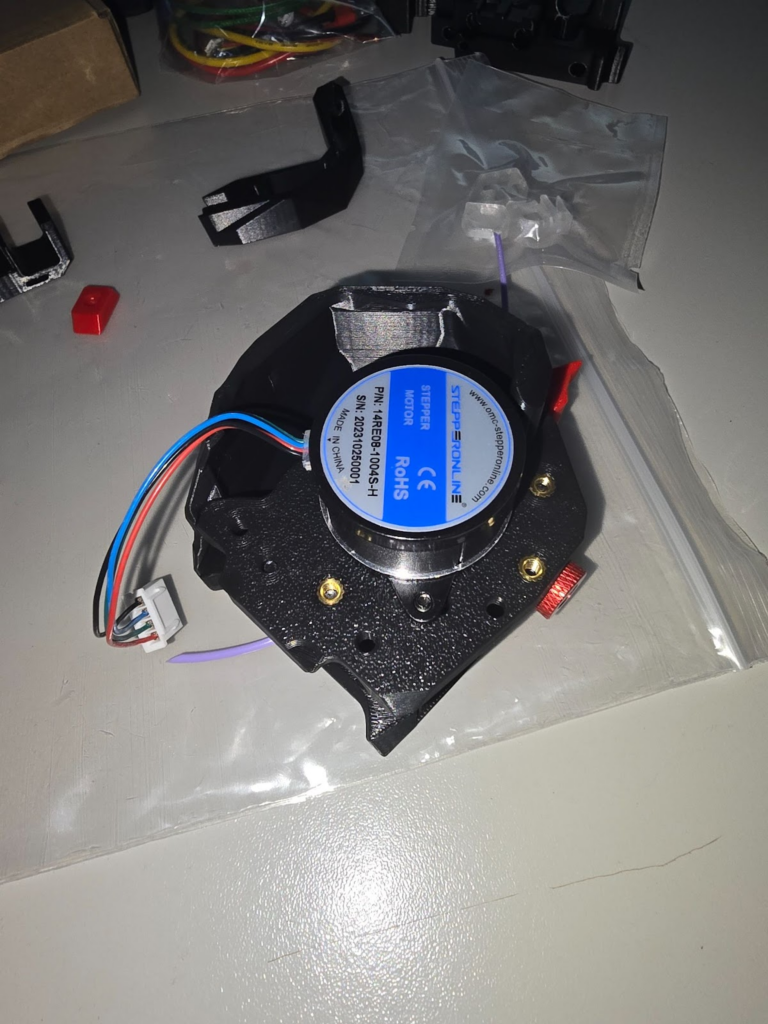
Et enfin mise en place du verrou.
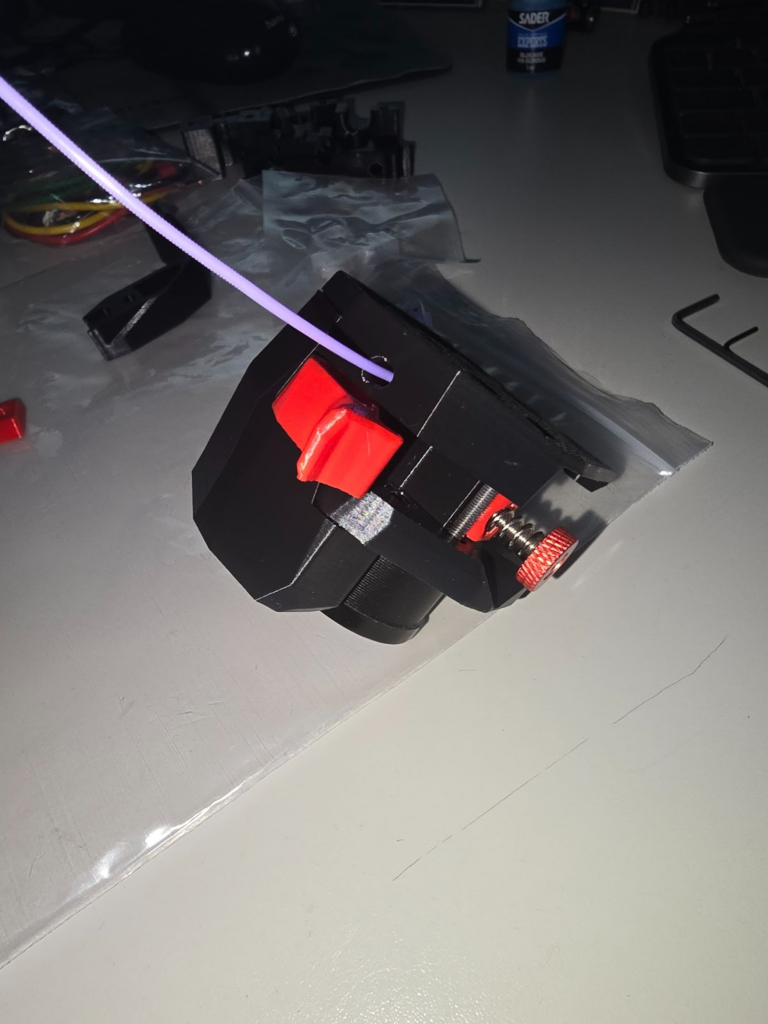
Préparation du Hotend Dragon de chez Phaetus. Cette tête est livrée avec une cartouche 24v de 65W et une sonde de température PT1000. La documentation de phaetus spécifie aussi que cette tête peut monter jusqu’à 500°C ! Hot ! je verrai à l’usage.
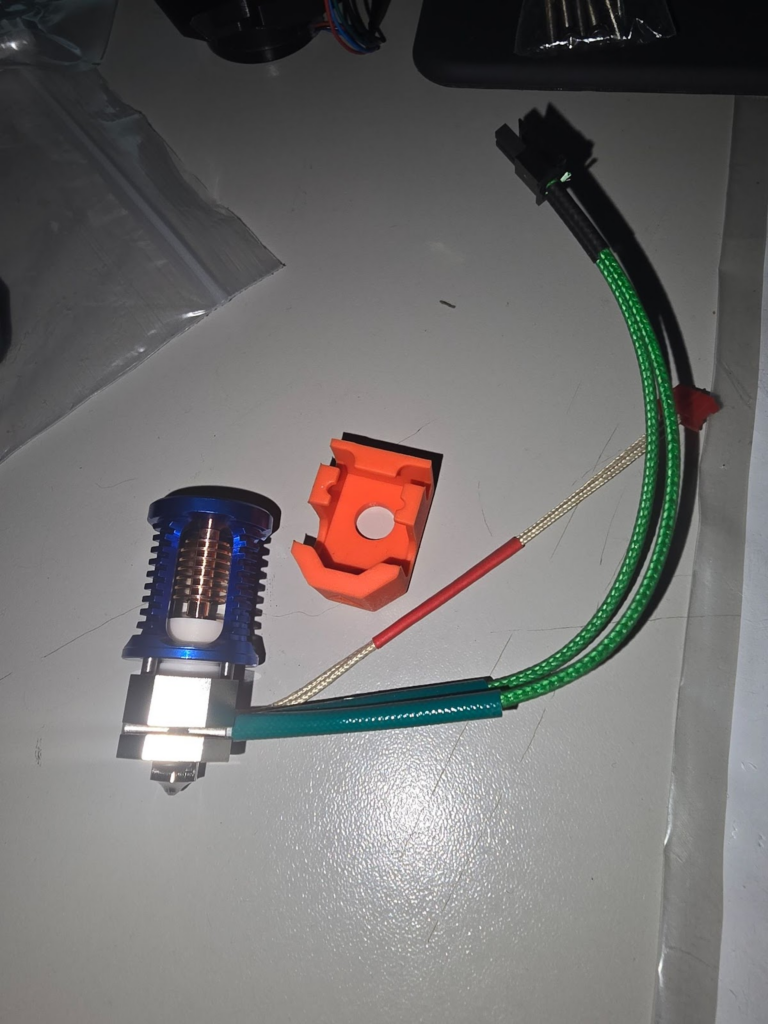
Montage de la tête dans le bloc inférieur.
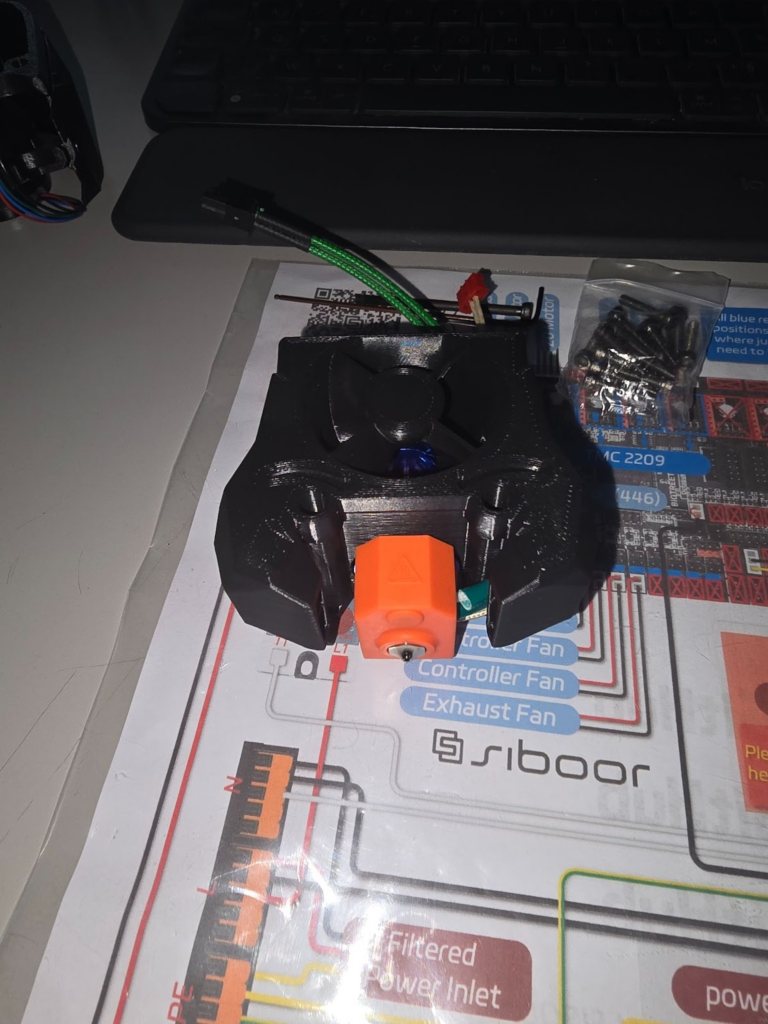
Le bloc supérieur avec l’extrudeur et le bloc inférieur avec la hotend prêt pour le mariage !
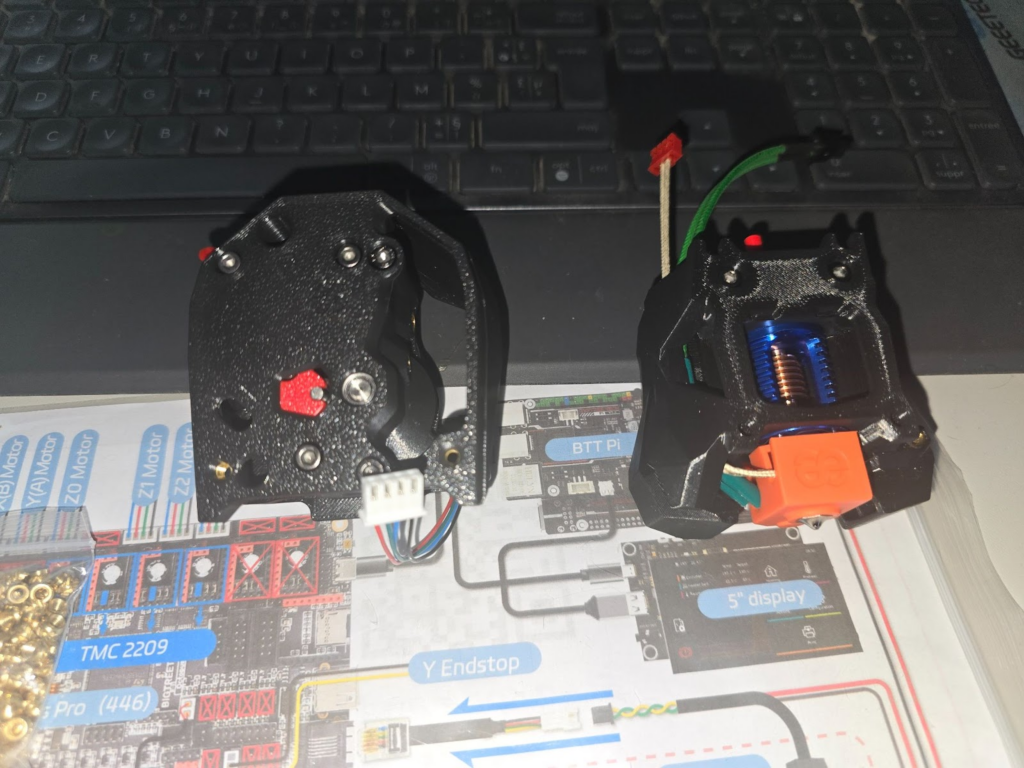
Préparation du couvercle avec la mise en place des leds d’éclairage “NeoPixel”
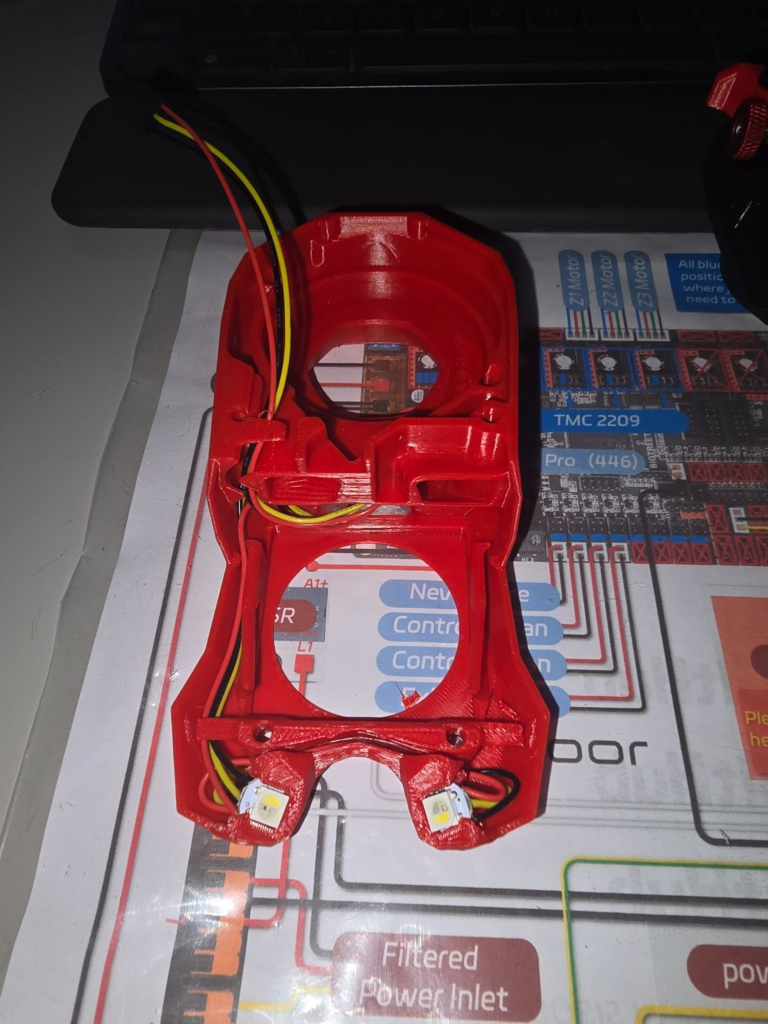
Préparation du blower Sunon. Cette partie est un peu déstabilisante car il faut ouvrir en deux le ventilateur et couper les oreilles de fixation.
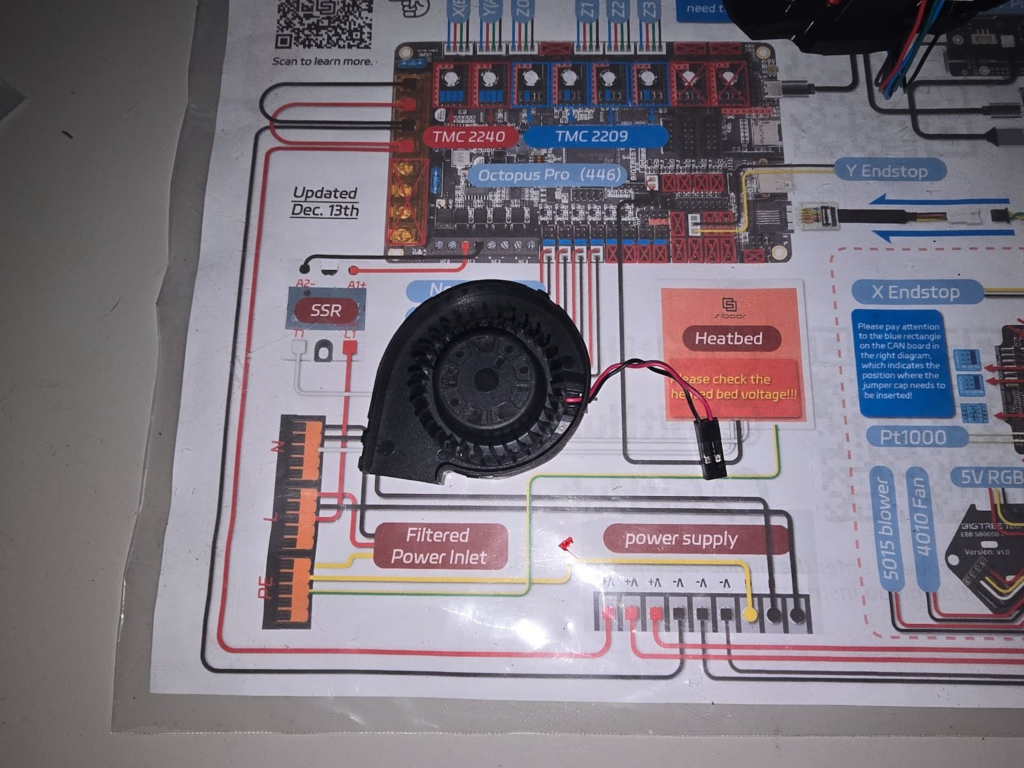
Puis mise en place du blower ‘préparé’ et du ventilateur de refroidissement de la hotend.
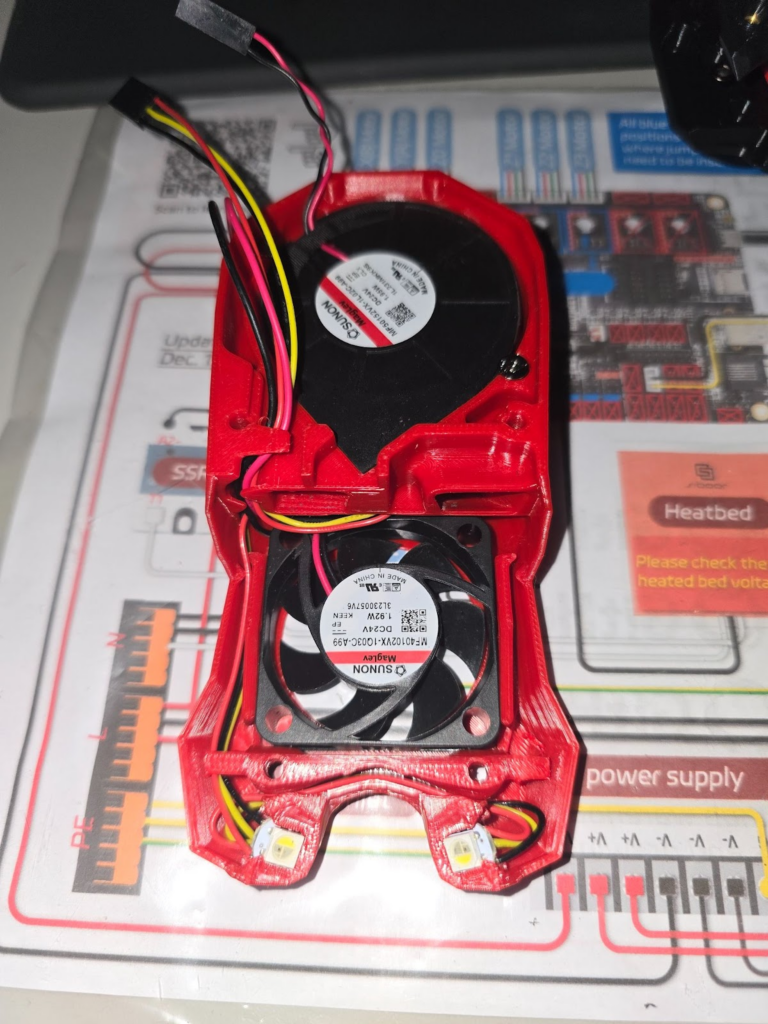
Début de l’installation de l’ensemble sur le châssis et passage des câbles.
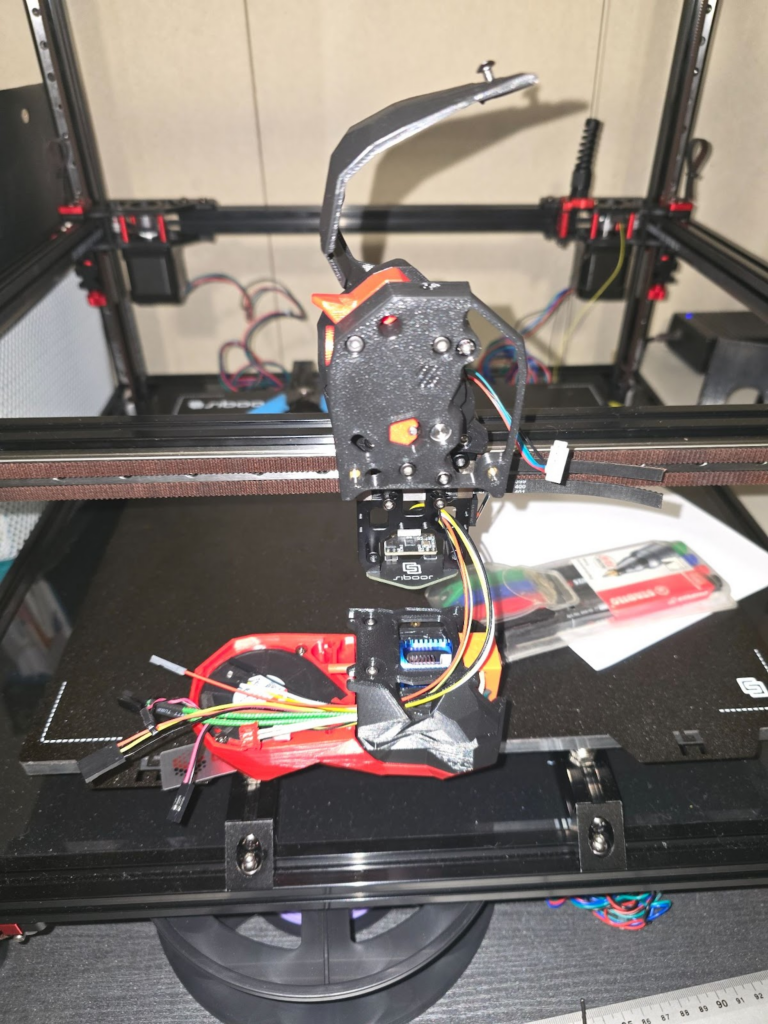
Mise en place de la plaque de câblage de la carte SB2209.
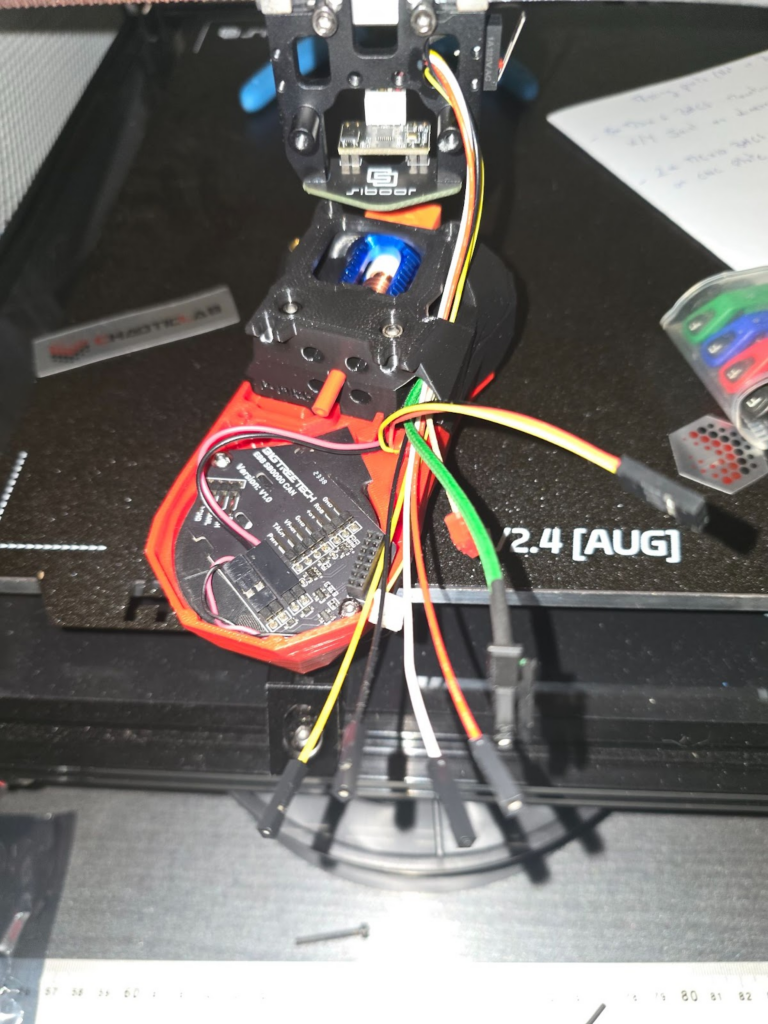
Dans la documentation, la partie principale de la carte SB2209 est fixée avec des vis M3x10 BHCS cependant encore un petit souci ….
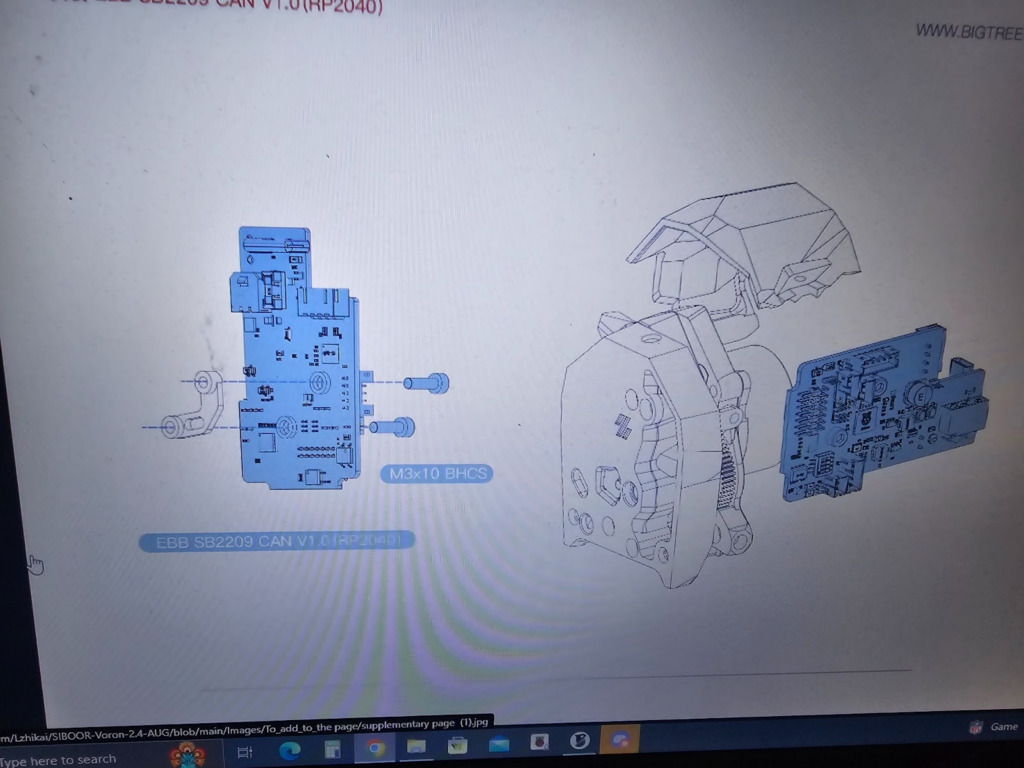
Aucune vis M3x10 BHCS n’est livrée avec le kit ! Je dois prendre dans mon stock !
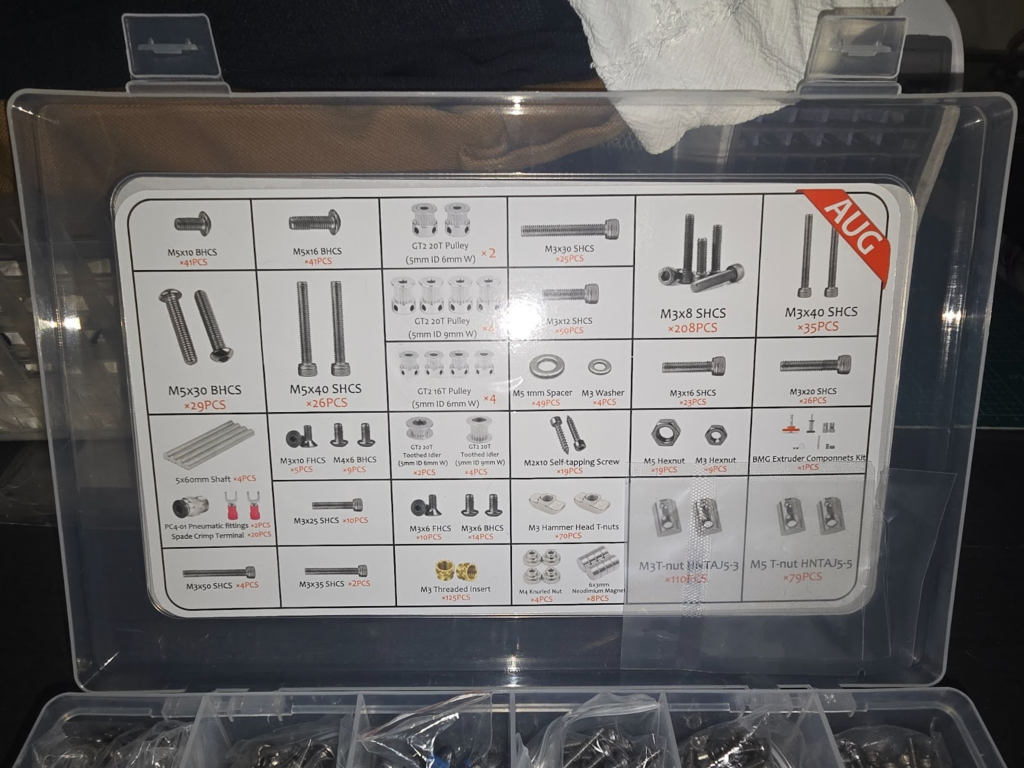
Et enfin mise en place de tous les éléments et câblage.
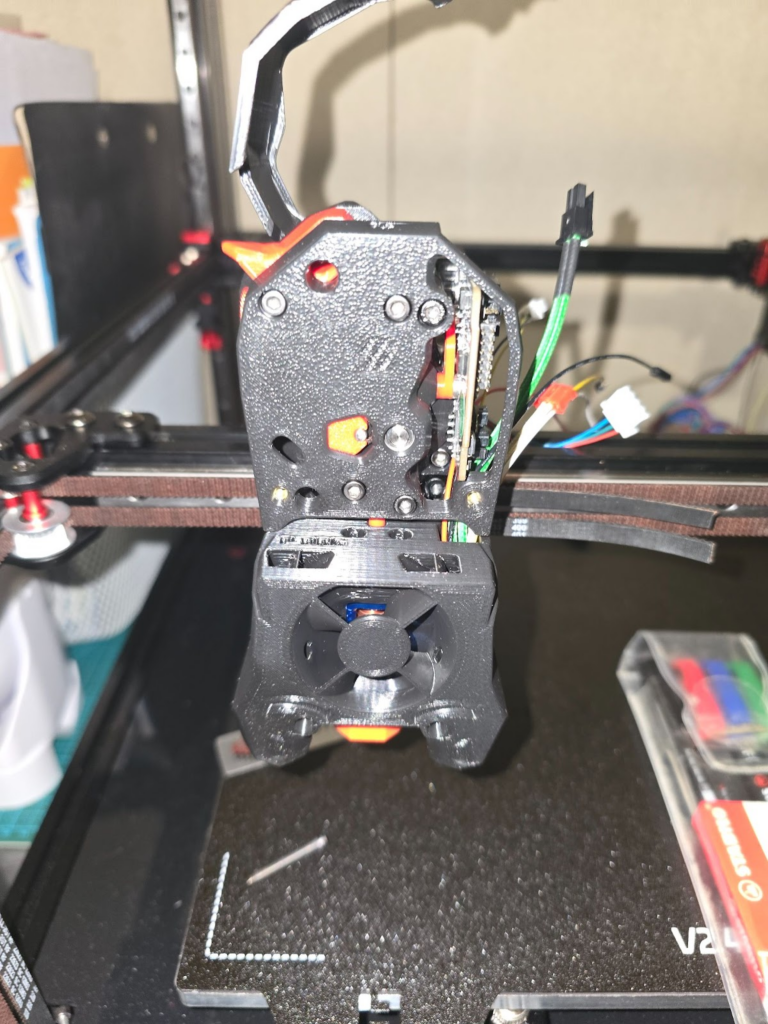
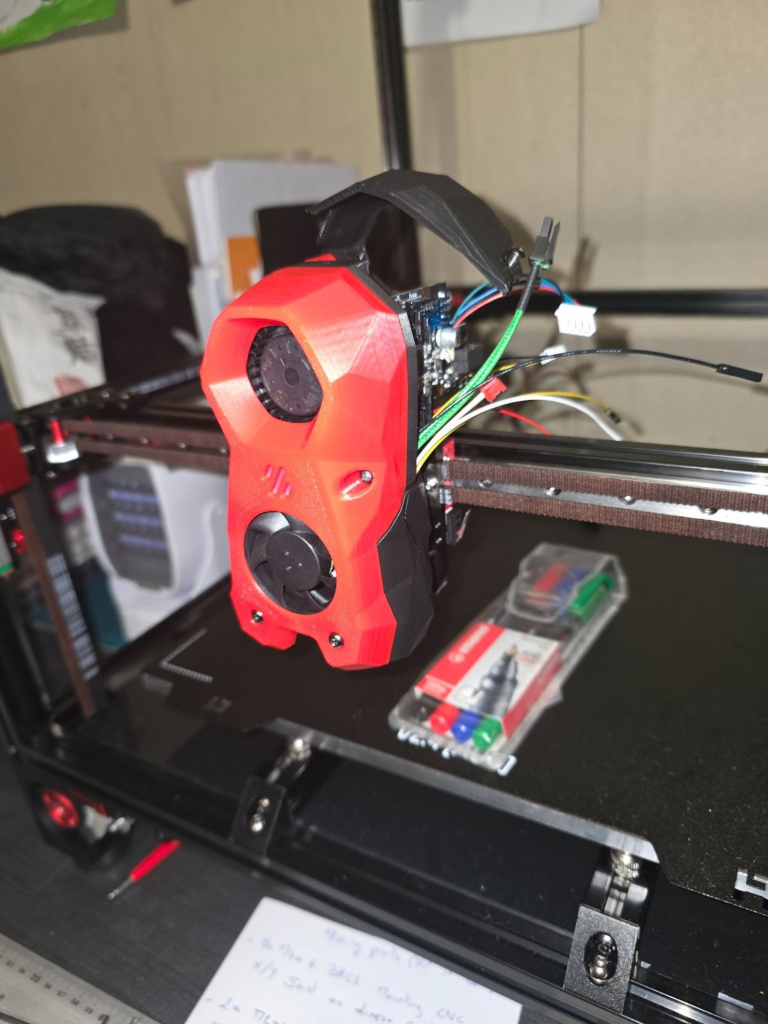
Le système est vraiment bien conçu et le câblage est propre.
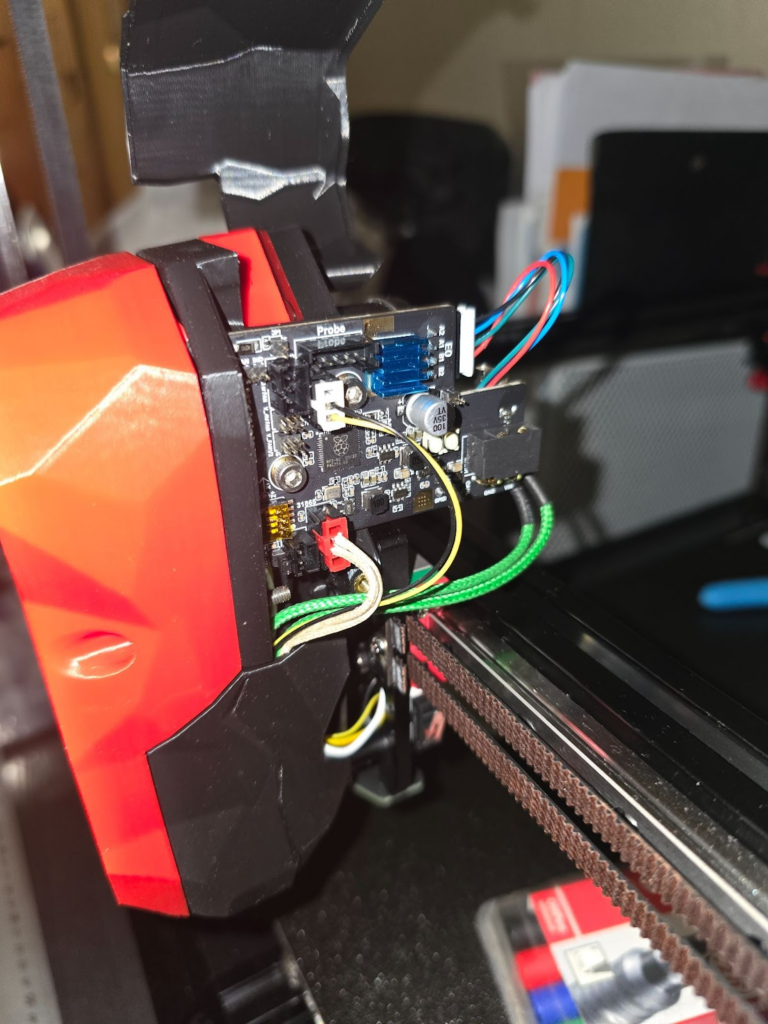
La dernière étape est la mise en place de la tige d’acier pour le maintien du câble CAN.
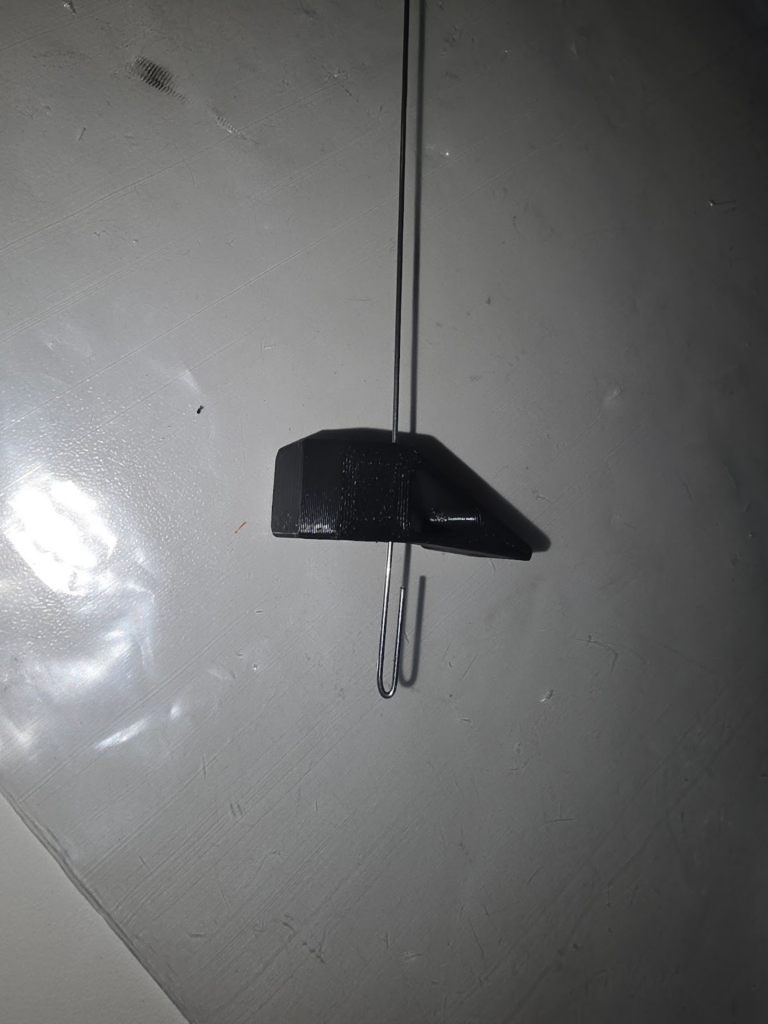
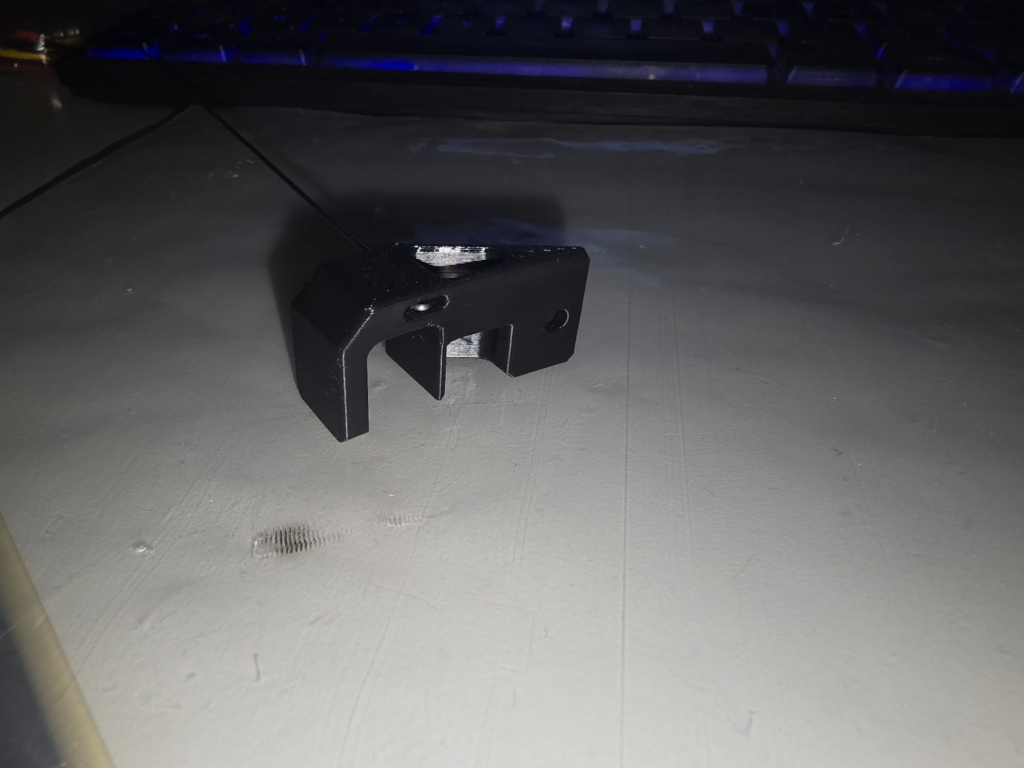
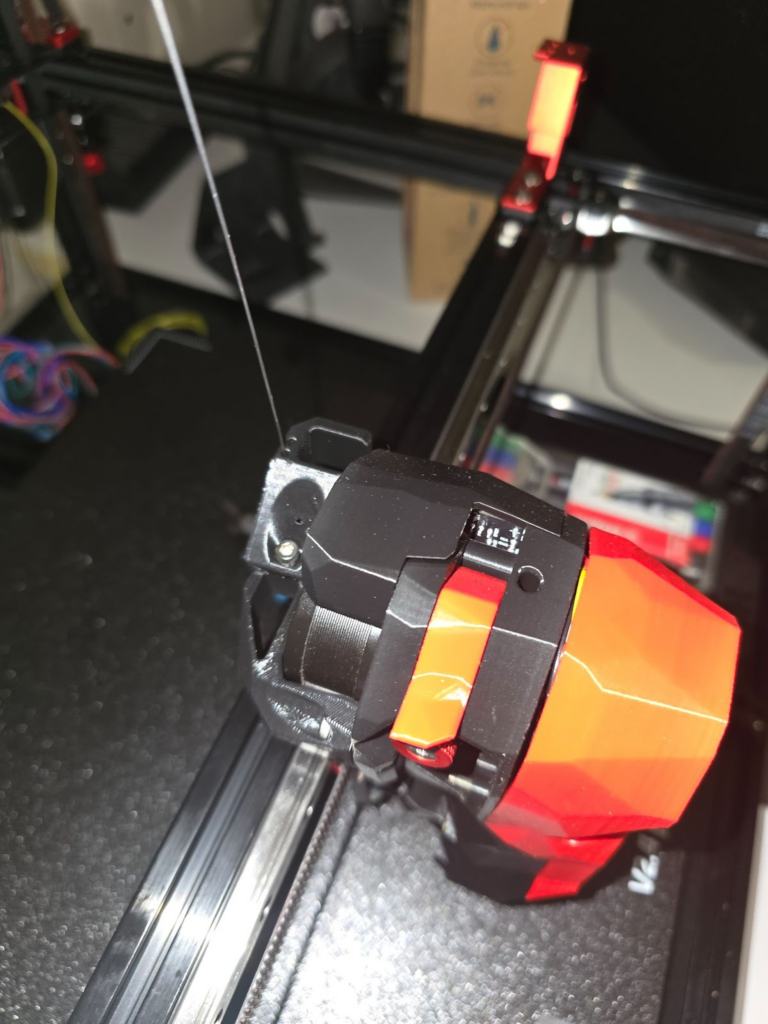
Le connecteur PG7 qui se visse dans le portique est livré avec de la gaine tressée, qui permet de maintenir le câble CAN contre la tige d’acier.
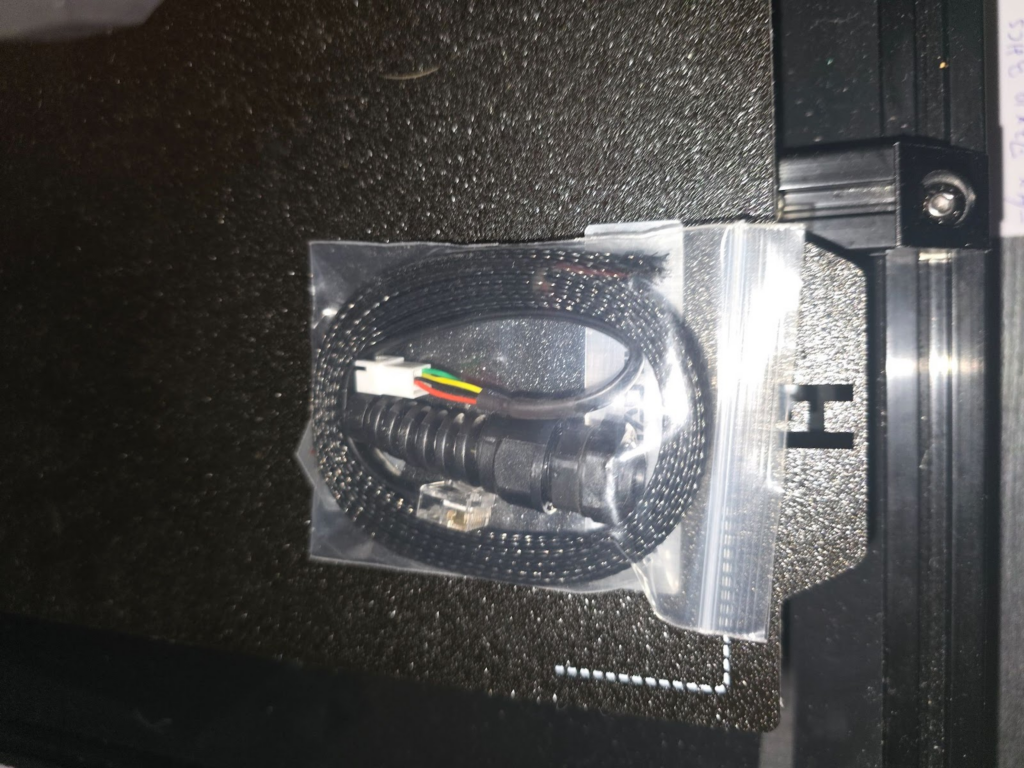
Et mise en place de l’ensemble !
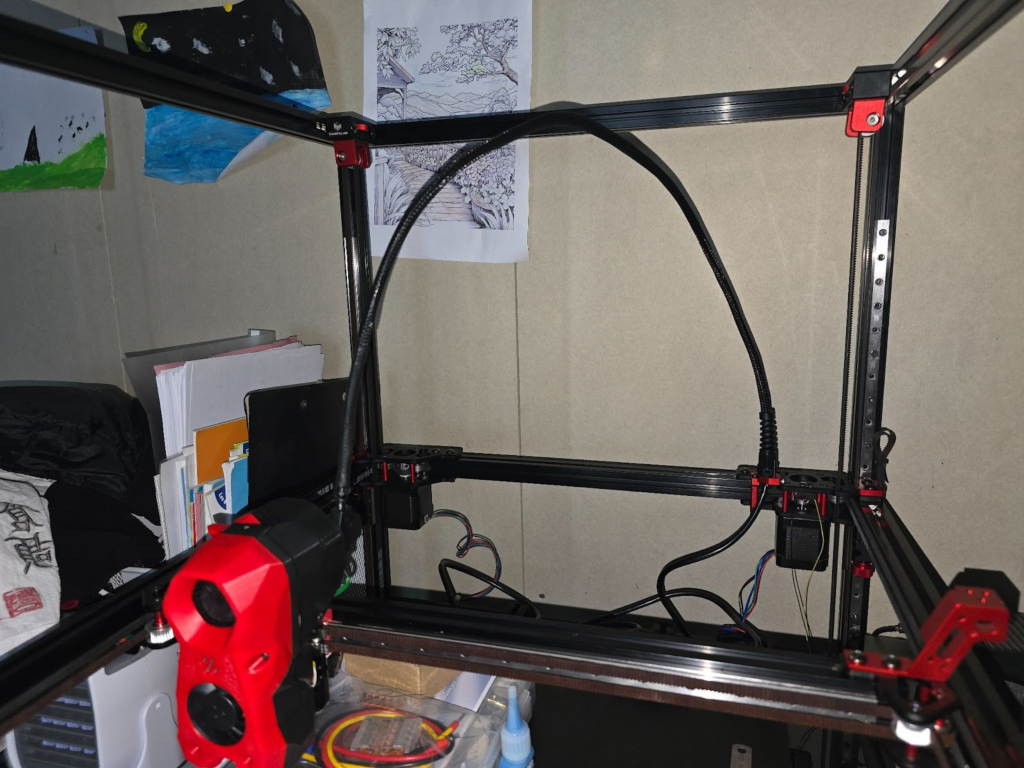
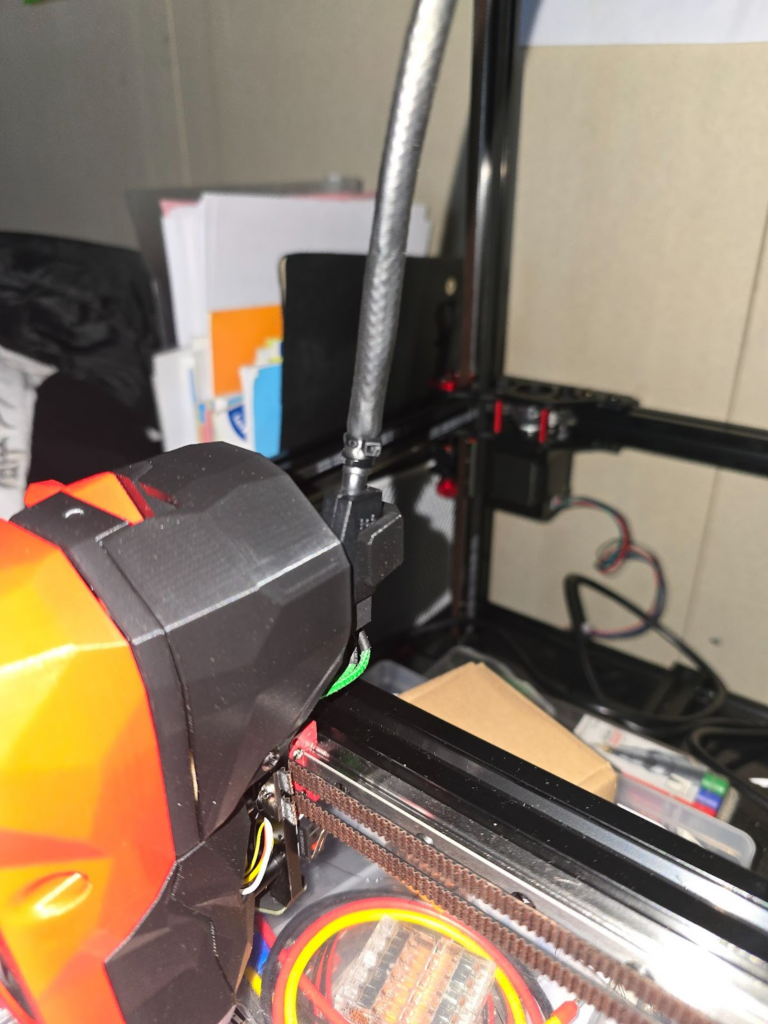
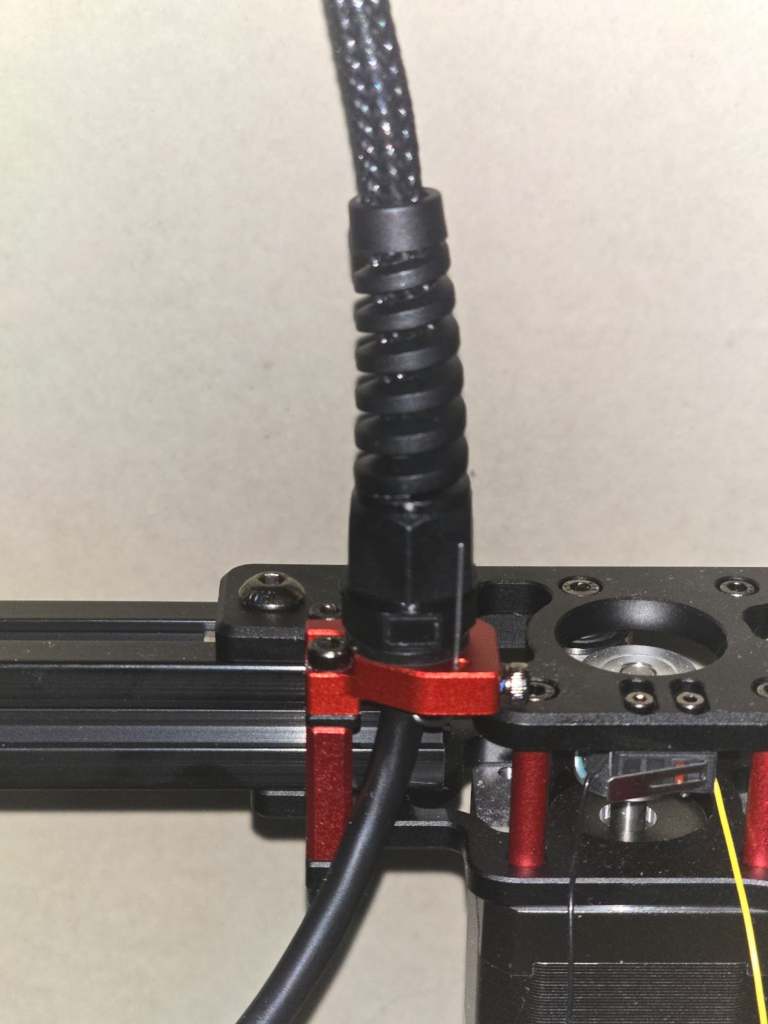
L’électronique et le câblage
Et maintenant, la partie sensible de l’assemblage de la machine, le montage des cartes électroniques et le câblage !
C’est sensible car, comme je le disais dans la première partie, un défaut de câblage peut engendrer des surchauffes, voire même un incendie !
Les rails din vont donc servir à installer tout ça proprement.
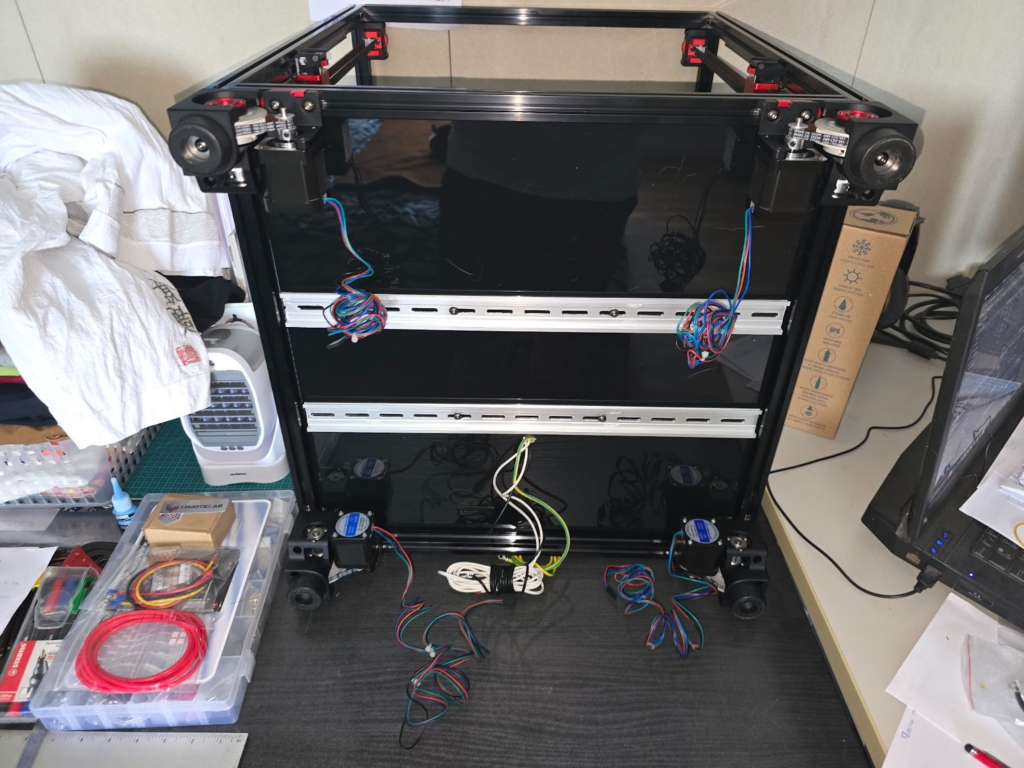
Et voici tout ce qui va aller dedans !
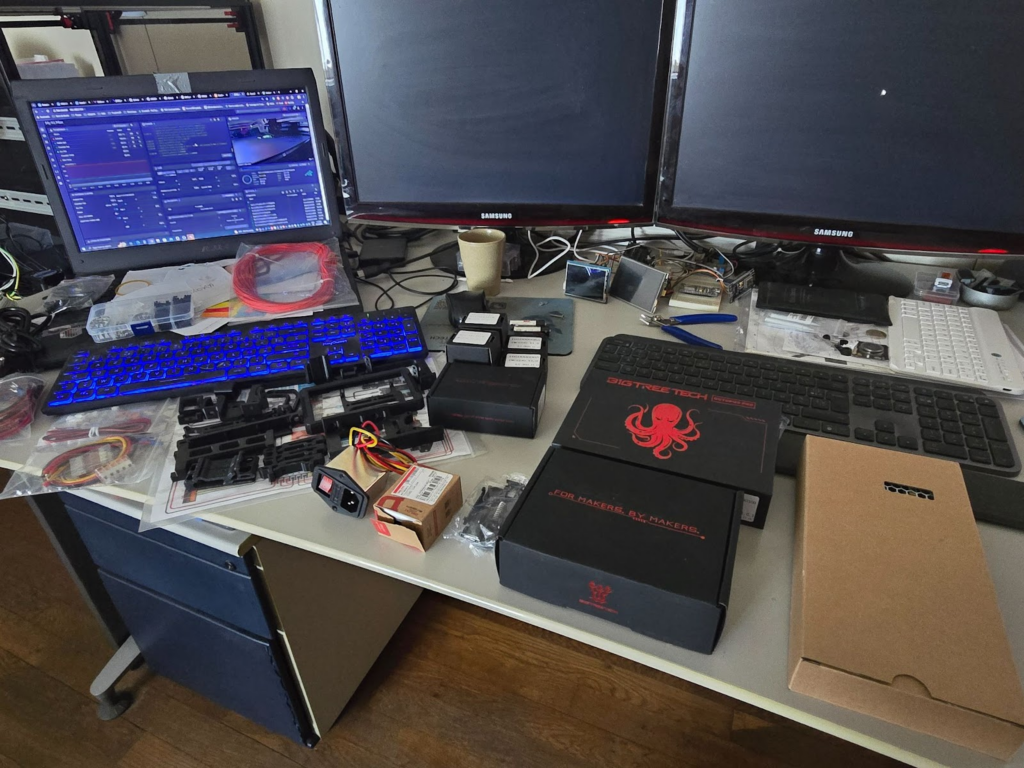
Je commence par l’assemblage de l’écran HDMI tactile de 5 pouces.
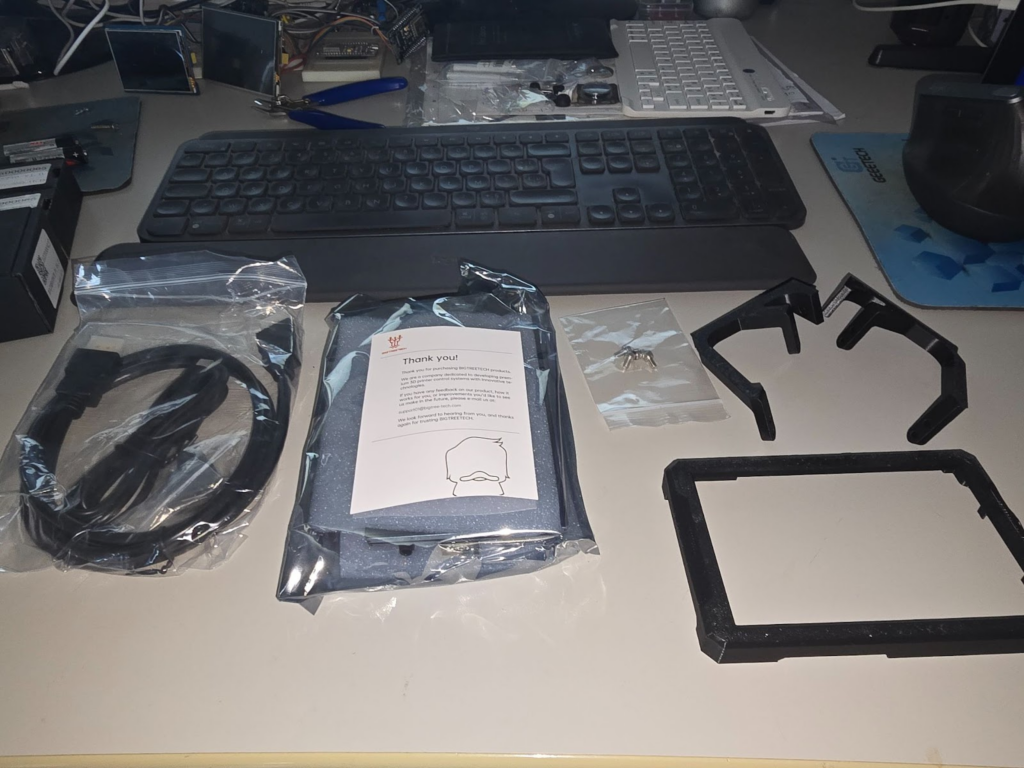
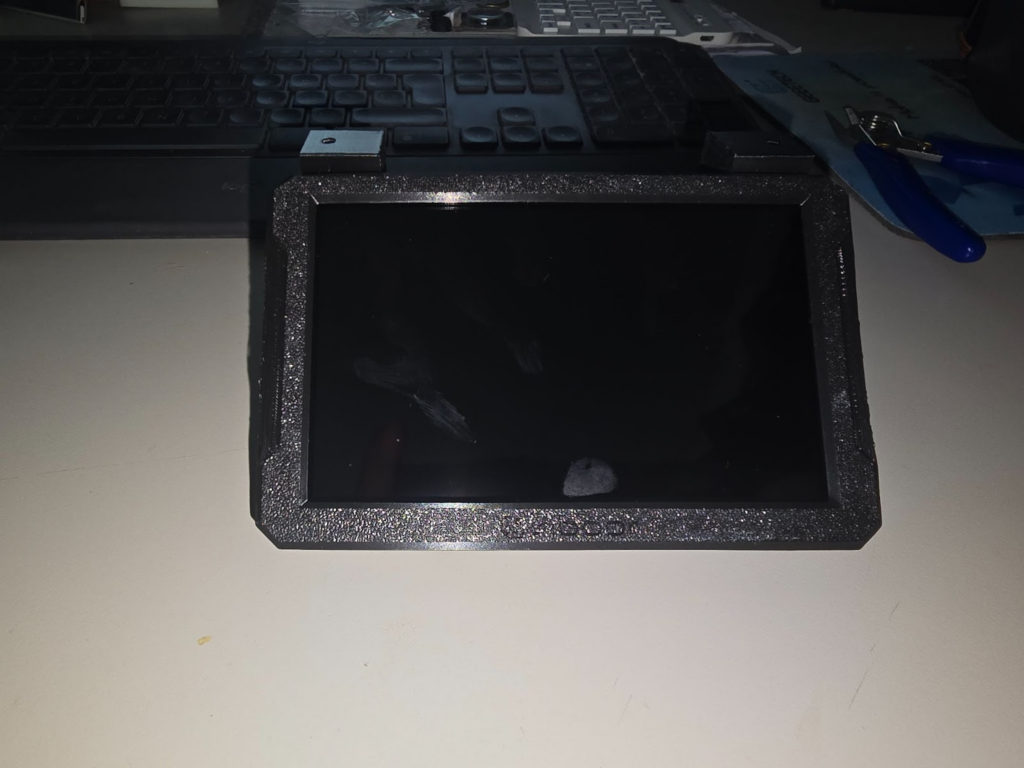
Mise en place de celui-ci sur le châssis.
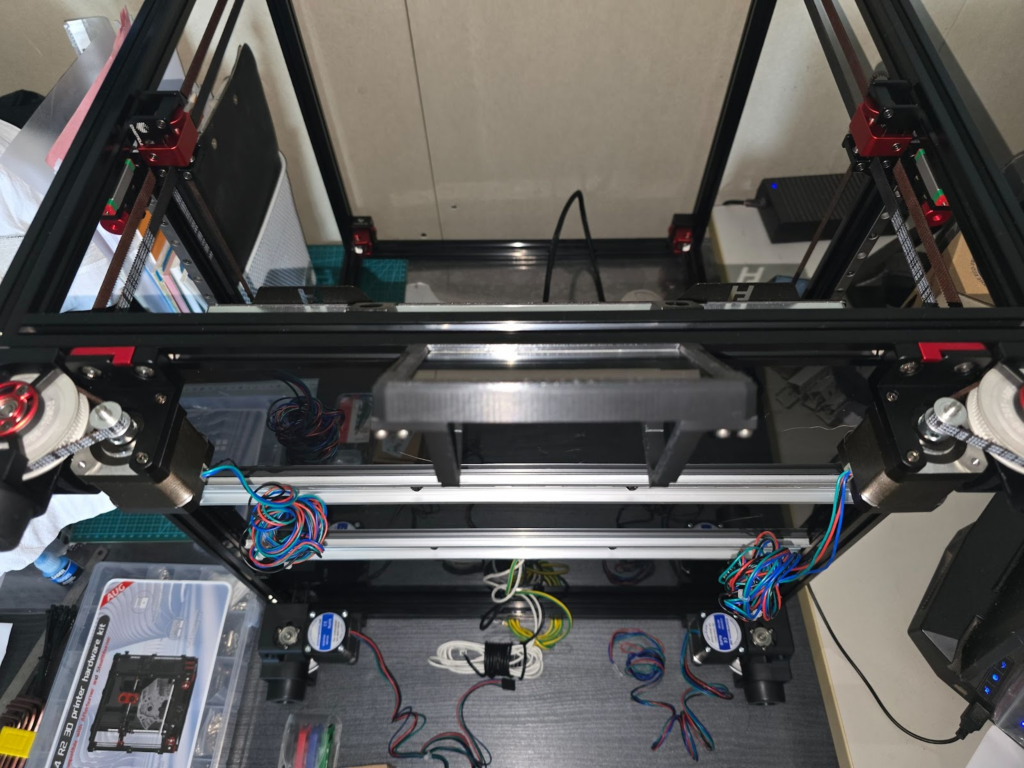
Préparation de la carte mère octopus pro de chez Bigtreetech.
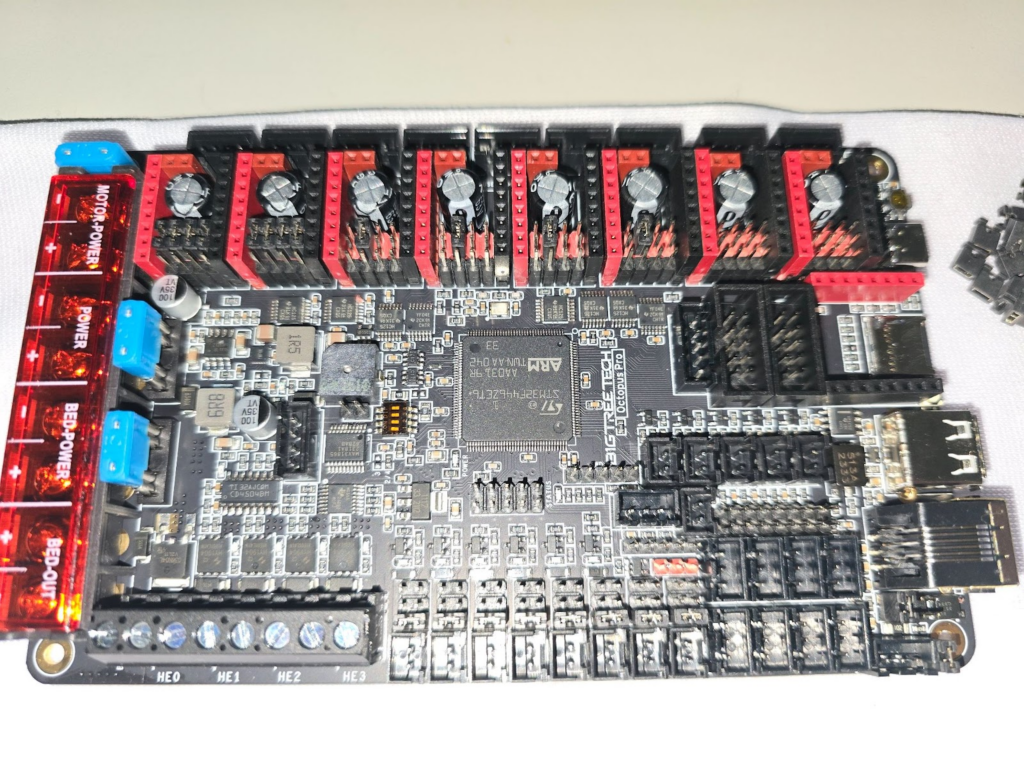
Préparation des connecteurs wago pour l’alimentation en 230V des différents composants.
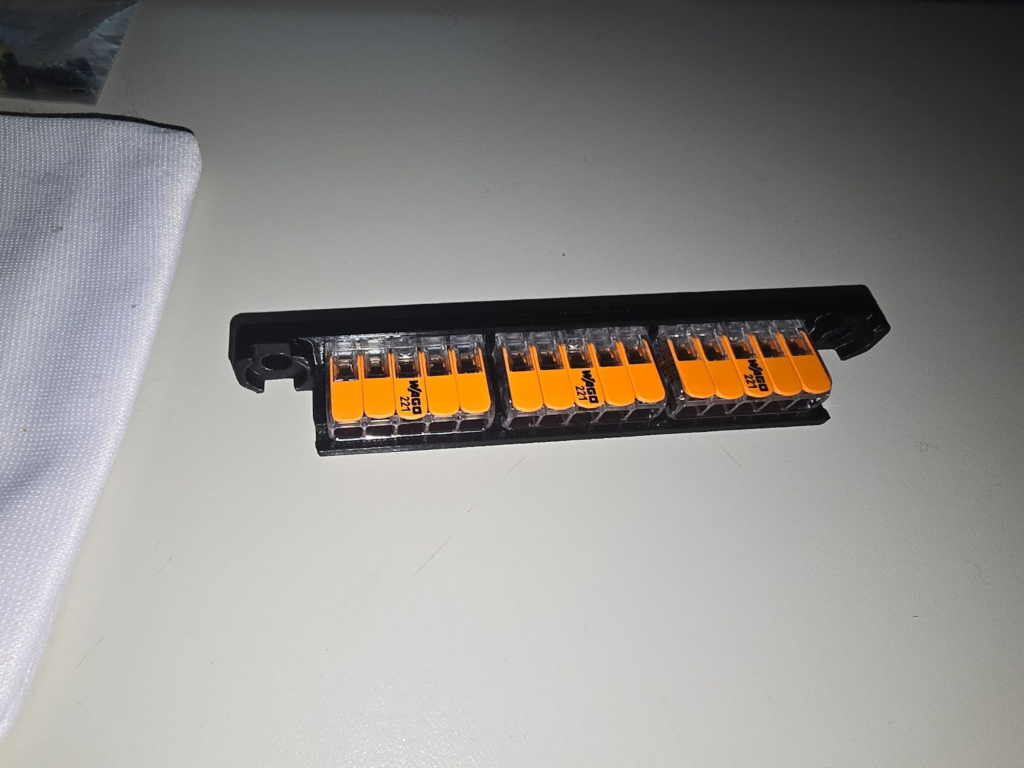
Assemblage du clip din sur le BTT Pi (clone du rasperry pi avec de nombreux avantages en plus)

Idem sur l’alimentation Meanwell
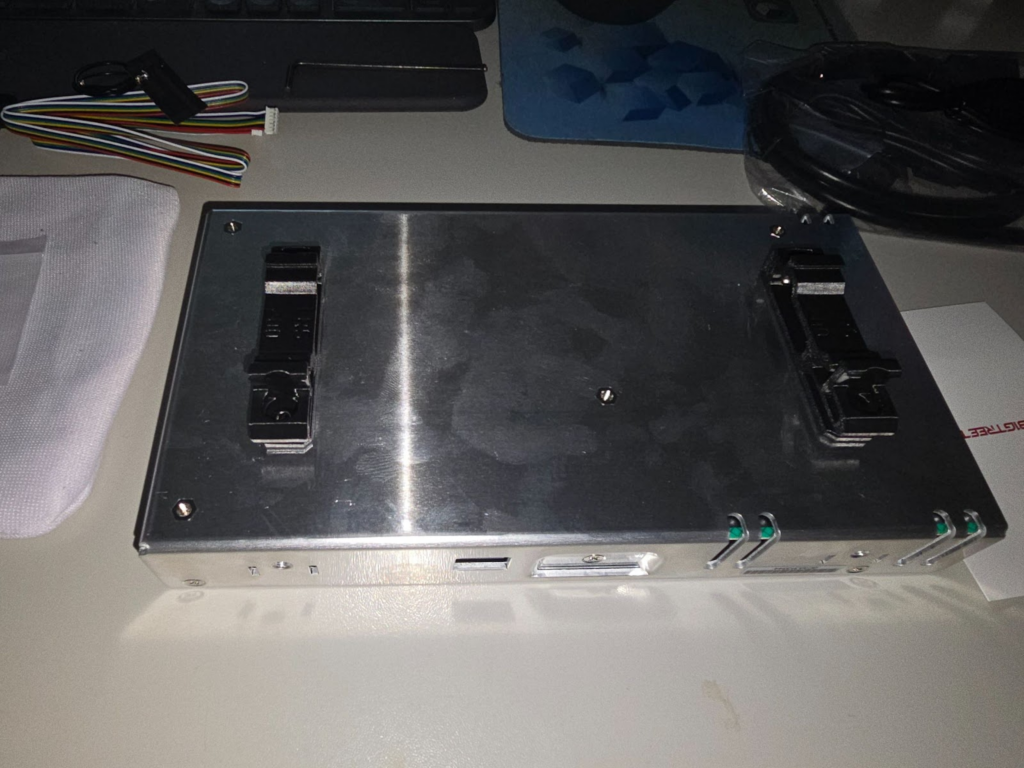
Pareil sur la carte mère.
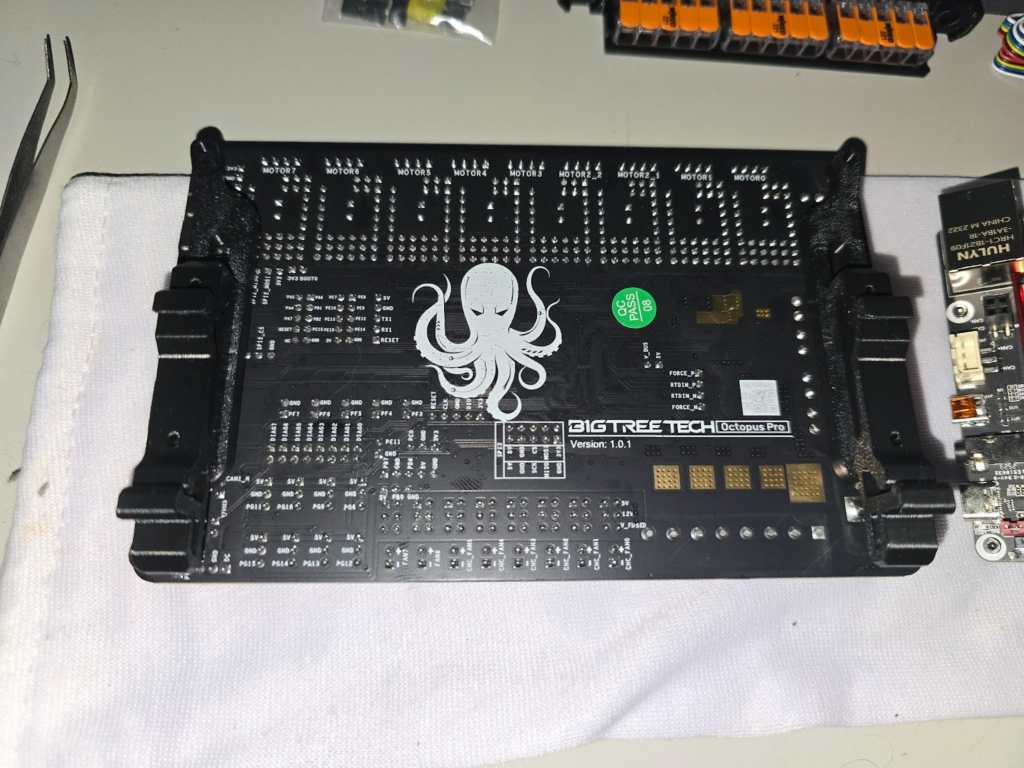
Et pour le SSR, par contre ce n’est pas en plastique mais un vrai connecteur din en métal (Certainement à cause de la chaleur dégagée par le module).
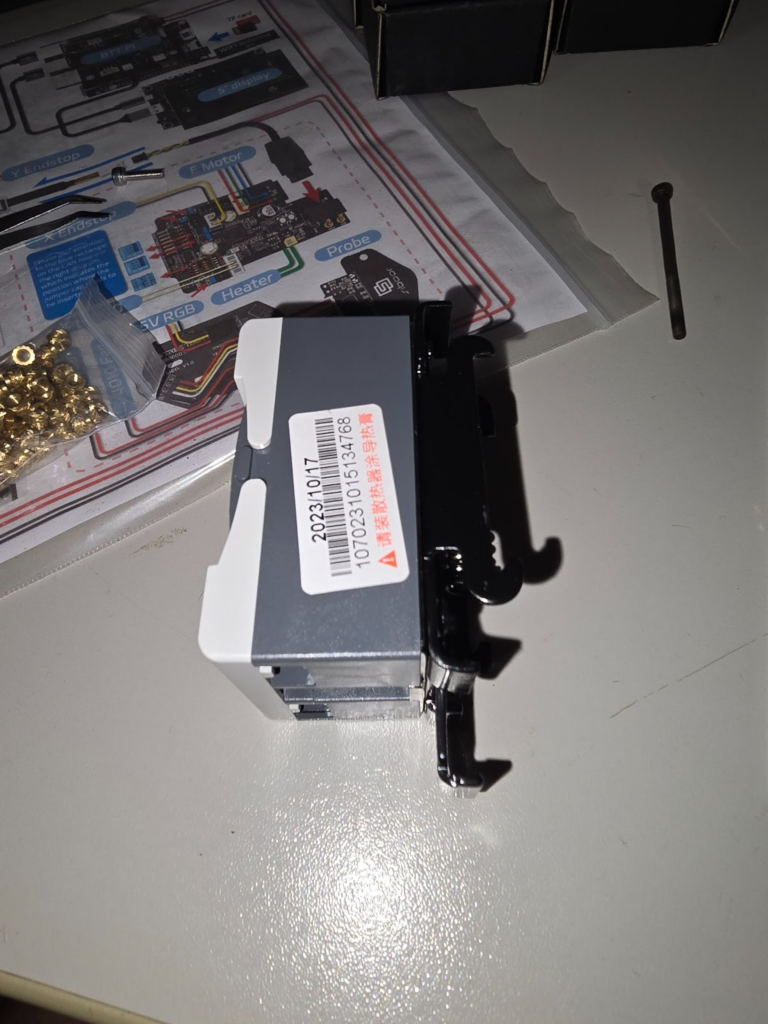
Assemblage du connecteur/bouton d’alimentation
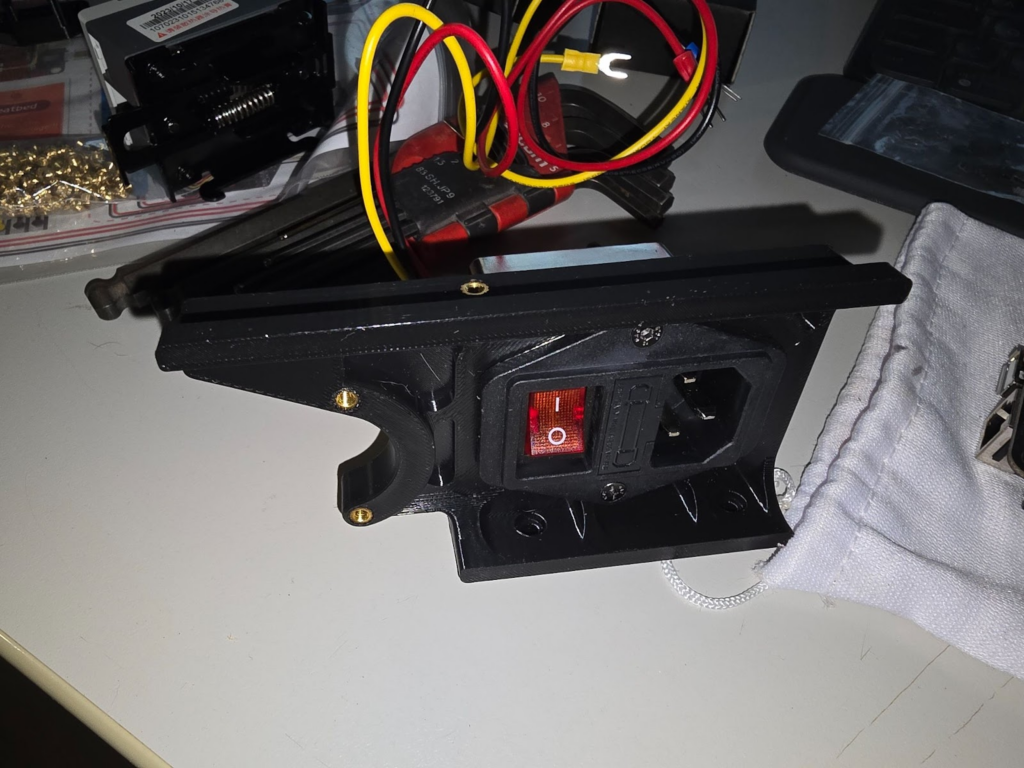
Et installation de l’ensemble sur le châssis.
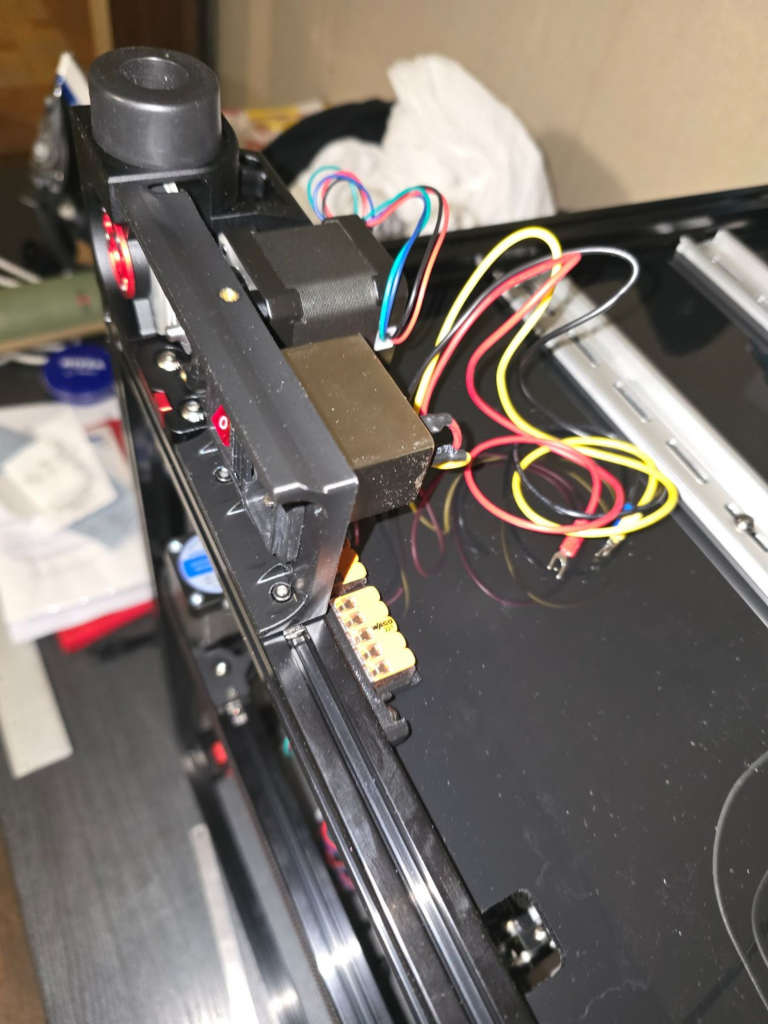
Mise en place des différents composants sur les rails din.
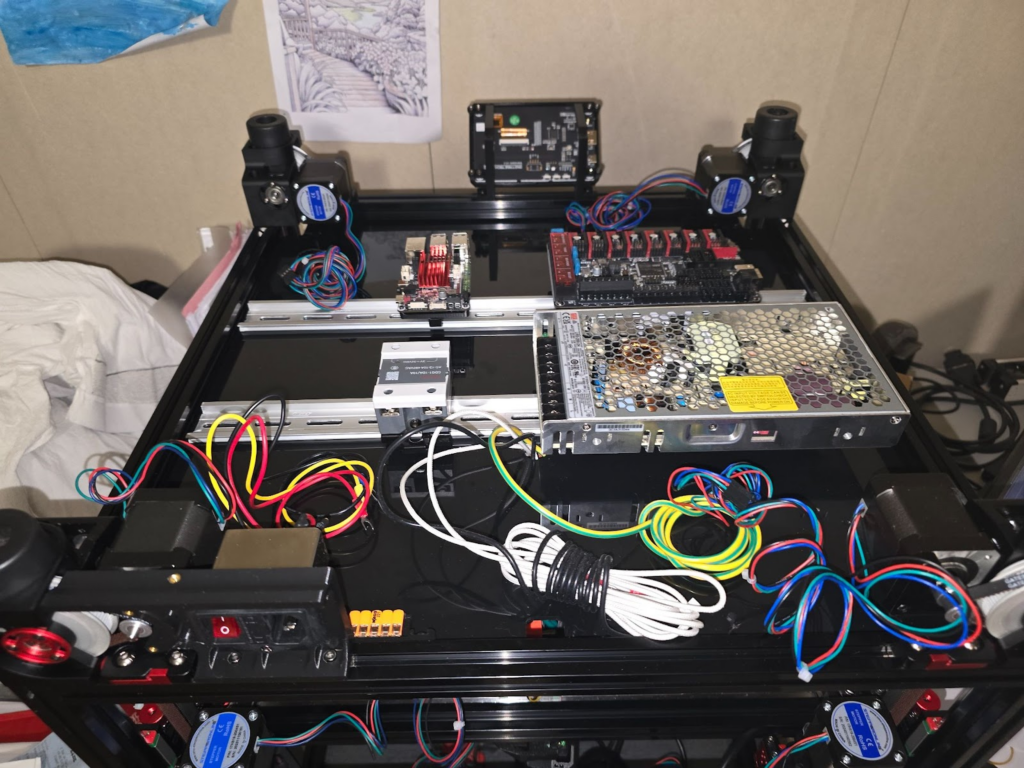
Pour la suite, ne cherchez pas dans la documentation, il n’y a absolument rien !
J’ai dû donc faire quelques recherches sur le net pour comprendre que l’agencement du câblage est laissé libre au monteur. Par déduction, j’ai aussi compris que le double face 3M fourni sert naturellement à coller les goulottes sur la plaque de polycarbonate.
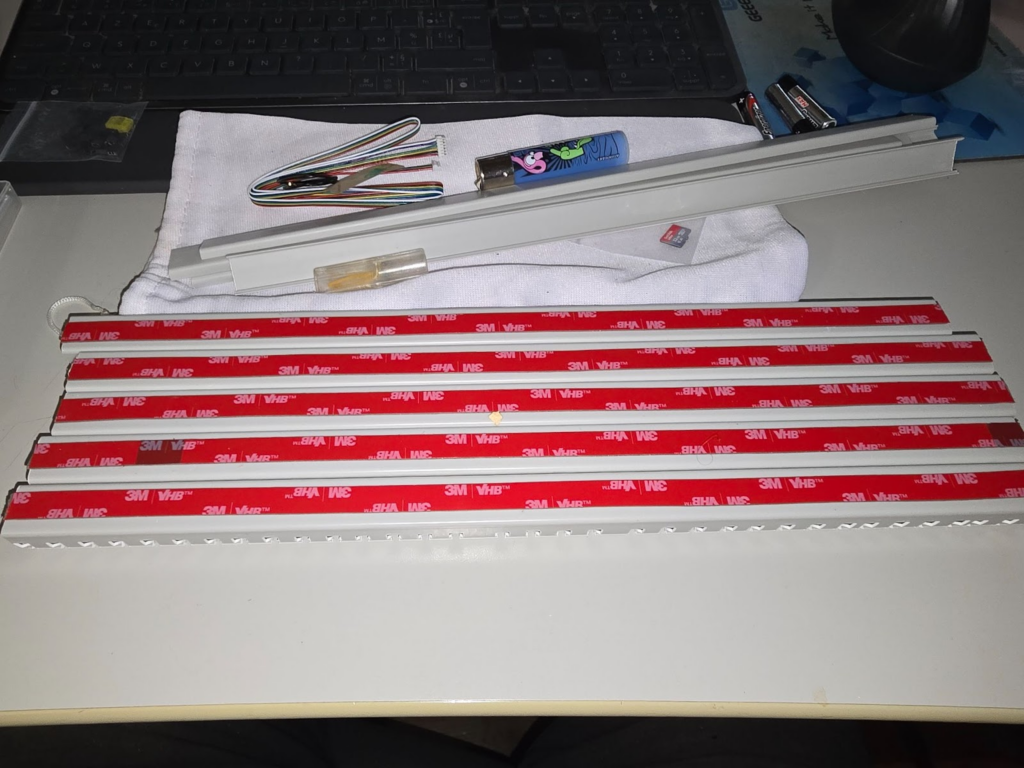
Mise en place des premières goulottes.
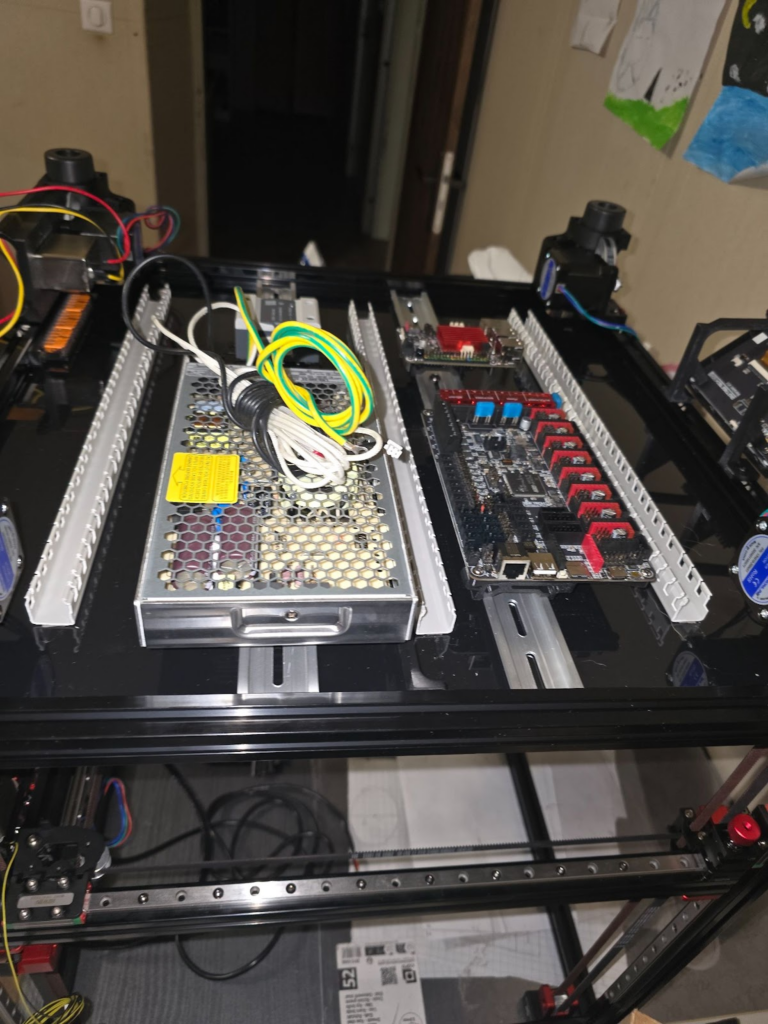
Et du reste :
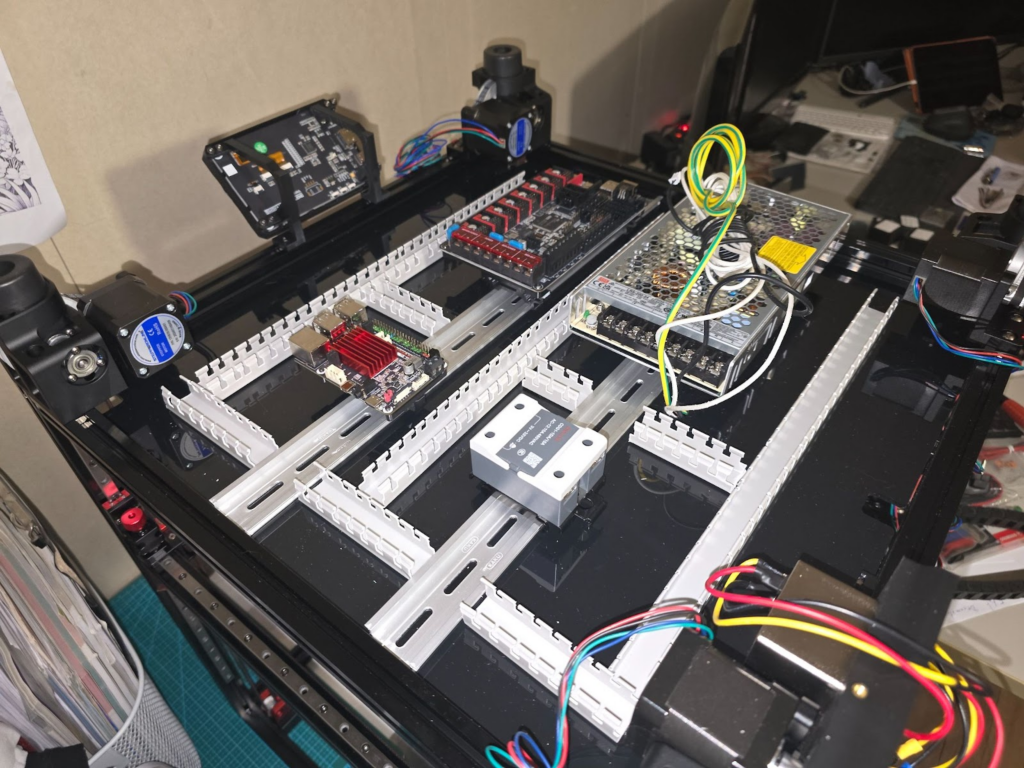
Préparation des drivers moteurs.
On remarque la différence entre les TMC2240 et les TMC2209:
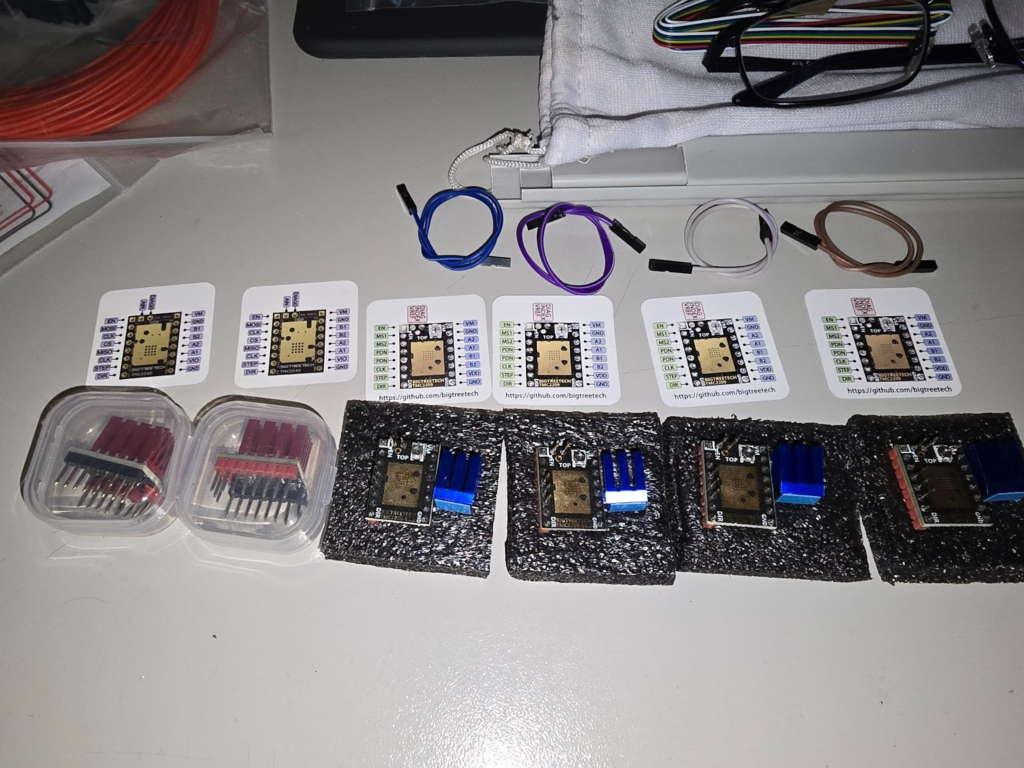
Installation de ceux-ci sur la carte mère :
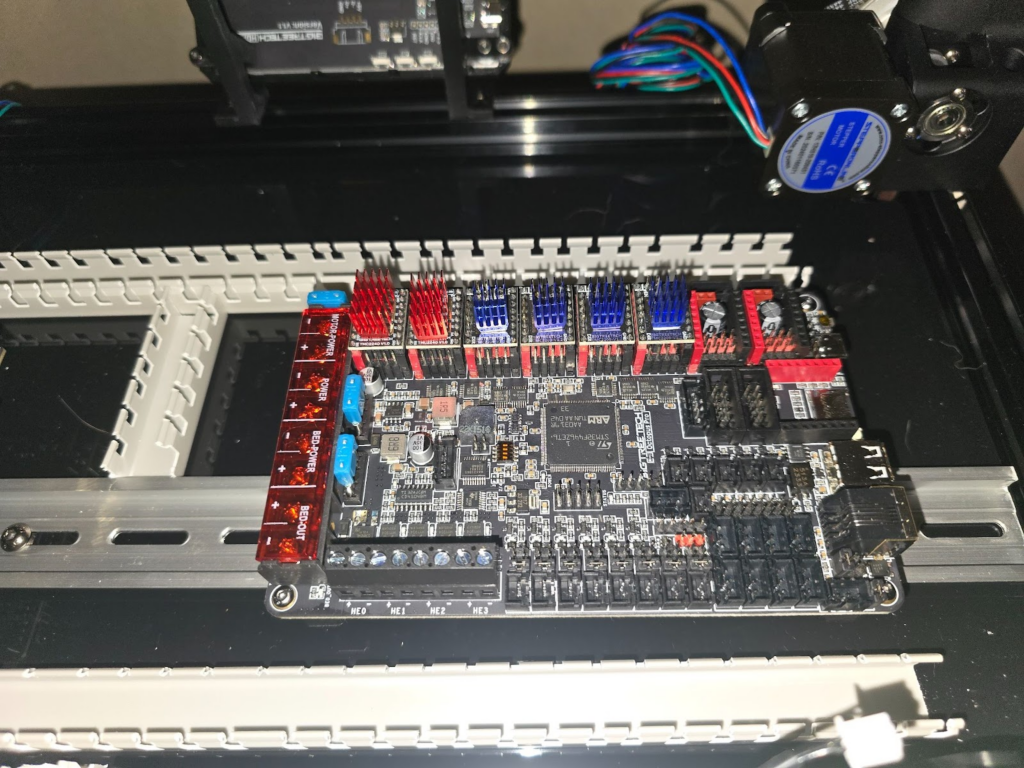
Maintenant, je passe au câblage et premier hic: les câbles pour l’alimentation en 230V sont sertis avec des cosses fourches, hors ils vont dans les connecteurs wago ….
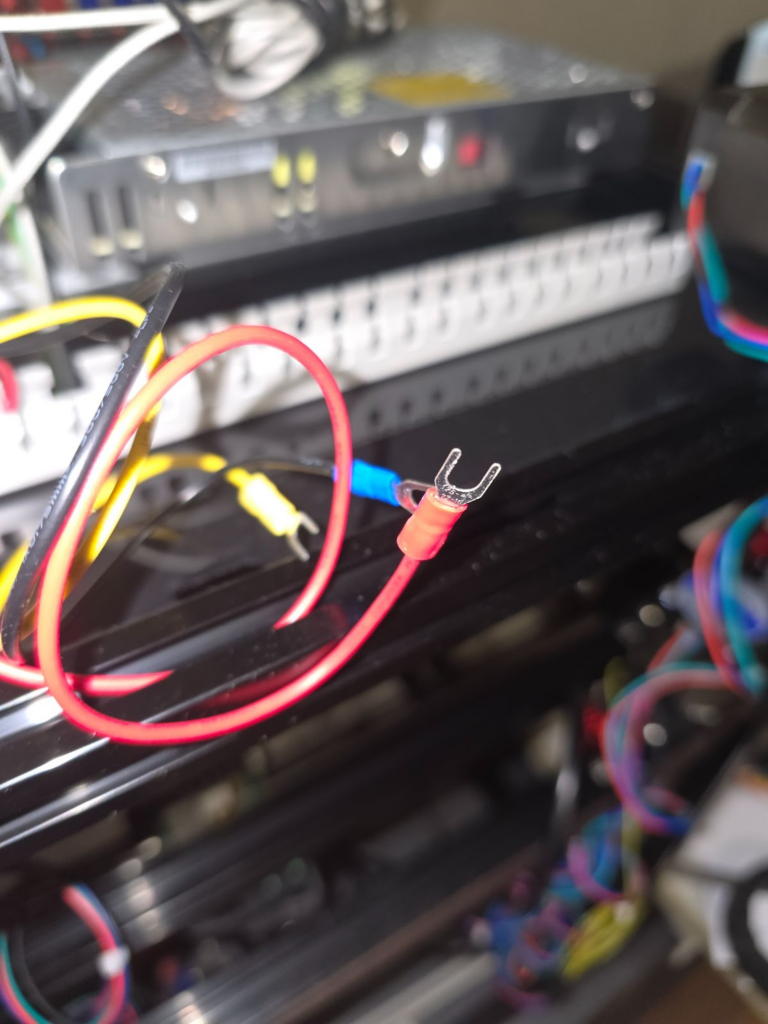
Donc souvenez vous, à la fin de la première partie, je recommandais l’achat de pinces à sertir avec des cosses, et bien voilà pourquoi !
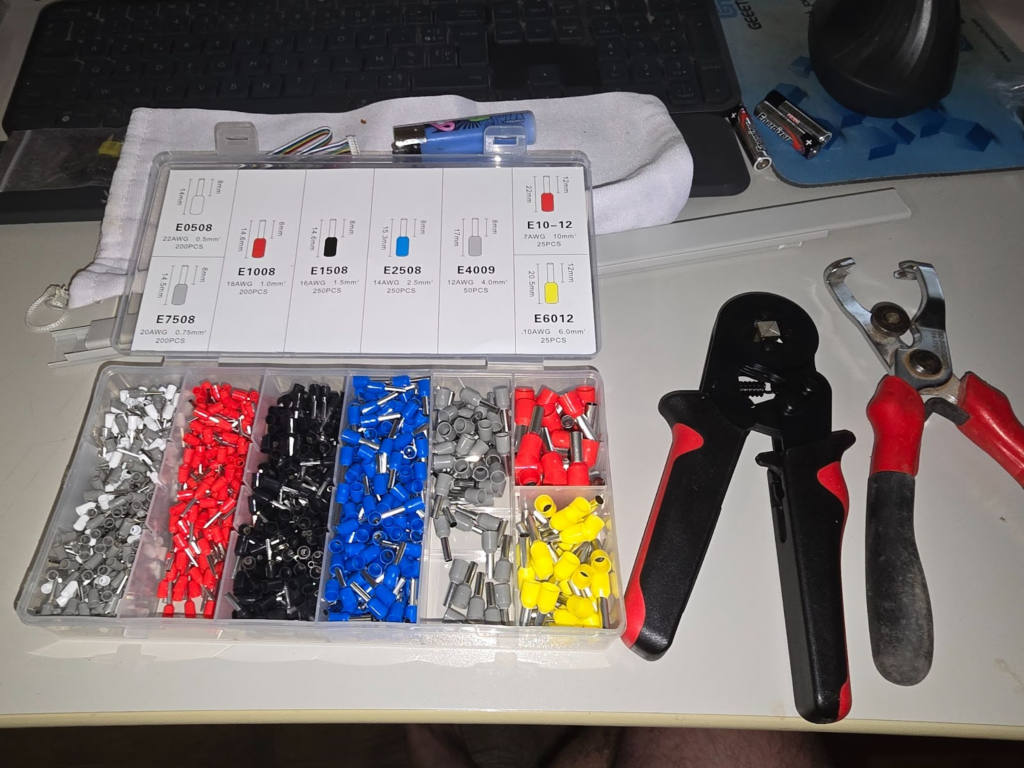
Donc, coupe des cosses fourches et mise en place de cosses terminales.
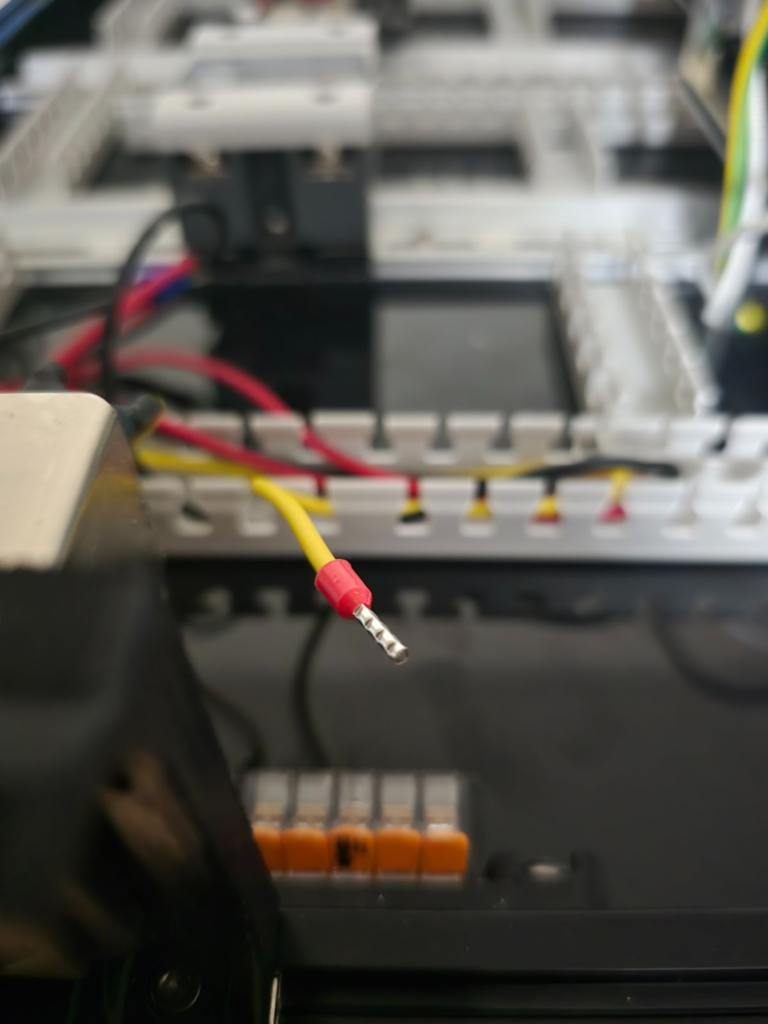
Puis installation dans les Wago et début du câblage.
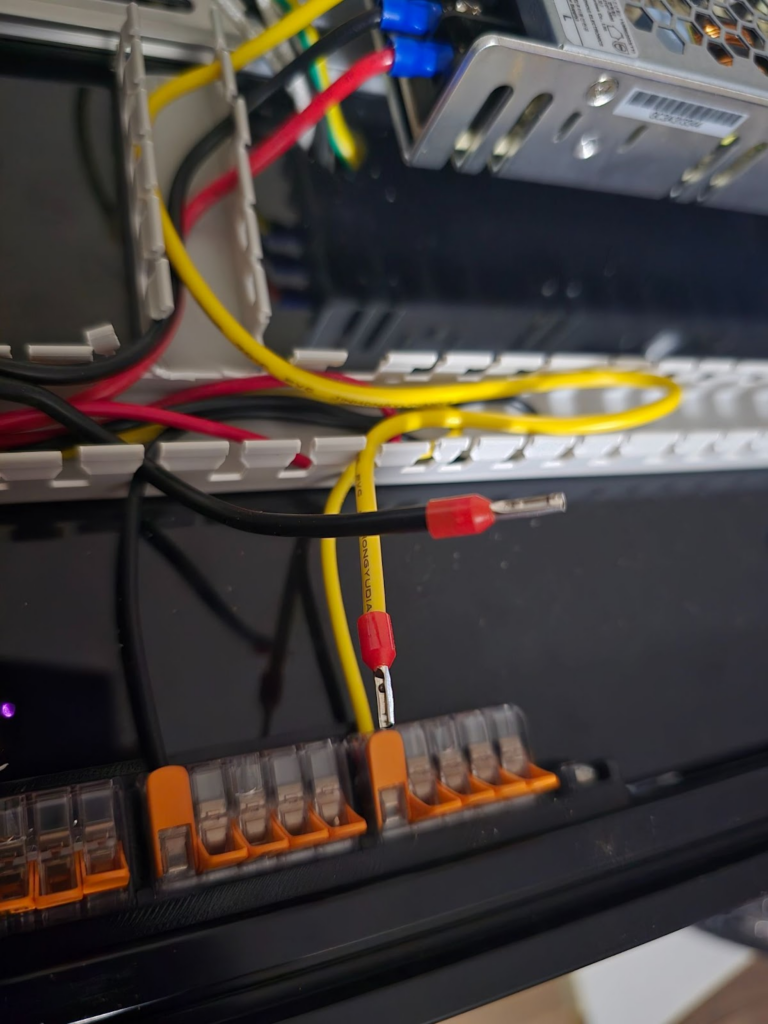
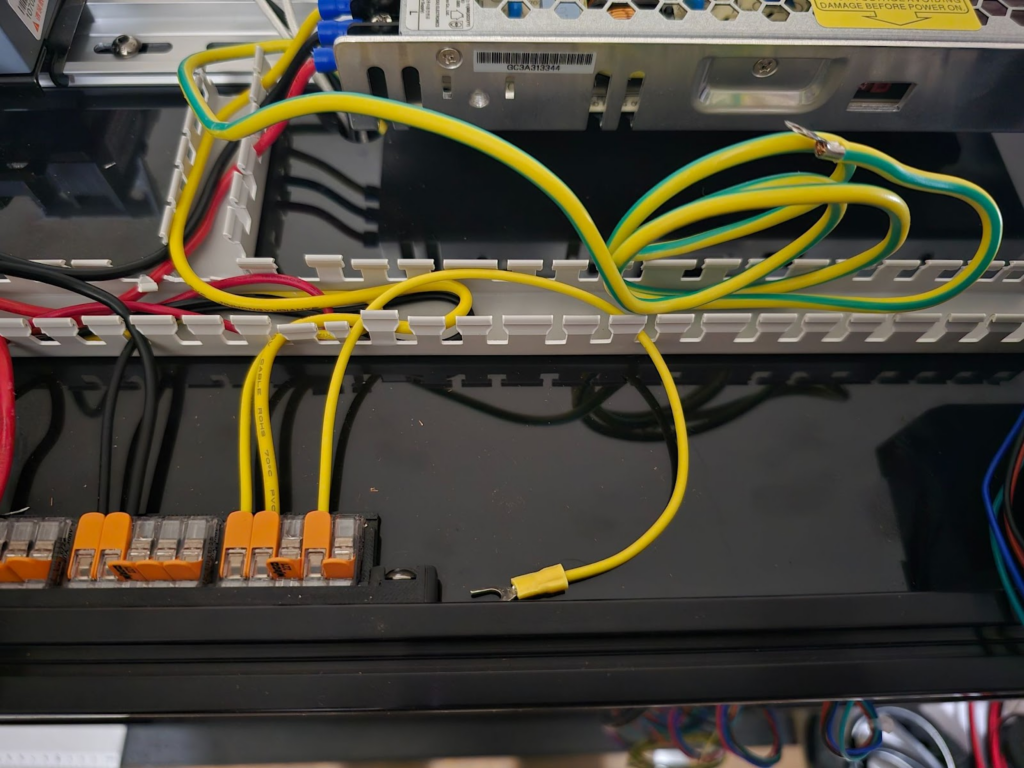
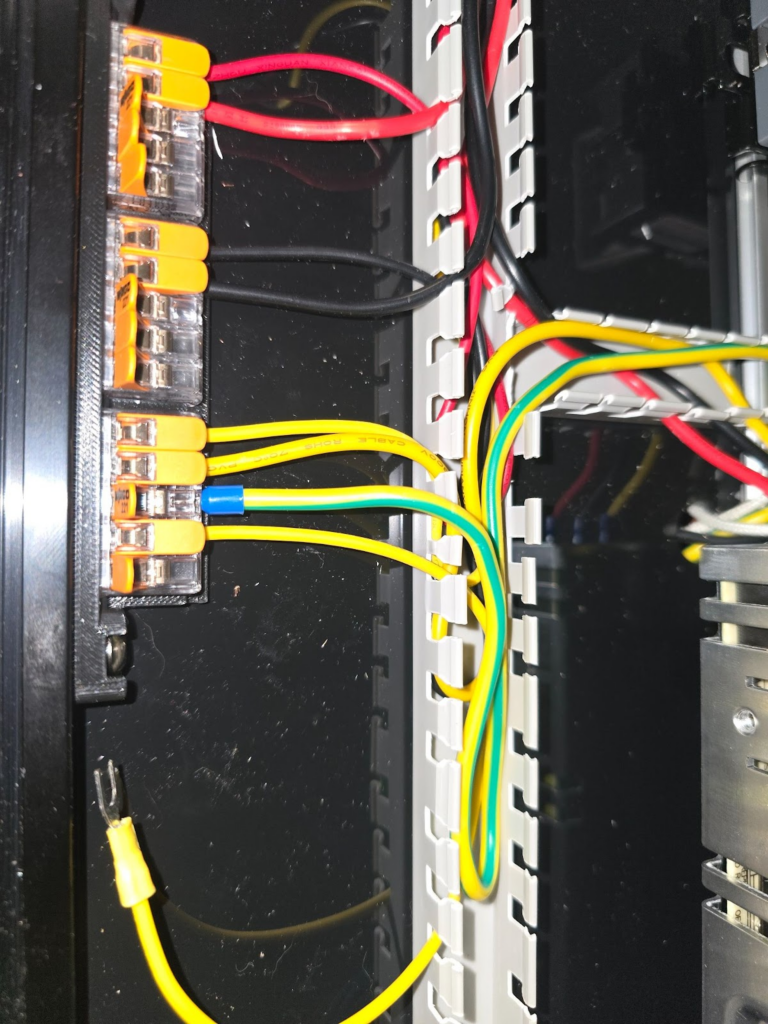
En ce qui concerne les moteurs, j’ai décidé de passer les 4 fils dans des gaines tressées de 6mm (je suis un maker prévoyant, et j’ai du stock de tout,pour tout ! 😛).
Pour deux raisons, c’est plus propre et c’est plus facile à manipuler.
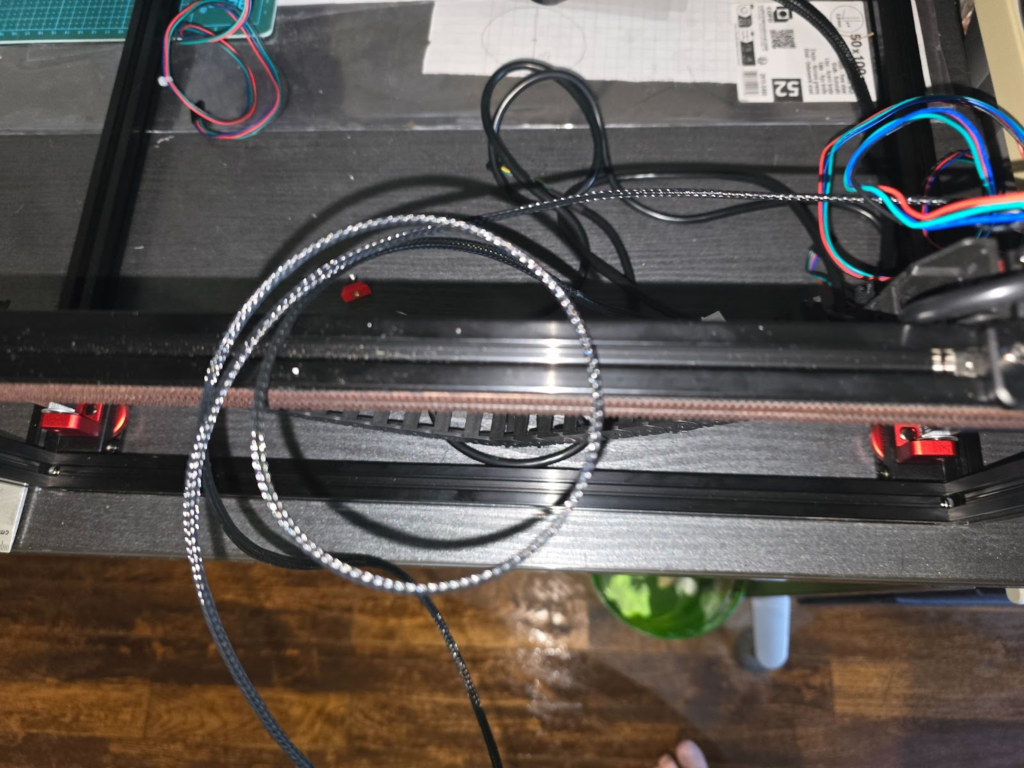
Et pour le moteur A (ou B … ) je passe la gaine dans le profilé alu et sécurise celui-ci.
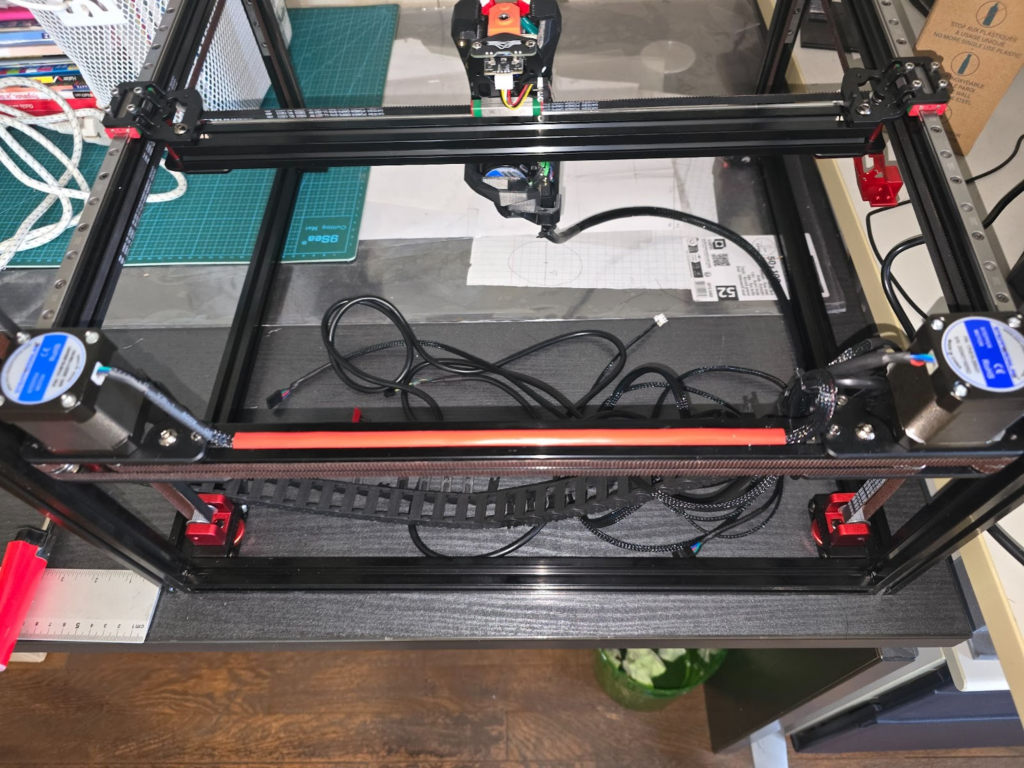
Et bien sûr, deuxième hic ! Le câble du moteur, une fois passé dans la chaîne Z, n’est pas assez long !
Je vais donc devoir faire un prolongateur.
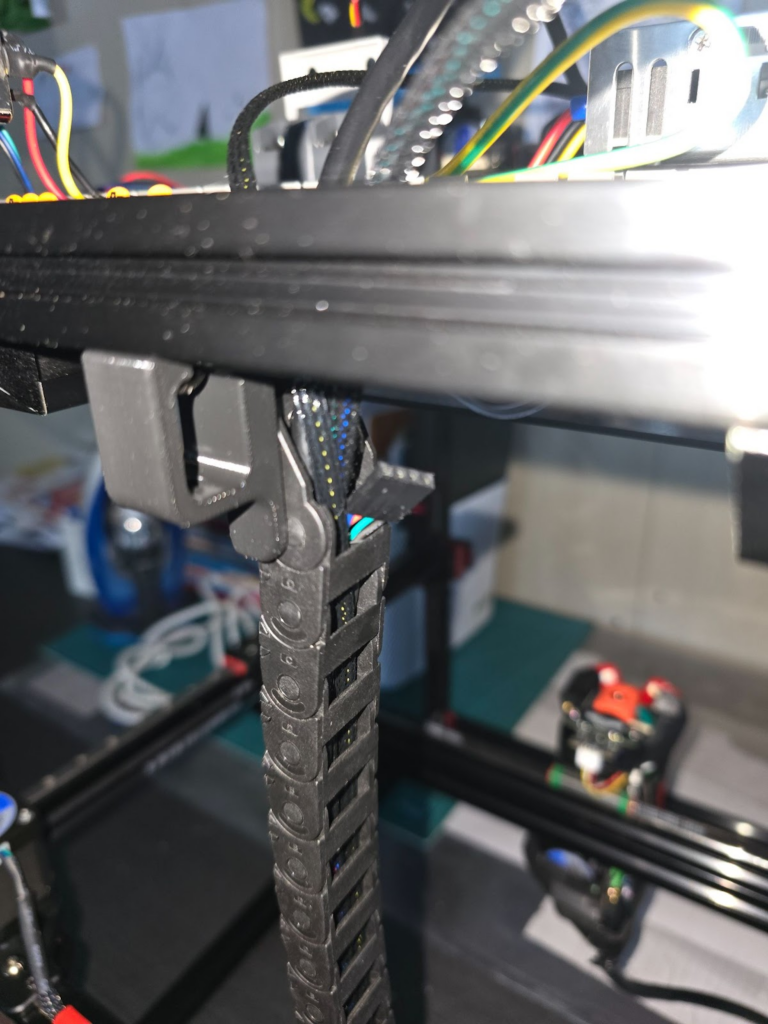
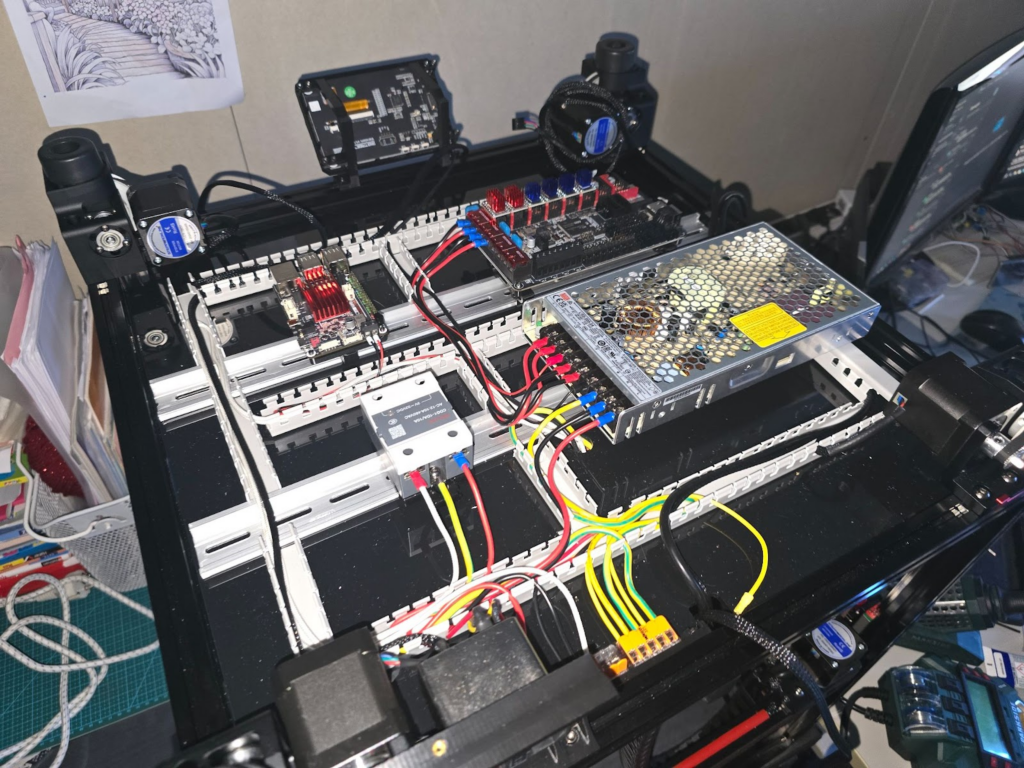
Passé cela, je continue tranquillement le câblage.
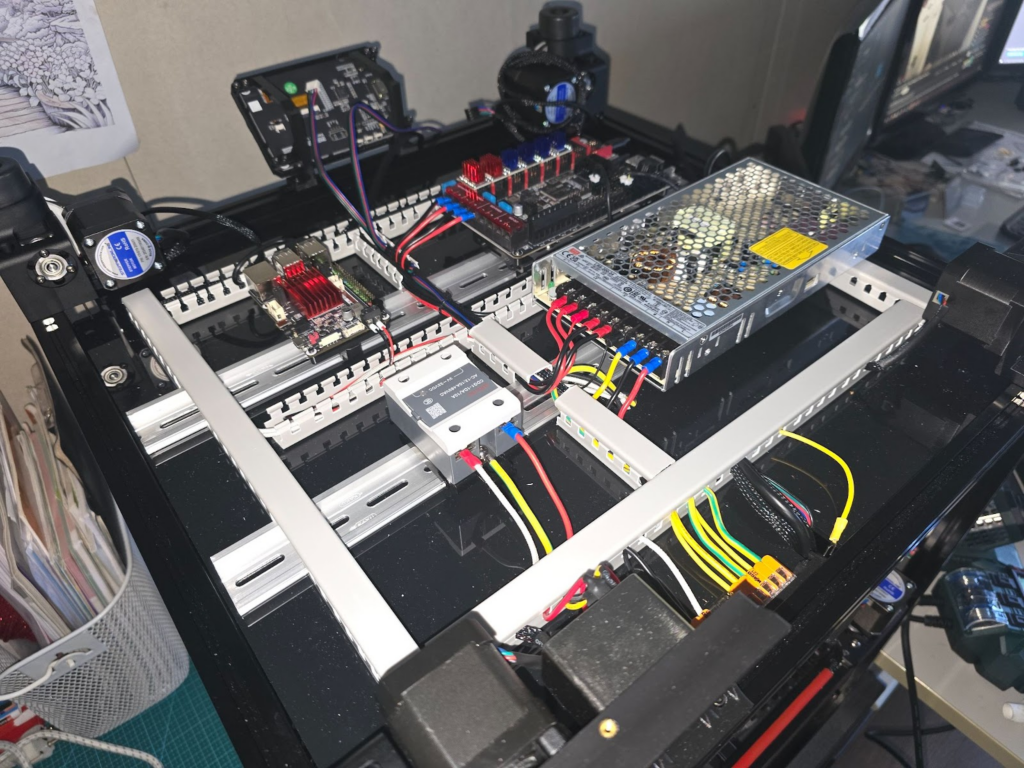
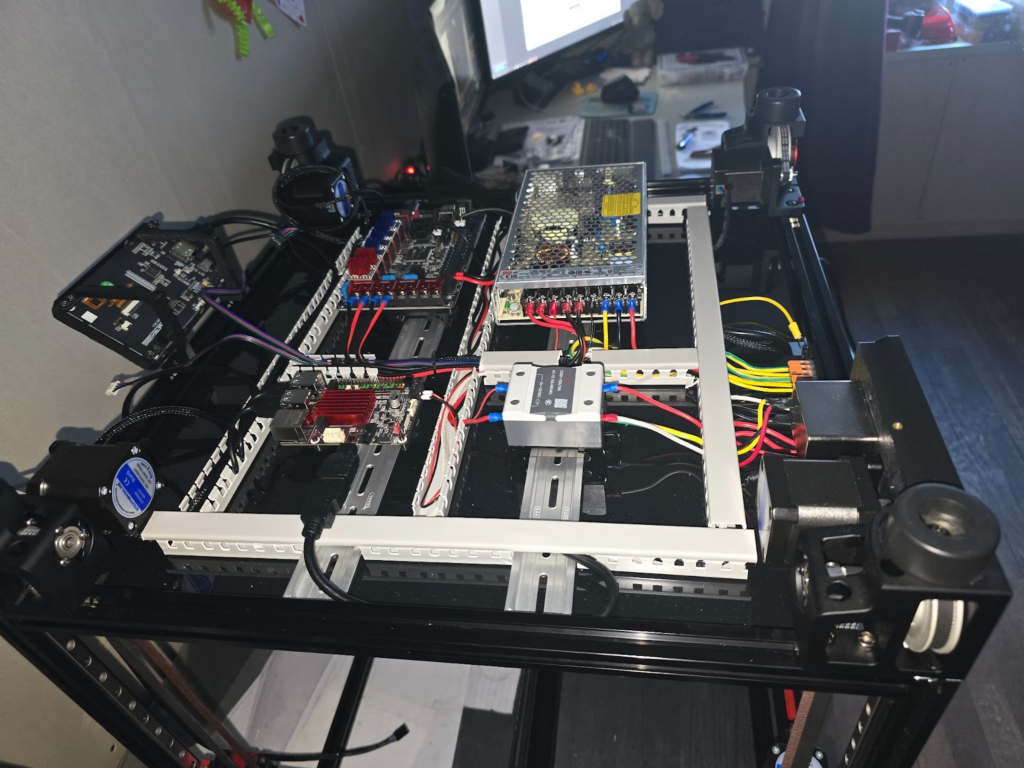
Vers la fin du cablage, je me rends compte que pour toutes les lignes 24V, celles-ci viennent directement du bloc d’alimentation. Hors pour le futur de la machine, je vais avoir besoin de plusieurs lignes 24V et notamment pour les différents bus CAN.
Je décide donc d’imprimer des supports Wago supplémentaires pour le 24V (+ et – ) et pour les bus can ( High et Low).
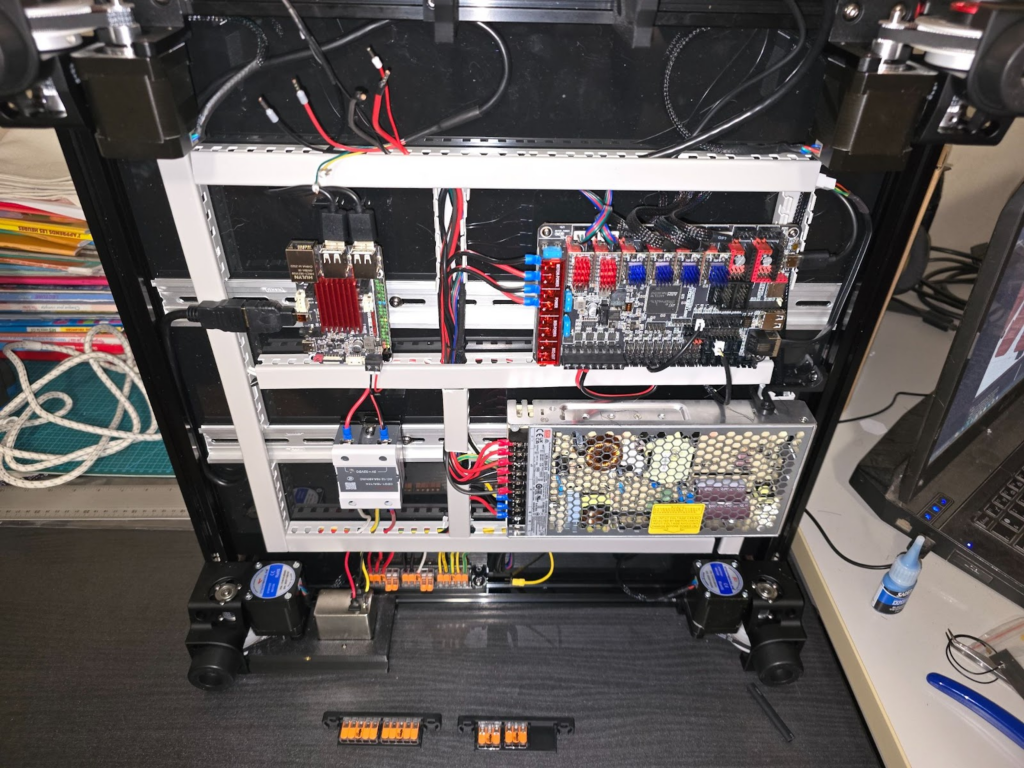
Mise en place du tout !
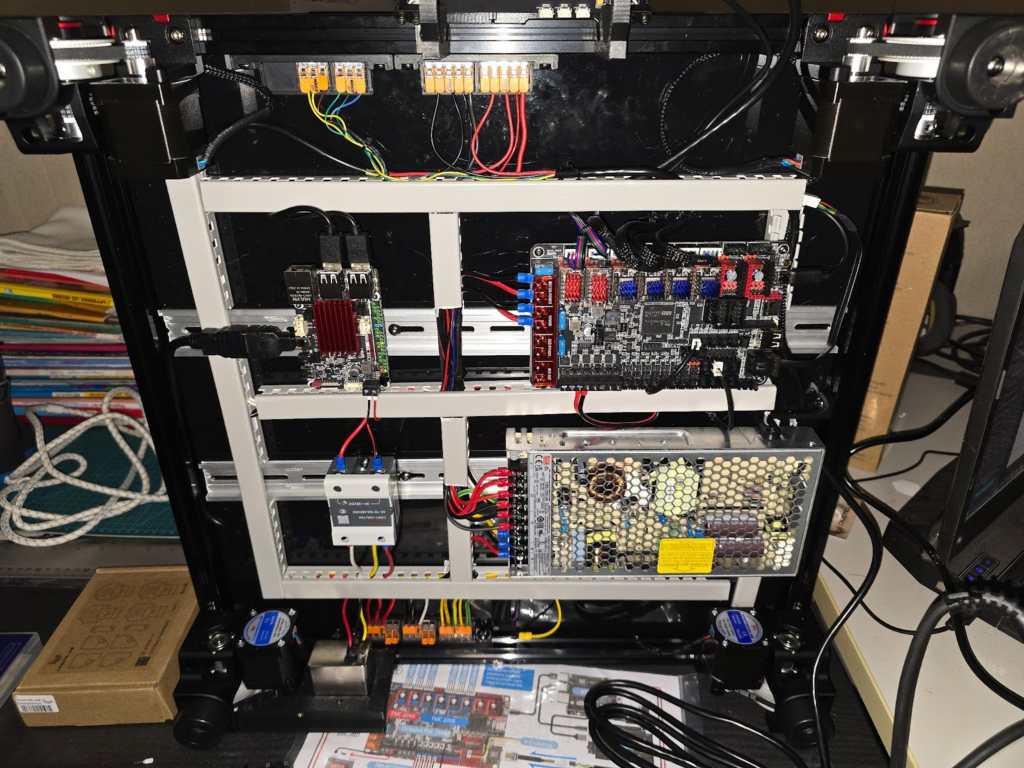
Les deux lignes CAN (pour la tête d’impression et le futur ERCFv2) sont en place et les lignes 24V aussi ( idem pour le CAN ERCFv2 et le futur Bloc de refroidissement CPAP)
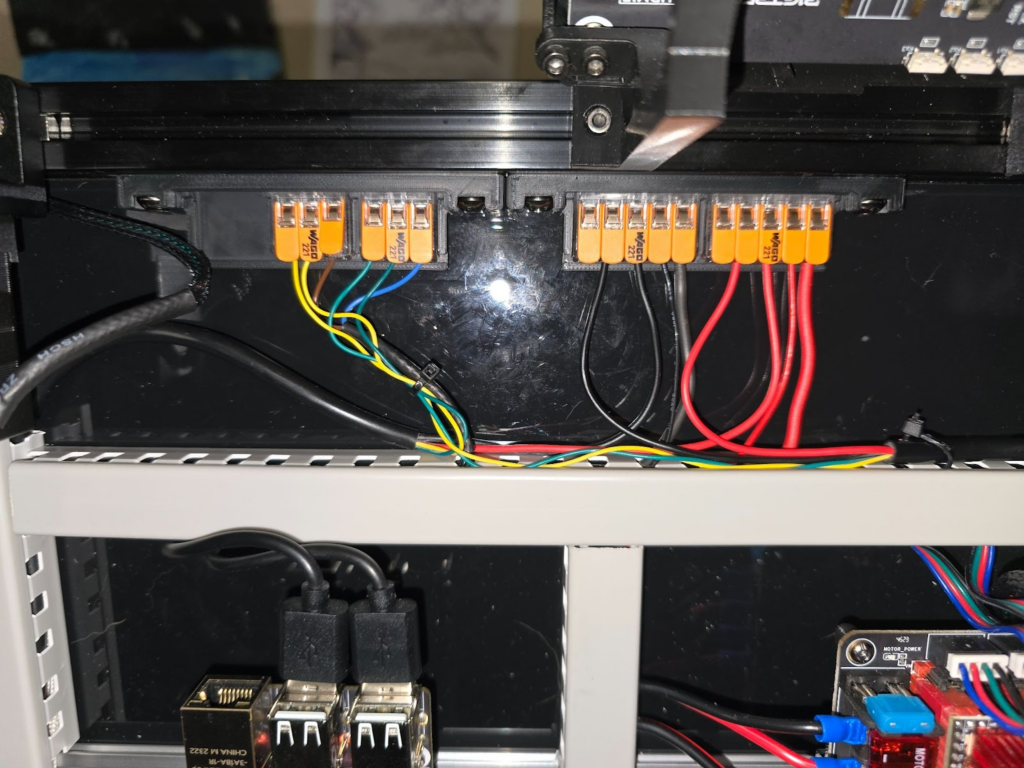
Voici le cable CAN qui ira au futur ERCF v2:
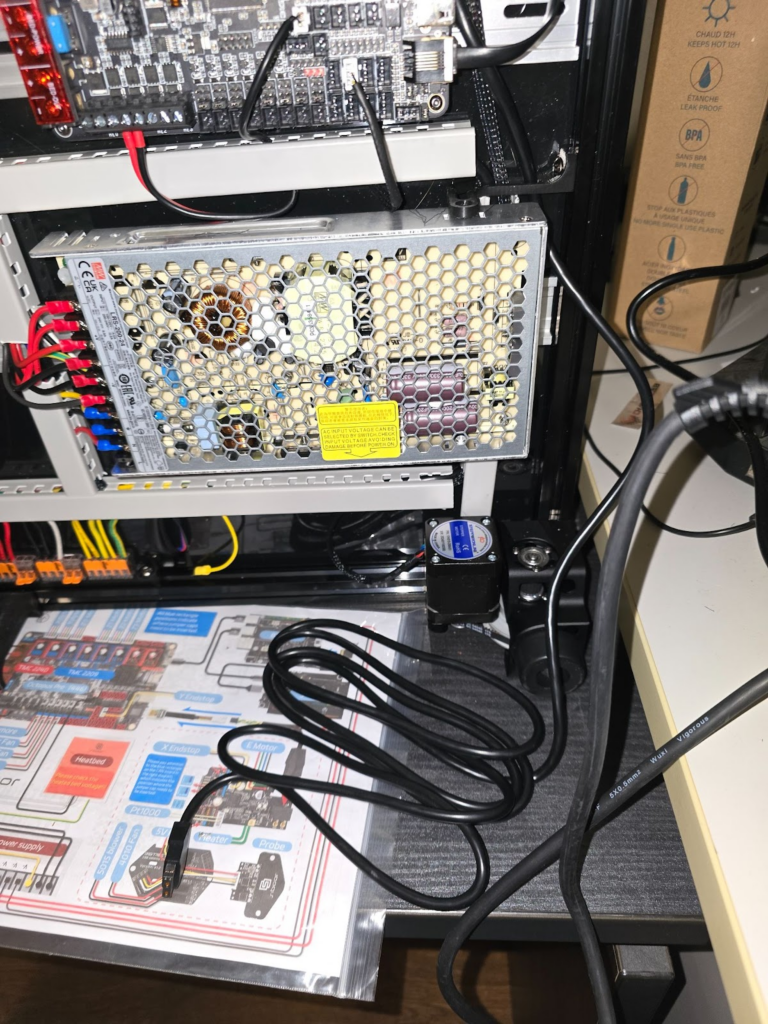
Encore une grosse partie de finie !
J’en suis à environ 24h de temps cumulé.
D’ailleurs le plus gros du montage est fini et la suite est bien plus simple.
Les parties décoratives et les ventilateurs
Cette partie est relativement simple.
La préparation des éléments imprimés consiste simplement à mettre des inserts laiton et à assembler le tout. Les ventilateurs de la partie électronique sont montés dans cette étape-ci aussi.
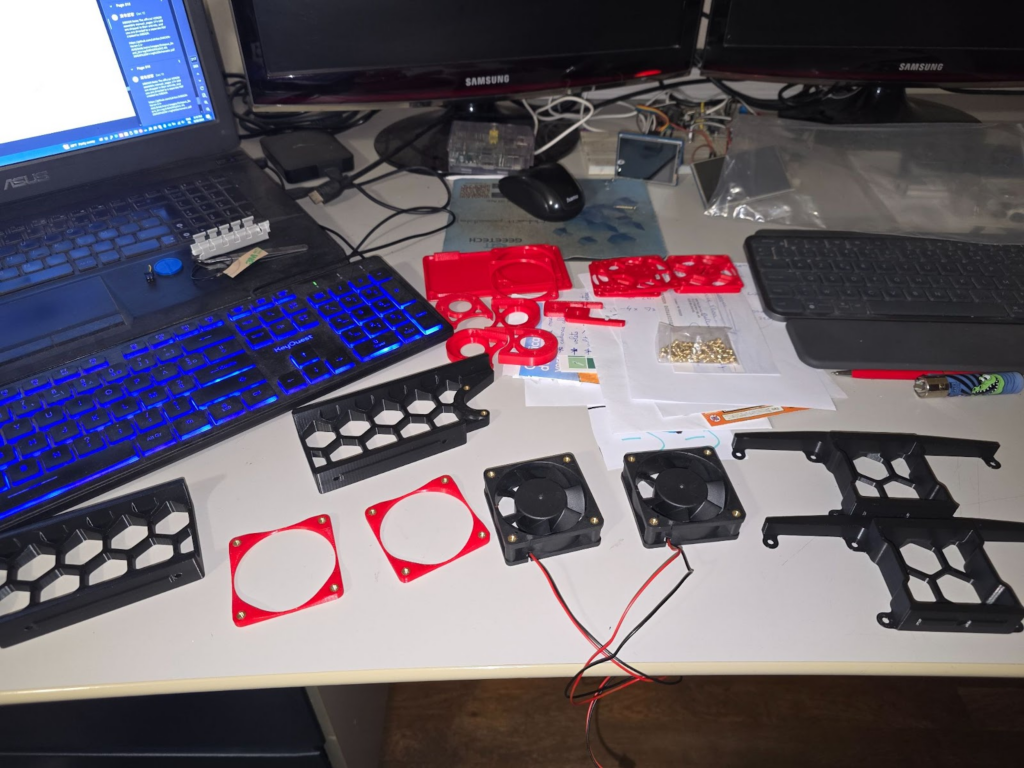
Montage des éléments frontaux :
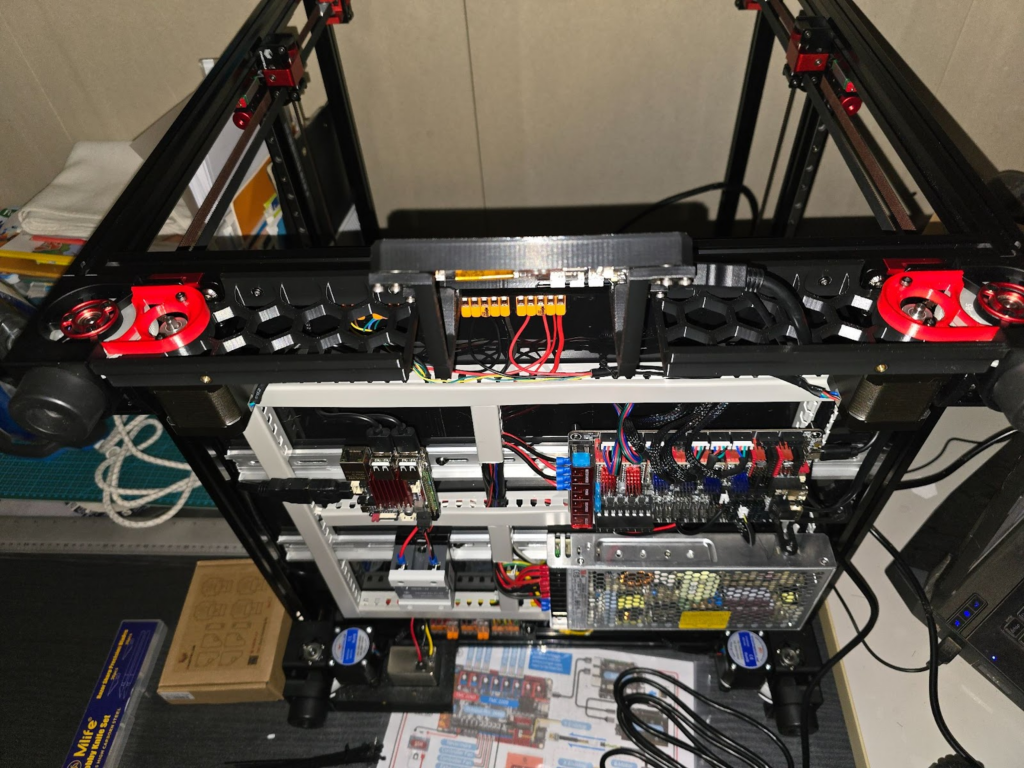
Puis la partie arrière :
On remarquera à droite qu’un des éléments est prévu pour des extensions (usb, report connecteur LAN, etc). Moi, j’ai décidé de m’en servir pour passer les câbles des futures extensions.
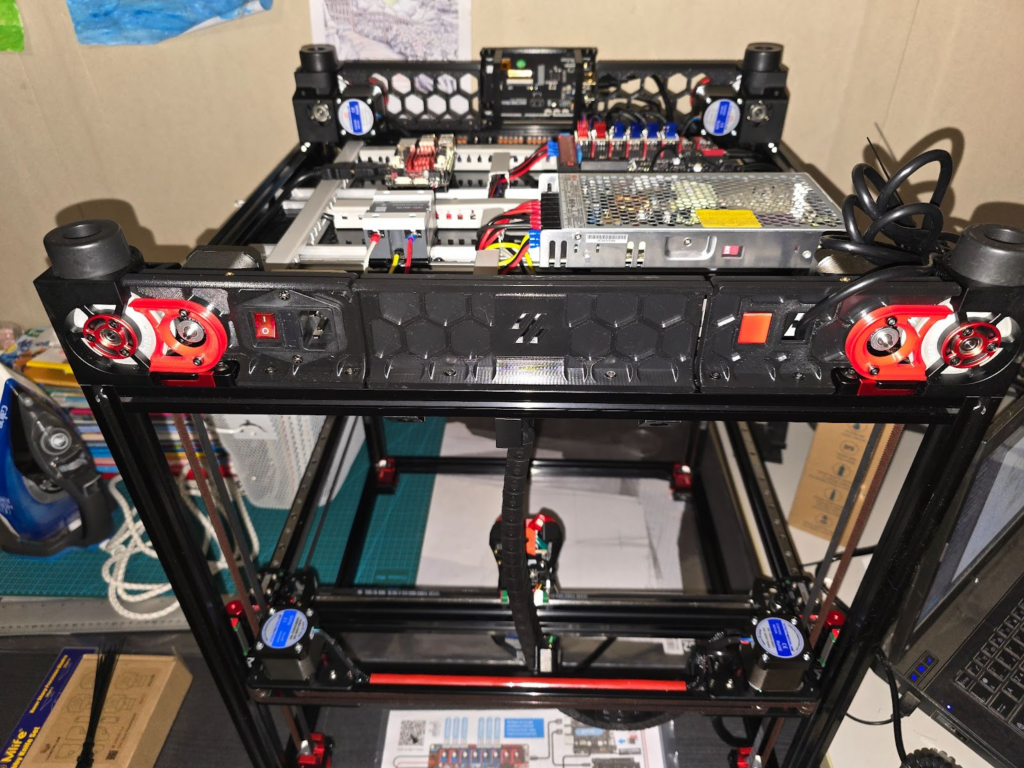
Première partie latérale sans les ventilateurs :
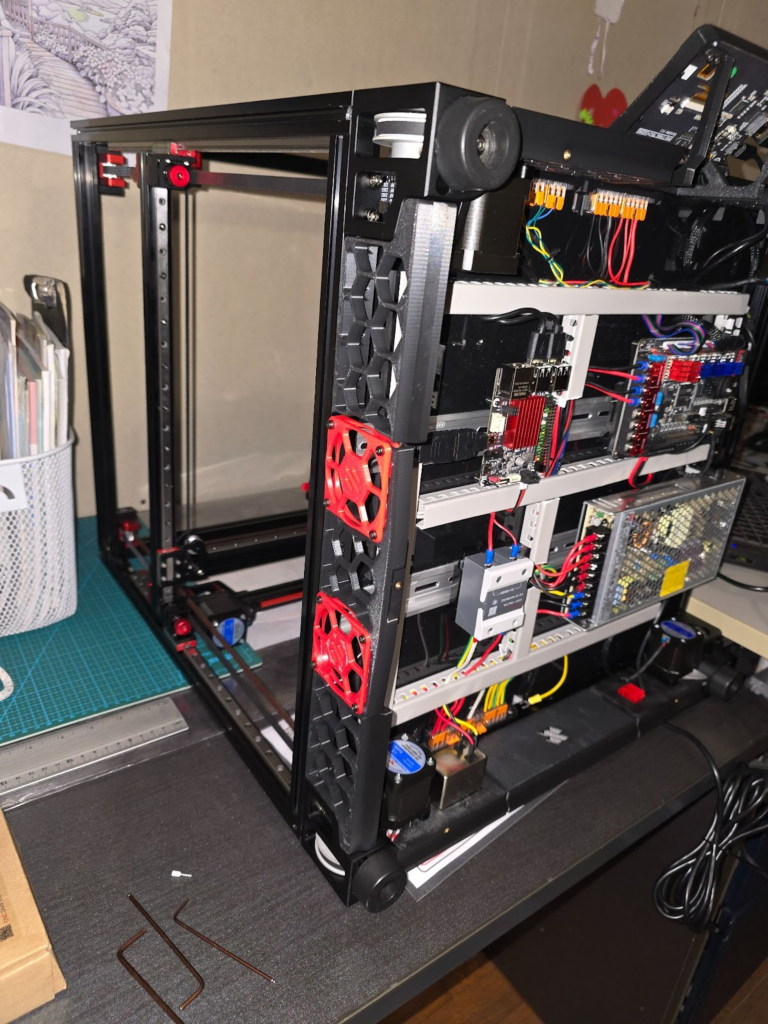
Et la deuxième avec les ventilateurs.
Voilà, c’est fini !
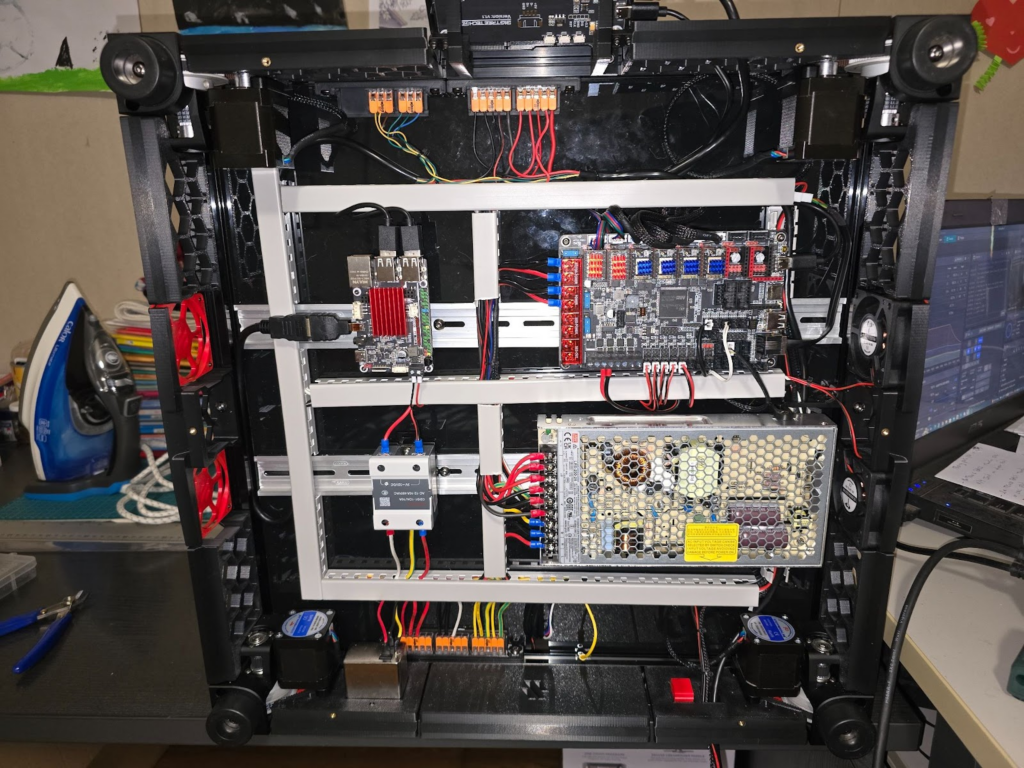
Les panneaux de polycarbonate
Concernant les panneaux, ils sont tous en polycarbonate.
Je suspectais que les transparents soient en acrylique mais non.
Je commence par l’installation de la plaque du bas qui vient recouvrir toute l’électronique.
Pour cela il faut appliquer du double face sur les parties imprimées qui maintiennent la plaque.
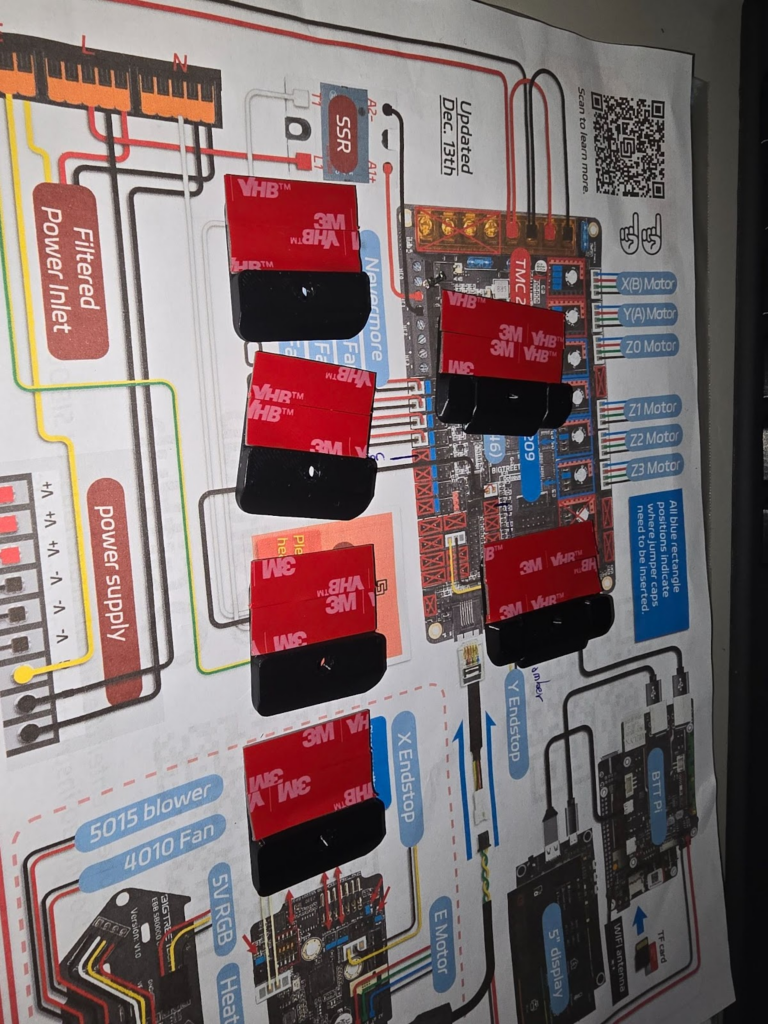
Et mise en place de l’ensemble.
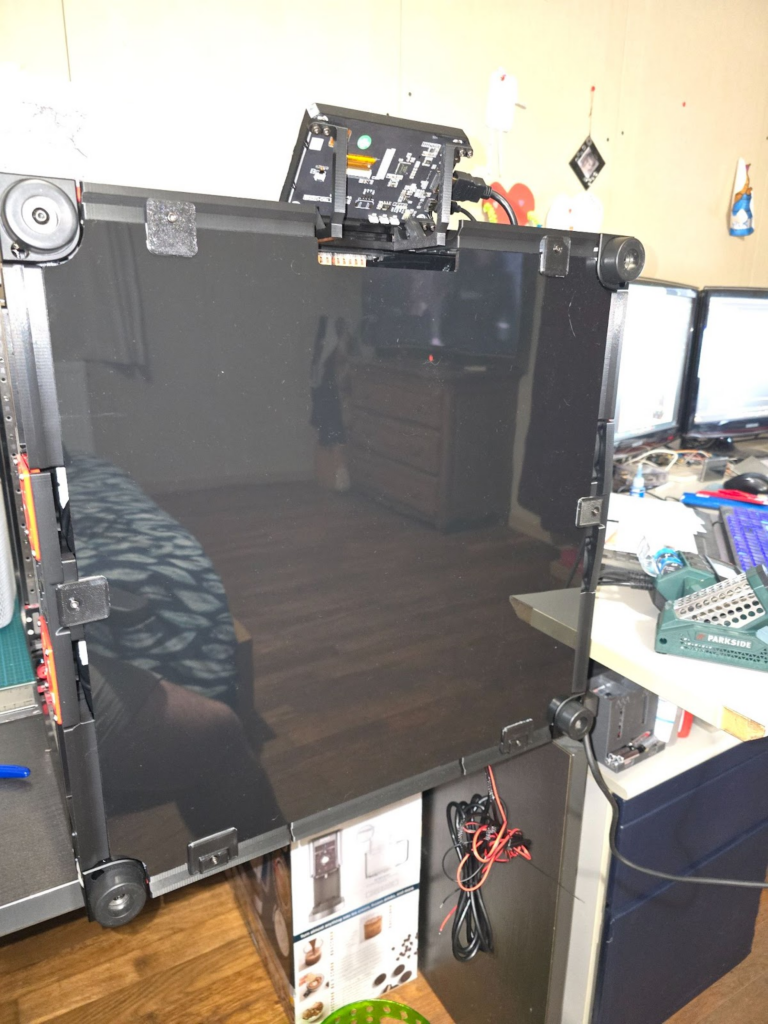
Ensuite, mise en place des caches pour les courroies Z.
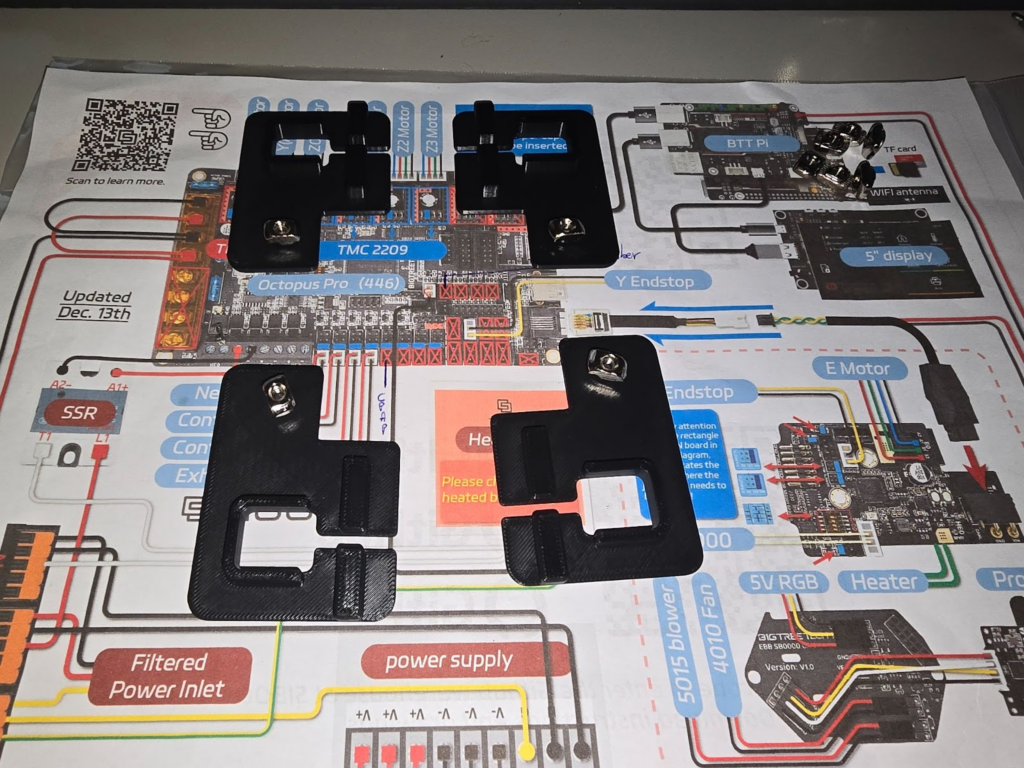
Ils se positionnent aux quatres coins.
Cela permet le maintien de la plaque de polycarbonate et de faire plus propre !
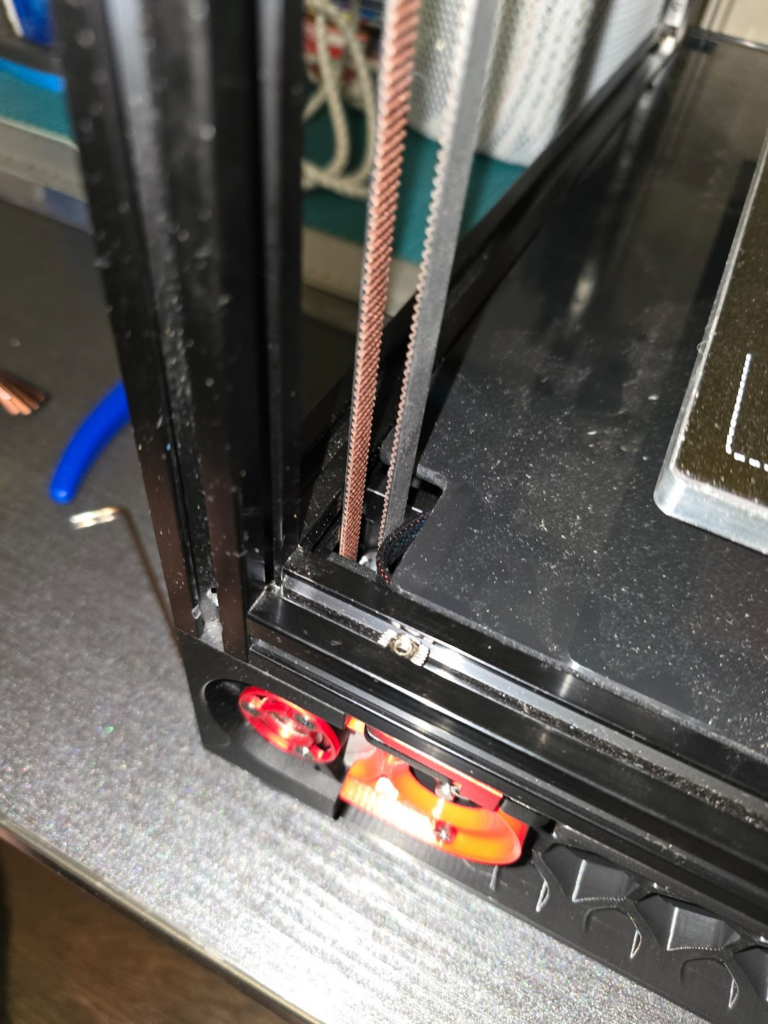
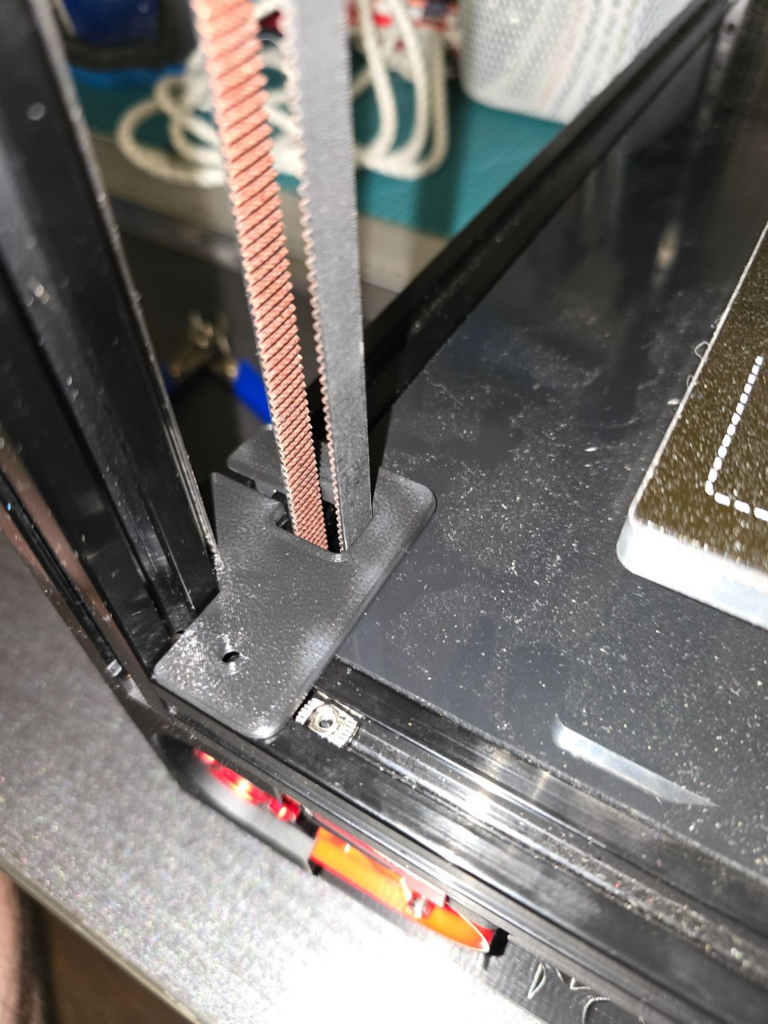
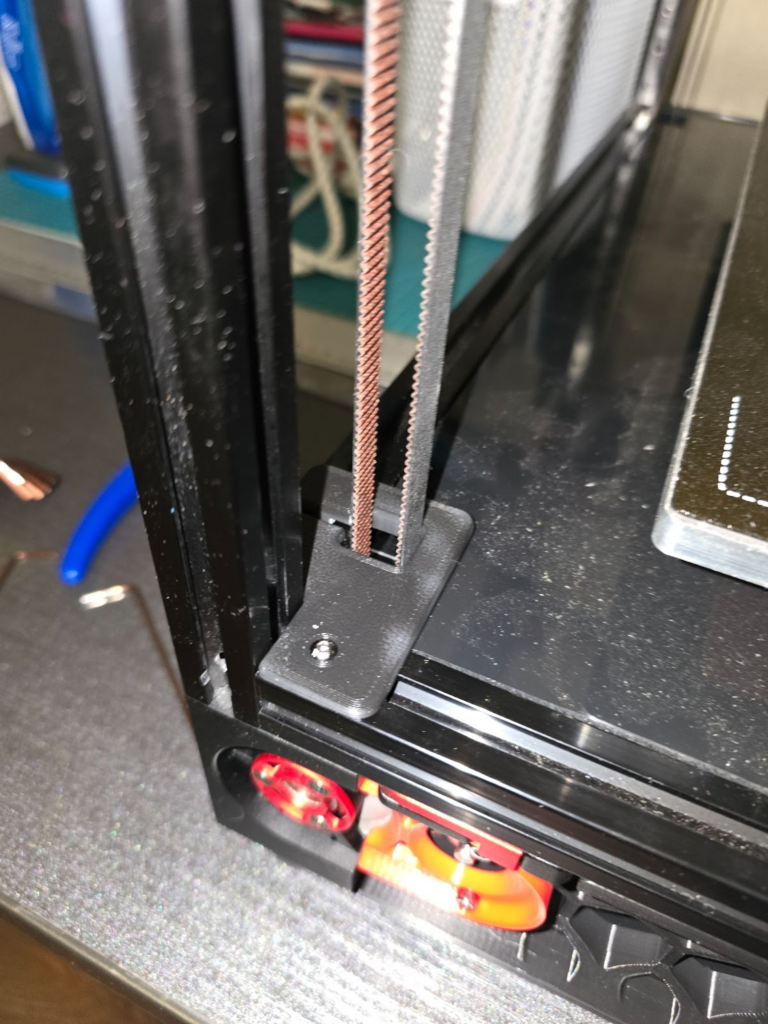
Avant l’installation du panneau arrière, je me suis permis une petite modification.
En effet, ayant prévu une sonde pour la température de la chambre, j’ai réimprimé le guide chaîne Z qui inclut un logement pour la sonde.
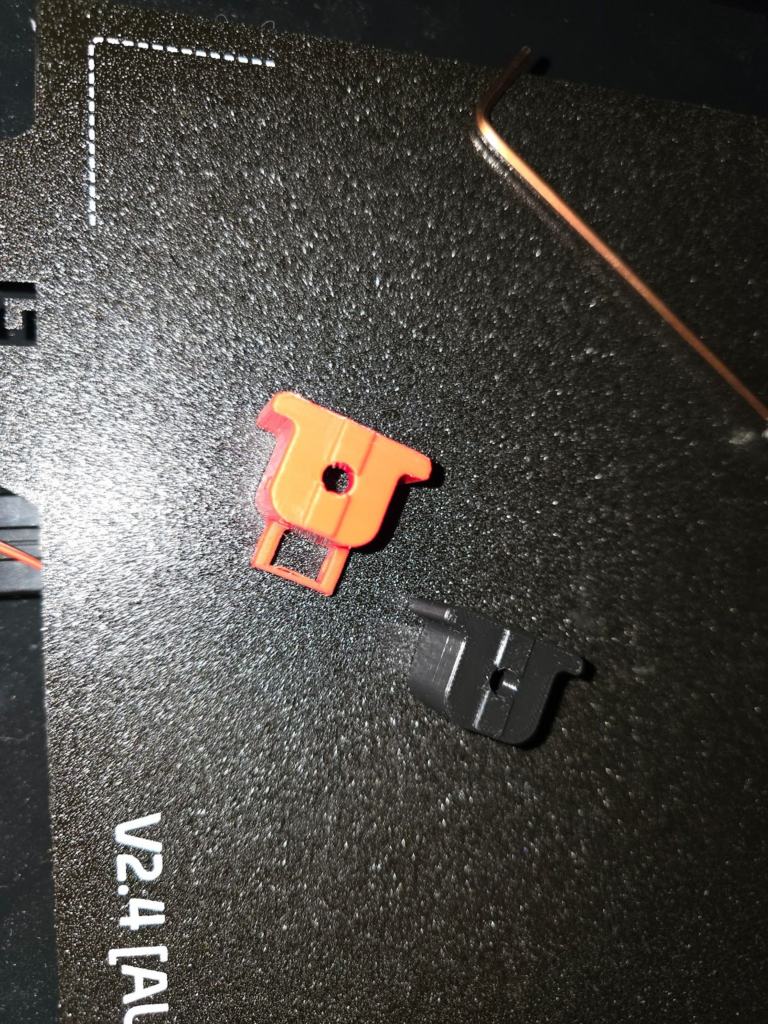
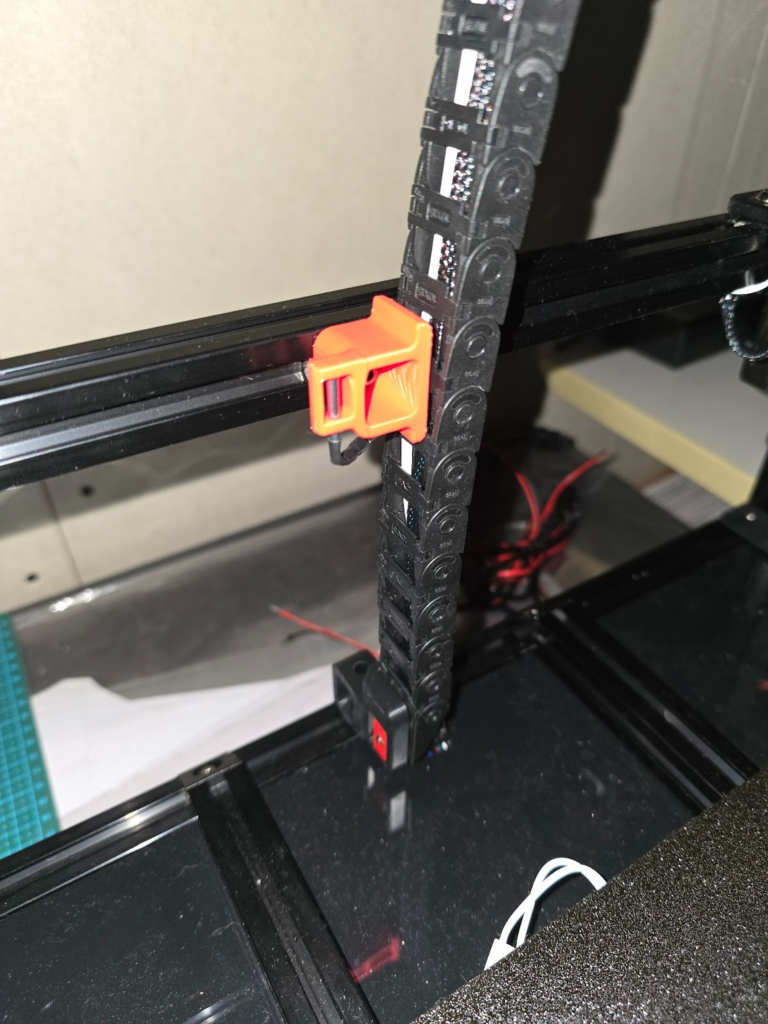
Pour les fixations du panneau arrière, il faut prendre les bonnes. En effet, il y a deux tailles:
4mm et 6mm d’épaisseur. Ici il faut celles de 4mm.
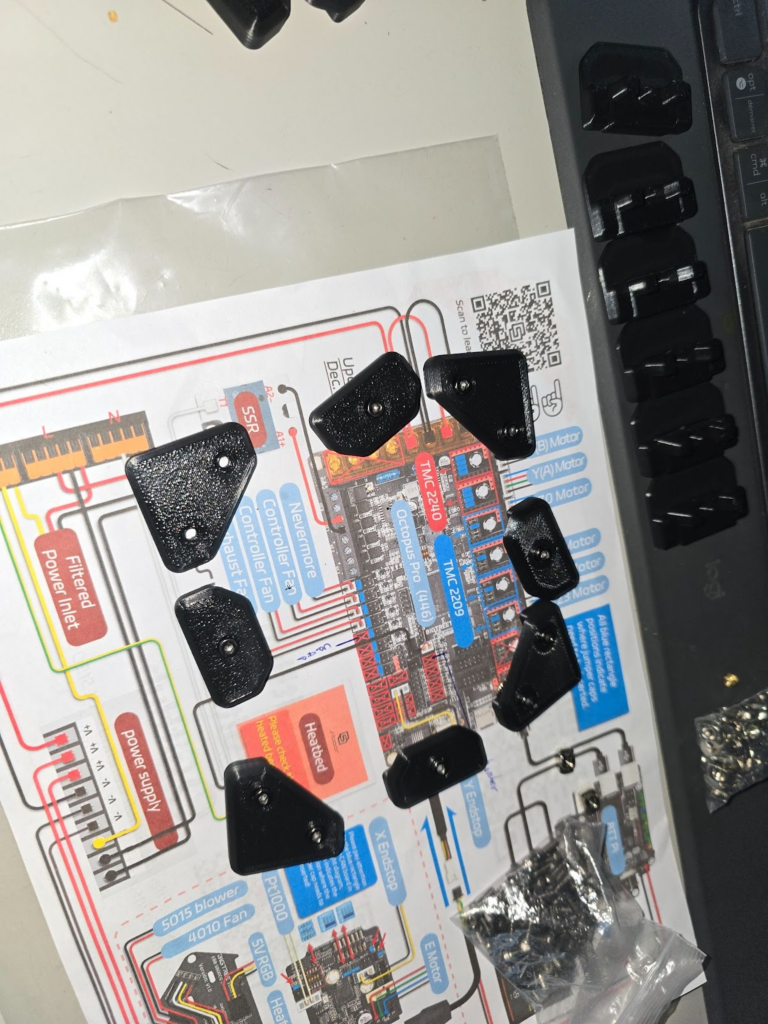
Et pour cause, c’est qu’il faut appliquer de la mousse autocollante de 1 mm d’épaisseur sur le pourtour du panneau. Cela permet de fait un joint pour conserver la chaleur dans l’enceinte.
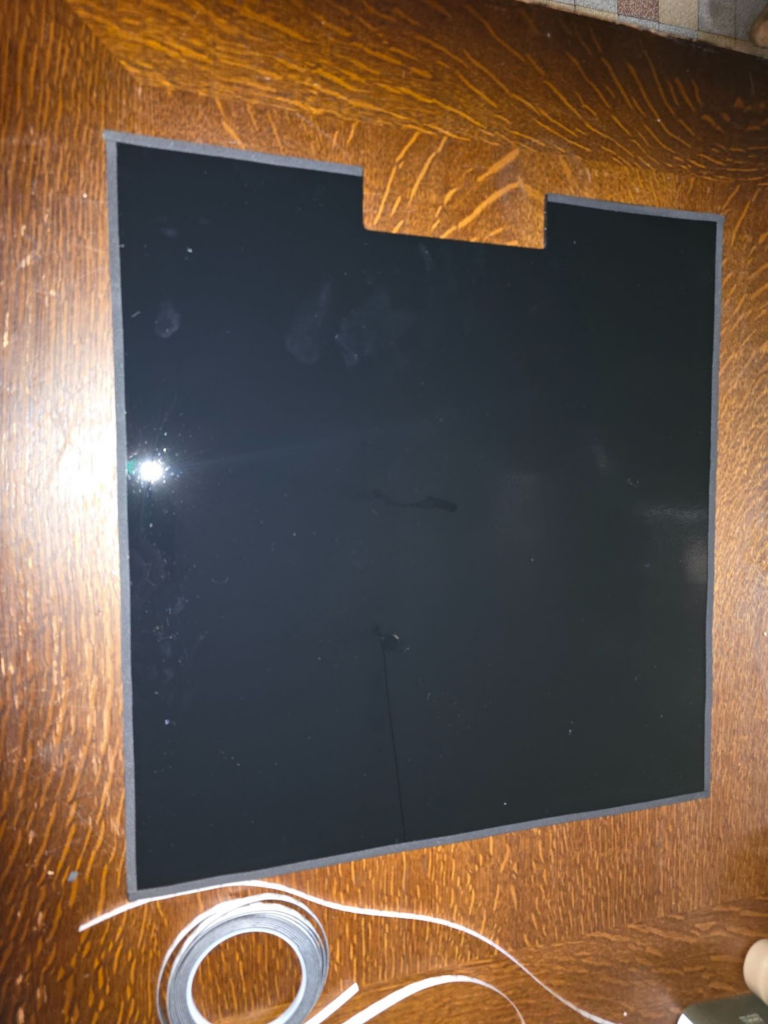
Mise en place de celui-ci.
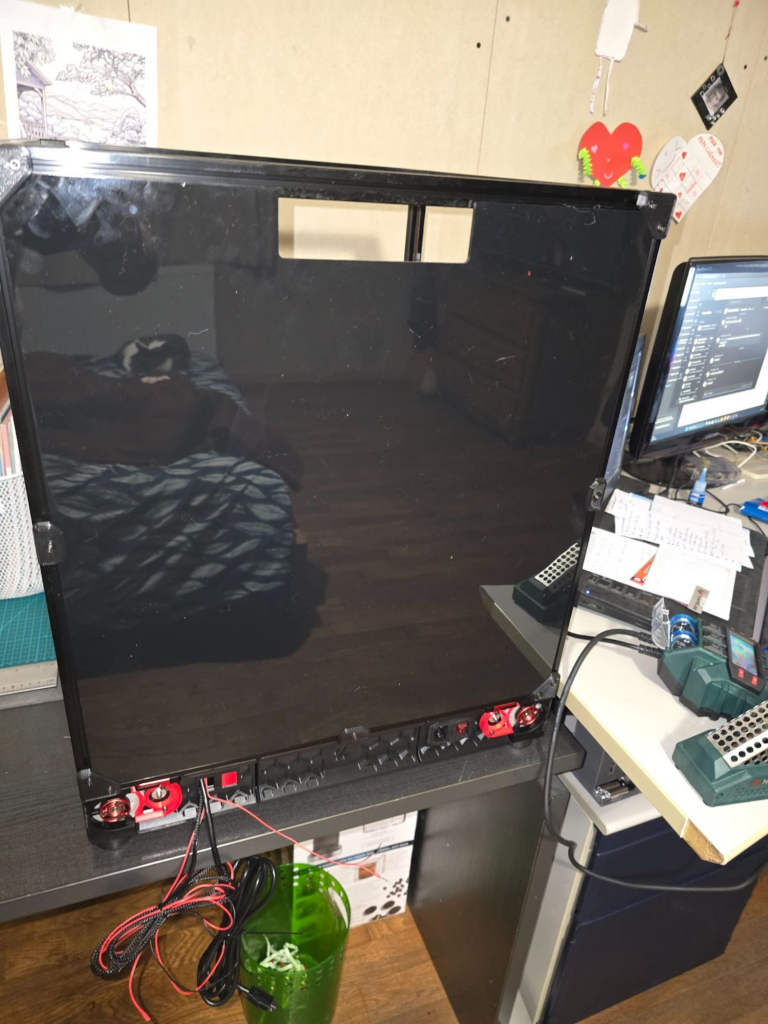
Comme rien ne peut être parfait, je me retrouve encore face à un souci:
Pour le montage des panneaux latéraux il faut des fixations de 6 mm.
Hors, je me retrouve avec seulement 4 coins de 6mm au lieu de 8 et 8 coins de 4mm au lieu de 4 (pour le panneau supérieur).
Idem pour les fixations centrales: là, je n’ai que 8 des 12 fixations de 6mm, ce qui veut dire qu’il va me manquer les 4 pour le panneau supérieur.
Les stls étant disponibles sur le github Voron, je vais donc les télécharger et imprimer ce qui manque.
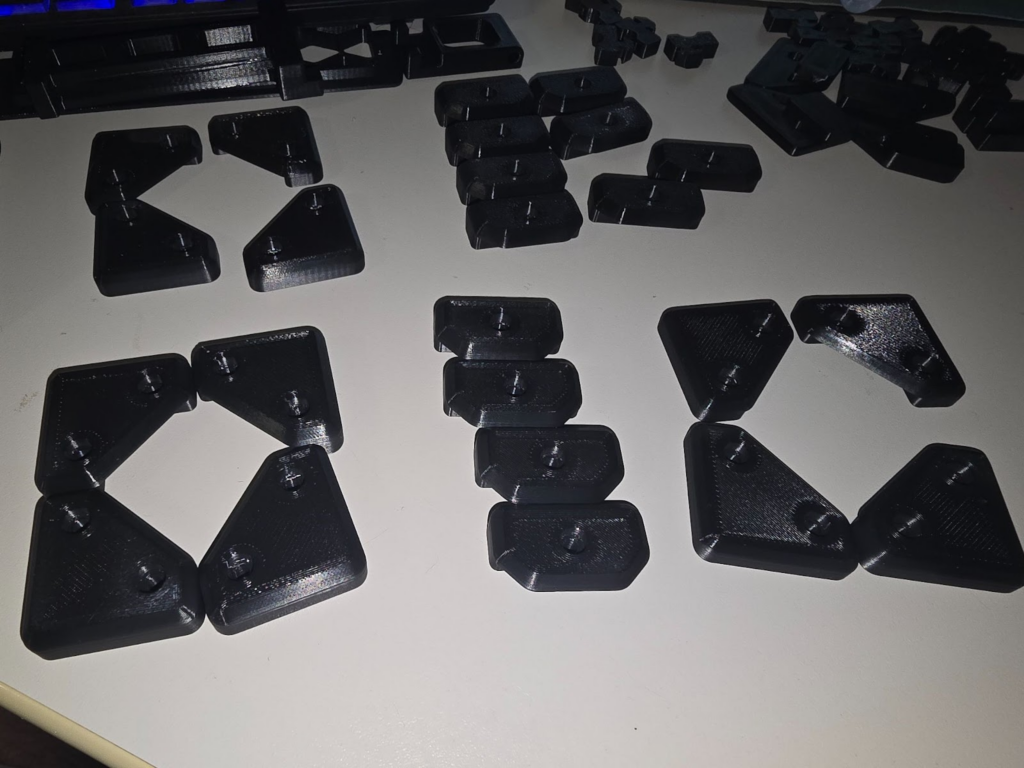
Pendant le temps d’impression, je constate dans le kit qu’il y a ce genre de pièces.
Seulement nul part dans la documentation, il n’en est fait mention.
Petite recherche internet, et j’apprends qu’en fait ce sont des clips qui vont dans le caisson électronique, qui se fixent par rotation dans les profilés aluminium pour maintenir en place la plaque de polycarbonate supérieur (celle qui est fixée par les rails din)
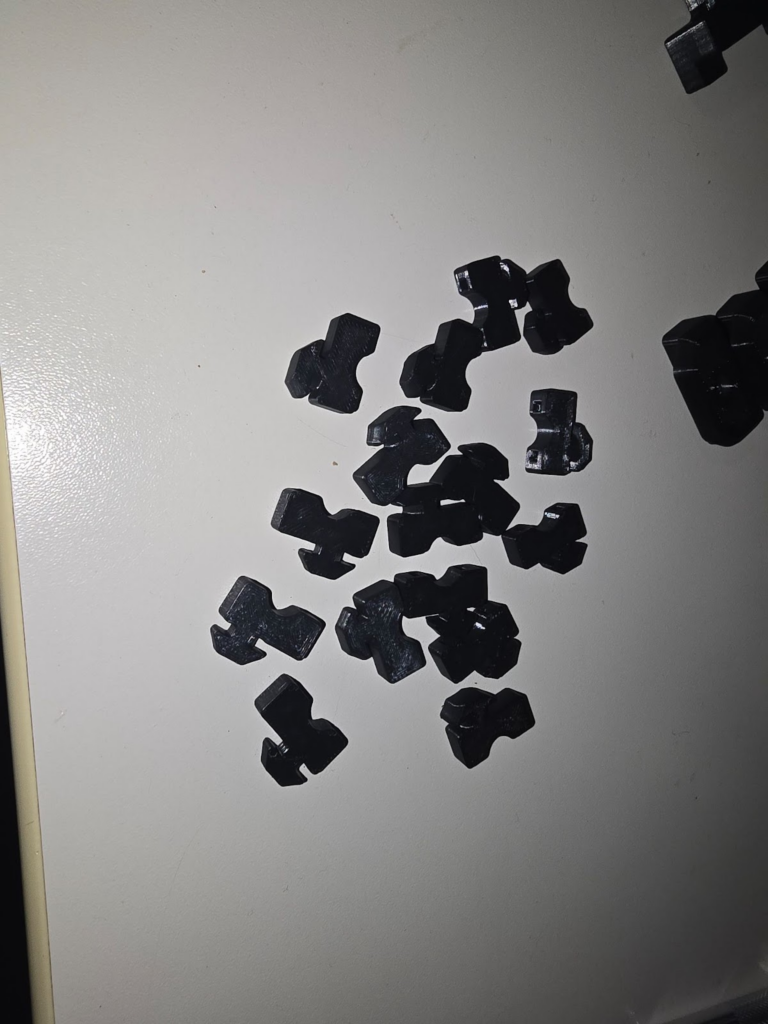

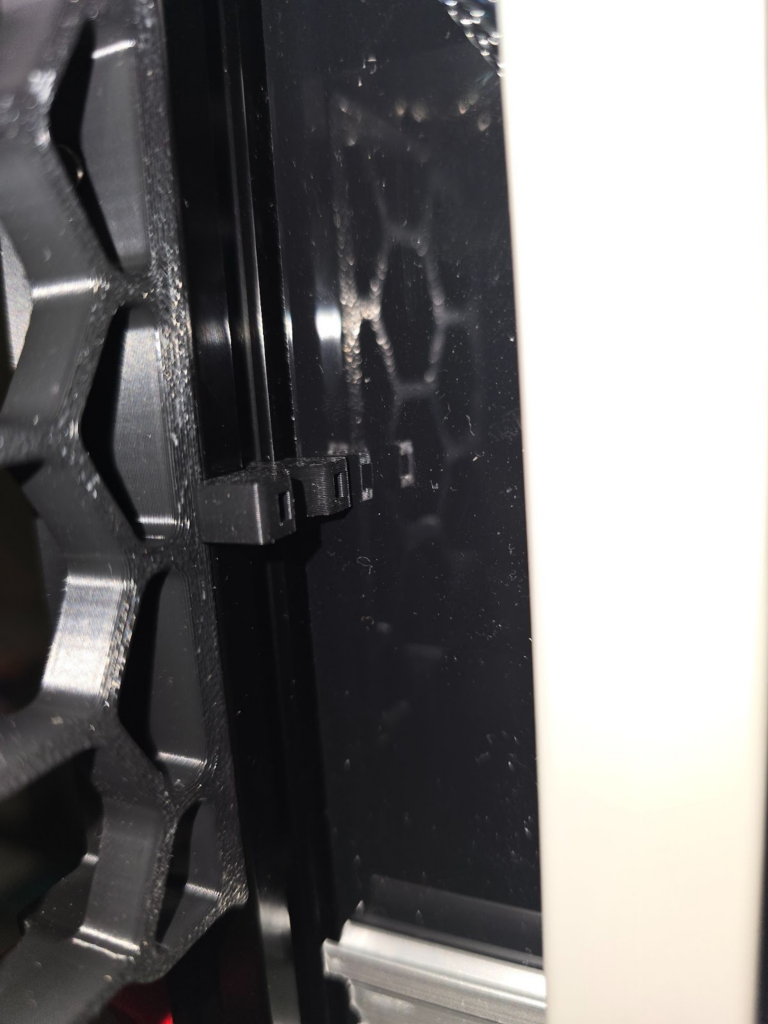
Ceci fait et les impressions des pièces manquantes terminées, j’installe les panneaux latéraux et celui du dessus (je les ai faites en rouge pour une petite touche custom !)
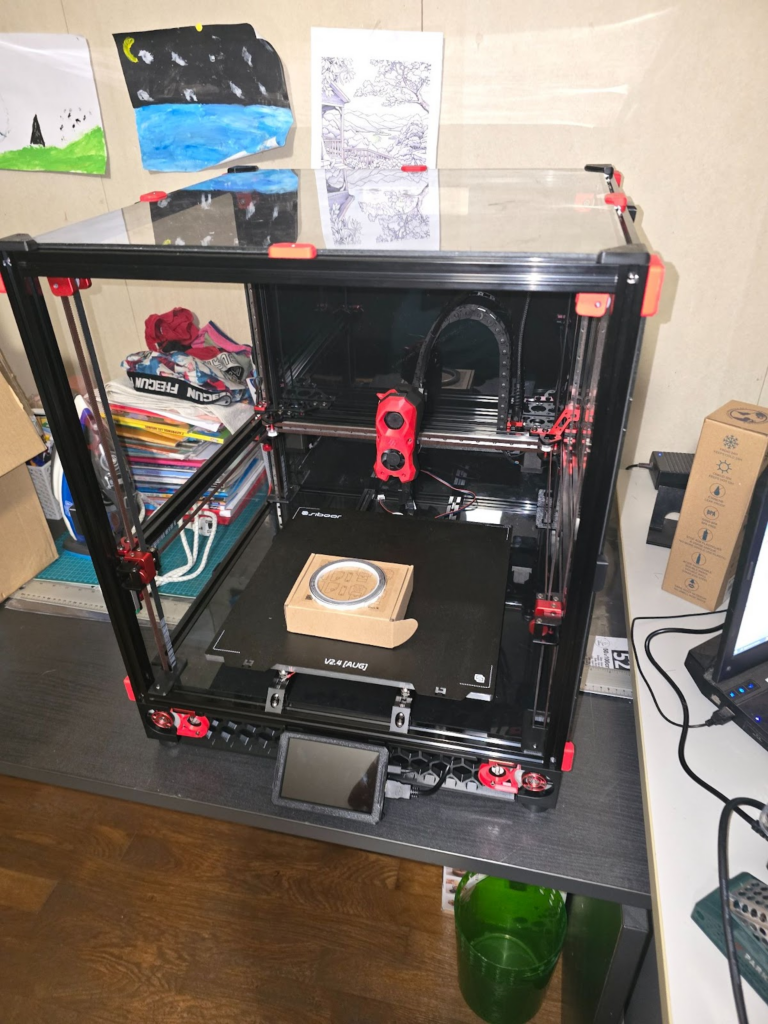
Passons aux portes maintenant.
Pour cela, je ne vais pas utiliser les parties imprimées du kit avec le scotch double face, mais j’ai acquis un kit de fixation CNC de Chaoticlab.
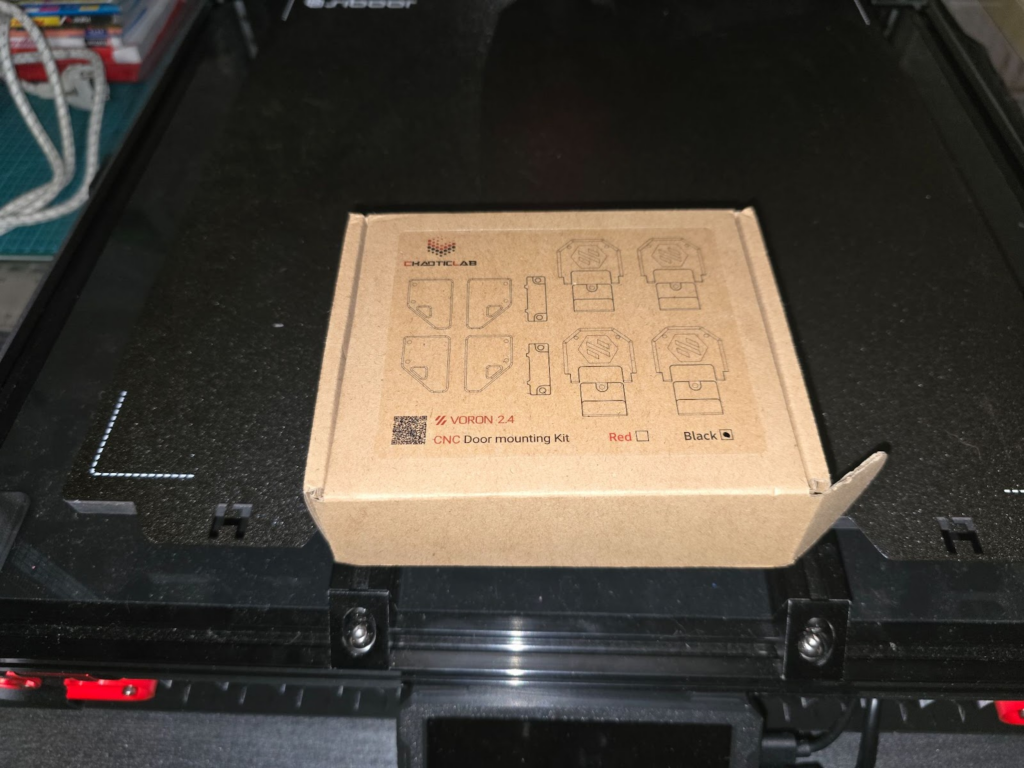
Comme tous les autres kits, les pièces en aluminium sont légères et d’excellente qualitée.
Cependant il n’y a aucune documentation sur l’installation de celui-ci.
Donc ça va être en mode découverte, analyse et bon sens.
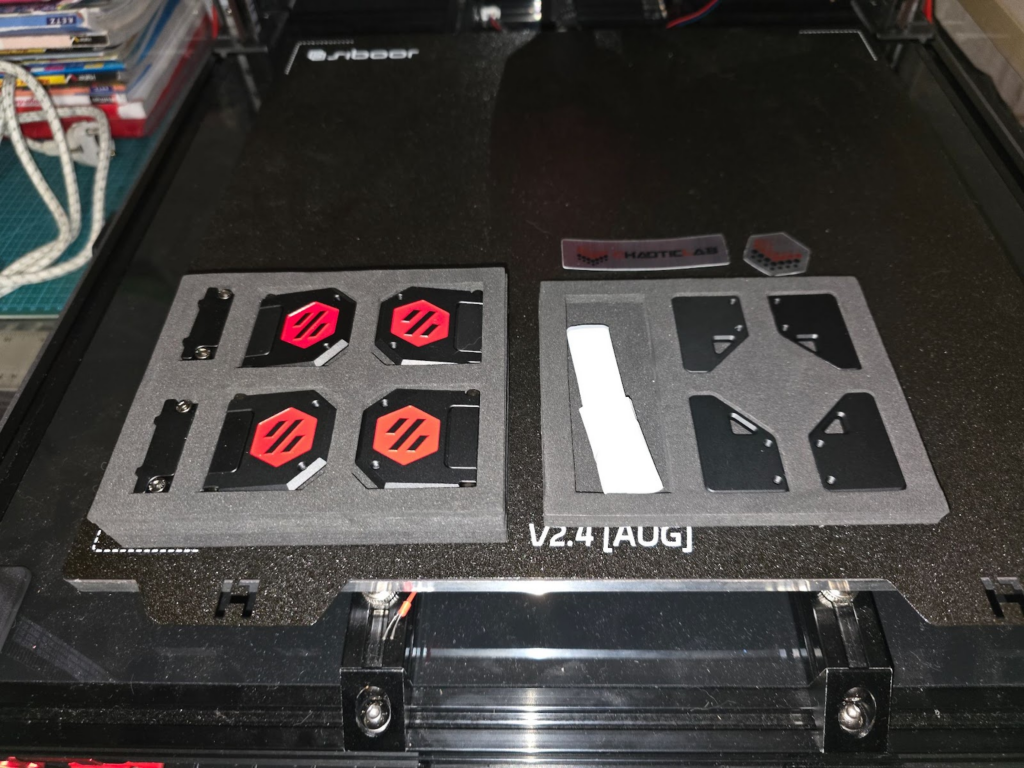
Je commence par les parties supérieures et inférieures. Contrairement aux parties imprimées, celles-ci ne sont pas collées au double face mais fixées à l’aide de vis. Il faut donc percer le polycarbonate. Pour cela je positionne la pièce en place, je pré-perce avec un foret de 2mm à travers le filet de la pièce aluminium, pour être sûr d’être au bon endroit, et ensuite je reperce avec un foret de 3.2mm pour que les vis de 3mm puissent bien passer.
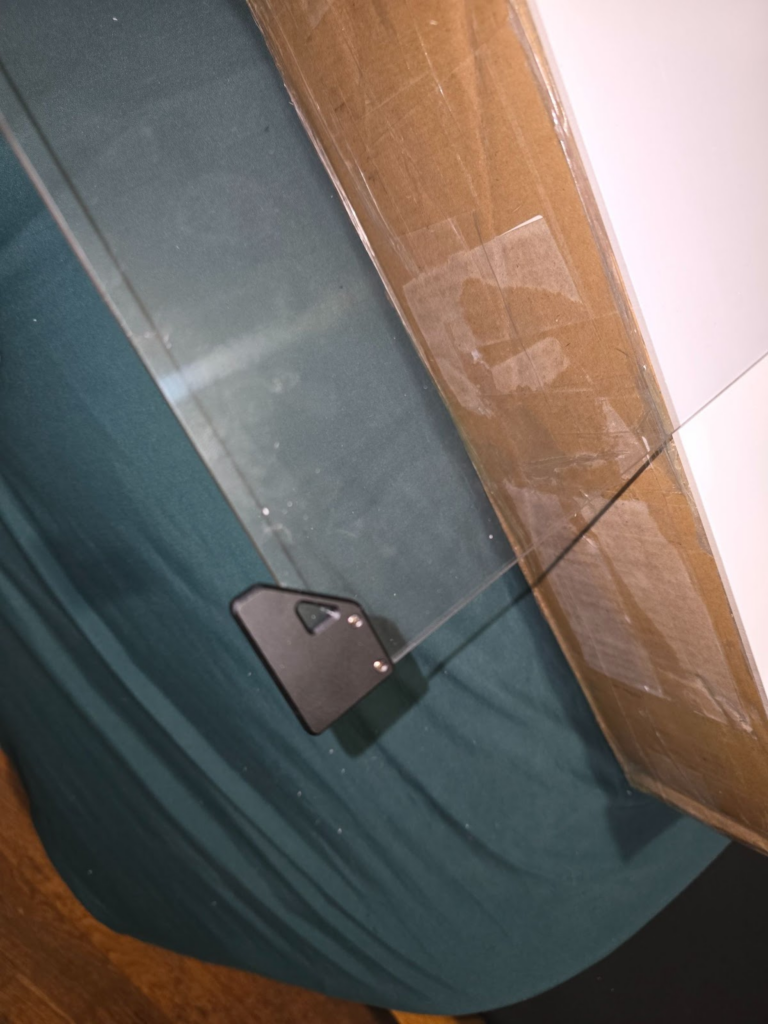
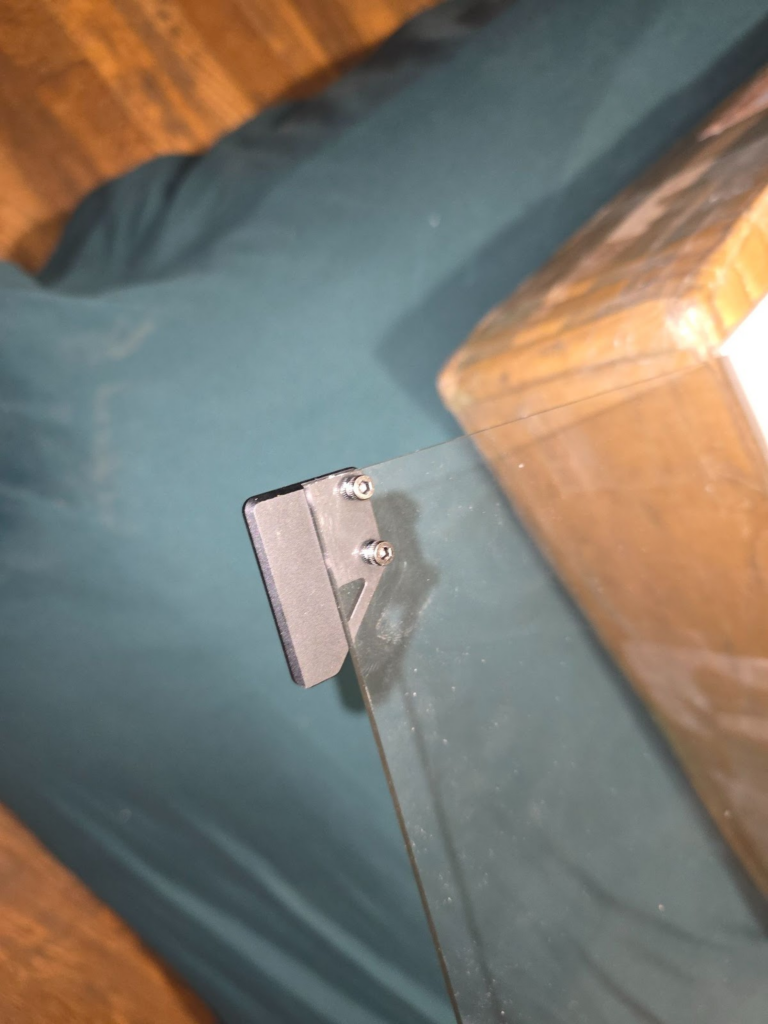
Les quatre parties supérieures et inférieures posées, je vais passer aux charnières.
Pour m’aider au positionnement, je vais utiliser de chaque côté une charnière imprimée au milieux.
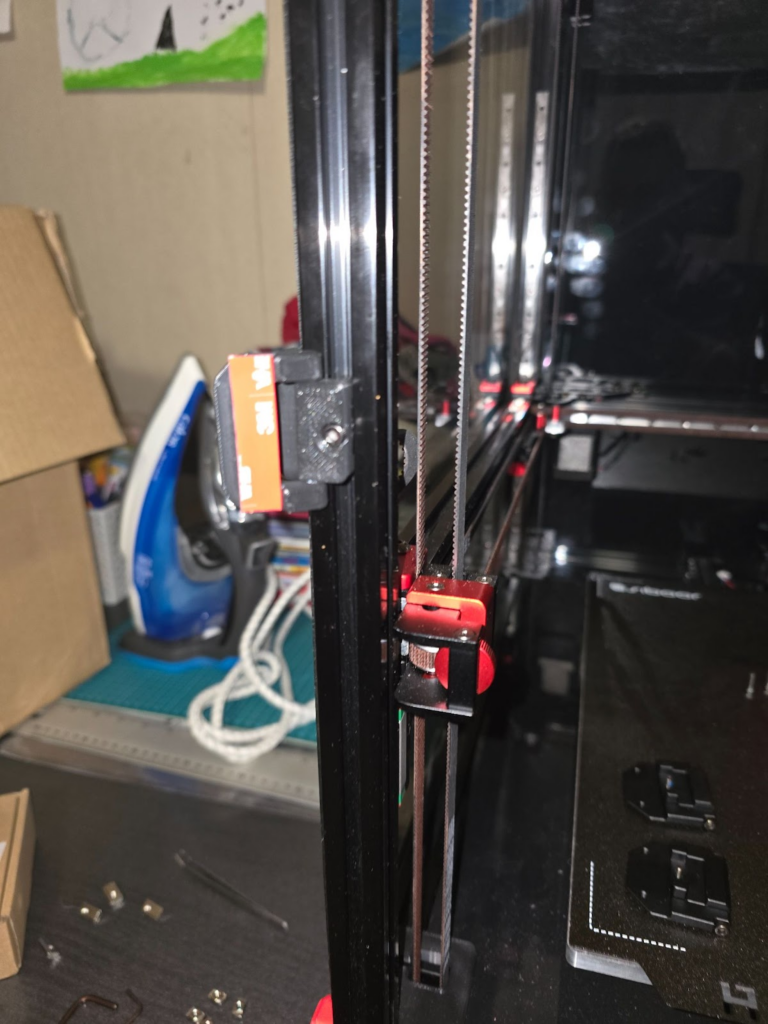
J’installe les parties hautes et basses avec les aimants, je positionne la porte, et je la maintiens en place avec une pince.
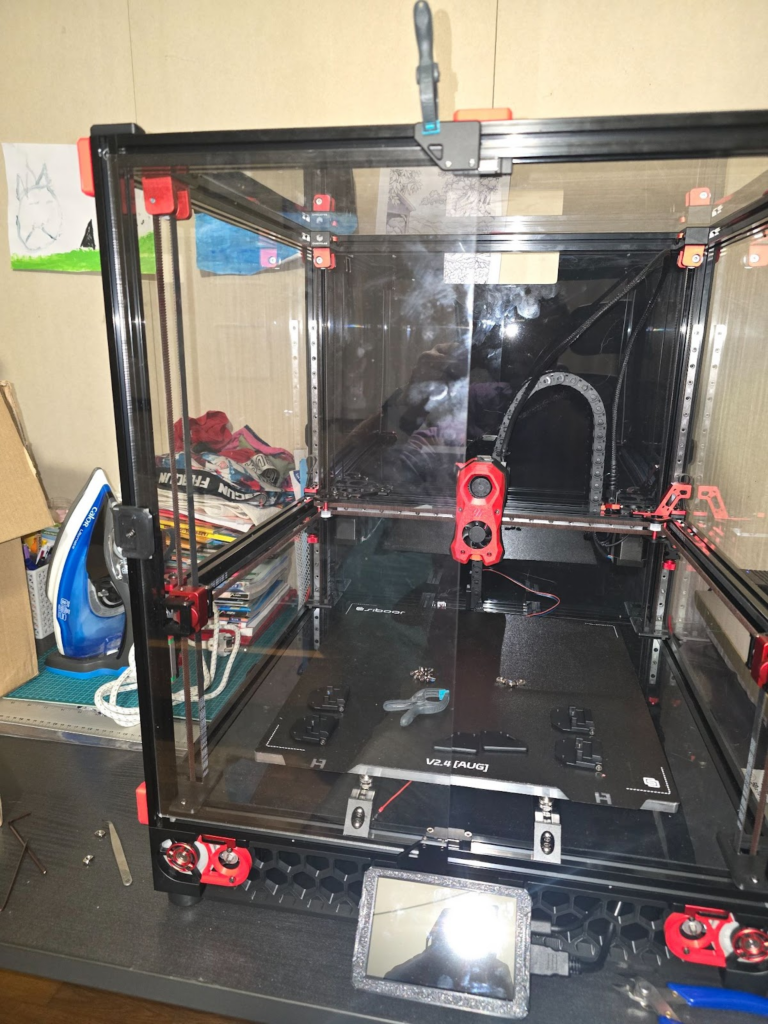
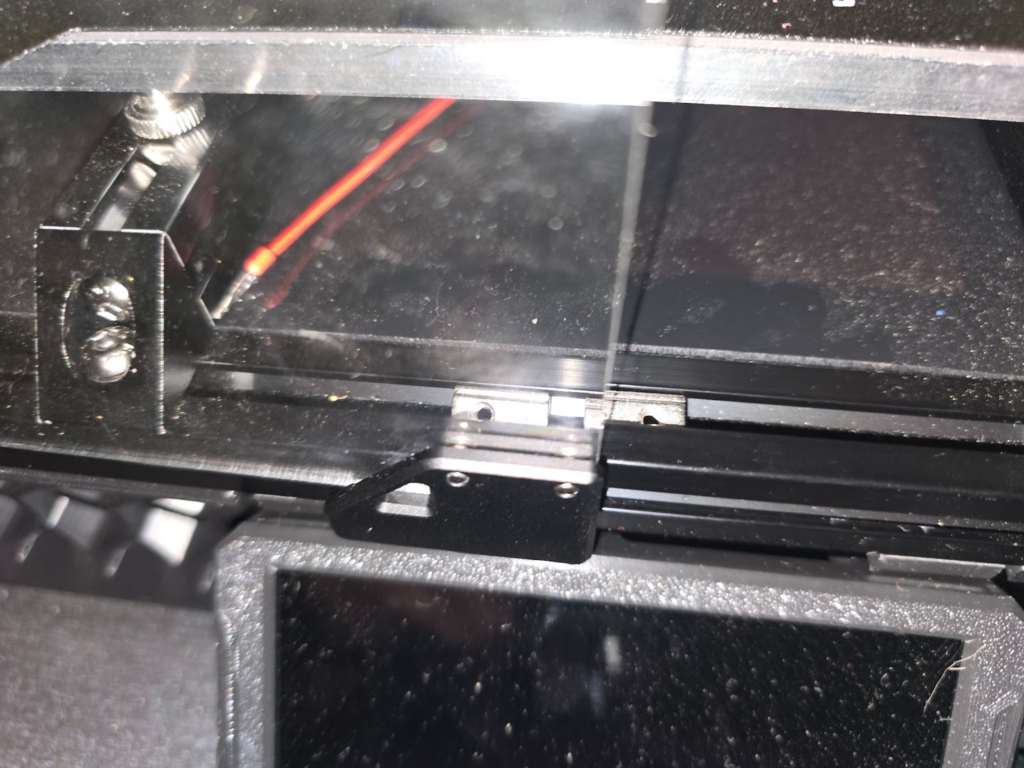
Je fais de même avec la deuxième porte.
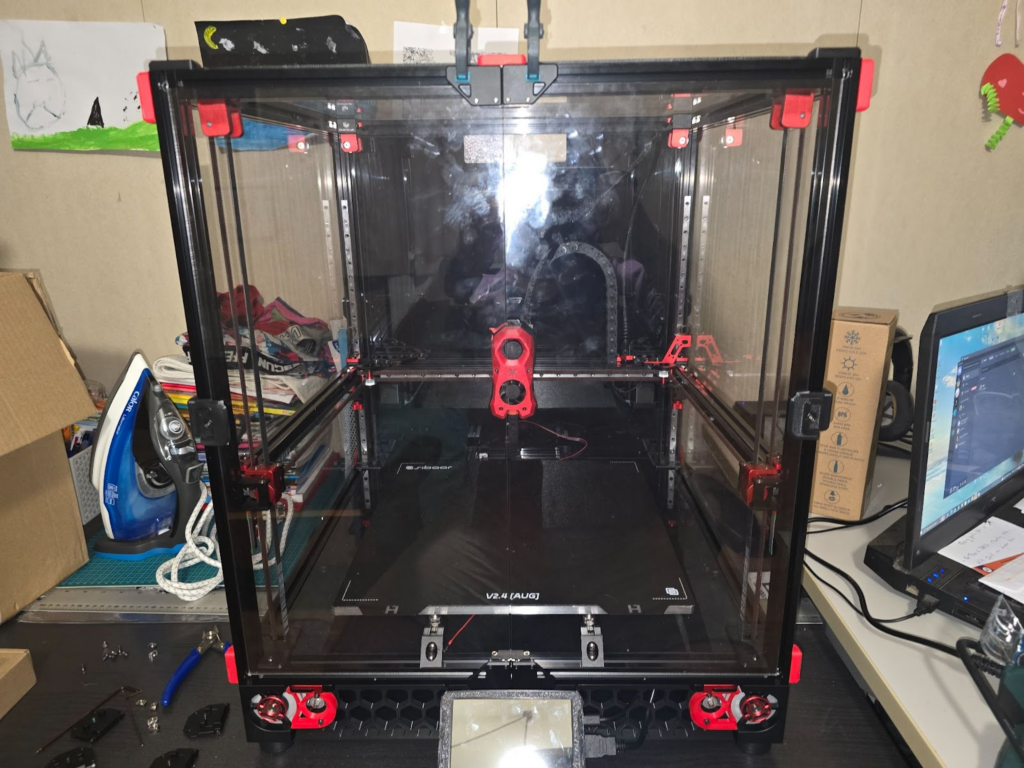
Je positionne les charnières du kit, et je procède avec la même méthode que précédemment: pré-perçage à 2 mm et agrandissement à 3.2mm.
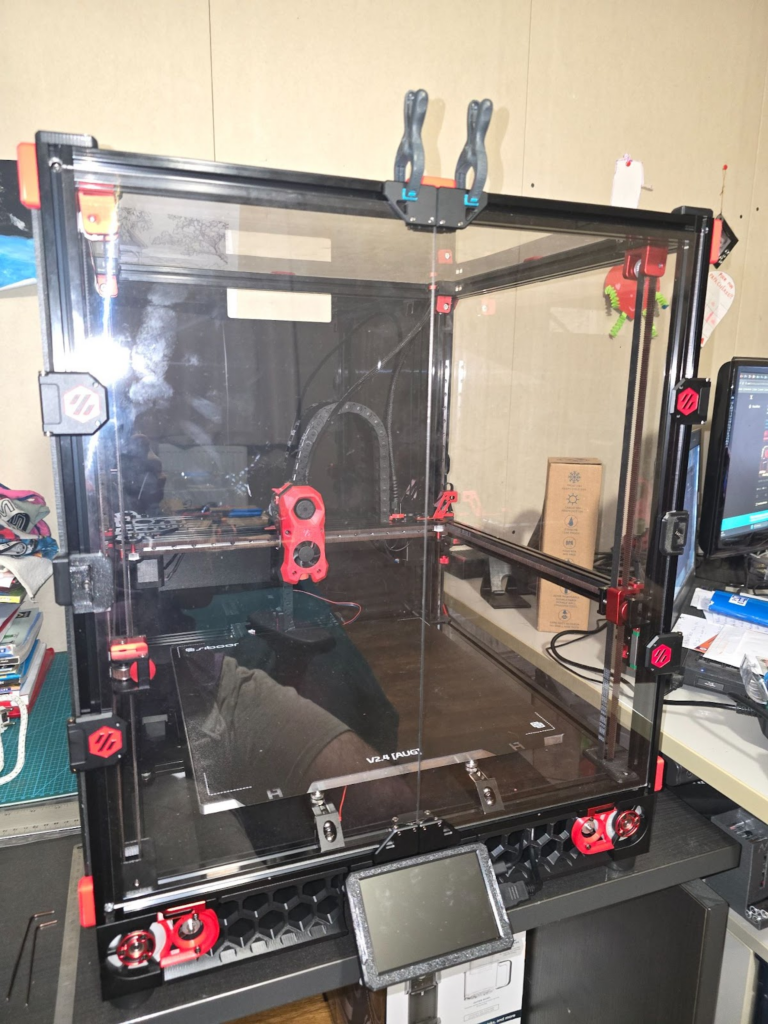
Une fois le tout en place, il me reste un peu de mousse autocollante de 1 mm. j’en profite donc pour faire les côtés et le haut des portes.
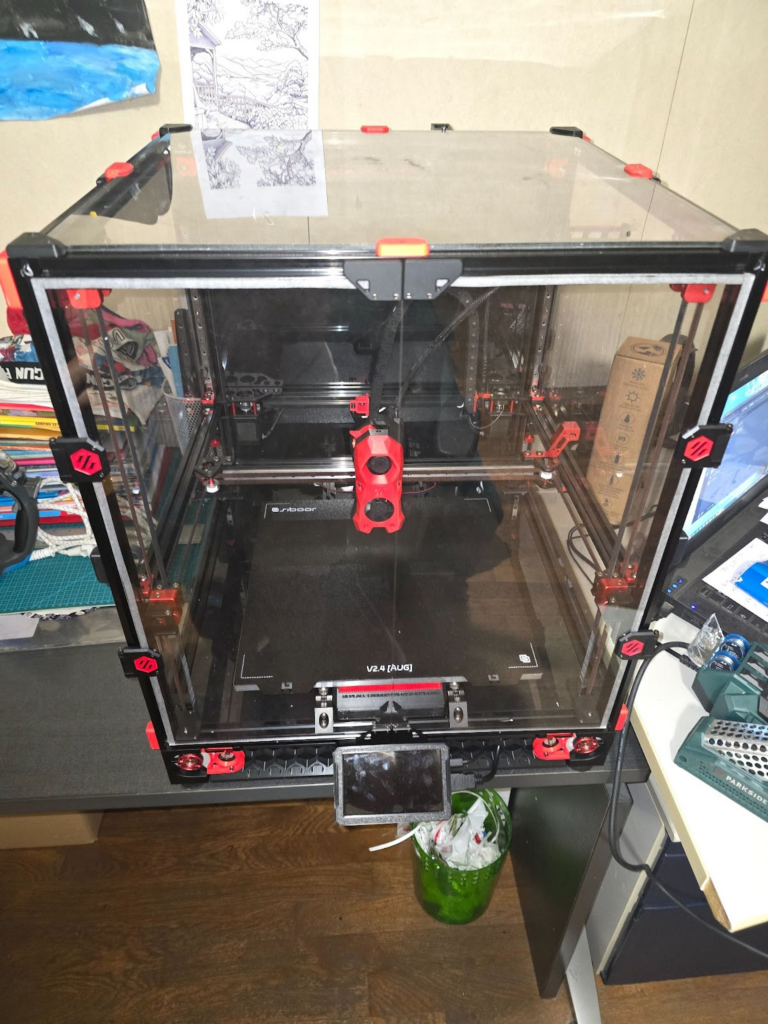
Et voilà !
J’ai préféré investir dans ce kit plutôt que d’utiliser les parties imprimées, car à mon avis celles-ci vont s’user dans le temps, vu le nombre d’ouvertures et fermetures des portes. J’ai donc voulu quelque chose de plus durable. Cependant, les aimants de maintien des portes sont vraiment costauds (Neodymium) et il va falloir que j’imprime des poignées pour que cela soit plus confortable à l’usage.
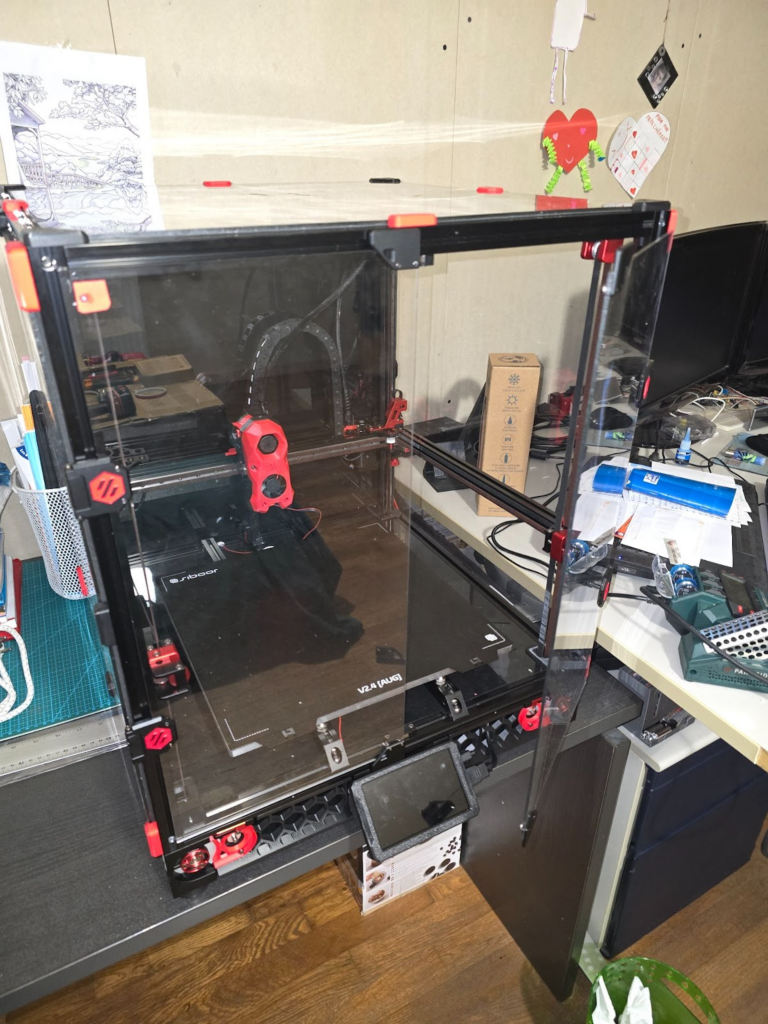
L’extracteur d’air (pour le contrôle de température de la chambre)
Voilà, c’est la dernière partie du montage de la machine !
Ce bloc est prévu pour réguler la température de la chambre mais aussi pour accueillir un élément filtrant si nécessaire. Il existe plein de mods pour adapter toutes sortes de filtres (personnellement, je vais partir de filtres Hepa prévus à la base pour les robots ménager Roomba)
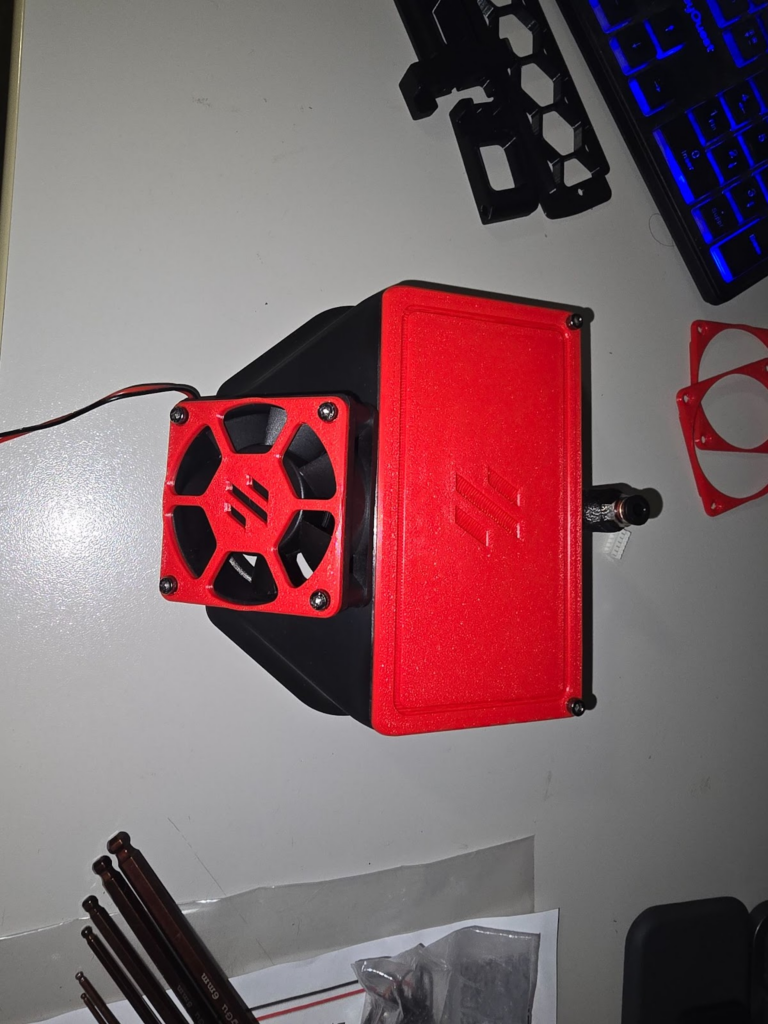
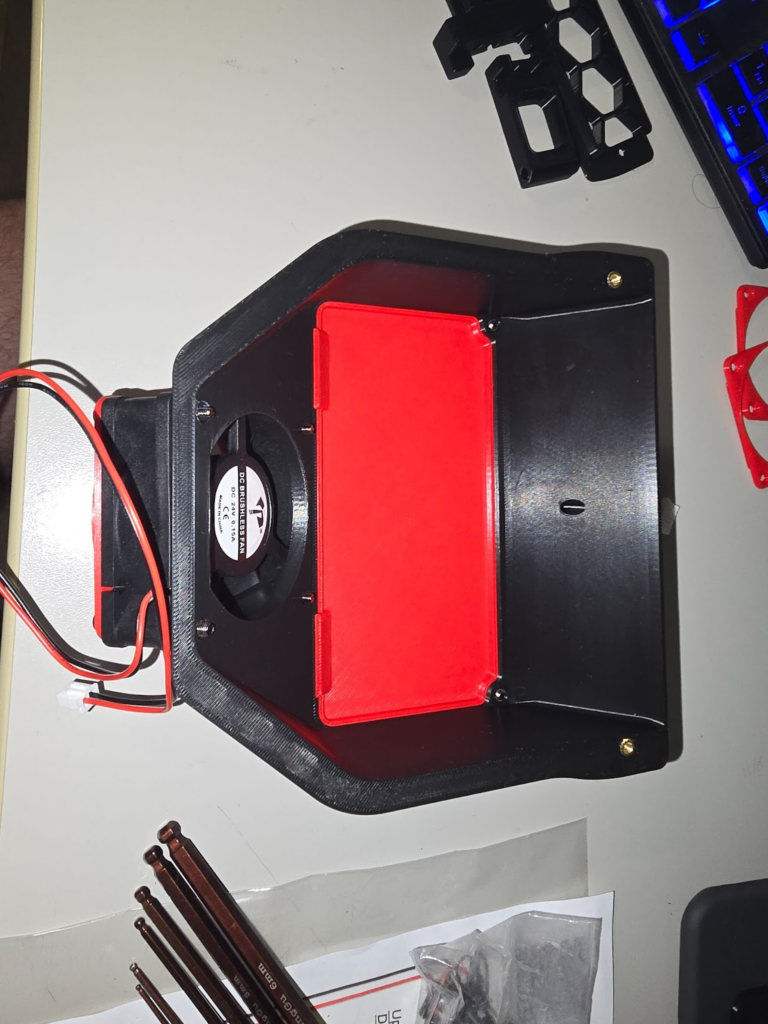
Application de scotch double face pour mise en place sur la plaque de polycarbonate.
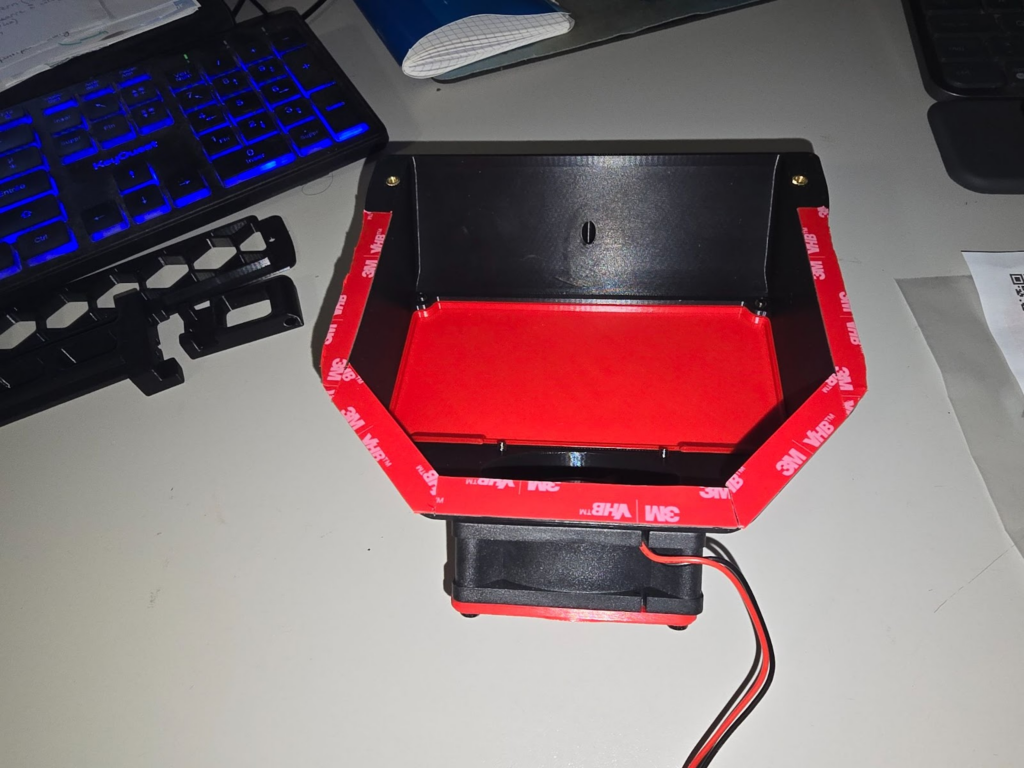
Mise en place des supports et de la grille de fixation
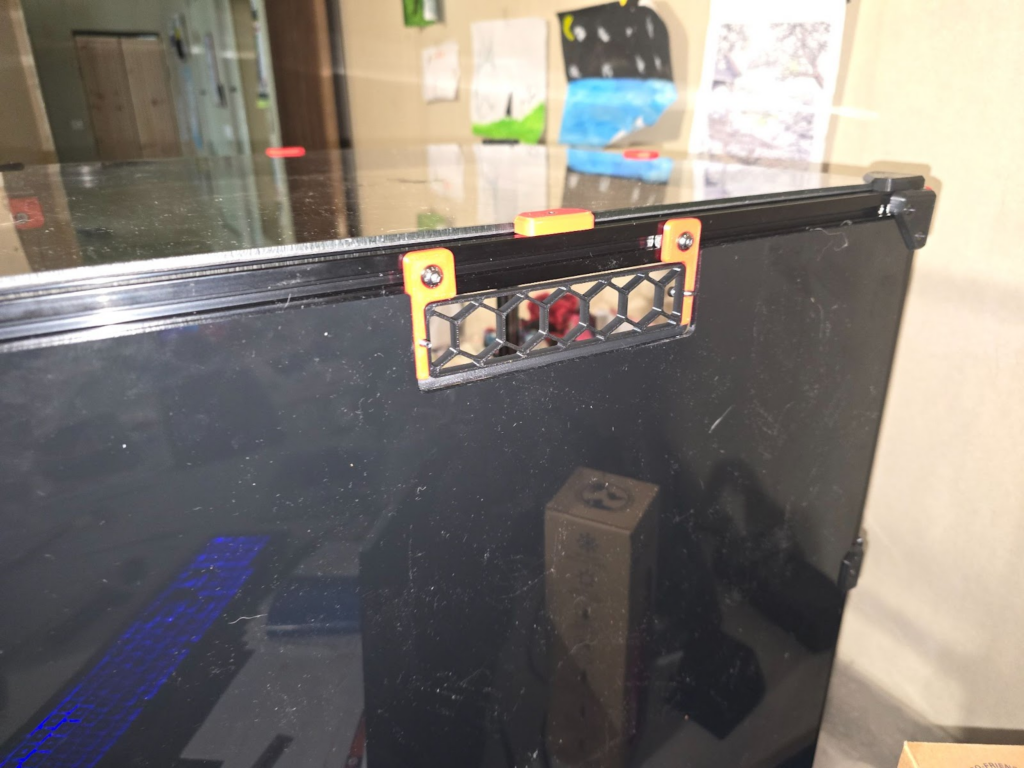
Pose de l’ensemble: alors je dois avouer qu’avec la version 350×350 de la machine, l’installation seule, c’est vraiment pas évident sauf si on a de très grands bras. En effet, les vis sont à l’intérieur de machine et il faut maintenir en face le bloc à l’extérieur avant de coller le tout … Bref, c’est plus simple à deux !
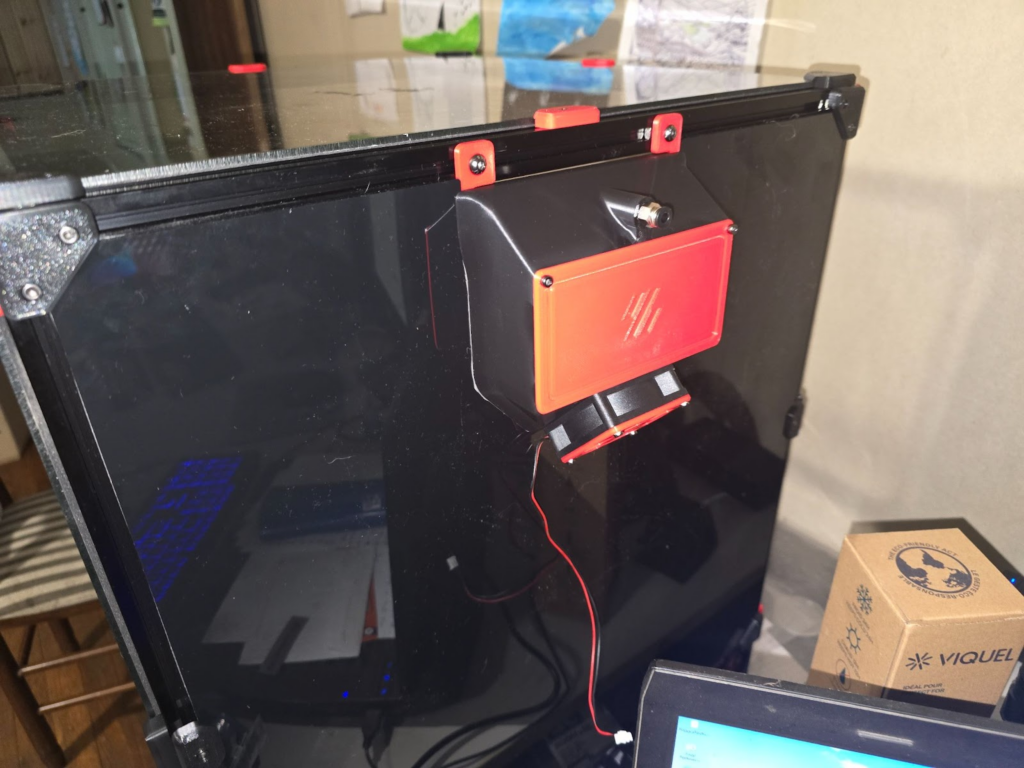
Et enfin, mise en place du guide PTFE et du support bobine !
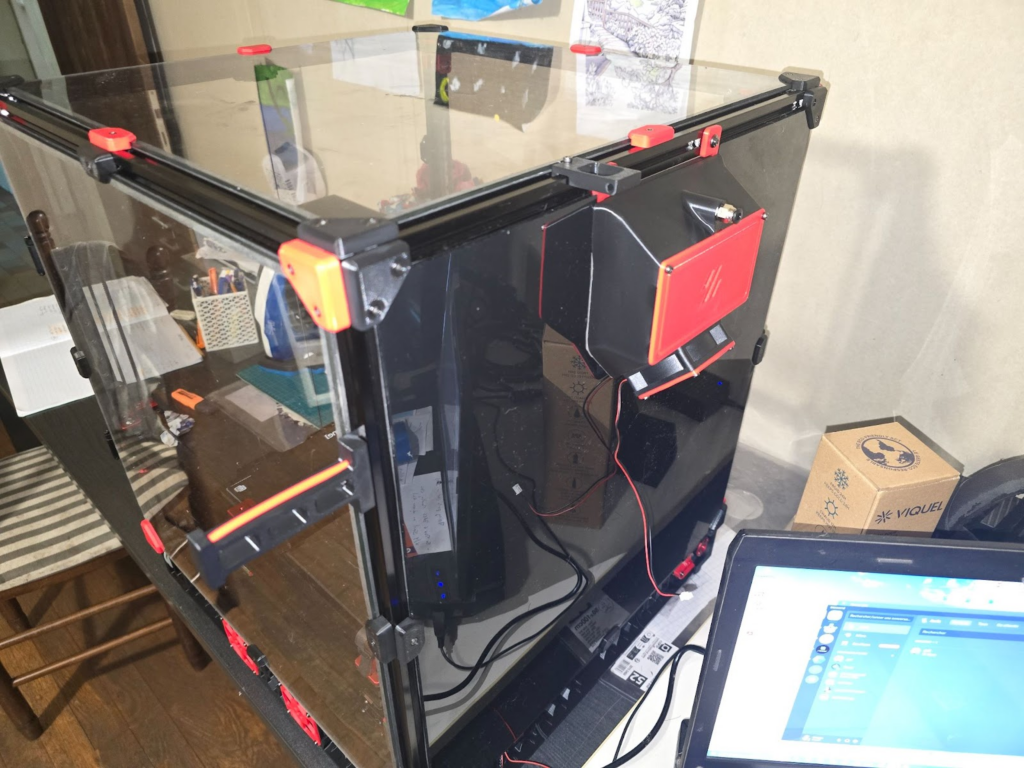
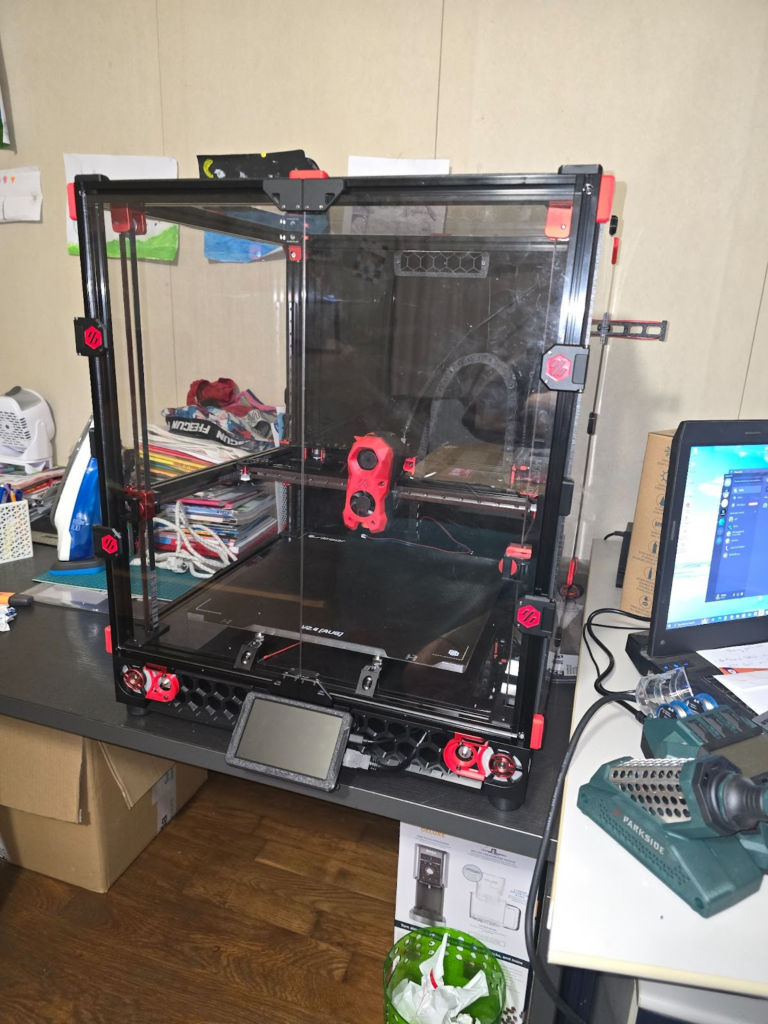
Le module Nevermore
La dernière partie de cet article concerne une amélioration fournie avec le kit: le module Nevermore, dans sa version 6. Ce module a deux fonctions: la circulation de l’air dans le caisson pour une meilleure homogénéité de la température lorsque que cela est requis, et la filtration des particules fines grâce à du charbon actif.
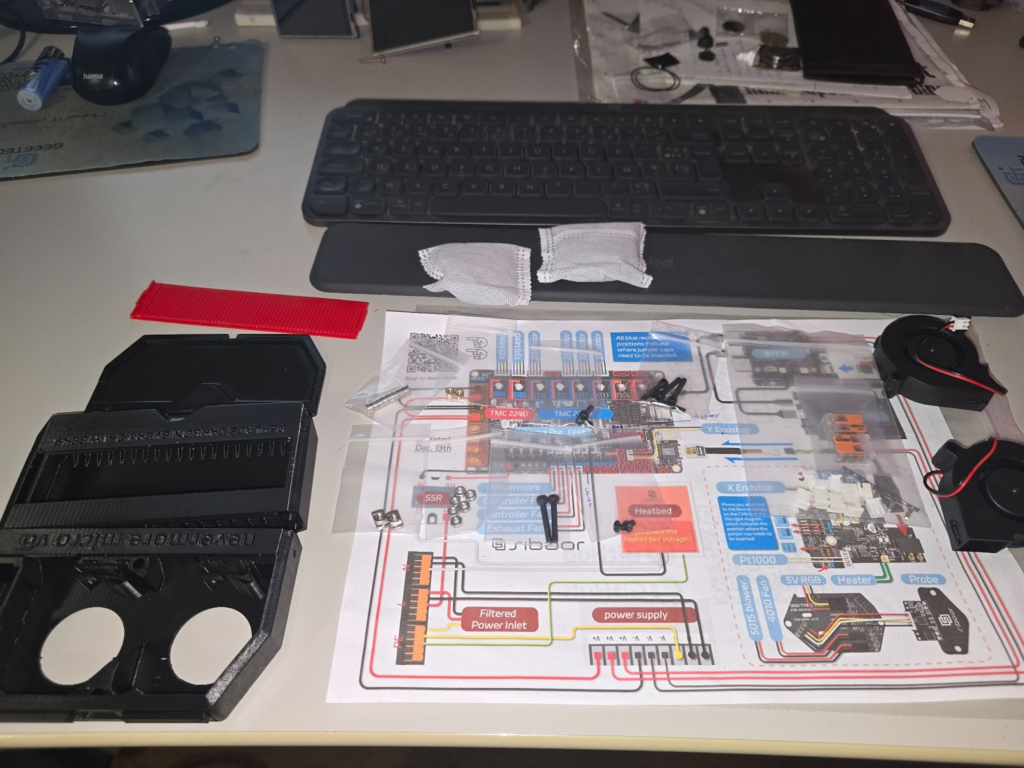
Je place les deux ventilateurs 5015 dans leurs logements ainsi que les aimants qui permettent aux deux parties de se maintenir ensemble. En effet, la partie avec les ventilateurs a pour vocation de rester à demeure dans la machine mais le bloc où viennent se loger les sachets de charbon actifs doit pouvoir être retiré facilement, d’où les aimants !
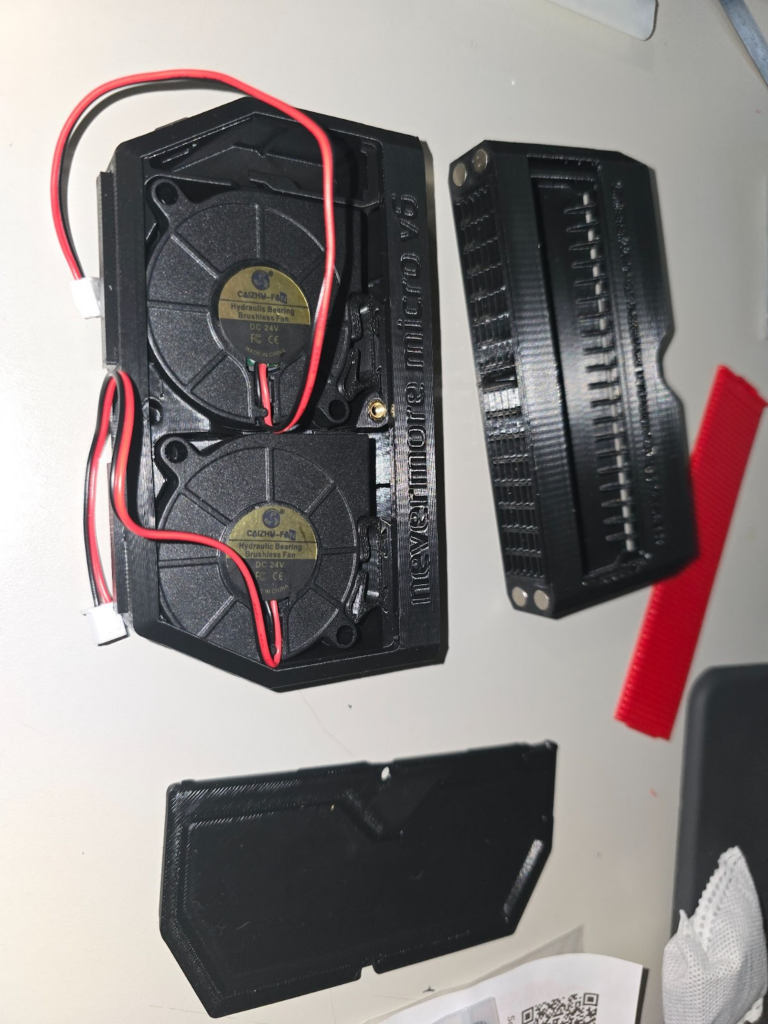
Câblage des ventilateurs avec des cosses terminales.
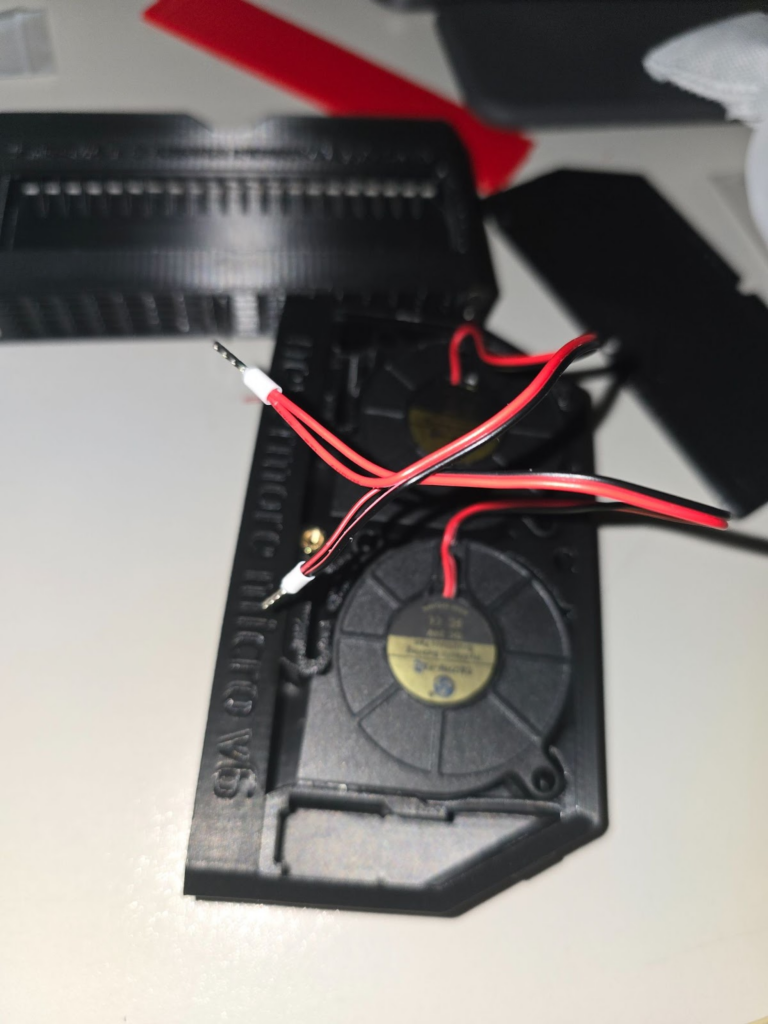
Mise en place dans les Wago. et connexion aux fils préalablement passés qui vont à la carte mère

Placement des sachets de charbon dans leur logement:
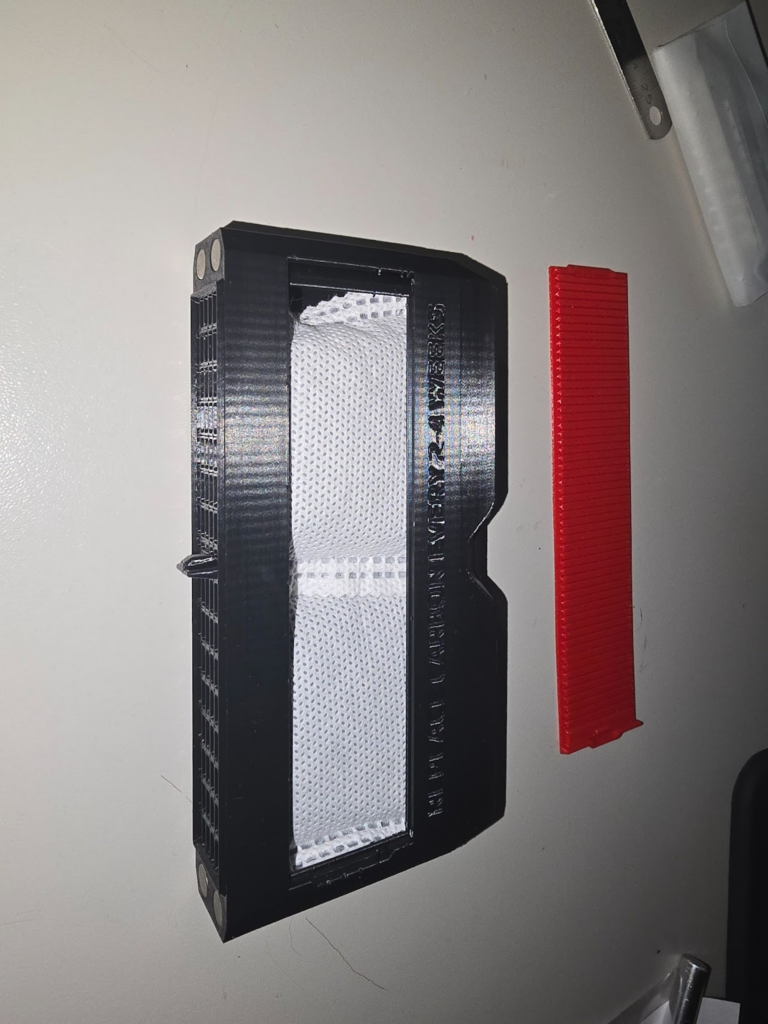
Mise en place de la partie 1 du module sous le lit chauffant.
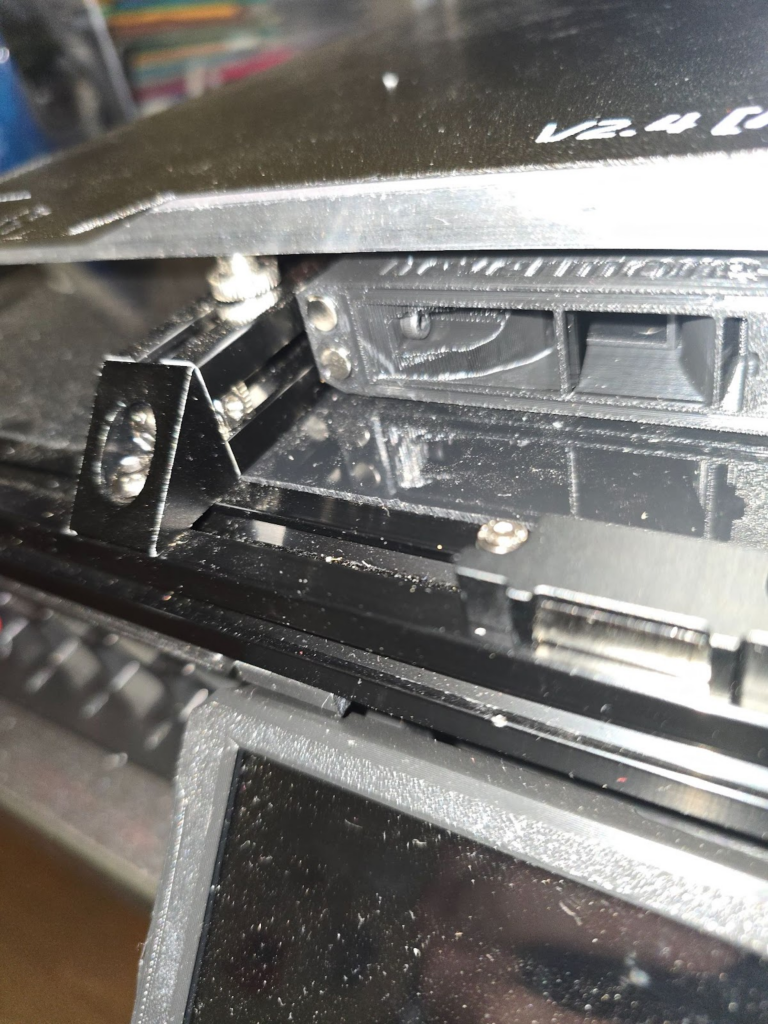
Et mariage de la deuxième partie grâce aux aimants !
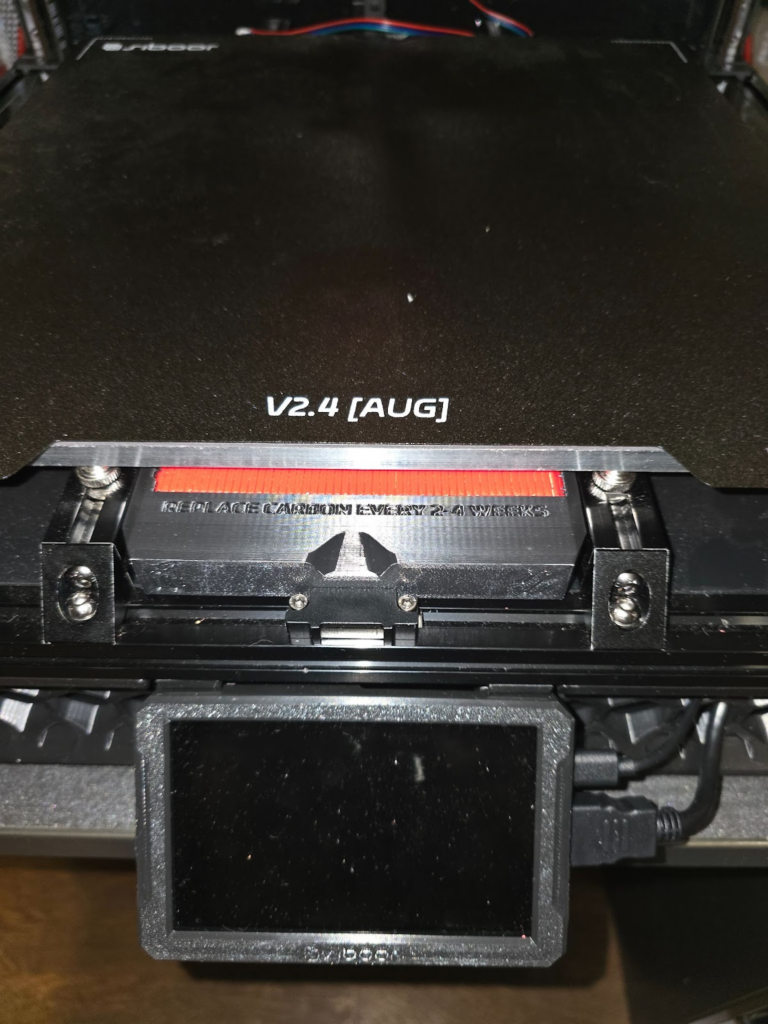
Et voilà, c’est fini !
Instant crucial: je branche la bête, j’allume et là, soulagement, elle démarre !!!
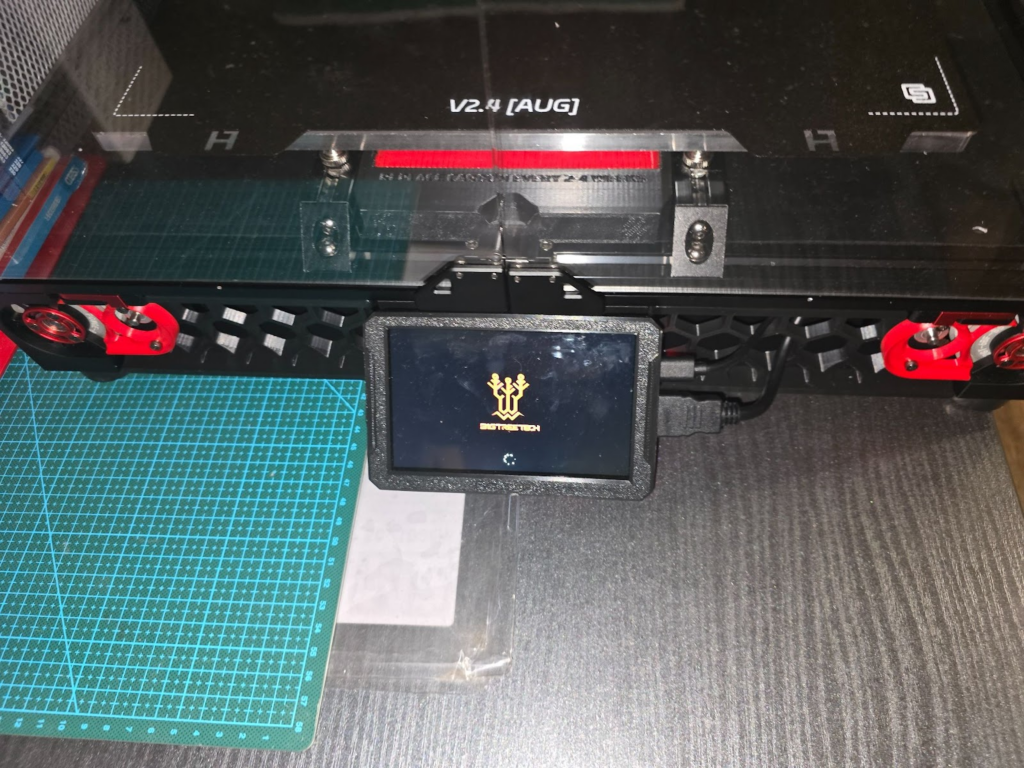
Conclusion :
Comme vous avez pu le voir tout au long de cet article fortement illustré, c’est une grande aventure dans laquelle il faut avoir de la patience et prendre son temps.
Il ne faut pas hésiter à contrôler son travail plusieurs fois et faire des pauses.
La partie électronique nécessite quelques compétences en câblage, mais lorsque l’on est maker il faut un peu savoir tout faire. Surtout lorsque l’on s’attaque à la maintenance ou à la conception d’imprimante 3D.
Ce kit aura nécessité un peu plus de 30 heures de temps cumulé pour le montage, que j’ai réparti sur 4 semaines (bah oui j’ai aussi une vie à côté 😛)
Néanmoins, comme vous avez pu le voir, le résultat est là !
Il me tarde de la mettre en fonctionnement mais pour cela il va falloir faire le firmware !
Siboor, dans son gitbub, fournit tout ce qui faut pour un démarrage rapide ainsi qu’un guide.
En ce qui me concerne (pour ceux qui me suivent, vous commencez à me connaître), je vais faire le firmware from Scratch ! Cela va me permettre une maîtrise totale de celui-ci et de pouvoir inclure toutes les options que je souhaite !
Rendez-vous à la partie 3 pour le Firmware !
A bientôt les makers !
FASTOCHE !!